Introduction to Hydraulic Check Valves
In the vast and complex machinery of life, where each component plays its pivotal role, hydraulic check valves stand as silent sentinels, ensuring that the lifeblood of machinery—hydraulic fluid—flows in harmonious unison. Imagine, if you will, a world where the rhythm of industry hums along, powered by these mechanical marvels. Check valves, in essence, are the guardians of fluid flow, preventing the chaos of backflow and preserving the integrity of a system’s pressure. As one immersed in the wisdom of years, I see the unassuming check valve not merely as a piece of hardware, but as the heartbeat of a hydraulic system. Without it, the very essence of control and order within would falter, leading to the possible demise of the hydraulic symphony.
The Role of Check Valves in Hydraulic Systems
Just like a carefully crafted narrative, a hydraulic system unfolds its power through a series of movements—extensions and retractions, pressure builds and releases. And at the core of this narrative are the check valves. They may seem mere footnotes in the grand scheme, akin to the commas and full stops in a story, yet without them, the flow would be uncontrolled, unpredictable, and potentially destructive.
The Basics of Hydraulic Check Valve Operation
How to Check Valves Function?
As we delve into the operational crux of a hydraulic check valve, picture a door that only swings one way. What a simple, yet profound concept. The valve allows the hydraulic oil to course through one direction, and just like a seasoned doorman, it denies entry the other way. This is achieved by what we call the “cracking pressure”— the minimum upstream pressure at which the valve will operate, allowing flow. To envision how crucial this is, let’s consider the human heart. Just as our heart’s valves prevent the reverse flow of blood, the hydraulic check valves ensure that the system’s lifeblood—hydraulic fluid—flows correctly, thus safeguarding the machinery’s vitality.
The Importance of Flow Direction
The direction of flow within a hydraulic system dictates how components interact, akin to dancers following a choreographed sequence. The check valve’s role is to maintain this dance’s directionality, making sure that each step is taken at the right moment, and no misstep occurs to disrupt the performance. Now, let’s embark on a journey through the various landscapes of hydraulic check valves, where each type holds its own story.
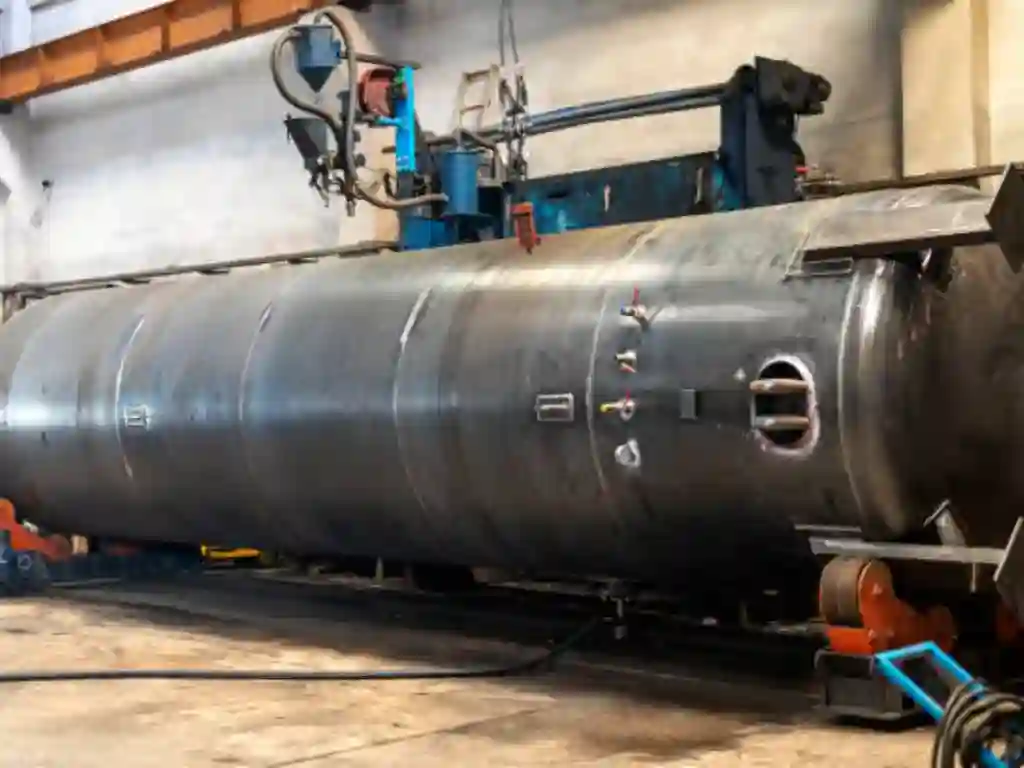
Types of Hydraulic Check Valves
Hydraulic systems are the lifeblood of many industrial applications, and within them, control valves are the guardians that ensure smooth operation. One of the paramount components in these systems is the hydraulic check valve. Let’s delve into the different types of check valves and understand their essence in fluid control.
Inline Check Valves
The most straightforward type of valve, these allow the flow of fluid in a singular direction. Boasting a simple design, they are ideal for compact systems. Given their small size, they exhibit minimal pressure loss, making them prevalent in applications where system pressure needs to be maintained without much drop.
Ball Check Valves
As the name suggests, these utilize a ball valve mechanism. When fluid seeks to reverse, the ball seals against a valve seat, preventing backflow. Think of water treatment plants, where ensuring a one-way flow is paramount. Here, the ball valves shine due to their efficient sealing against the unwanted reverse flow, even under high hydraulic pressure.
Swing Check Valves
Featuring a disc, these valves allow the flow rate to remain uninterrupted. The disc swings open when pressurized fluid is present and quickly closes upon flow reversal. Large Large volume systems, such as sewage pumps, adopt swing check valves since they can manage vast quantities without pressure loss.
Cartridge Check Valves
These are the mechanical device masters of high-pressure scenarios. Designed to fit snugly into a hydraulic application, they can tackle high system pressures while being effortlessly maintained. Industries with machinery that operates under immense hydraulic pressure, such as heavy-duty presses, predominantly use cartridge valves.
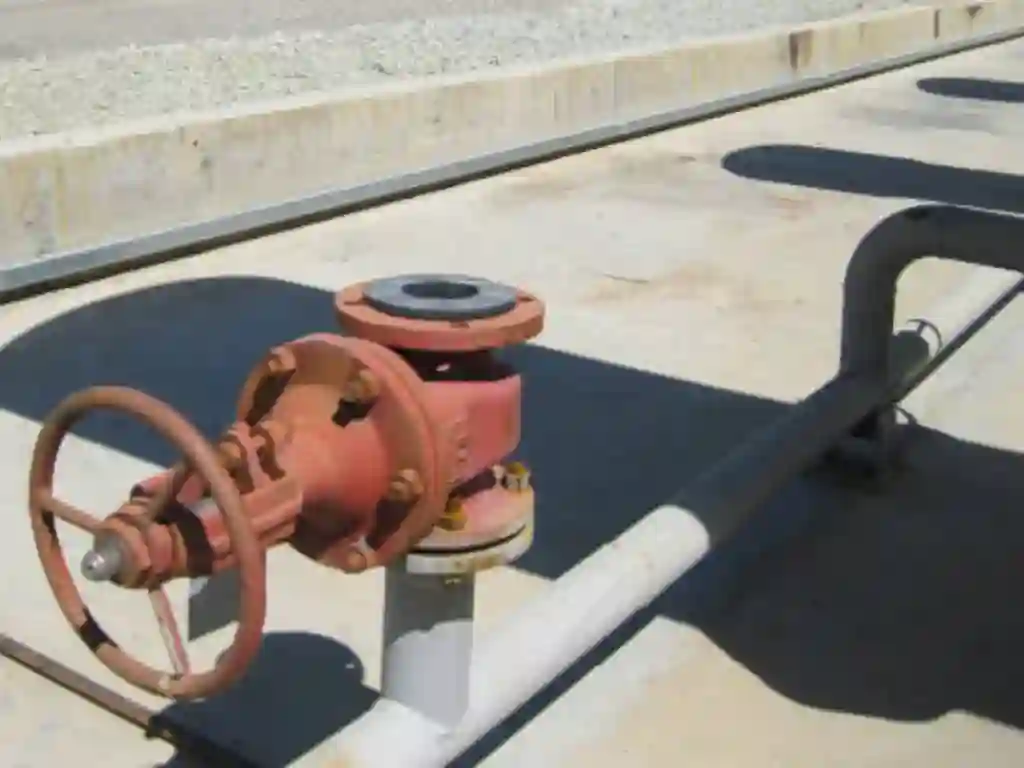
Pilot-Operated Check Valves
The beauty of these valves lies in their ability to be opened by external pressure. Complex hydraulic circuits, for instance in aerospace, need precise control over both flow rate and hydraulic pressure. These valves, with their specific cracking pressure, offer that exact control.
Cone Check Valves
Using a cone-shaped plunger, these valves can regulate flow even under intense hydraulic pressure. The oil and gas sectors, known for their high-pressure requirements, favor cone check valves for their reliability and robustness.
Flapper Check Valves
These come equipped with a hinged flap that responds to the flow of fluid. As the fluid moves forward, the flap opens; on flow reversal, it shuts. Due to their simplicity, they find their home in consumer-grade appliances, like sump pumps.
Directional Control Valves
Not strictly a ‘check’ valve, but an essential type of valve in the hydraulic world. As the most common directional control valve, its primary function is to dictate the direction of fluid flow. Their pivotal role in mobile hydraulics for heavy machinery can’t be understated.
Valve Type | Function | Key Feature | Common Application |
Inline | Directs flow one way | Simple design | Small hydraulic systems |
Ball | Prevents backflow | Tight seal | Water treatment plants |
Swing | Allows full flow | Minimal pressure drop | Sewage pumps |
Cartridge | Fits in a circuit | High-pressure capability | Industrial machinery |
Pilot-Operated | Controlled by external pressure | Precise flow control | Aerospace hydraulics |
Cone | Durable high-pressure control | Robust design | Oil and gas industries |
Flapper | Simple backflow prevention | Easy to use | Consumer appliances |
Directional Control | Directs fluid flow | Versatile application | Mobile heavy machinery |
Materials Used in Hydraulic Check Valves
Brass, Stainless Steel, and Cast Iron Options
Brass, with its golden hues, speaks of traditionalism and reliability, while stainless steel shines with its promise of strength and corrosion resistance. Cast iron stands stoic, embodying the age-old virtueof endurance in the face of high pressures, a testament to the robustness required in many a hydraulic system.
Aluminum and Its Applications
Aluminum, the lightweight contender in this material medley, brings forth the agility required in applications where weight is as critical as strength. Its use speaks of a modern touch, a nod to industries that value innovation and efficiency.
Understanding Check Valve Specifications
Size and Pressure Ratings
In the realm of hydraulic check valves, size and pressure ratings are akin to the tailored suits of the business world—each must fit its intended role with precision. Too small, and the valve will choke under the system’s demand; too large, and it becomes an inefficient use of space and resources. The pressure rating, meanwhile, must match the system’s highest demands to avert the specter of failure.
Cracking Pressure Essentials
The concept of cracking pressure in the world of check valves is akin to the first brushstroke on a canvas—it sets the tone for the entire system’s operation. It is the minimal pressure that prompts the valve to open, a critical factor that ensures the valve’s responsiveness and reliability.
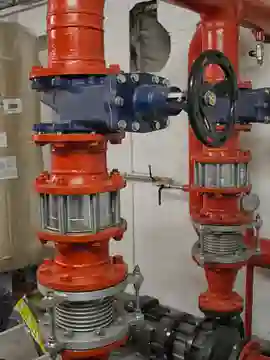
Applications of Different Check Valve Types
Industrial Uses
In the big world of factories and industry, check valves are super important to keep things running smoothly. These valves, especially the flow control valves, are key players in managing how fast or slow the fluid goes and keeping the pressure just right. Take a factory that uses big machines to move liquids around, for instance. They need to be sure the pressure is set just so. That’s where pressure relief valves come in to save the day, making sure nothing gets too pressured and causes trouble. Then, we’ve got hydraulic valves in things like hydraulic cylinders, which are part of the system in lots of machines. These valves make sure the fluid that’s pushed through is going just where it should, so everything works like a charm. They’re built tough to handle any pressure changes and keep the machine humming along for a long time.
Mobile Hydraulic Systems
Now, when we talk about mobile hydraulic systems like the ones you’d find in diggers on a construction site or tractors on a farm, the game changes a bit, but those check valves are still the stars of the show. These systems need the fluid to move just right to manage how the machinery lifts and moves all that heavy stuff. The hydraulic valve, and particularly the flow control valves, make sure the fluid’s moving at the perfect speed for the job. Let’s say we’ve got a hydraulic excavator—the hydraulic pump sends fluid to the cylinders to move the arm up and down. Any mess-up in pressure can really goof up the arm’s moves. That’s where pressure control valves step in, keeping the fluid’s pressure steady and making everything run without a hitch. These valves have got a big enough surface area to deal with all the action in mobile systems, making sure that even when things get tough, the fluid keeps flowing just right.
The Role of Check Valves in System Safety
Preventing Backflow and Contamination
Like a steadfast gatekeeper, the check valve stands guard, ensuring that backflow is a tale of fiction, not of reality, thus preserving the purity and functionality of the hydraulic system.
Pressure Control and Relief Mechanisms
In the event of a pressure surge, the check valve acts, not unlike a pressure relief valve, as a safeguard, a protector against the potential ravages of unchecked pressure spikes.
Selecting the Right Hydraulic Check Valve
Assessing System Requirements
Selecting the right hydraulic check valve is akin to choosing a companion for a journey. One must consider the path ahead, the challenges to be faced, and the qualities needed to overcome them. The system requirements are the map; the check valve, the chosen companion.
Compatibility with Hydraulic Fluids
The compatibility of a check valve with hydraulic fluids is as crucial as the compatibility of ink to paper. The wrong match can lead to degradation, contamination, and ultimately, system failure.
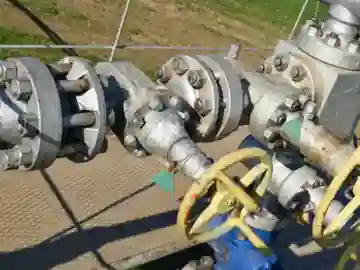
Installation Considerations for Check Valves
When you’re putting in a hydraulic check valve, it’s like making sure a door is tough enough to handle a strong wind without slamming shut and causing trouble. The valve’s house has to be strong to deal with the system’s set pressure without making a pressure drop that messes things up. Say you’ve got a valve in a high-pressure zone; the spring force inside must be spot on. This keeps the valve snapping shut right on time, stopping any backflow.Now, where you place the start (inlet port) and end (outlet port) points is super important. Get it wrong, and you might cause an excess pressure party, and nobody wants that—it’s bad news for the system. Picture this: you put the check valve in the wrong way around; no fluid can get through, and pressure builds up like a crowd at a closed store on Black Friday. This could totally wreck your system.So, really getting what the valve does and knowing the pressure of the fluid where it lives is key. Every valve is a piece of a bigger puzzle—a part of a circuit. And you’ve got to stick it in with a keen eye on which way the fluid’s going and the pressure it’s going to meet. This way, everything runs smooth and easy.
The Economic Impact of Valve Choice
Cost-Efficiency and Valve Selection
In the economic theater, the choice of a hydraulic check valve is a strategic decision, one that balances initial cost against the backdrop of operational efficiency and longevity.
Long-Term Financial Benefits of Quality Valves
Investing in quality valves is akin to planting a tree. The initial effort is rewarded by years of shelter from the storms of maintenance woes and system inefficiencies.
Conclusion: Integrating Check Valves into Your Hydraulic System
As we draw the curtains on our exploration, we reflect on the myriad of hydraulic check valve types—each with its own tale, its own role in the grand hydraulic narrative.
In conclusion, the selection and integration of the right hydraulic check valve types are not merely technical decisions but are choices that resonate with the rhythm of the system, the harmony of operation, and the melody of economic wisdom. In this journey through the world of hydraulic check valves, we have woven a tapestry of technical knowledge, practical insights, and the subtle art of selection. May this serve as a guide for you, the reader, as you craft your own narrative in the vast expanse of hydraulic systems.
Choose Dombor as Your Partner
Looking for top-notch hydraulic check valves? Check out DomBor! Since 2001, they’ve been crafting custom valves that really last. They use the latest tech and seriously tough equipment, so their valves can handle even the toughest jobs. Perfect for places like refineries and mines. Plus, they’ve got a huge range of products, all meeting strict global standards. And get this, they offer everything from custom orders to quick delivery and expert help after you buy. With their ISO-certified quality and a bunch of other certifications, you can trust DomBor valves to do the job right. Give ’em a try for your valve needs!