What Is a Gas Meter and Regulating Station?
Gas meters and regulating stations are essential components in a gas distribution network and it plays a crucial role in monitoring, controlling, and measuring the flow of gas from the distribution network to the end user.
A gas meter measures the amount of gas used by a customer or business for billing purposes. While regulating stations are used to adjust the pressure of gas flowing through the pipes before it reaches customers.
Valves are also important to the gas meter and regulating station because it helps to regulate the flow of gas in the distribution area. The industrial ball valve acts as a control mechanism to turn the flow of gas on and off or to adjust the pressure of the gas, as needed.
By controlling the flow of gas, the valve helps to ensure that the gas meter, located at the gas metering station, accurately measures the amount of gas used by a customer or business. These components ensure the safety and efficiency of the gas distribution system.
Benefits of Gas Metering Station
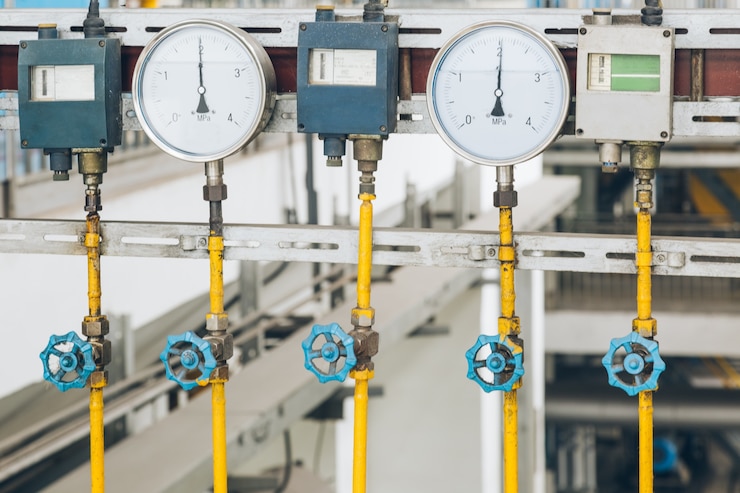
Gas metering stations play an important role in ensuring the quality and accuracy of natural gas that is delivered to commercial customers. They are designed to monitor and measure the amount of natural gas consumed by consumers, as well as calculate the cost of the gas consumed. As such, they offer several key benefits.
One of the primary benefits offered by gas metering stations is accurate billing. Through the installation of gas meters at each consumer’s location, companies can effectively measure and record the amount of gas used by customers. This helps them to accurately bill customers for the precise amount of natural gas that has been consumed by them.
Another benefit offered by gas metering stations is improved safety and quality control measures. By regularly monitoring and measuring the exact pressure and volume of natural gas that is being delivered to customers, companies can ensure that no irregularities or safety issues arise in their pipelines or within their systems.
This helps prevent dangerous situations such as pipeline explosions or significant loss of pressure, keeping both customers and providers safe.
Another benefit is to provide companies with detailed insights into consumer usage patterns. Through regular monitoring and measurement of consumer usage, companies can gain useful insights into consumer behavior, enabling them to identify trends and develop new strategies to improve services or manage resources more efficiently.
This is particularly useful in the energy industry, where companies can use data from gas metering stations to develop more efficient and cost-effective energy distribution models.
Natural Gas Supply Chain
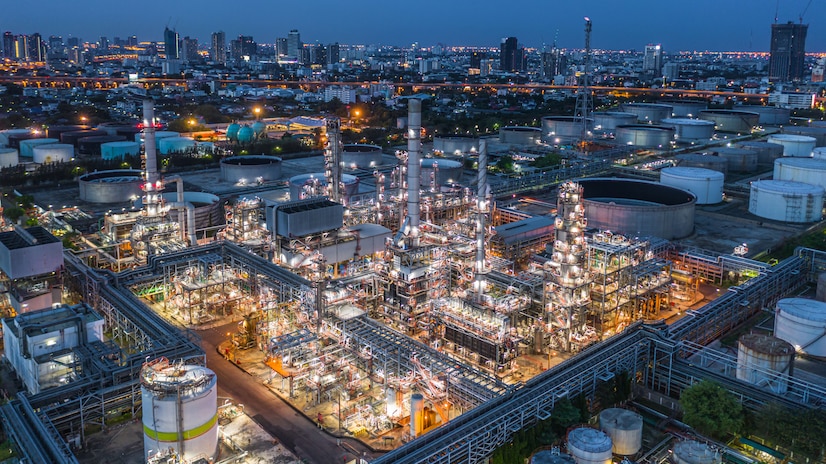
The natural gas supply chain is composed of many different participants, from the drillers and producers in the upstream, to the processors and distributors in the midstream, and finally to the end-users at the point of consumption.
Upstream
In the natural gas supply chain, “upstream” refers to the early stage of the production process, including the exploration, extraction, and production of natural gas, which involves activities such as drilling wells, processing raw natural gas to remove impurities, and transporting the purified natural gas to storage and processing facilities.
Industrial valve manufacturers play a crucial role in the upstream segment of the supply chain by providing the necessary valves for controlling the flow of natural gas at various stages of production, from extraction to transportation to storage facilities.
The upstream segment of the natural gas supply chain is typically owned and operated by oil and gas companies, who work to find and extract natural gas from underground reservoirs and use industrial valves to ensure safe and efficient operations.
Midstream
This refers to the transportation, storage, and processing of natural gas between the upstream production stage and the downstream distribution stage. This segment of the supply chain is responsible for moving natural gas from the production site to the point of consumption, usually through pipelines and storage facilities.
Midstream activities also include processing natural gas to remove impurities and to make it suitable for end use. The midstream segment of the natural gas supply chain is typically owned and operated by specialized companies that focus on transportation, storage, and processing.
Downstream
Downstream is the final stage of the process, including the distribution, marketing, and sale of natural gas to end-users.
This segment of the supply chain includes activities such as delivering natural gas to commercial, and industrial customers through pipelines, as well as selling natural gas to customers for heating, electricity generation, and other purposes.
The downstream segment of the natural gas supply chain is typically owned and operated by utility companies and other energy companies that specialize in distributing and selling natural gas to customers.
The natural gas is typically transported from the midstream segment to the downstream segment through pipelines, where it is then distributed to customers through a network of local distribution systems.
Applications of Flow Meter Station
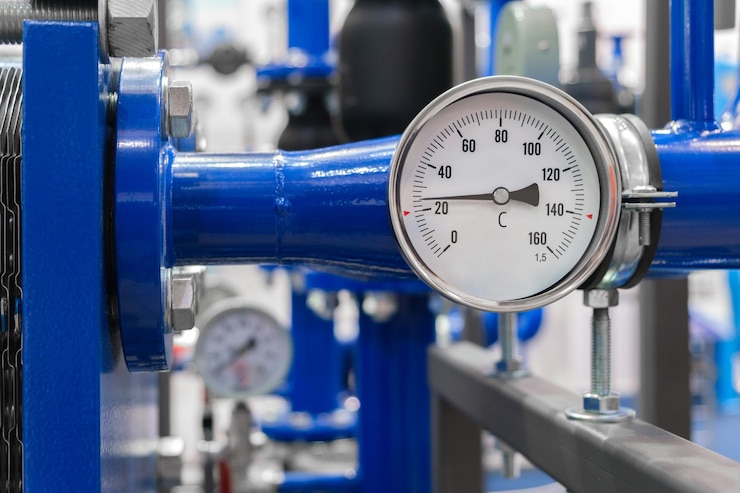
The use of flow meters is widespread, from chemical engineering to food processing, and they are often categorized according to the type of measurement they provide. Flow meter stations combine multiple flow meters into a single comprehensive unit that can be used to measure different parameters of a process. They are widely used in various industries and applications, including:
Water and Wastewater Treatment
Flow meter stations are used to measure the flow of raw water into treatment plants, the flow of treated water into distribution systems, and the flow of wastewater in collection and treatment systems. This information is used to optimize treatment processes, monitor system performance, and ensure compliance with regulatory standards.
It provides accurate and reliable measurement data, which is essential for the efficient and effective operation of water and wastewater treatment systems, as well as for ensuring that water resources are used sustainably and waste streams are managed safely.
Oil and Gas Production and Transportation
Flow meter stations play a critical role in oil and gas production and transportation by measuring the flow of fluids and gasses in the production and transportation process.
For example, flow meters are used in oil and gas production to measure the flow of oil, gas, and water from wells and to monitor the flow of these fluids in production and transportation pipelines.
Chemical and Pharmaceutical Processing
Flow meters are used in chemical and pharmaceutical processes to measure the flow of reactants, solvents, and intermediates, as well as to monitor the flow of finished products. Flow measurement data help process engineers ensure consistent product quality, detect process anomalies, and optimize production processes.
In addition, flow meter stations can be used for metering and control of critical process streams, such as those used for sterile and high-purity applications, which helps to prevent contamination and ensure product safety.
Power Generation
The important role of a flow meter station in power generation is that they measure and control the flow of fluids and gasses in power generation processes. Flow meters are used in hydroelectric power generation to measure the flow of water in dams and to control the flow rate for optimal power generation.
In renewable energy generation, flow meters are used to measure the flow of liquids in biofuel and biomass processes, as well as the flow of fluids in geothermal and solar thermal power generation.
Food and Beverage Processing
Flow meters are used in food and beverage processing to measure the flow of ingredients, such as liquids, syrups, and purees, and to monitor the flow of finished products, such as beverages and sauces.
This information is used to monitor product quality, and ensure the consistency of the final product.
Automotive Manufacturing and Testing
To ensure the highest quality standards, manufacturers rely on testing and measurement devices to verify the accuracy and reliability of the parts they produce. One essential measurement tool is the flow meter station, which is used to measure the accuracy of flow rates in automotive systems.
Flow meters work by measuring the pressure or velocity of a liquid or gas as it passes through a tube. This data is recorded, allowing the user to accurately determine volumetric flow rates, which are vitally important for the proper functioning of engines, transmissions, fuel injectors, and other automotive systems.
Flow meter stations provide real-time data about system performance, so manufacturers can monitor their product as it goes through its manufacturing process.
Gas Metering and Regulator Operations
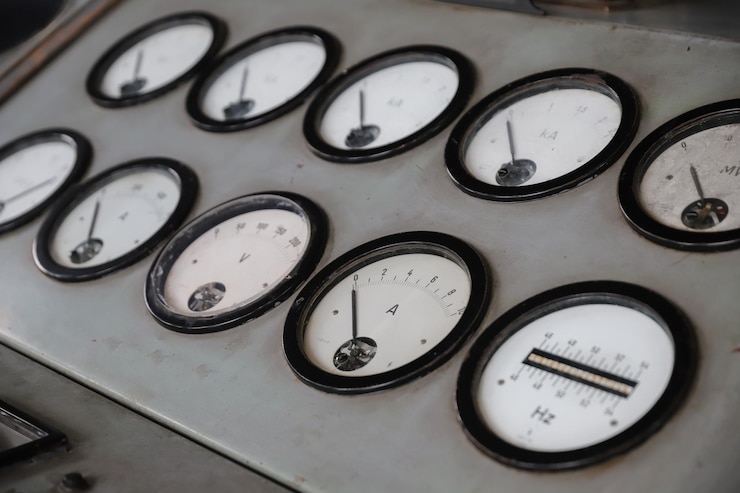
Gas metering and regulator operations are essential to ensuring the safe delivery of natural gas. Gas meters measure the amount of gas that has been used, while regulators maintain constant pressure in the system.
One of the components of gas metering and regulator operations is regulators. Regulators reduce the pressure from high levels in the pipeline to lower levels for distribution to the customer.
This low-pressure delivery is necessary to prevent damage to appliances and machines. Regulators also ensure that the flow rate is maintained at an acceptable level.
Gas meter and regulator operations must be monitored on a regular basis to ensure the safe delivery of natural gas. The accuracy of these systems must also be checked periodically, as errors can have serious implications for both safety and efficiency. It is important to regularly inspect piping, valves, regulators, and other components for signs of wear and tear or damage.
Gas Metering and Regulator Station Types
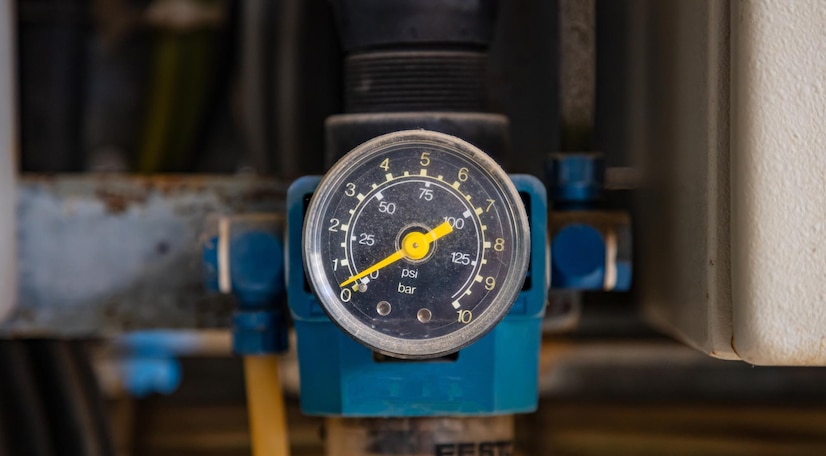
Automatic Shutoff Valves
One of the many types of gas valves that can be used in gas metering stations is the Automatic shutoff valve which is a useful safety feature in both industrial and residential contexts that can help to prevent accidents and property damage.
These valves are designed to close automatically when they detect high pressure, temperature, or flow rates that exceed predetermined levels, thus cutting off the flow of water or other fluids.
Pressure Reducing Regulators
Pressure-reducing regulators are used to controlling the pressure of a gas or liquid within a closed system. They work by regulating the flow of fluid within a pipe in order to maintain a desired steady pressure. These devices are typically used in industrial, commercial, and residential applications.
The primary purpose of these regulators is to keep the pressure acting on a system from becoming too high. This is particularly important for liquids and gasses in order to prevent damage and ensure safety.
Flow Meters
These are measurement devices used to measure the rate of flow of a liquid or gas. They are commonly used in many industries such as water treatment, petrochemical, and power generation.
Back Pressure Regulators
A back pressure regulator works by controlling the flow of a fluid so that the pressure behind the valve does not exceed a predetermined level. This is accomplished by using a spring-loaded diaphragm or disc, which opens or closes depending on the pressure of the fluid.
The mechanism is designed so that when the pressure of the fluid exceeds a certain point, the regulating device will constrict the flow and lower the pressure. In this way, it can regulate both pressure increases and decreases.
Vaporizers
This type of device become increasingly popular in recent years as an alternative to smoking. Vaporizers heat up plant material, such as herbs, tobacco, and wax, to create an inhalable vapor. Many people prefer using a vaporizer over other forms of inhalants because the inhalation process is less harmful than traditional methods of smoking.
Vaporizers range in size and style. The most common type is the personal-use model, which is designed for personal use and typically fits into a pocket or handbag
Differential Pressure Switches
Differential pressure switches are typically used in process control and instrumentation systems to detect changes in the differential pressure of a fluid in a pressurized system.
This type of switch is suitable for monitoring the pressure difference between two points, such as a liquid level in two tanks, or for detecting clogs in filters or pumps. Differential pressure switches can also be used in ventilation systems to detect changes in air velocity and pressure.
It works by using an external power source to operate an electrical contact that opens or closes when the set threshold differential pressure is reached.
Check Valves
Check valves, also known as one-way valves, are devices used to allow the flow of fluids in one direction only and prevent the reverse flow. They are a vital yet often-overlooked component in fluid systems as they serve the critical purpose of protecting pipelines and equipment in maintaining pressure integrity.
The valves are highly reliable and cost-effective, making them an important part of many industrial processes. It comes in many designs, the most common being swing check valves, disc check valves, ball check valves, and dual-plate check valves.
Allocation Regulators
Allocation regulators are a set of policies and regulations that govern the use and distribution of resources. It put restrictions on the use of resources to promote efficiency and equity.
By controlling supply and demand in the market, these regulations can ensure that resources are being used justly and adequately distributed. It also reduces competition between consumers, producers, and retailers to make sure everyone has access to resources at reasonable prices.
Solenoid Control Valves
Solenoid control valves are electromechanical devices used to regulate the flow of liquids and gasses. They are used for both industrial and commercial applications and can be found in all sorts of settings, from factories and garages to building plumbing systems.
A solenoid valve is composed of three main components – a solenoid coil, a plunger, and an armature. The current running through the solenoid activates the valve, allowing fluid to pass or not depending on how the valve is set.
By incorporating a butterfly valve, the solenoid control valve can effectively control the flow rate and regulate the pressure of the fluid in the system. Today, there are a number of prominent butterfly valves suppliers that also sell solenoid control valves that include integrated butterfly valves.
Magnetic Flow Meter Shutoff
This device, which consists of a magnetic coil, works by measuring the strength of the magnetic field in the flow of the fluid and then controlling the flow rate accordingly.
This type of device is commonly found in water treatment systems, wastewater treatment plants, chemical processing plants, and other places where precise flow regulation is necessary.
Equipment Used in Gas Metering Station
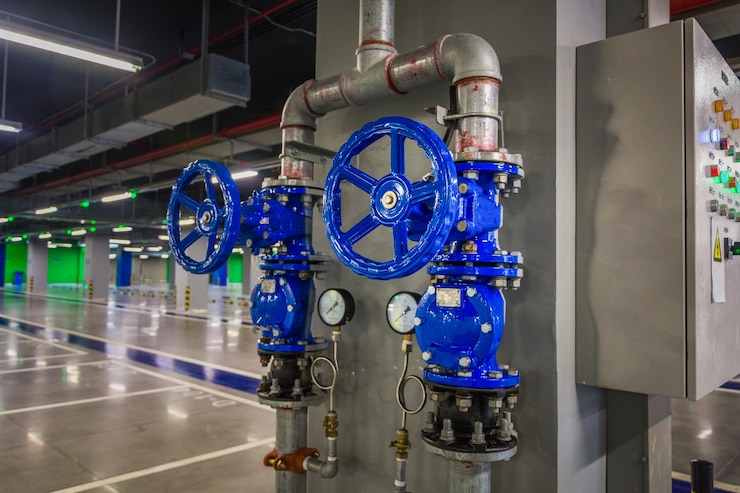
Gas Metering Station Piping
Gas metering station piping is responsible for safely conveying natural gas from one point to another, typically from the source to the consumer.
High-Pressure Gauges
They are an integral part of industrial processes that involve handling gases and liquids under very high pressure, such as those found in chemical plants, gas refineries, and natural gas lines.
These gauges come in a variety of sizes and styles, including dial and digital, to suit different requirements.
Rotary Turbine Meters
Rotary turbine meters monitor liquid and gas flow. Fluid dynamics cause the meter’s rotor to revolve. The meter’s fluid volume is calculated from the rotor’s rotating speed, which is proportional to the flow rate.
It has a cylindrical body, a multi-bladed rotor, and rotor bearings. Sensors capture the rotor’s spin as fluid flows through the meter. The meter’s total fluid volume is calculated from the rotor’s rotational speed, which is proportional to the flow rate.
Ultrasonic Flow Meters
Ultrasonic flow meters are an advanced technology solution for measuring the flow rate of liquids, gasses, and steam. They are designed to measure the velocity of a flowing medium by sending sound waves through it and detecting the time difference between them.
Gas Odorizers
Gas odorizers are devices used to add a distinctive smell to natural gas, propane, and other gasses to make them easier to detect in case of a gas leak. Natural gas and other gasses are odorless, making it difficult to detect a gas leak by smell alone. Adding a distinctive odor to the gas makes it easier to detect leaks and reduce the risk of gas-related fires and explosions.
Sampling Valves
Sampling valves are instruments used to take small volumes or samples of gas, liquid or powder from tanks, pipes, pumps or process lines for quality control. This helps in inspecting a sample before it is tested or processed further.
They come in various types and sizes depending on the material being sampled and the application it is meant for.
Filters
These are devices used to remove impurities, debris, and other particles from the natural gas before it is measured and delivered to the customer.
It plays an important role in maintaining the accuracy and reliability of the gas metering system, and they help to ensure that the gas being measured is free of contaminants that could affect the measurement accuracy.
Processor-Controlled Regulators
Processor-controlled regulators are capable of providing exceptionally precise control over gaseous or liquid substance flow in industrial environments.
Regulators with Relief Valves
They serve two key functions – to limit the pressure of a system and to protect the system from overpressurization. These regulators, when installed properly, help to ensure safety during operations.
Pressure Transmitters
This equipment is used to measure pressure and convert it into an output signal. These are used in a variety of industries for various applications, including process control, automotive, medical, aerospace, and industrial systems.
Shut Off Valves
Shut-off valves are units that can control, regulate or stop a liquid or gas from flowing. They are used in plumbing and piping systems to provide emergency shut-off of the flow of liquids and gasses, as well as for maintenance, repair, and adjustments to systems.
Other Primary, Secondary, and Auxiliary Devices
Secondary and Auxiliary devices are additional pieces of technology that provide further functionality to a primary device. These devices typically work in conjunction with the primary device either to perform additional tasks or increase the efficiency of existing tasks.
Primary Devices
The primary devices are the components used to measure and regulate the flow of natural gas. These devices typically include meters, regulators, filters, odorizers, and valves. They are used in combination to measure and regulate the flow of natural gas and ensure its safe and efficient delivery to the customer.
Secondary Devices
Secondary devices are components that provide additional functionality or support to the primary devices in the station. They work in conjunction with the primary devices to improve the efficiency, accuracy, and safety of the gas measurement and delivery process.
Some examples of secondary devices in a gas metering station include pressure transmitters, flow transmitters, control panels, data loggers, alarms.
These are some examples of secondary devices which play a role in improving the efficiency, accuracy, and safety of the gas measurement and delivery process.
Auxiliary Devices
Auxiliary devices supplement the primary and secondary devices by providing additional support or functionality. They collaborate with the other components to enhance the overall performance and safety of the gas measurement and delivery process.
Pressure regulators, filters, valves, heaters, and pressure and temperature sensors are examples of auxiliary devices in a gas metering station.
These are some examples of auxiliary devices in a gas metering station, and they are essential in enhancing the performance, efficiency, and safety of the gas measurement and delivery process.
Conclusion
Gas metering and regulating stations are essential components of a natural gas distribution network. It is responsible for measuring and controlling the flow of natural gas to ensure its safe and efficient delivery to customers. It is critical to understand all of the components involved in establishing a gas metering station, as well as their individual roles in the system.
From automatic shutoff valves, regulators, flow meters, check valves, allocation regulators, solenoid control valves, and magnetic flow meter shutoffs to sampling valves and pressure transmitters, these stations use a variety of equipment to guarantee the efficient operation of a system.
One of the valve manufacturers Dombor is a market leader in the manufacture of high-performance valves. They provide a wide range of valve solutions for the various gas metering systems that a consumer may have. The company’s valves have been certified for fire safety, low leakage, and other security features, and they have a high level of durability and tolerance due to their streamlined manufacturing process.
China valve manufacturer Dombor offers a wide range of valves for measuring and regulating gas flow in gas metering stations, all made from high-quality materials for dependable and long-lasting performance. Contact Dombor today to learn more about their high-performance valves that are available to meet the needs of any gas metering station.
FAQs
What is a gas meter pressure regulator?
A gas meter pressure regulator is a device that helps to maintain the pressure of gas flowing through pipelines. These regulators are found in both residential and commercial structures, and they play an important role in keeping the gas from entering through too high of a pressure which can be dangerous. Having a gas meter pressure regulator installed ensures that the gas enters the home or building at a safe, consistent pressure level.
What are the functions of a natural gas meter station?
A natural gas meter station is a specialized facility used in the delivery of natural gas. It serves as an interface between the main gas pipeline and the local distribution network, performing critical functions to ensure reliable and secure operation of the system. The primary functions of a natural gas meter station include measuring and regulating the flow of gas, controlling pressure in the pipeline, monitoring line integrity, providing emergency shut-off protection, and allowing access for service and maintenance.
What is the purpose of a gas regulator station?
A gas regulator station’s purpose is to ensure that natural gas is transported safely and efficiently from the transmission system to customers. By adjusting the pressure, the station makes it possible to maintain the integrity of the pipelines and protect the public and the environment.