Fluid power refers to hydraulic and pneumatic technologies that transfer power from one area to another using a fluid, either a liquid or a gas. These are different methods of power transmission that transform energy into usable energy and transfer it to the required locations.
Hydraulic, electrical, and mechanical power are the three most popular ways to transmit power. The fluid power systems can be utilized in almost any field or situation. However, it is most frequently used in mining, packaging, medical, offshore/marine, aerospace, construction, robotics, automation, etc. Acquiring the fluid systems from reliable valve manufacturers like Dombor valve is the best bet.
What Is Industrial Fluid Power System
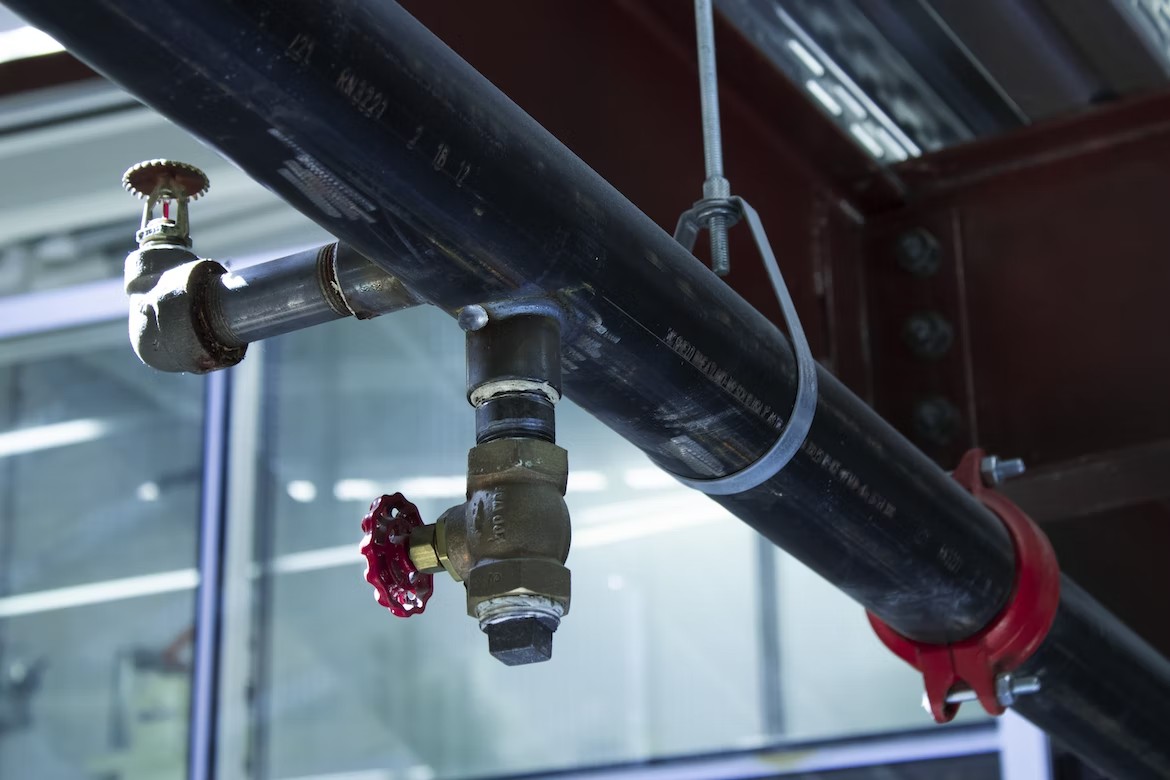
The fluid power systems are classified into pneumatic (gas) and hydraulic (liquid). Industrial fluid power systems are utilized to transmit power and control motion for industrial machinery. They are utilized in a wide range of applications, including heavy machinery, robotics, construction, and automobile braking systems.
The hydraulic or pneumatic cylinders that are used in fluid power systems provide linear motion. With the usage of transducers, sensors, and microprocessors, fluid power systems can be efficiently associated with other technologies. At low speeds or when locked, fluid power motors and cylinders will not overload. They carry less risk of unintentionally igniting flammable environments.
In comparison to electric systems, fluid power control systems are frequently simpler to understand and rectify errors. They can be utilized without risk in submerged or underwater settings. The fluid power systems made by a dependable industrial ball valve manufacturer poses a low risk of fire, arc flash, etc. It is utilized in commercial and military aircraft applications and also in power mobile equipment.
Compared to electrical or mechanical drives, fluid power systems normally retain a much tinier physical footprint. Additionally, they provide precise and efficient speed, force, direction, and torque control through the use of control valves. Since electrical power is frequently not needed for fluid power systems, there is little to no danger of sparks, electrical shock, or explosions.
Components Of Industrial Fluid Systems To Ensure Safety
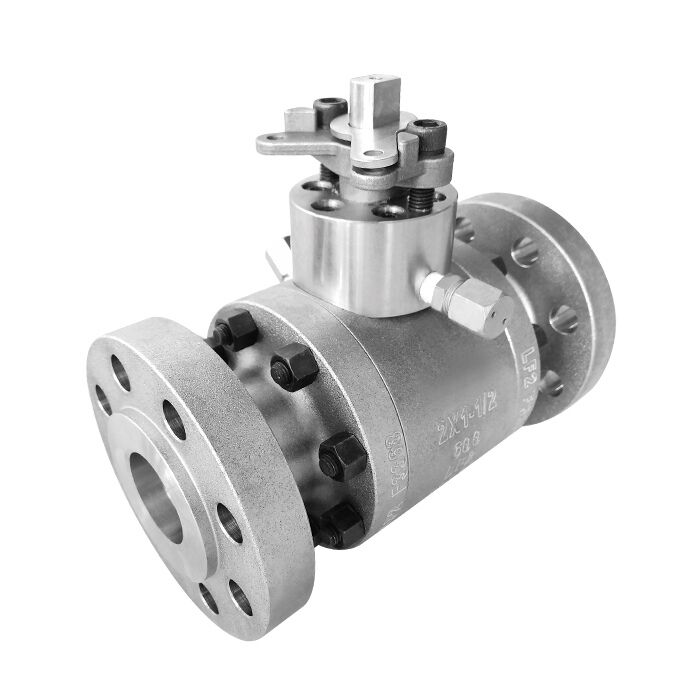
The fluid power process system retains several components like cylinders, pumps, valves, fittings, hoses, gauges, filters, sensors, seals, reservoirs, etc. Nevertheless, the main components of the hydraulic and pneumatic fluid power systems comprise the reservoir/receiver, valve, pump/compressor, and actuators.
- Reservoir
The hydraulic and pneumatic reservoir stores a certain amount of liquid or gas, removes heat, permits solid pollutants to occupy, and makes it easier for the fluid to discharge air and moisture. A reservoir or tank holds the fluid needed to power the fluid system. Based on the fluid system and application, the reservoir’s size will change.
Aeration and other issues such as trapped air in the fluid will arise. Thus, the reservoir is made to release trapped air and cool pressurized liquid. Additionally, additional room is built into the system to prevent overfilling. The reservoir’s maximum fill level is set by the rim at the filler neck. It is also possible to deter overfilling by inspecting the fluid level.
- Pump
Mechanical energy is converted into hydraulic energy by the hydraulic pump which is accomplished by fluid movement. Hydraulic pumps come in a variety of designs, including vane, piston, and gear. Each of these pumps comes in a variety of subtypes intended for particular uses.
In pneumatic systems, a compressor or pump lowers the volume of air to raise the pressure. This pump may run on either gas or electricity and it increases the PSI of the air compression. Before the air is discharged into the pneumatic track, compressors retain a tank attached to store it. One particular type of gas compressor is an air compressor.
- Valve
In a hydraulic system, industrial valves control the flow of fluid, steer it through the system, and manage fluid pressure. The industrial butterfly valve models with mechanical, electric-solenoid, and pilot operation are all readily accessible. Three significant types of hydraulic valves are pressure control valves, directional control valves, and flow control valves.
The airflow in pneumatic systems is handled by valves to make sure that the air discharged is at the proper pressure for the machinery. The pipe that links the compressor to the buffer tank has one-way valves attached to it. While deterring backflow into the compressor tank, they allow compressed air to accumulate in the buffer tanks.
- Actuators
Actuators are utilized in hydraulic systems to transform fluid power into mechanical power. The actuators receive pressured hydraulic fluid from the hydraulic pump, which transforms the fluid’s energy into mechanical energy. There are various kinds of actuators, including rotary actuators (hydraulic motors) and linear actuators (hydraulic cylinders).
Actuators in pneumatic systems convert potential energy that has been reserved in the reservoir back into kinetic energy. Generally, they employ a piston to propel them forward and backward. Pressurized air is used to power several different kinds of actuators. The cylinder and plunge types are most often utilized.
How To Control Industrial Fluid System
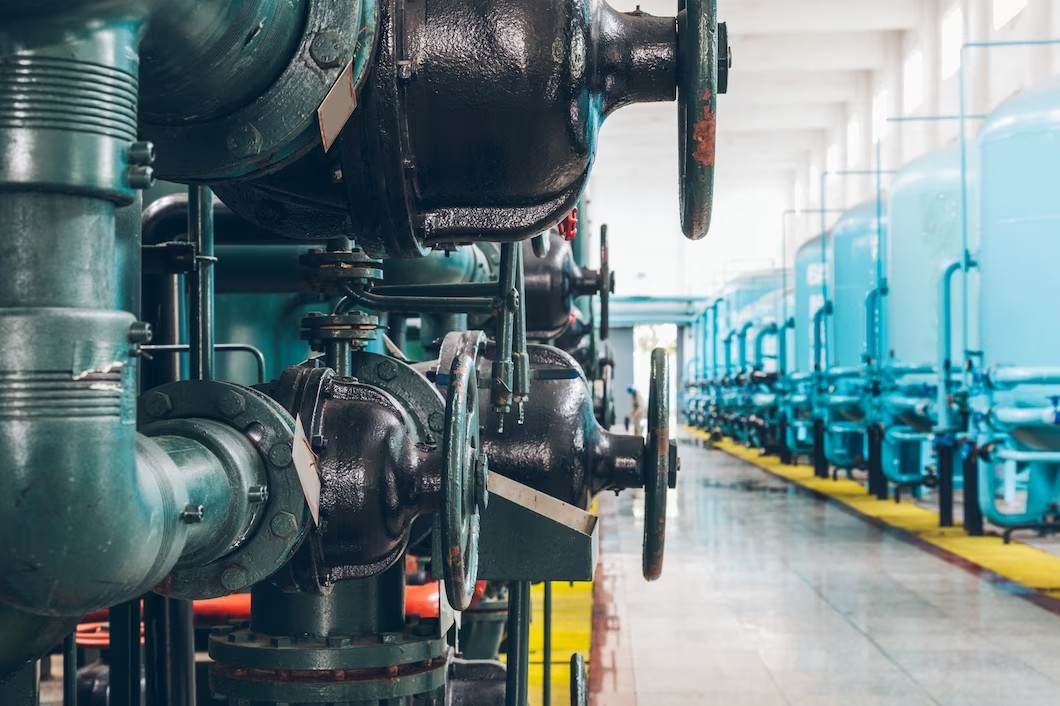
It is vital to know how to control industrial fluid systems so that they operate fully at their best performance.
- Stick To Simple Designs
Potential difficulties can be lessened by simplifying the fluid system. The fluid power and controls that are simpler are also more efficient to maintain because technicians can solve issues quickly as there will be less components. For instance, to lessen potential leak locations, it is better to switch piping runs to bendable tubes.
- Acquire Required Components
It is crucial to choose the right materials and components to deter corrosion in fluid systems. Understanding all aspects of the procedure is necessary for choosing the best components. Future leakage can be avoided with the right material and component selection manufactured by a top-notch industrial valve supplier.
- Ensure Component Safety
In order to enable operators to make precise changes, make sure to add comprehensive tags on the machinery and hoses that describe what occurs within the system. In order to reduce the chance of unintentional contact with moving objects, it is also better to install extra components.
Additionally, color coding tubes, handles, and pipes can help personnel in your facility quickly recognize the fluids or gases passing through them, minimizing the possibility of mistakes. A lockout can be added to a crucial process valve to help avoid unintentional activation and get rid of any safety issues.
- Consider Working Conditions
During routine operations, vibration, pressure changes, and temperature variations all take place. As a result, one should confirm that these concerns were taken into account when designing the system. To prevent tubes and fittings from becoming too drained during high-pressure operation, use the appropriate supports. As motion can weaken parts and connecting points, give moving parts an appropriate range of motion. If there will be a lot of vibration during regular operation, utilize a hose rather than tubing.
- Avoid Using Different Brand Components
Not all industrial parts are created equally. By using and combining parts from several brands, there is a risk of environmental discharges, unreliable performance, compatibility issues, safety issues, higher prices, etc. The ideal option is to select a dependable fluid system component manufacturer that produces high-quality fluid power items.
- Internal Environment
Unreliable performance, machine downtime, and component failure can result from improper internal temperature regulation during production. About 90% of the production time for industrial fluids will be spent in reservoirs. Consistency at the point of usage is ensured by complete temperature control at this phase. In addition, it can help operators improve fluid performance, get rid of fluid-related component failure, and cut down on waste.
- External Environment
The fluid performance can be especially affected by the production environment, primarily the temperature. To lessen the effects of the outside world, make sure the liquid is kept near the dispenser. By doing this, the amount of time the fluid spends outside of a controlled environment will be greatly reduced. Also, the insulated feed pipes can lessen temperature changes even further.
- Connection Leakage
Verify that no connections have leaks. Incorrect installation, such as not completely sticking in tubing, over-tightening connections, loose connections, or placing bends very near to the tube’s end, frequently leads to leaks. Besides, pipe or tube components that have surface flaws or are of poor quality can all result in leaks.
Conclusion
The applications of fluid power systems are relatively wide as they are used in several industries, including industrial machinery, electronics, aerospace, etc. Acquiring the ideal parts for the fluid power systems is essential to ensure their performance.
It is best to order fluid power system components from a reliable manufacturer so that they will be durable and last for an extended period. Make sure to contact valves manufacturer Dombor for purchasing industrial valves for the hydraulic and pneumatic system at an affordable price.