Introduction to Valve Standards
Overview of API, ISO, and ANSI Valve Standards
When we delve into the world of valve standards, it’s like opening a time-tested manual that has shaped the way we interact with our most fundamental utilities. The American Petroleum Institute (API), the International Organization for Standardization (ISO), and the American National Standards Institute (ANSI) aren’t just acronyms; they’re the backbone of an industry that thrives on precision.Valve standards, including those outlined by the American Society of Mechanical Engineers and others, serve as the guardians of efficiency and safety in a high-pressure environment where there is no room for error. The balance between flow control and tight shutoff is often a matter of a few turns of a gate valve or the seamless operation of solenoid valves.And yet, it’s not just about turning a ball valve in a piping system or ensuring the correct pressure ratings; it’s about a legacy. A legacy that’s woven by standard organizations and the hands of skilled workers in the valve industry across the United States and beyond ensures every component fits its intended use, from a butterfly valve in a suburban home to a complex array of control valves in a refinery.
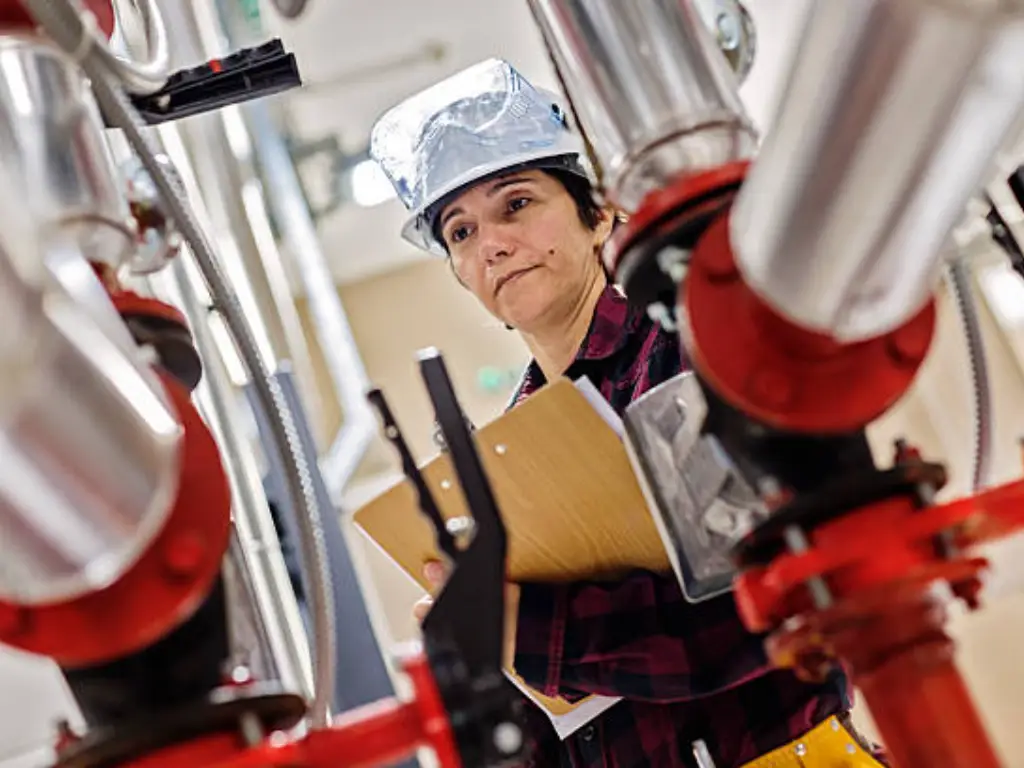
Understanding the Scope of Valve Standards
What Do Valve Standards Cover?
Valve standards are not just a collection of guidelines—they are the epitome of what it means to channel force through the conduits of civilization. High temperatures, the caustic flow of natural gas, and the very essence of process control rest upon these standards. From ASTM International to the Fluid Control Institute, every standardization society contributes a threat to this tapestry.Whether it’s a relief valve in a pressure vessel or a pinch valve in the fittings industry, the standards dictate the performance. The pressure ratings, temperature ratings, and even the specific standards for test procedures are all part of a larger narrative—a narrative that emphasizes proper functionality and overall performance.
Impact of Valve Standards on Valve Manufacturing
Every check valve and ball valve that makes its way into a pipeline transportation system is a testament to a manufacturer’s adherence to these standards. It’s not merely about compliance; it’s about upholding a tradition of excellence and safety. Major standard organizations dictate that a standard valve isn’t just another piece of metal; it’s a vessel for engineering prowess.Imagine a stainless steel valve designed for hydraulic fluid control—a piece that must withstand the relentless pressure and flow rate demands. It’s here that international standard organizations like the American Society play a critical role, setting the stage for what becomes the industry norm.
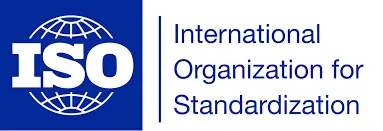
ISO 5208: The International Valve Standard
Key Requirements of ISO 5208
ISO 5208 (EN 12266-1) stands as a monolith in the international standard landscape. It is not merely about ensuring that a globe valve can execute flow control, but that every nuance, from its material to its structural integrity, can meet the stringent requirements set forth by a global consortium.In this intricate dance of metals and mechanics, terms like ‘standard valve’ and ‘international valve and instrument’ are not just thrown around—they are venerated. The specifications within ISO 5208 encompass an array of valve types, each with its own unique role in the fluid control symphony.
Testing Procedures and Acceptance Criteria
Diving deeper, ISO 5208 doesn’t just set the stage; it dictates the script by which every valve performance is judged. Testing materials, flow rates, and tight shutoff parameters are not just line items—they are the chapters of a story that each valve must tell flawlessly.The testing procedures and acceptance criteria within ISO 5208 are akin to the rehearsals of an orchestra—each instrument must play its part, and each valve must adhere to its role, ensuring the harmony of functionality and safety.
Test Procedure | Standard Division | Valve Type Applicable |
ISO 5208 Rate A | Zero leakage for soft seated valves | Ball Valves, Butterfly Valves |
ISO 5208 Rate B | Very slight leakage allowed | Gate Valves, Globe Valves |
ISO 5208 Rate C | Limited leakage acceptable | Check Valves, Plug Valves |
ISO 5208 Rate D | Leakage rate as agreed upon by customer and manufacturer | Special Purpose Valves |
API Standards: API 598 and API 6D
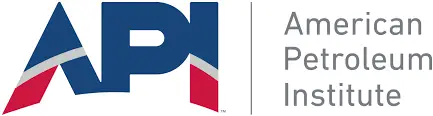
API 598: Valve Inspection and Testing
API 598 is like the vigilant overseer of the valve world. It doesn’t simply suggest; it demands that every valve be put through the paces of rigorous inspection and testing. When a valve manufacturer embarks on this journey, it’s with the understanding that every check valve, gate valve, and globe valve will face the test of fire and pressure.It’s a meticulous process where pressure relief valves and safety valves are subjected to scenarios far beyond their intended use. The purpose? To guarantee that when a valve claims to meet the API standard, it’s not just a badge—it’s a promise.
API 6D: Pipeline Valve Specifications
Meanwhile, API 6D is the script for a specific cast—the pipeline valves. These are the gatekeepers of the natural gas industries, the sentinels of the pipeline transportation systems. In the realm of high pressure and high stakes, API 6D is the rulebook that every player knows by heart.This is where specifications translate to safety and efficiency. The valve industry, much like the United States itself, is built on a foundation of standards, and API 6D ensures that this foundation is rock-solid.
Standard Code | Standard Name |
API 598 | Valve Inspection and Testing |
API 600 | Bolted Bonnet Steel Gate Valves for Petroleum and Natural Gas Industries |
API 602 | Compact Steel Gate Valves – Flanged, Threaded, Welding, and Extended-Body Ends |
API 607 | Fire Test for Quarter-turn Valves and Valves Equipped with Nonmetallic Seats |
API 609 | Butterfly Valves: Double-flanged, Lug- and Wafer-type |
API 6D | Specification for Pipeline and Piping Valves |
API 6A | Specification for Wellhead and Christmas Tree Equipment |
ANSI Valve Standards and Their Integration
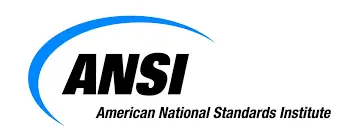
How ANSI Standards Complement ISO and API
In the complex orchestra of valve standards, ANSI conducts with a steady hand. It doesn’t seek to overshadow ISO or API; instead, it enhances, integrates, and solidifies. The American National Standards Institute’s guidelines weave through the fabric of valve specifications, ensuring that every thread—be it for a solenoid valve or a pressure vessel—is strong enough to hold the immense pressures they are subjected to.ANSI standards, often seen as a bridge between the robust American Society of Mechanical Engineers’ regulations and the global reach of the International Organization for Standardization, ensure a harmony that allows for seamless international cooperation and technological exchange.
ANSI Standards in Valve Selection and Application
The selection and application of a valve are pivotal decisions that resonate throughout the life span of a piping system. Whether it’s a stainless steel ball valve or a cast iron butterfly valve, the ANSI standards ensure that these components not only meet the minimum requirements but also fit elegantly into the grand design of a facility’s process control architecture.
Standard Code | Standard Name |
ANSI/FCI 70-2 | Control Valve Seat Leakage |
ANSI B16.34 | Valves – Flanged, Threaded, and Welding End |
ANSI B16.10 | Face-to-Face and End-to-End Dimensions of Valves |
ANSI B16.5 | Pipe Flanges and Flanged Fittings |
ANSI B16.25 | Buttwelding Ends |
ANSI B16.1 | Cast Iron Pipe Flanges and Flanged Fittings |
ANSI/ISA 75.01 | Specification for Process Control Valves |
ANSI/ISA 75.02 | Control Valve Response Measurement from Step Inputs |
Valve Types and Related Testing Standards
Common Valve Types Defined by Standards
The world of valves is as varied as the applications they serve. From the humble gate valve to the more complex control valve, each has its role, its personality, if you will. And for each, there’s a set of standards that define its existence and ensure its performance.
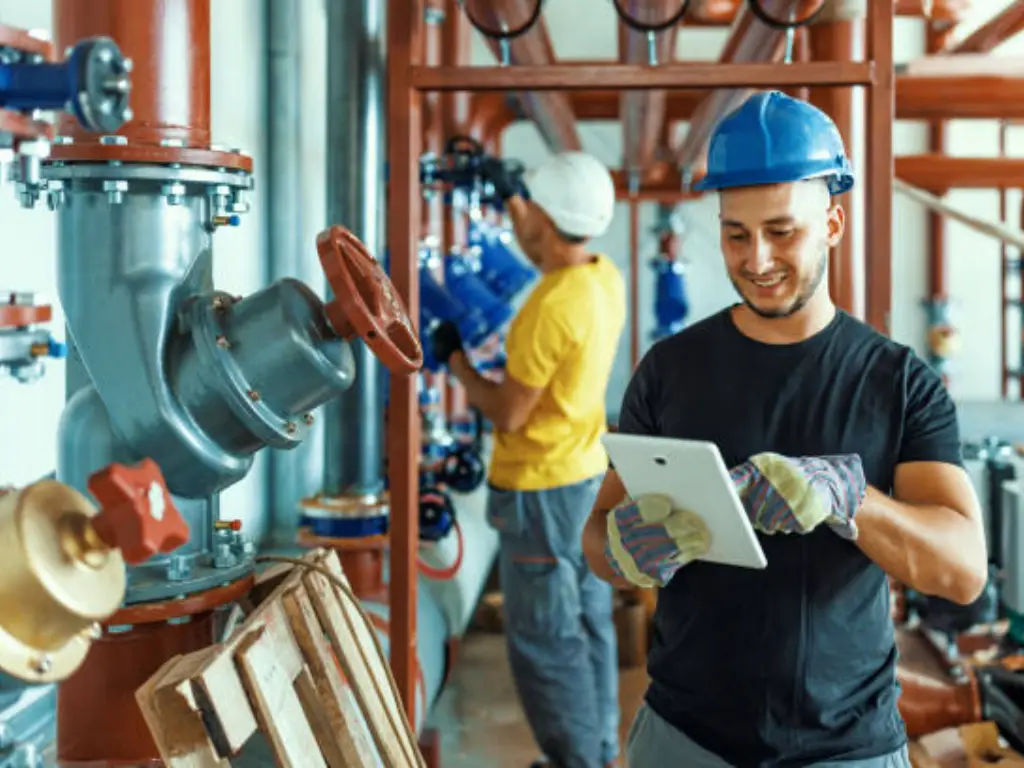
Test Standards Specific to Valve Types
The specificity of test standards for different valve types is crucial—it ensures that a ball valve meant for a cryogenic application doesn’t falter when faced with the extreme cold, or a globe valve for a steam system maintains integrity under the relentless heat.
Conclusion: The Continuous Evolution of Valve Standards
The story of valve standards is ever-evolving, much like the technology and industries they serve. The American Society of Mechanical Engineers, the American Petroleum Institute, and the International Organization for Standardization, along with many others, continue to adapt and refine their standards to meet the challenges of new materials, new processes, and new environmental considerations.In this dynamic field, a seasoned engineer’s insight is invaluable. A lifelong accumulation of knowledge, tempered by experience and an unwavering commitment to quality and safety, ensures that the valves of today not only meet current standards but are ready to evolve with the standards of tomorrow.As we close this chapter on valve standards, we look ahead to the next with anticipation and confidence that the industry’s commitment to excellence will continue to fuel innovation and safety in equal measure. The keyword is not just ‘standard”—it’s ‘evolution’.If you still have some questions about those standards, talk to Dombor and we will offer professional help.