What Is Socket Weld?
A socket weld is a type of welding joint typically used to connect small diameter pipes. This method involves two different sized pieces of pipe, where the smaller pipe is inserted into the larger one. A fillet weld is then applied around the joining area to secure the connection. This welding technique is relatively easy to install, only requires basic welding skills, and does not necessitate intensive surface preparation. Despite its simplicity, socket welds offer considerable strength and excellent corrosion resistance, particularly useful in high-stress conditions.
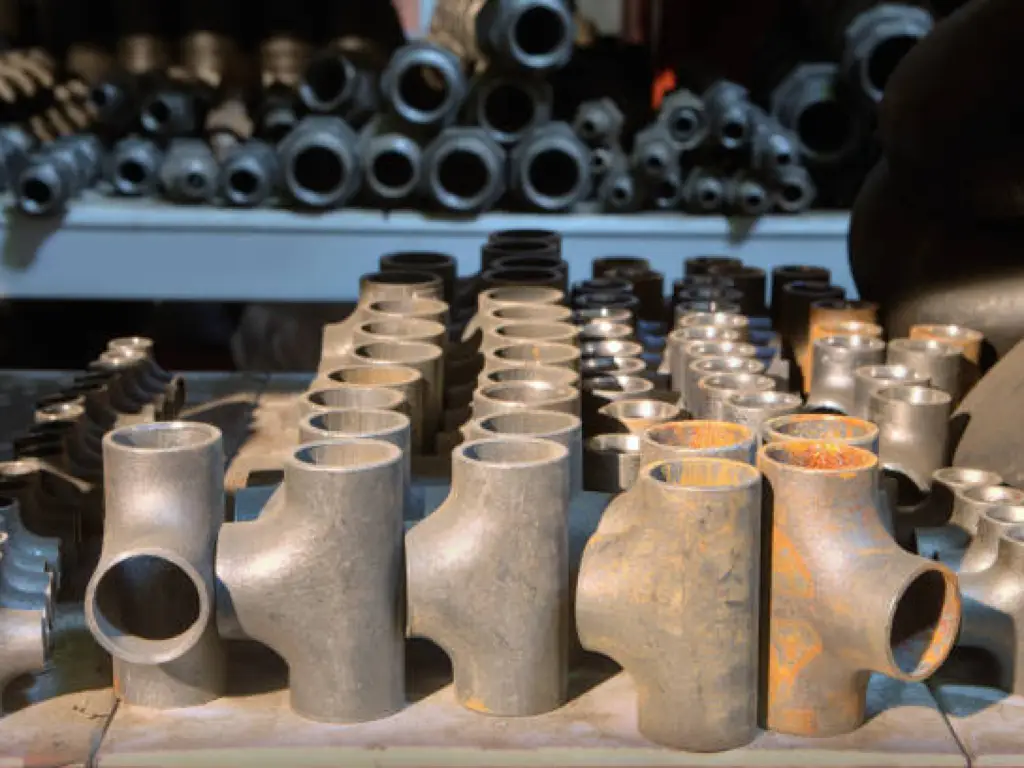
What Is Butt Weld?
Butt welding, on the other hand, involves connecting two similar sized pieces of pipe end-to-end, hence the term ‘butt’ weld. Unlike socket welds, butt welds require more precise surface preparation including beveling the pipe ends to improve weld penetration. When executed correctly, butt welds create a continuous, leak-proof system with impressive strength and integrity, making them suitable for high pressure or temperature applications. Although butt welding demands a higher level of welder skill, it provides a robust connection, excelling in terms of strength, fatigue resistance, and corrosion resilience. This type of weld is commonly used in the construction of pipelines, pressure vessels, and other industrial applications.
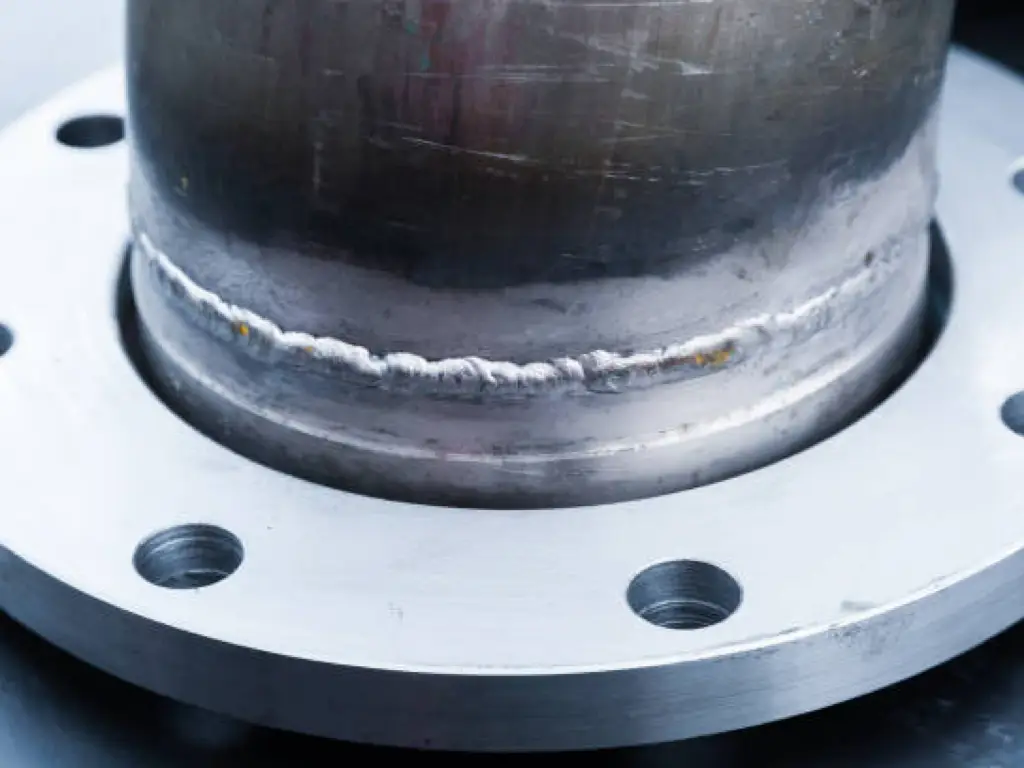
Socket Welds vs Butt Welds: What Are Their Differences?
Dimension | Socket Welds | Butt Welds |
Strength | Adequate strength for smaller diameters | Superior strength, suitable for larger diameters and high pressure systems |
Corrosion Resistance | Acceptable corrosion resistance, but potential for crevice corrosion | Excellent corrosion resistance, especially in critical or corrosive environments |
Surface Preparation | Less extensive surface preparation required | More intensive surface preparation, including beveling |
Welding Complexity | Easy to install, requires basic welding skills | More complex installation, higher level of welding expertise required |
Joint Integrity and Leakage Risks | Generally high, but potential leakage if not installed correctly | Reduced risk of leakage with proper installation |
Cost | Expensive fittings, but simplified design process | Lower material cost, but higher labor and skill requirements |
Industry Standard and Code Compliance | Compliant with ASME B16.11 | Compliant with ASME B16.9 |
Applications and Suitable Industries | Small diameter pipelines, change in direction applications | High-pressure and high-temperature systems, large diameter pipelines |
Non-Destructive Examination (NDE) | Magnetic particle testing, Penetrant testing | X-ray inspection |
Welder Skill Level and Training Requirements | Basic welding skills required | Higher level of welding skill and training required |
Performance in High-Pressure Environments | Suitable for low to medium pressure | Excellent performance, suitable for high-pressure systems |
Ease of Installation | Relatively simple and faster installation | More complex and time-consuming installation process |
Ends
Socket WeldsSocket welds utilize a socket weld flange that joins pipe fittings and pipes. The smaller piece of pipe is inserted into a recessed area of the larger pipe, and a fillet weld is applied to create a secure joint. Unlike butt welds, socket welds do not require beveled ends for welding. This simplifies the installation process and reduces the need for extensive surface preparation. However, it is essential to ensure a proper fit between the socket and pipe to prevent leakage and maintain joint integrity, especially when using sockolet or socket weld fittings. The use of sw fittings is common in industries such as oil and gas, chemical, and petrochemical.Butt WeldsIn contrast, butt welds require beveled ends to facilitate welding and ensure proper penetration of the welding bead. The bevel angle typically ranges from 30° to 37.5°, allowing for effective fusion between the workpieces. The beveling process adds complexity to the surface preparation, but it is vital to create a strong and robust joint. The proper alignment of the beveled ends is crucial for achieving a fully penetrated weld and avoiding potential defects, including the expansion gap. Another option for creating a strong joint is to use a weldolet, which eliminates the need for beveling and simplifies the welding process.
Welding Seams
Socket WeldsSocket welds primarily utilize fillet welding seams, including the fillet weld of the fitting. A fillet weld forms a triangular cross-section along the joint, providing sufficient strength for smaller pipe diameters. The fillet weld is relatively simple to execute, making socket welds accessible for welders with basic skills. Non-destructive testing methods such as magnetic particle testing and penetrant testing can be used to ensure the quality of socket welds.
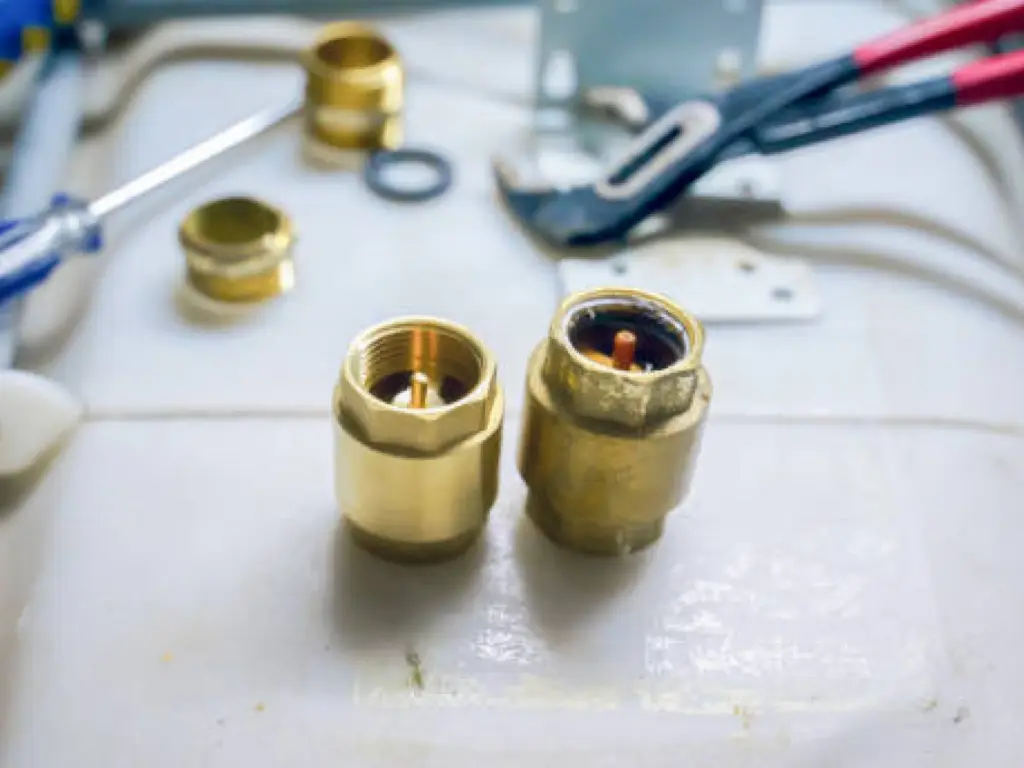
Butt WeldsButt welds, on the other hand, employ butt welding seams. Butt welding involves joining the two pipe ends by aligning them precisely and applying heat to create a molten pool of weld metal. As the weld solidifies, it forms a continuous joint along the entire length of the workpieces. Butt welds require careful control of parameters such as heat input, alignment, and filler material to achieve proper fusion and integrity throughout the weld. Non-destructive testing, such as radiographic inspection, is commonly used to examine butt welds for any defects or discontinuities. The use of bw is crucial in achieving a strong and reliable butt weld joint.
Strength and Durability Comparison
Socket WeldsSocket welds offer their own pros in terms of substantial strength and durability, particularly when applied to smaller diameter pipes. The absence of welding filler material enhances the joint’s strength, making socket welds less prone to failure under high-stress conditions. This characteristic is especially valuable in applications where reliability and structural integrity are critical, and where saving much time is essential. Additionally, socket welds exhibit good fatigue resistance and can withstand moderate levels of external forces and vibrations.However, it is important to note that the strength of a socket weld is typically around half that of a butt weld. Therefore, socket welds may not be suitable for extremely high-pressure systems or large diameter pipelines where the strength requirements are significantly higher.Butt WeldsButt welds are widely recognized for their exceptional strength and durability, ensuring temperatures compliance. By joining the two workpieces through full penetration welding, butt welds create a joint that is equivalent in strength to the base metal itself. This makes them highly suitable for high-pressure applications, such as pipelines and systems subject to significant mechanical stress. Butt welds provide excellent resistance to fatigue, withstanding repetitive loading and cyclic forces without compromising the integrity of the joint. However, there are some cons to consider, as the discontinuity of the smooth pipe internals can cause turbulence and pressure drops, which can lead to increased energy consumption and decreased efficiency.The strength and durability of butt welds make them the preferred choice for critical infrastructure, where safety, reliability, and long-term performance are paramount.
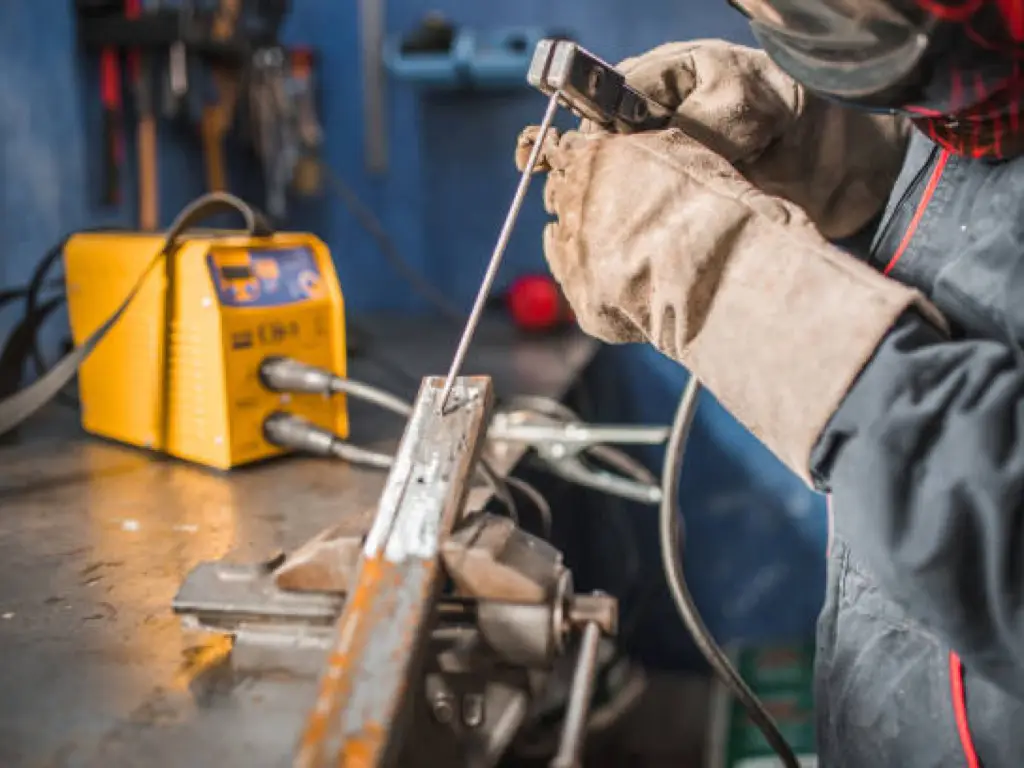
Corrosion Resistance
Socket WeldsSocket welds have acceptable corrosion resistance, especially when constructed using corrosion-resistant materials. However, the crevice between the larger and smaller pieces of pipe in socket welds can be a breeding ground for corrosion under certain circumstances, such as when transporting corrosive fluid service. Therefore, socket welds may not be ideal for systems containing fluids that are sensitive to contamination or cause corrosion.Butt WeldsButt weld fittings offer superior corrosion resistance, as they yield a smooth and continuous path without any crevices that might induce corrosion. They are usually the preferred choice for corrosive or high-purity applications. Special alloys or stainless steel can be used to enhance the corrosion resilience of butt weld fittings, making them suitable for a wider range of applications, including those that require compliance with ansi standards.
Size and Diameter Considerations
Socket WeldsGenerally, socket welds are an excellent option for small-diameter pipes, typically those under DN50. Despite requiring the use of high-cost fittings, the socket weld technique benefits from its simplicity, lending itself well to small scale applications.
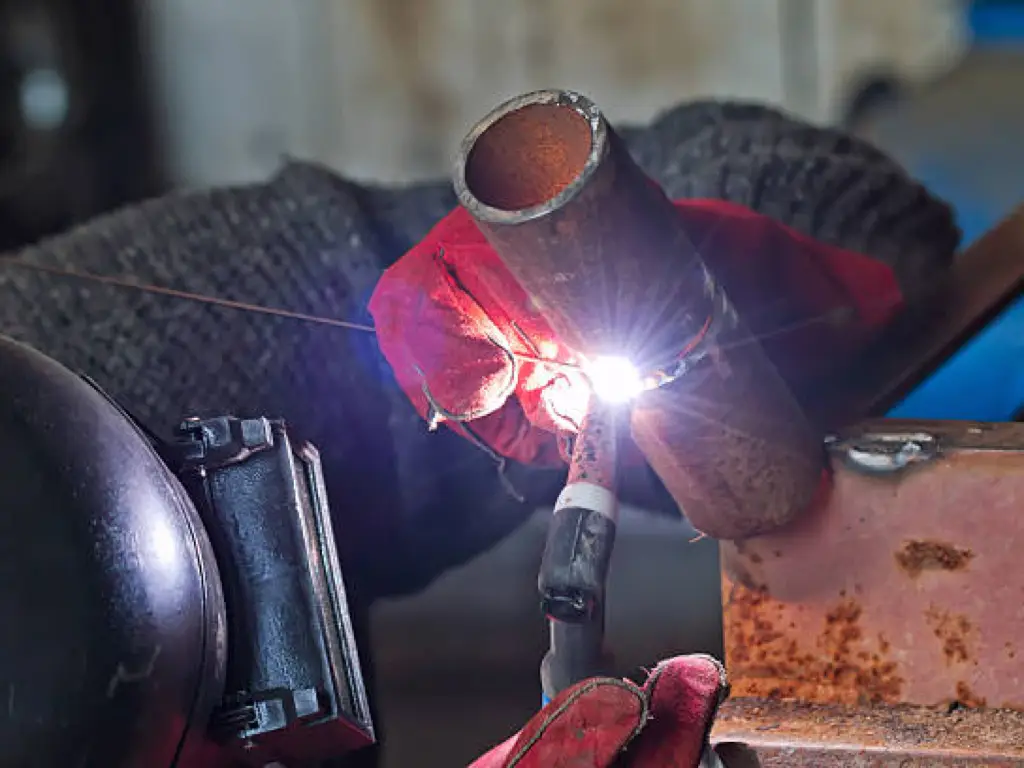
Butt WeldsButt welds, conversely, are a preferred choice for larger pipes because of their superior strength. They can handle the greatest diameter and high-pressure systems, delivering leak-proof and robust connections under all conditions.
Surface Preparation and Welding Techniques
Socket WeldsSocket welds require less intensive surface preparation compared to butt welds. The pipes and fittings are simply cut square, and the exterior surfaces are cleaned prior to installation.Butt WeldsButt welds require well-prepared surfaces for effective welding. As the thickness of the parent metal increases, beveling becomes necessary to promote better weld penetration. When both sides of a joint are accessible, full penetration through back-gouging ensures improved weld root integrity.
Installation Complexity and Speed
Socket WeldsSocket welding is relatively uncomplicated, faster to install, and does not demand high welding skills. It’s less complex, making the operations easier to manage and reducing the overall timeline of your project.Butt WeldsButt welding, on the other hand, demands a high degree of skill and precision. The installation process is more complex and involves more extended periods, resulting in a slower operation speed.
Joint Integrity and Leakage Risks
Socket WeldsThe joint integrity of socket welds is generally high due to the fillet weld created during installation. However, a notable risk associated with socket welds is leakage if the fitting isn’t installed correctly. An inadequate gap for thermal expansion or any misalignment of the pipes can contribute to joint failure and potential leakage. It’s crucial that quality management measures are in place to ensure correct installation and maintain joint integrity.Butt WeldsWith butt welds, the integrity of the joint is often superior to that of socket welds. The preparation and execution of butt welds, though intricate, ensure a fully penetrated and robust joint. Risks of leakage are reduced, as the joint is often as strong as the parent metal, provided the weld has been accurately executed. This makes butt welds appropriate for high-pressure systems where a leak-proof connection is paramount.
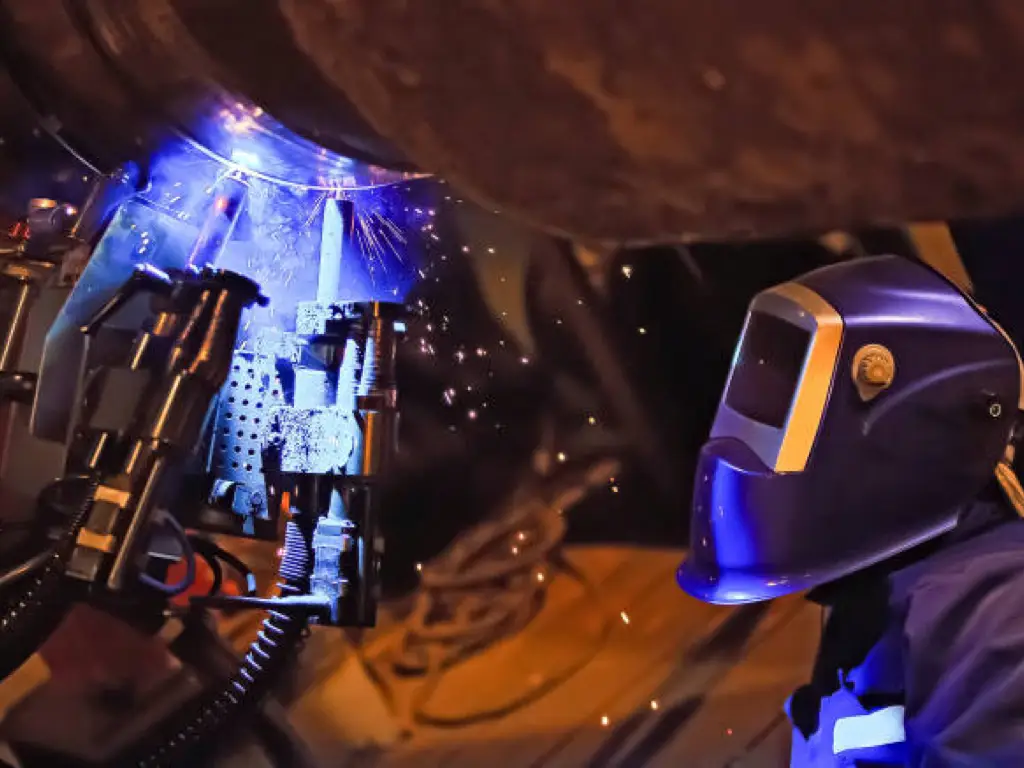
Cost Analysis
Socket WeldsDespite being simpler to install, the price of socket weld fittings can be costlier than butt welds because of the expensive fittings required for their assembly. However, the simplified design process and lower skill level required can offset this cost.Butt WeldsThough butt welds are typically less expensive in terms of materials, the higher skill level required and the more intensive surface preparation can lead to higher overall costs, particularly for large-scale projects.
Industry Standard and Code Compliance
Socket WeldsSocket weld pipe fittings must comply with ASME B16.11, which stipulates the standards for forged fittings used in high-pressure piping systems. Adhering to these industry standards ensures safety, quality, and reliability.Butt WeldsButt welds should follow the ASME B16.9 standard, which provides specifications for factory-made wrought butt-welding fittings. Compliance with the industry standard ensures the butt weld’s functionality and durability.
Applications and Suitable Industries
Socket WeldsDue to the strength of the joint, socket welds are commonly used in pipelines with a small diameter range, typically from DN50 to DN100. They’re also employed where there’s a change in direction in the piping network, as in the petrochemical, oil, and gas industries.Butt WeldsGiven their high strength, butt welds are often used in high-pressure or high-temperature environments, making them suitable for large diameter pipelines that are common in heavy industries such as power, oil and gas, and shipbuilding.
Strength Testing and Non-Destructive Examination (NDE)
Socket WeldsSocket welds can undergo non-destructive testing methods to ensure their integrity. Magnetic particle testing is commonly conducted for carbon steel socket welds, while penetrant testing is ideal for stainless steel socket welds. These tests help identify any potential defects or discontinuities in the weld, ensuring the quality and reliability of the joint.
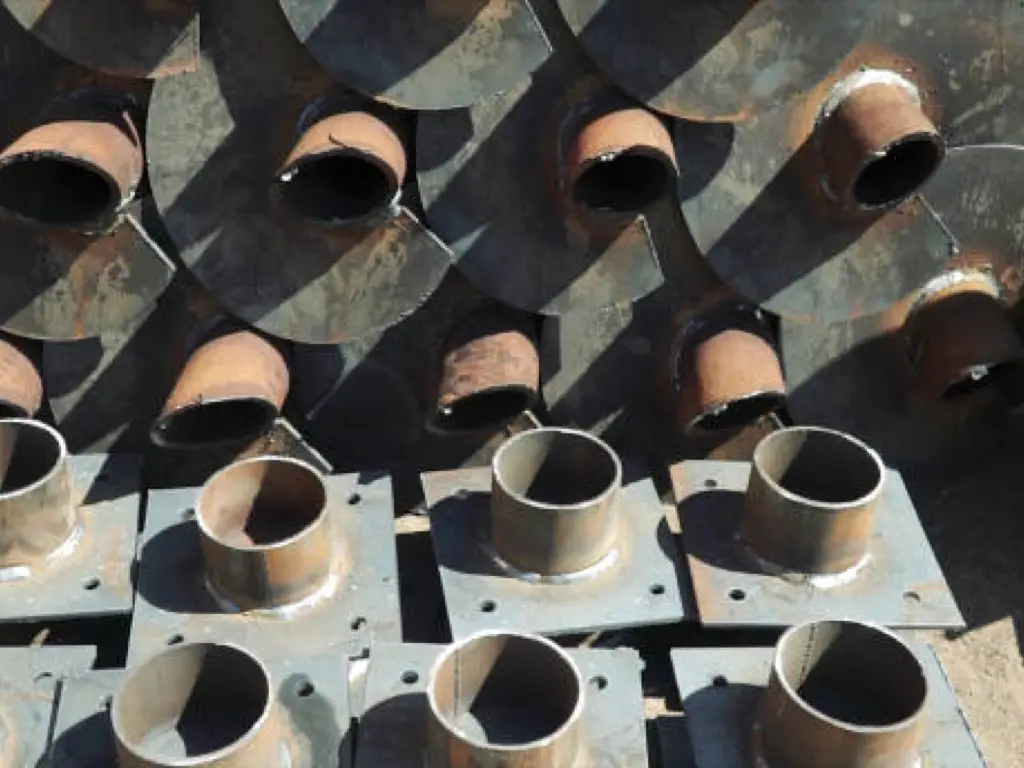
Butt WeldsButt welds often undergo more complex weld testing requirements due to their critical applications. X-ray inspection is the commonly used non-destructive testing method, providing a comprehensive analysis of the weld’s internal structure. This type of inspection allows for a thorough examination of the weld’s integrity, ensuring it meets the required standards and specifications.
Welder Skill Level and Training Requirements
Socket WeldsSocket welds generally require less welding skill and expertise compared to butt welds. Welders with basic skills can effectively execute socket welds, making them accessible for a wider range of workers. However, proper training and understanding of welding techniques and procedures are still necessary to ensure the quality and reliability of the joints.Butt WeldsButt welds require a higher level of welding skill and expertise due to their more complex nature. Skilled welders with extensive training and experience in butt welding techniques are essential for achieving proper weld penetration, joint strength, and overall integrity. The complexity of butt welds necessitates dedicated training programs and certifications to ensure the welder’s capabilities align with industry standards.
Comparative Performance in High-Pressure Environments
Socket WeldsSocket welds provide reliable performance in high-pressure environments, typically up to 600 PSI. However, for extremely high-pressure applications or systems with pressure rating classes 3,000, 6,000, and 9,000, butt welds are the preferred choice due to their higher strength and pressure resistance.Butt WeldsButt welds excel in high-pressure environments, providing a strong and secure connection capable of withstanding significant pressure and temperature fluctuations. Their full penetration welding ensures the joint’s integrity and resistance, making them suitable for critical applications in various industries.
Conclusion
In conclusion, socket welds and butt welds each have their own advantages and considerations. Socket welds are simpler to install, require less extensive surface preparation, and are suitable for smaller diameter pipes. Butt welds, on the other hand, offer superior strength, durability, and corrosion resistance, making them ideal for larger diameter pipes and high-pressure systems.By carefully assessing the project requirements, considering factors such as pipe size, pressure, corrosion resistance, and budget, you can make an informed decision on whether to employ socket welds or butt welds for your specific application.
Rely on Dombor for Your Welding Solutions
Dombor, established in 2001, is a leading manufacturer of premium custom valves. Dombor’s extensive expertise extends into the realm of welding solutions, specifically focusing on services and products related to socket welds and butt welds. Their rich industry experience, coupled with their dedicated commitment to quality and innovation, equips Dombor with the capacity to provide top-notch welding solutions that meet your distinct requirements.