Valves are needed in every industry. They are the ones to direct the flow, in these sectors, such as water treatment, oil and gas and food and beverage. Their role is essential in the control and protection.
What are the reasons behind the significance of the valves? For instance, think of oil and gas industry. The valves are responsible for regulating the oil and gas flow in the pipelines. A failed valve may result in huge losses and cause damages to the environment. For example, the ball valve which has been designed for this purpose can be used to control the oil flow accurately thus reducing pressure loss. This will lead to a reduction in the operational costs. Industry data demonstrate that high-tech valves can increase flow control precision up to 30%. This can be said to be the main factor that makes the production process to be more effective and safer.
Our guide will discuss what valves are used for in industrial applications. Different industries do not have the same needs. We will examine different valve types, their functions, and the problems that they can address.
Optimizing Water Systems: Valve Applications in Water Treatment
Water treatment is key in our lives, providing clean water for homes, businesses, and public areas. In this vital industry, valves are indispensable for guiding and managing the water flow with precision.
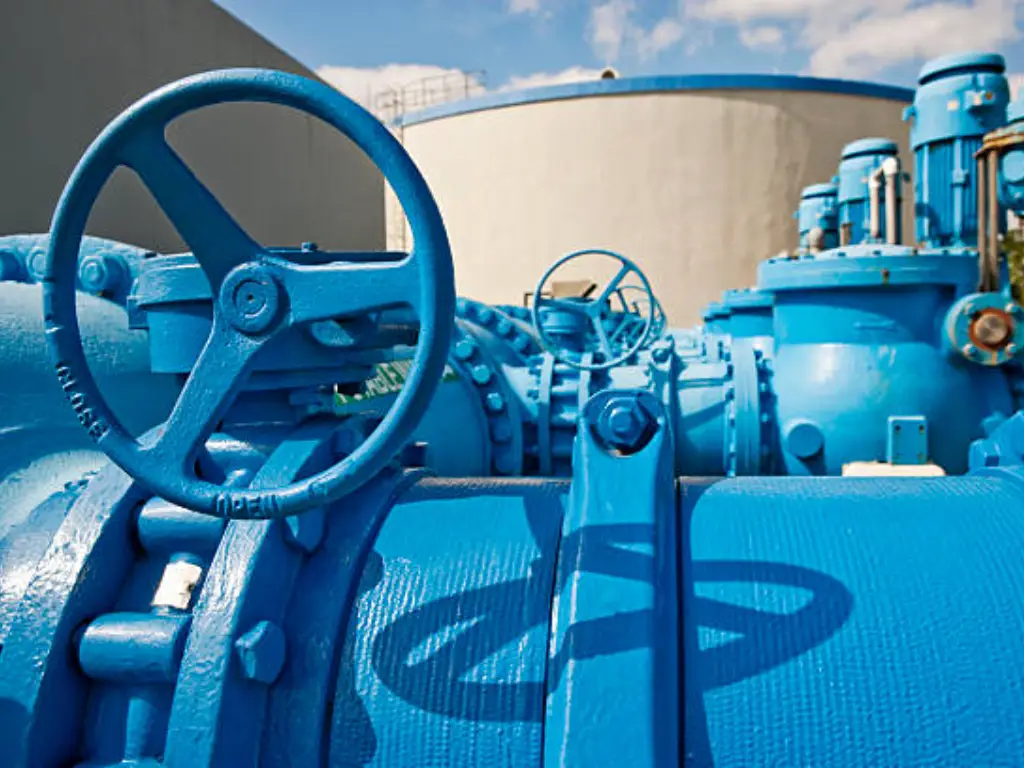
Among the variety of valves used, certain types are more prevalent due to their functionality matching industry demands. Ball valves, with a usage rate of around 20%, are favored for their robust sealing and capacity to handle high pressure, crucial for the rigorous processes within water treatment facilities. Gate valves, with their ability to serve as isolation valves and control the flow of liquid through pipes, account for approximately 15% of use and are essential in regulating water supply. These mechanical devices are selected for scenarios requiring little to no flow resistance, ideal for smooth water passage. The standout, however, are butterfly valves, occupying a 25% share. Their compact design and efficiency in handling large water volumes make them a primary choice, especially when the valve’s port matches the pipe diameter.
Below is a table summarizing valve use in water treatment:
Valve Type | Function | Usage % | Materials | Wastewater Type |
Butterfly Valves | Regulates flow | 25% | Stainless Steel, PVC | Chemical, municipal |
Gate Valves | On/off control | 20% | Cast Iron, Brass | Residential, industrial |
Check Valves | Stops backflow | 20% | Stainless Steel, PVC | Mixed, stormwater |
Ball Valves | Precise control | 15% | Brass, PVC | Lab, pharma |
Diaphragm Valves | Against corrosives | 20% | Plastic, Rubber | Acidic, chemical |
Fueling Progress: Valve Use in Oil & Gas Exploration and Refining
The oil and gas industry is vital worldwide. It powers many parts of our lives and economy. Valves play a big role in making this sector work safely and smoothly.
Different types of valves are crucial in the oil and gas industry, with various applications for controlling the flow of gas and fluid. For example, ball valves make up about 30% of the valves used and are great for stopping and starting the flow of gas due to their strength and ability to handle high pressure conditions, including minimizing pressure drop. Gate valves, accounting for about 25% of cases, are mainly used to open or close the path for gas to move through the pipes. Lastly, globe valves, accounting for about 20% of use, are essential for carefully adjusting the flow of gas under high-pressure conditions. These percentages show how each type of valve plays a crucial role in handling gas, ensuring safety and reliability in the oil and gas industry. Additionally, selecting the right valve design is important in minimizing damage and failure in the system, making it a crucial aspect of oil and gas exploration and refining.

Valves here must deal with pressures from 200 to 15,000 psi and temperatures from -46°C to 250°C. Such extreme conditions require valves made from tough materials like stainless steel or special alloys to prevent rust and wear.
Keeping these valves in good shape is key. Regular checks and upkeep help avoid leaks and ensure everything runs as it should. This keeps operations efficient and safe, making sure the equipment lasts longer.
Here’s a quick table for reference:
Valve Type | Function/Preference | Usage % | Fluid Medium | Materials |
Ball Valve | Quick shut-off; Reliable for high pressure and volume | 25% | Oil, gas, water | Steel, stainless steel |
Gate Valve | Minimal pressure drop; Ideal for on/off control | 30% | Crude oil, natural gas | Forged steel, cast steel |
Globe Valve | Flow regulation; Precise control for throttling | 15% | Water, steam, gas | Stainless steel, alloy steel |
Butterfly Valve | Large volume flow control; Compact and economical | 10% | Air, gas, oil | Cast iron, stainless steel |
Check Valve | Prevent backflow; Automatic operation | 20% | Oil, gas, water | Stainless steel, carbon steel |
Powering Up: The Role of Valves in Energy Generation
Energy production is crucial for powering industries and cities, involving different types like renewables (wind and solar) and traditional (coal, nuclear, hydroelectric). Each plays a significant role in our ability to sustain operations and promote growth.
Valves are crucial in the process of energy generation. They play a vital role in controlling the flow of fluids and ensuring the safe operation of energy systems. In industries that use coal or gas, gate valves are commonly used, accounting for approximately 30% of all valves in these settings. These valves are effective in completely stopping or allowing flow, making them essential for managing high-pressure situations. In nuclear energy plants, globe valves make up about 25% of all valves used. They are chosen for their ability to carefully control flow, which is crucial for maintaining the plant’s cooling systems. In renewable energy sources, such as water power plants, butterfly valves are commonly used, accounting for around 20% of all valves. This type of valve is ideal for handling large amounts of water quickly, making it essential for controlling the flow of fluids for power generation.
Here’s a simple table showing this info:
Energy Source | Valve Type | Function/Preference | Usage % | Fluid Medium | Materials |
Hydroelectric | Butterfly Valve | Regulate flow; High capacity, low head loss | 0.4 | Water | Stainless steel, cast iron |
Thermal (Coal, Gas, Nuclear) | Globe Valve | Precise flow control; Good for throttling | 0.3 | Steam, water | Alloy steel, stainless steel |
Solar Thermal | Ball Valve | Quick shut-off; Minimal leakage | 0.25 | Thermal oil, water | Stainless steel, carbon steel |
Wind | Check Valve | Prevent reverse flow; Protect system integrity | 0.2 | Air, hydraulic fluid | Stainless steel, carbon steel |
Biomass | Gate Valve | Isolation; Minimal pressure drop | 0.3 | Steam, biomass slurry | Cast iron, stainless steel |
Chemical Processing and Valves: A Precision-Based Partnership
In the world of chemical manufacturing, valves play a key role. They help control the flow of materials. This control is essential for safety and for making sure reactions happen correctly.
In chemical plants, you’ll find several types of valves. Ball valves are quite common, used about 30% of the time. They are great at sealing tightly, which is very important for handling dangerous chemicals safely. Butterfly valves are also used, making up 20% of usage. These valves are good for controlling big flows of liquid at lower pressures, and they don’t cost too much. Gate valves are another 25%. They’re chosen for tasks that need a clear path for the flow, with little resistance. Safety valves, also known as safety relief valves, are crucial in chemical processing as they act as a pressure relief valve to protect equipment from exceeding required limits. This precision-based partnership between chemical processing and safety relief valves, which operate based on fluid pressure, ensures the safe handling of dangerous chemicals and maintaining the set limit for pressure.
Maintenance for these valves is crucial. It prevents problems and ensures everything runs smoothly. Every year, keeping valves in good shape can cost between $100-$1,000. This cost covers checking the valves, cleaning them, and replacing any parts that wear out. Regular maintenance stops unexpected shutdowns and increases the service life.
Here’s a simple table for a quick look:
Valve Type | Function/Preference | Usage % | Fluid Medium | Materials | Maintenance Cost (Annual, Approx.) |
Ball Valve | Secure shut-off; High durability against chemicals | 30% | Gases, Liquids | Stainless steel, PTFE | $1,000 |
Butterfly Valve | Flow regulation; Economical, space-saving | 25% | Gases, Light liquids | Stainless steel, PVC | $800 |
Gate Valve | Minimal pressure drop; For viscous fluids | 15% | Liquids, Slurries | Cast iron, Stainless steel | $1,200 |
Globe Valve | Precise throttling; High pressure control | 20% | Gases, Liquids | Stainless steel, Alloy | $1,500 |
Diaphragm Valve | Leak-free operation; Handles corrosive materials | 10% | Liquids, Gases | PTFE, EPDM, Stainless steel | $900 |
Valves in Agriculture: Irrigation and Water Management Solutions
Agriculture is essential in our daily lives. It provides food for the world and supports communities. Valves play an important role here. They help manage how much water plants get, saving lots of this valuable resource.
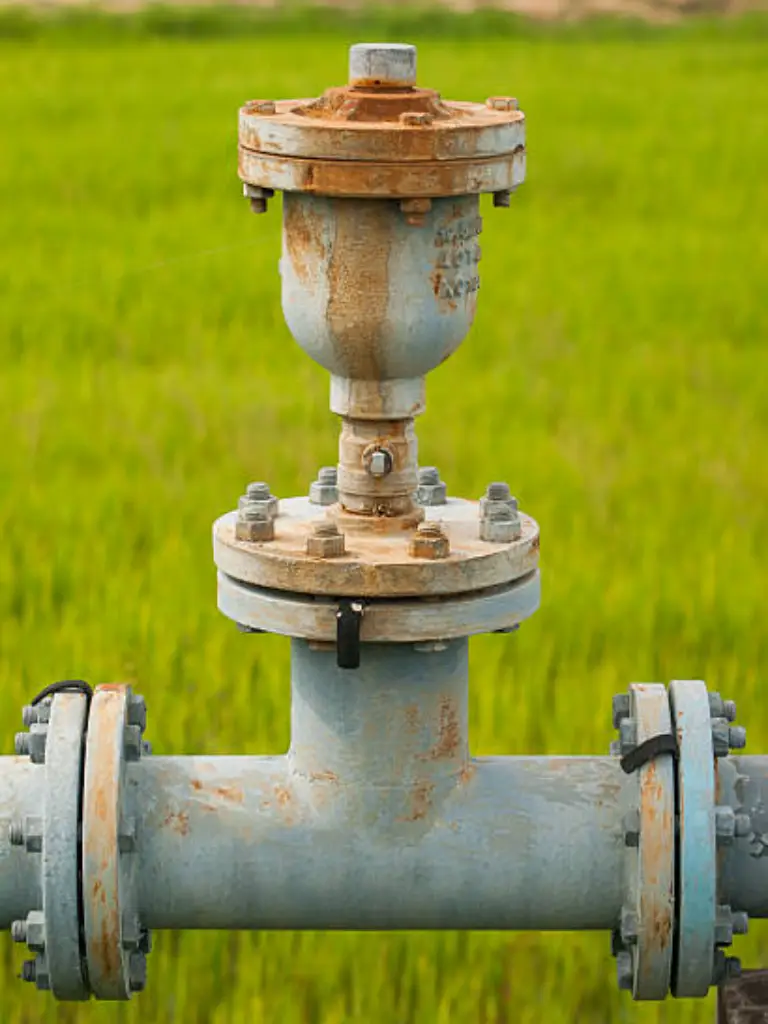
Valves are mainly used in two places in farming: in irrigation systems and for managing water resources. There are several types of valves used, each with its own job. Globe valves, known for their ability to control water flow accurately, are about 20% of the valves used in agriculture. This accuracy is very important for giving crops just the right amount of water for healthy growth. Gate valves, another type making up about 30% of use, are essential for starting or stopping water flow across large farms due to their valve size being able to accommodate the pipeline diameter.
For better crop growth, automatic control valves come highly recommended. These smart valves adjust water flow based on what the plants need, making them very useful. They help make sure plants get just enough water without wasting any.
Here’s a simple table for a quick look:
Valve Type | Function/Preference | Usage % | Fluid Medium | Materials |
Gate Valve | Minimal pressure loss, reliable | 25% | Water, wastewater | Cast iron, stainless steel |
Butterfly Valve | Flow regulation, compact | 20% | Water, air, gases | Cast iron, PVC, stainless steel |
Ball Valve | Precise control, durable | 30% | Water, chemicals | PVC, stainless steel, brass |
Check Valve | Prevents backflow, automatic | 15% | Water, wastewater | Stainless steel, brass, PVC |
Diaphragm Valve | Corrosion-resistant, precise control | 10% | Water, fertilizers, acids | PVC, stainless, rubber-lined |
Pharmaceuticals and Biotech: Valves in Clean and Controlled Environments
The pharmaceutical and biotech fields are essential for health care progress, creating medicines and vaccines that are life-saving. Valves are key in these industries, ensuring environments are clean and controlled, critical for keeping drug quality high.
Diaphragm valves are most used, taking up about 40% of valve use. They’re chosen for their low contamination risk, perfect for clean processes. Ball valves, making up 30%, are picked for their strong and steady flow control. Butterfly valves, at 20%, are good for managing flow in big pipes, while check valves, at 10%, stop fluid from flowing backward, keeping the process safe.
Valve materials important in these industries are:
- Stainless Steel: Often used for its corrosion resistance and easy cleaning.
- PTFE (Polytetrafluoroethylene): Found in diaphragm valves for not reacting with materials.
- PVC (Polyvinyl Chloride): Used where direct contact isn’t an issue, chemical resistance and cost-effectiveness.
These materials are selected for keeping cleanliness, prolonging service life, and not reacting with drugs, ensuring processes stay pure and effective.
Here’s a simple table for a quick look:
Valve Type | Function/Preference | Usage % | Fluid Medium | Materials |
Diaphragm Valve | Sterile processing; Minimizes contamination risk | 40% | Liquids, Gases | Stainless steel, EPDM, PTFE |
Ball Valve | Secure shut-off; Easy to clean, low maintenance | 20% | Liquids, Gases | Stainless steel, PTFE |
Butterfly Valve | Flow regulation; Compact design, easy operation | 15% | Liquids | Stainless steel, PTFE, EPDM |
Check Valve | Prevents backflow; Self-acting, ensures purity | 10% | Liquids, Gases | Stainless steel, PTFE |
Solenoid Valve | Precision control; Fast response, for automated systems | 15% | Liquids, Gases | Stainless steel, PTFE, brass |
Marine and Shipping: Navigating Valve Applications at Sea
Marine shipping is crucial for global trade, carrying goods across the sea. Valves are important on these vessels, controlling liquids and gases to keep everything running smoothly.
On ships, different valves have their jobs. Gate valves are common, making up about 30% of all valves. They’re liked for their ability to let flow through without much resistance, useful for moving fuel. Globe valves, about 20% in use, are good for adjusting flow, important for cooling things down. Ball valves, which are about 25%, are chosen for their strength and leak-proof nature, needed for handling water in and out of the ship, ensuring smooth fluid flow. Another important valve in marine and shipping applications is the valve body, which is a major component of a globe valve and allows for precise control of fluid flow.
The size and application of a vessel significantly influence the number and types of valves used. For example, a large tanker would require a more extensive valve system, including engine valves, compared to a small cargo ship, impacting maintenance and operational efficiency. Using too few valves, including engine valves, could compromise the ship’s safety and functionality, while too many could lead to unnecessary complexity and maintenance issues.
For marine use, valves must handle the ocean’s tough conditions, including saltwater. Bronze and stainless steel are top choices:
- Bronze: Resists saltwater corrosion well, perfect for use with seawater.
- Stainless Steel: Strong and lasting, important for high-pressure areas.
Here’s a simple table for a quick look:
Valve Type | Function/Preference | Usage % | Materials |
Gate Valve | Isolation; low friction, durable | 20% | Bronze, stainless steel, cast iron |
Globe Valve | Flow control; precise throttling, drop across the valve | 25% | Bronze, cast iron, stainless steel |
Ball Valve | Quick shut off; reliable sealing, easy operation | 30% | Bronze, stainless steel |
Butterfly Valve | Throttling/regulation; low pressure drop, compact design | 15% | Stainless steel, aluminum, bronze |
Check Valve | Prevent backflow; automatic operation | 10% | Bronze, stainless steel, cast iron |
Valves in Food and Beverage: Ensuring Safety and Quality
The food and beverage sector is key to our well-being, offering the nourishment we depend on daily. Valves in this field are vital for keeping products safe, high-quality, and making production smooth. They help manage liquids and ensure clean conditions.
In this industry, butterfly valves are most common, making up 35% of use because they control flow well and are easy to clean. Ball valves, at 30%, are chosen for their strong seal and quick use. Diaphragm valves, which account for 20%, offer precise flow control and meet cleanliness needs. Check valves, filling the remaining 15%, stop unwanted backflow and keep products safe.
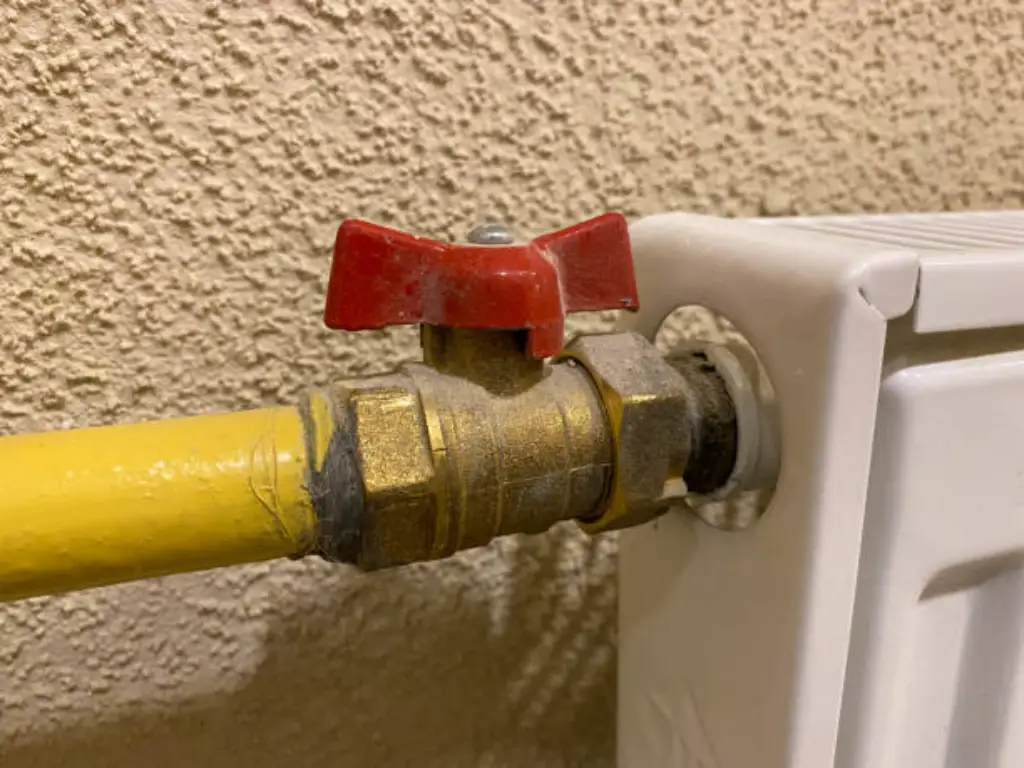
Valves must follow strict rules to make sure food safety is upheld. Materials like stainless steel and specific plastics that touch food must meet safety standards. Such as those set by the FDA and the European Food Safety Authority, which specify materials and designs that prevent contamination and are easy to clean and sterilize. These materials are non-reactive and simple to clean, preventing any contamination.
Here’s a summary of valve use in the food and beverage industry:
Valve Type | Usage Percent | Purpose | Material Must-Haves |
Butterfly Valve | 35% | Flow control, easy cleaning | Stainless steel, safe seals |
Ball Valve | 30% | Handling liquids, sealing | Stainless steel, PTFE seals |
Diaphragm Valve | 20% | Precise control, cleanliness | Safe elastomers, stainless steel |
Check Valve | 15% | Blocking backflow | Stainless steel, suitable seals |
Pulp, Paper, and Textiles: Valves in the Production Process
The pulp, paper, and textile sectors play crucial roles in our everyday lives, supplying materials for writing, packaging, and clothing. Valves in these industries manage fluid and gas flows, ensuring production runs smoothly and safely.
In pulp and paper, gate valves, used in 40% of applications, are ideal for thick pulp. Ball valves, 30%, provide secure sealing for chemical handling. Butterfly valves, chosen for 20% of uses, adjust flow in large pipes efficiently. Diaphragm valves, at 10%, are precise for wastewater treatment.
For textiles, ball valves lead at 50% for their flexibility in dyeing and finishing. Butterfly valves, at 30%, work well in water and steam management. Check and gate valves, each at 10%, are vital for backflow prevention and water control, ensuring consistent processing quality.
Here’s a detailed valve usage table for both industries:
Industry | Valve Type | Usage Percentage | Purpose | Material |
Pulp & Paper | Gate Valve | 40% | Thick pulp flow | Stainless steel |
Ball Valve | 30% | Chemical process control | Stainless steel | |
Butterfly Valve | 20% | Flow regulation in large pipes | Cast iron | |
Diaphragm Valve | 10% | Wastewater treatment | Plastic | |
Textiles | Ball Valve | 50% | Dyeing and finishing | Stainless steel |
Butterfly Valve | 30% | Water and steam flow control | Cast iron | |
Check Valve | 10% | Prevent backflow | Brass | |
Gate Valve | 10% | Water flow regulation | Stainless steel |
Mining and Mineral Processing: Valves on the Front Line
The mining and mineral processing industry is key for industrial growth, supplying essential materials for various sectors. Valves are critical here, controlling the movement of slurries, water, and chemicals efficiently and reliably.
Slurry valves, including pinch valves, which handle abrasive substances, represent about 40% of valve use in this field due to their specialized design. Ball valves, with a 30% share, are chosen for their strong seal and versatility in managing liquids. Plug valves, at 20%, are ideal for high-pressure and high-temperature applications, including vacuum systems. However, they do require substantial force to operate due to friction. Check valves, making up the remaining 10%, prevent reverse flows, ensuring system safety and are selected based on the type of material they are compatible with.
Here’s a quick summary of valve applications in the mining and mineral processing industry:
Valve Type | Function/Preference | Usage % | Fluid Medium | Materials |
Knife Gate Valve | Abrasive/slurry control; durable against solids | 30% | Slurries, abrasive fluids | Stainless steel, ductile iron |
Ball Valve | Tight sealing; for liquids and gases | 20% | Water, chemicals, air | Stainless steel, carbon steel |
Butterfly Valve | Flow regulation; compact, economical | 15% | Water, slurries | Stainless steel, high-performance polymers |
Diaphragm Valve | On/off control; prevents leakage | 10% | Chemicals, slurries | Rubber-lined, stainless steel |
Pinch Valve | Handling abrasive/slurry; flexible closure | 25% | Slurries, abrasive liquids | Rubber, high-performance polymers |
Emerging Applications of Valves in Renewable Energy
Renewable energy is crucial for our planet. It helps us use less oil and gas. We get renewable energy from the sun, wind, water, and the earth’s heat.
Valves are very important in making renewable energy work well. Solar power uses ball valves (30%) to manage heat fluids. Wind power uses butterfly valves (25%) for cooling and lubrication. Water power depends on gate valves (30%) for controlling water flow and water distribution. Geothermal energy uses check valves (15%) to stop fluid from going the wrong way. Additionally, solenoid valves are becoming increasingly popular in renewable energy applications, including temperature control in heating and cooling systems. These valves use electric energizing or de-energizing to open or close, making them an efficient and precise control unit for various renewable energy processes.
Here’s a simple look at valves in renewable energy:
Renewable Energy Source | Valve Type | Function/Preference | Usage % | Materials |
Hydro Power | Butterfly Valve | Flow control; High flow capacity, low head loss | 30% | Cast iron, stainless steel |
Gate Valve | Isolation; Durable in water, low flow resistance | 20% | Stainless steel, bronze | |
Wind Power | Ball Valve | Secure sealing; Minimal maintenance required | 40% | Stainless steel, carbon steel |
Check Valve | Prevent backflow; Automatic operation | 20% | Stainless steel, plastic | |
Solar Power | Solenoid Valve | Precision control; For fluid temp regulation | 50% | Brass, stainless steel |
Butterfly Valve | Regulation/Isolation; Compact and economical | 30% | Stainless steel, ductile iron | |
Biomass | Ball Valve | Easy operation; Secure sealing for slurries | 25% | Stainless steel, carbon steel |
Knife Gate Valve | Slurry control; Handles solids, abrasive fluids | 35% | Stainless steel, ductile iron |
Future Trends: Smart Valves and Automation in Industrial Applications
The future of valves in industry will become smart and automated. Valves-related reports show that new valves with sensors and software are becoming popular. These smart valves can check data in real-time, predict when they might need fixing, and can be remote controled.
The main driver for this change comes from the development of the Industrial Internet of Things (IIoT). This means machines are connected and can share information. For instance, in the oil and gas industry, using smart valves has made things safer and work better. Data shows that smart valves can cut down the time operations are stopped by up to 30%. In water treatment, smart valves help control water flow and quality accurately, which is better for the environment.
Moving towards smart valves and automation is a big step for industries. This new direction will change how valves are used and make industries more modern and efficient. As these technologies keep getting better, they will open up new chances for better valve use in all kinds of work, leading to an industrial world that’s more connected and smart.