Navigating the world of pressure systems in industrial applications, often requires an understanding of the critical system elements. One of the key components is the pressure regulator valve. This device not only ensures optimal operational conditions but also maintains user safety in various applications. Given the essential role of pressure regulator valve plays in gas and fluid flows, it’s paramount to understand its functionalities, types, and different features.
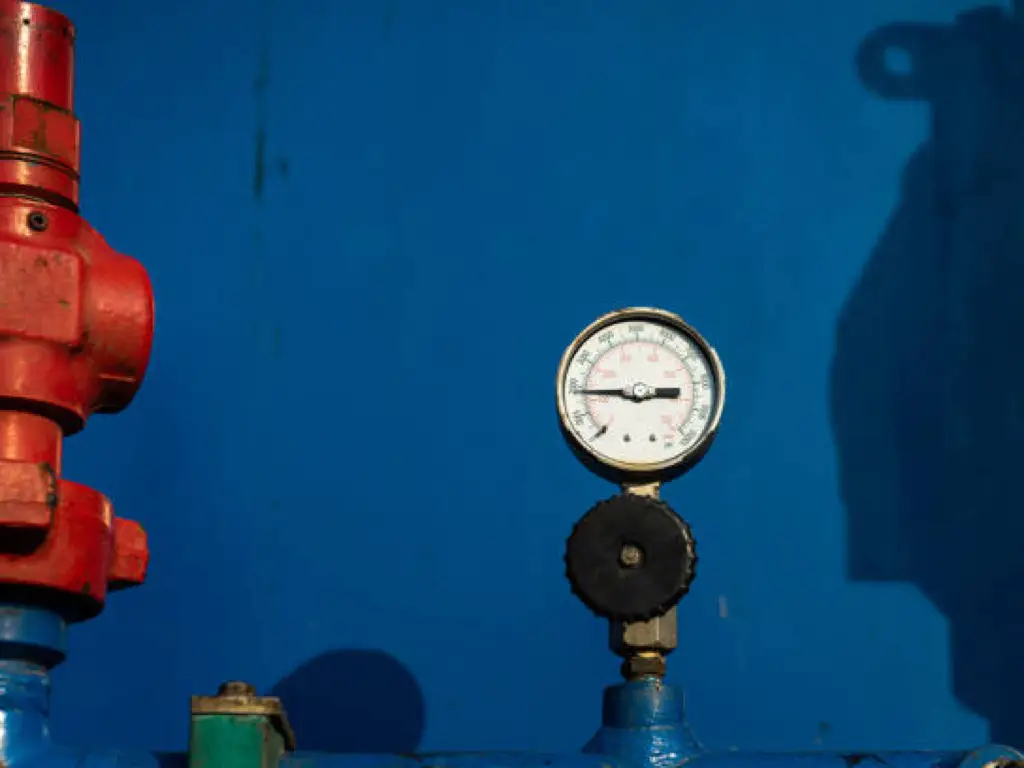
What Are Pressure Regulator Valves?
A pressure regulator valve controls the amount of pressure in a fluid or gas in different systems. In industrial applications, these devices help to contain and manage pressure variations that could otherwise cause damage or render an appliance or system unworkable. They fall into a broader category of regulators, whose primary purpose is to maintain a set amount of pressure or flow rate within a system.
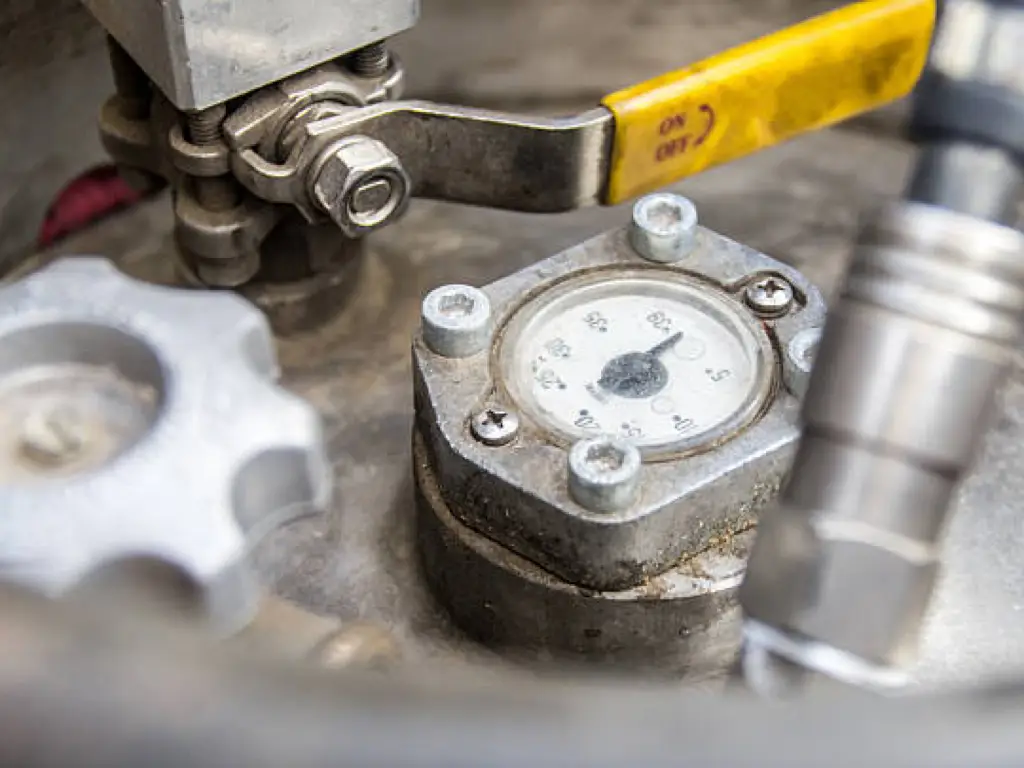
Pressure regulator valves work following the governing laws of fluid dynamics. They respond to alterations in pressure by either restricting or allowing more fluid or gas into a system, consistently keeping this influx at a pre-set level. In this way, they prevent overpressure or underpressure conditions that could destabilize the operational environment. The pressure regulator valves ensure that the pressure is maintained at the desired level, typically measured in inches.
Elements of Pressure Regulator Valves
Restricting Element
The restricting element is a critical component of a pressure regulator. It might be a poppet valve, a butterfly valve, or a globe valve, depending on the specifics of the regulator. These control valves restrict the flow of gas or fluid within the system, hence the name. They adjust according to the changes in system pressure, opening wider when pressure drops and reducing the opening size when much pressure increases.
Loading Element
The loading element is usually a spring, piston actuator, weight, or diaphragm combination. It applies force to the restricting element–the valve–and aids in its opening and closing. In the presence of high pressure in the system, the loading element helps close the valve, and vice versa, ensuring the system operates within the required pressure range.
Measuring Element
The measuring component is the “senso”r of pressure regulator valve setups. Often, this is the diaphragm itself which calculates when the inlet flow equals the outlet flow, ensuring balance within the system.
How Do Pressure Regulators Work?
The primary function of a pressure regulator is to maintain a fixed output pressure, providing consistent operation despite any changes in the input pressure or downstream usage levels. They function by releasing excess pressure from the system when it rises above a pre-determined level, which significantly contributes to the overall security of the setup.
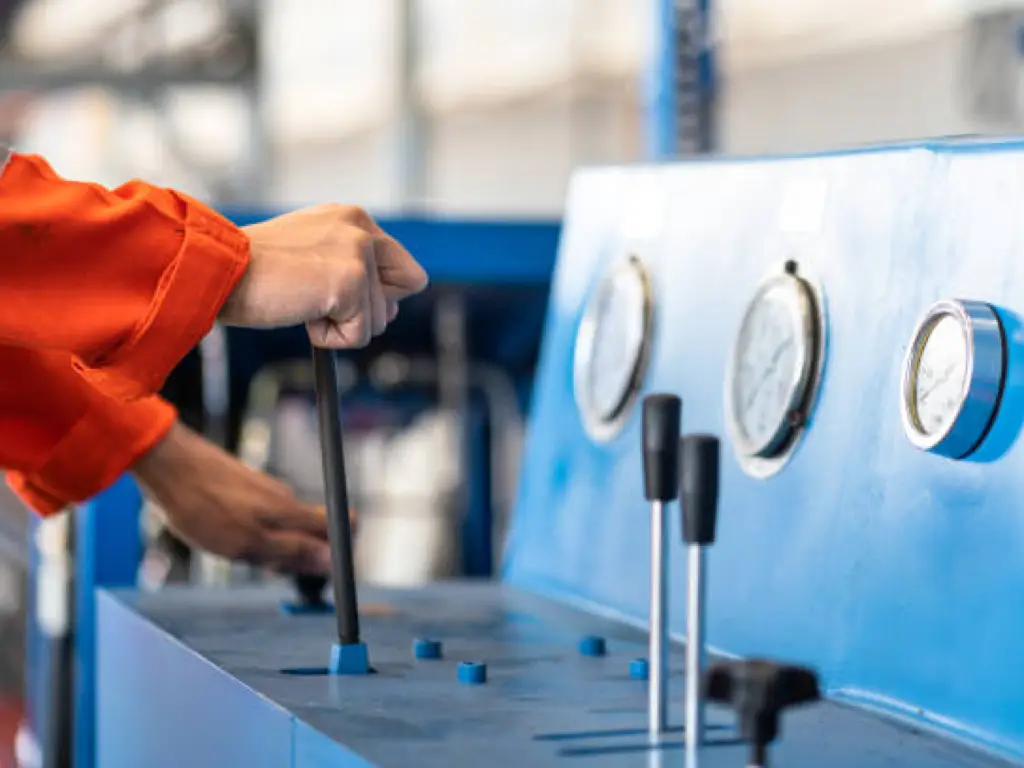
The pressurized flow travels through the inlet and enters the regulator. Here, the spring-loaded diaphragm or piston opens or closes the valve accordingly, regulating the amount of gas or fluid entering the system downstream of the valve. The outlet pressure is continually compared to the setting of the control spring, and whenever a difference from the desired setting is detected, the valve moves to correct it, ensuring maximum pressure control and set pressure.
Types of Pressure Regulator Valves
Pressure Reducing Valves | Back-Pressure Regulator Valves | |
Definition | A valve that reduces an input pressure to a lower output pressure. Also referred to as a pressure reducing regulator. | A control valve that maintains a set upstream pressure. These are typically closed valves, controlled by inlet or upstream pressure. |
Functionality | Aims to control and stabilize output (downstream) pressure, regulating the fluid/gas flow to maintain set pressure levels. | Aims to control and stabilize (upstream) inlet pressure, releasing excess pressure when the inlet pressure exceeds a pre-set point. |
System connection | Located at the outlet side of a system | Located at the inlet side of a system |
Used in | Commonly used in systems where stable downstream pressure is required, such as in water supply pipelines, air compressors, and propane supply lines. | Frequently used in settings where constant upstream pressure is needed, such as in gas chromatography, piping systems and in natural gas applications. |
Principle of Operation | Relies on pressure fluctuations in the system and responds to them by adjusting their valve opening to maintain steady downstream pressure. | Achieves pressure regulation through limitation and precise control of the upstream pressure of a system. It remains closed until the system’s pressure increases at the inlet port. When the system pressure surpasses the loading pressure, the valve opens to allow fluid to flow through. |
Pressure Reducing Regulators
What are They?
Pressure reducing regulators, also known as pressure reducing valves (PRV), are used to reduce or regulate the pressure in a system to the desired level on its outlet side.
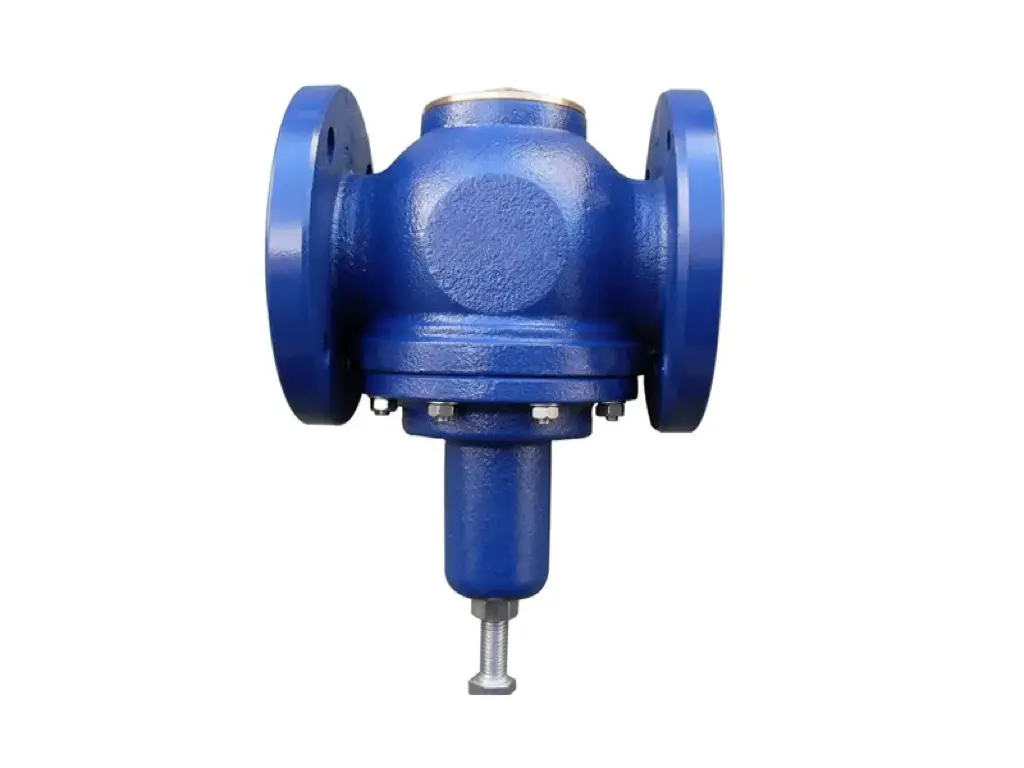
How to Operate?
Functioning on a principle of balancing pressure against a spring, pressure reducing regulators automatically adjust their valve opening to manage and maintain consistent downstream pressure. This is achieved by restricting or allowing fluid and gas flow when required. When pressure increases in the system, the regulator reacts by narrowing the valve opening, thus decreasing the flow. When pressure drops, the valve expands to allow more flow.
What are Their Applications?
Air or gas service: Used in compressed air systems, power tools, and pneumatic control systems.Water pressure reduction: Applied in industrial water distribution services, fire protection systems, and plumbing systems to regulate water pressure.Propane/LP gas: Employed in handling propane or liquified petroleum gas in commercial applications, such as heating and cooking systems.Mining industry: Utilized in the mining sector for maintaining optimal pressure in the operation of heavy machinery and equipment.
Back Pressure Regulators
What are They?
A back pressure regulator is a type of control valve responsible for managing a system’s set upstream pressure. This type of regulator works by maintaining inlet pressure and allowing excess pressure to vent through it, rendering it similar to a relief valve in function but with an emphasis on accurate pressure control.
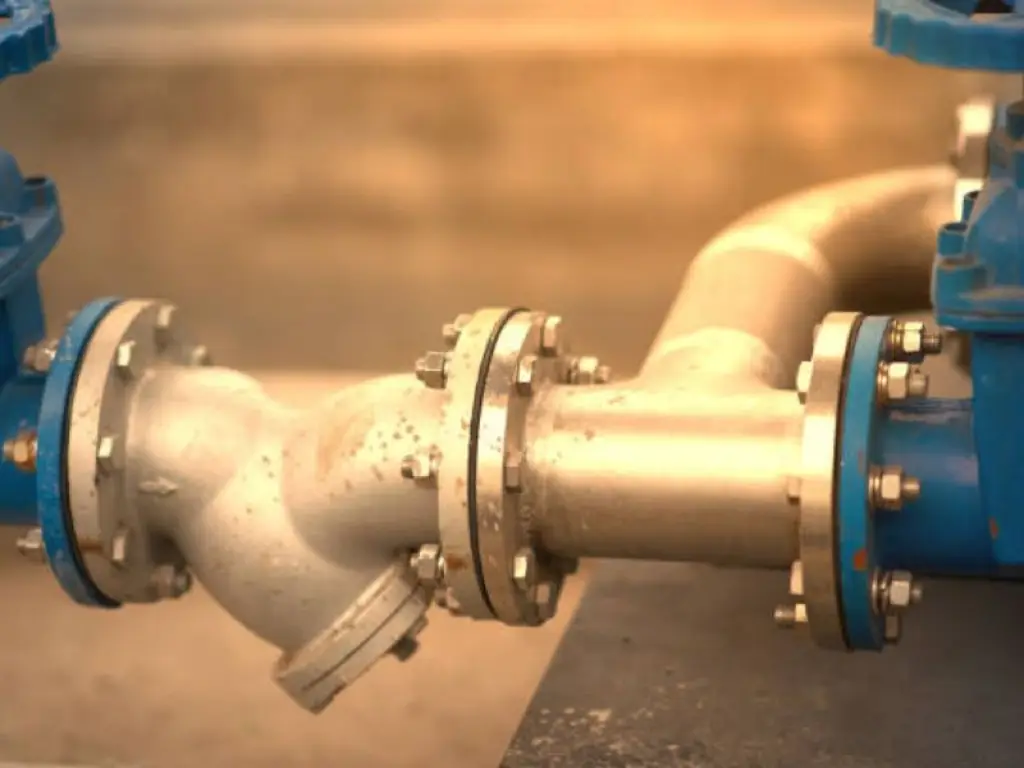
How to Operate?
In a back pressure regulator, the valve remains closed until the system’s pressure increases at the inlet port. This pressure increase provides a counterforce beneath the sensor that opposes the original force, leading to the valve’s opening. This balance allows fluid to flow through, decreasing system pressure until an equilibrium state is achieved, where the system pressure equals the loading force.
What are Their Applications?
High-pressure applications: Integrated into systems that operate under high pressures, ensuring upstream pressure remains constant and safe.Fuel and oil burner control: Implemented in the management of fuel and oil burners for stable inlet or upstream pressure required for efficient combustion.Fuel and oil atomization: Employed to maintain consistent fuel and oil pressure to facilitate atomization before combustion within engines or burners.Natural gas applications: Used in natural gas systems to ensure constant upstream pressure, enabling efficient distribution and storage of natural gas in industrial applications.
Difference Between Pressure Reducing Valves and Pressure Regulator Valves
Operation location: Pressure reducing valves work on the outlet side of a system and regulate downstream pressure. Back-pressure regulators control the inlet side, ensuring a steady upstream pressure.Functionality: Pressure reducing valves open or close according to changes in the system pressure to maintain a stable output pressure. Back-pressure regulators open as upstream pressure rises above a set point, regulating inlet pressure.Purpose: Pressure reducing valves are built to manage and regularize the output or downstream pressure, making them optimum for systems necessitating stable output pressure. Back-pressure regulators are designed to sustain consistent upstream or inlet pressure, ideal for systems needing constant pressure before the valve.
Assistants of Regulating Pressure
Single Stage Regulators
Single-stage regulators are designed such that the pressure control valve, the restrictor and the sensor are all integrated seamlessly into one body. This type of regulator maintains constant outlet pressure despite fluctuations in upstream pressure, making it useful in applications where steadiness is key.
Double Stage Regulators
Double-stage regulators are essentially two single-stage regulators combined in the same housing. They reduce pressure in two steps instead of one, providing more consistent and reliable pressure regulation, particularly in applications with likelihood of significant supply pressure variations.
Conclusion
In sum, pressure regulator valves play an integral role in ensuring smooth and safe operation of both simple and complex systems involving fluid or gas flow. Understanding their functionality, the basic elements, types, and operation can facilitate better decision making when investing in or troubleshooting issues associated with these essential devices. Given the spectrum of regulators available in the market, understanding ones’ specific needs will prove crucial in selecting the right form of the pressure regulator valve for a given application.
When considering pressure regulator valves, DomBor is a manufacturer worth noting. With 20 years of experience in the industry, DomBor has a reputation for producing high-quality custom valves, capable of withstand hard conditions. Their products are designed for optimal performance and durability, especially suitable for demanding industrial applications.
Regardless of your specific needs, DomBor’s range of pressure regulator valves adds another layer of security and efficiency to your operation, reinforcing the importance of such devices in today’s industrially focused world.