Valves are essential components of a fluid control system, and their proper functioning is critical to ensure system efficiency and longevity. Cavitation in control valves is a common problem that can significantly impact the valve’s performance and lifespan.
Unanticipated cavitation can cause deep havoc by destroying the control valve’s internals and even lead to catastrophic system failure. Hence, it’s important to understand what valve cavitation is, its causes, effects, and possible mitigation measures.
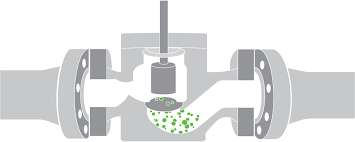
What is Valve Cavitation
Valve cavitation refers to the rapid formation and collapse of vapor bubbles that occur when the pressure of a liquid flowing through a valve drops below its vapor pressure. This phenomenon generates high-frequency pressure waves that can cause damage to valve components, create noise and vibration, and reduce system efficiency.
Valve cavitation damage can also be in the form of erosion and pitting on valve components, leading to leaks, reduced flow rates, and decreased control accuracy. Contacting industrial valve manufacturers to implement anti-cavitation valve measures is crucial to maintain system performance, minimize damage, and extend valve life.
Valve Cavitation Data
Cavitation in valves can be quantified by measuring the sound and vibration levels generated during operation. High-frequency vibrations and noise levels are typical indicators of valve cavitation. These measurements can provide valuable information about the severity of cavitation and help identify potential damage to valve components.
There are three basic levels for valve cavitation calculation, which are:
- Incipient: The cavitation beginning stage where intermittent popping noises are heard.
- Constant: A consistent rumbling sound associated with the start of the valve’s damage.
- Choked: The vaporization of the fluid attains sonic velocity in the valve’s port and restricts the smooth flow through the valve.
Considering quarter-turn valves like industrial butterfly valve and control valves, it’s best to use constant cavitation when judging the effect of cavitation on the valve’s lifespan. For quiet operation, incipient cavitation data is best. Choked analysis should only be used with special valves that have cavitation trim.
What Cavitation in a Control Valve is Caused by
Cavitation in control valves is caused by several factors, including:
- High Velocity: If the liquid flowing through the valve is traveling at a high velocity, it can create low-pressure areas that cause vapor bubbles to form. This is particularly true if the liquid is forced through a small opening, such as a narrow valve opening.
- Pressure Drop: As the liquid flows through the valve, there is often a pressure drop between the inlet and outlet. If the pressure drop is too high, it can cause the liquid to vaporize, leading to cavitation.
- Temperature: High temperatures can increase the likelihood of cavitation, as they can cause the liquid to reach its boiling point at a lower pressure.
- Liquid Properties: Certain liquids are more prone to cavitation than others. For example, liquids with a low vapor pressure or high viscosity are more likely to experience cavitation.
- Valve design: The design of the valve can also play a role in cavitation. If the valve has sharp edges or abrupt changes in direction, it can create turbulence in the liquid flow that can lead to cavitation.
How Does Cavitation Affect Control Valves
Cavitation in a control valve can lead to reduced efficiency, increased maintenance costs, and even valve failure. The rapid formation and collapse of vapor bubbles can cause erosion and pitting on valve components, leading to leaks, reduced flow rates, and decreased control accuracy.
This can affect the ability of the valve to maintain the desired flow rate, pressure, or temperature and may result in system instability or poor process control. In severe cases, you will need valve components, like seats, plugs, and stems that become damaged or even disintegrate due to the impact of the collapsing vapor bubbles.
Cavitation can also generate excessive noise and vibration, which can be harmful to system components and personnel. The high-frequency pressure waves can cause valve components to vibrate, leading to mechanical wear and potential failure. Excessive noise levels result in interference with communication, disruption in work environments, and violation of noise regulations.
Cavitation Prevention Solutions in Control Valves
Prevention of cavitation in control valves is important to ensure their proper functioning and avoid potential damage to the system. There are various anti cavitation relief valve approaches, but they can be categorized into two – avoidance and design.
Avoidance
The best anti-cavitation valve measure is to avoid it altogether. These are the measures that can be implemented.
- Reduce fluid velocity: One of the primary causes of cavitation is high fluid velocity. Therefore, reducing the velocity of the fluid by increasing the pipe diameter or reducing the flow rate can help prevent cavitation.
- Increase system pressure: Another way to prevent cavitation is to increase the system pressure, which will reduce the pressure drop across the valve and minimize the likelihood of cavitation.
- Modify the fluid properties: Changing the fluid properties, such as viscosity or temperature, can also help prevent cavitation.
- Select the right valve: Partner with a reliable valve supplier for a valve that is better suited to your specific application. For example, selecting a valve with a larger capacity, a different trim material, or a different type of valve can help reduce the likelihood of cavitation.
Design
If cavitation is unavoidable, then the valve must be designed to handle it and minimize the effects. This can be achieved using three anti-cavitation relief valve measures. Oftentimes, two or even all of these measures are implemented in valve designs.
- Robustness: This involves the use of high-strength materials for manufacturing the critical parts of the valve that will encounter cavitation. While cavitation may ultimately damage the internal components of the valve, robust materials will help resist the damage for a longer period of time.
- Isolation: This involves diverting or directing the collapsing bubbles toward the middle of the flow stream where microjets and shock waves cannot damage the valve components.
- Elimination: This involves reducing cavitation by taking the pressure drop severally rather than all at once. A single pressure drop often has a larger dip, resulting in drops below the liquid vapor pressure. But if the pressure drop is taken in series like three to four times, the pressure dip will be eliminated, and the pressure remains above the vapor pressure.
Select the Right Valve Manufacturer to Avoid Cavitation
Selecting the right valve manufacturer is very important as it influences the reliability of your valve in preventing cavitation. Dombor Valve is a professional and experienced manufacturer of all kinds of control valves that are applicable in various industries. Having an expert R&D team with vast knowledge about curbing cavitation, the valves produced are extremely durable and functional.
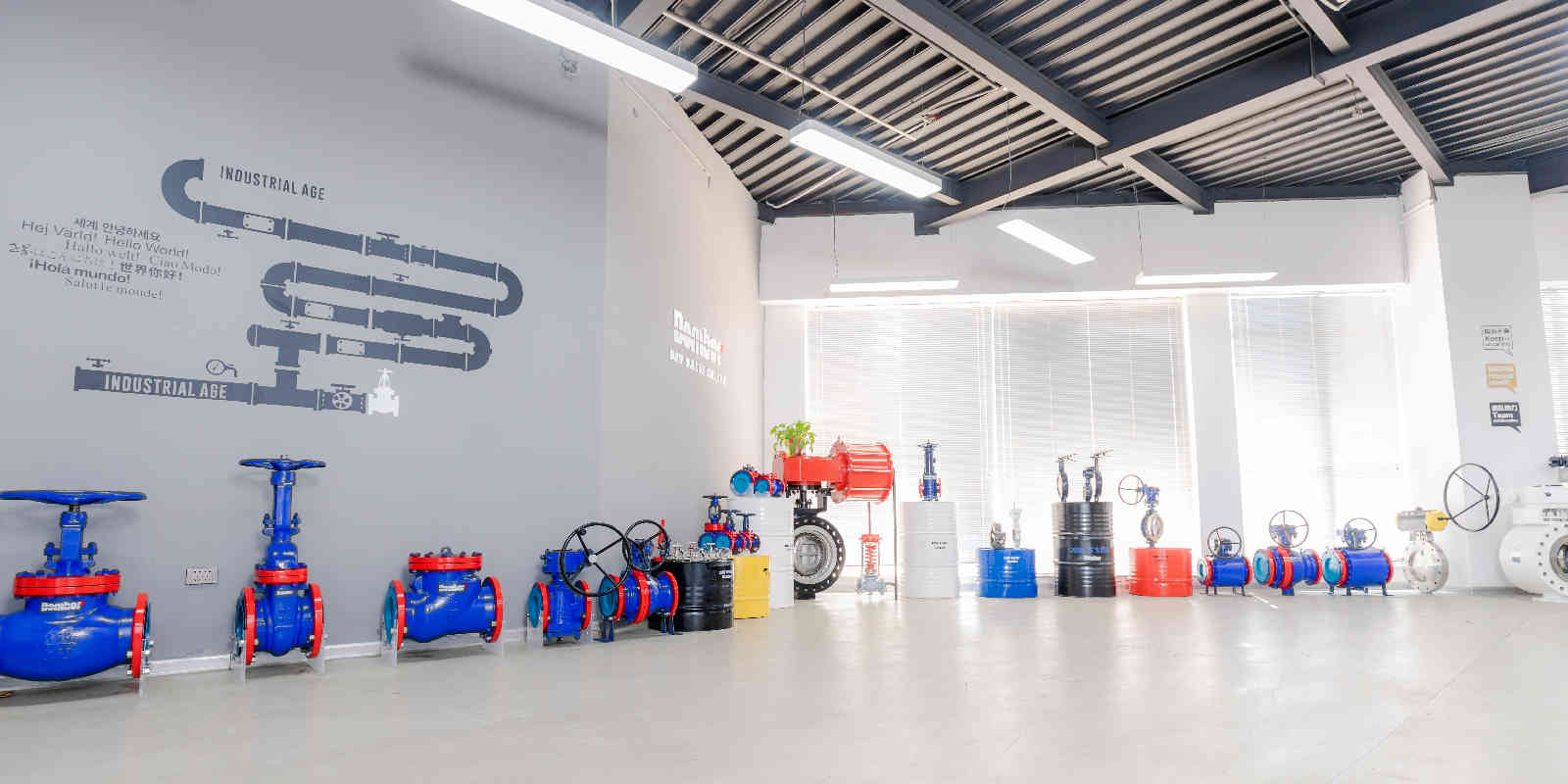
This makes us stand out among the competition, including industrial ball valve suppliers on the market. We have a reliable supply chain, which ensures only high-quality materials that are compliant to industry standards are used. With this, we provide you with valves that are resistant to cavitation, allowing for system efficiency and reduced maintenance cost.
Conclusion
Valve cavitation is a significant problem in many fluid systems that can result in equipment damage, reduced efficiency, and safety hazards. Understanding the causes and effects is critical to effectively managing it.
Proper anti-cavitation valve selection, design, and maintenance can help mitigate the impact of cavitation. Overall, the prevention of valve cavitation requires a comprehensive approach that involves understanding the root causes, implementing appropriate prevention measures, and regularly monitoring and maintaining the system to ensure its optimal performance.