Flow control valves are essential parts of most flow systems. They regulate the rate at which fluids pass through a system, providing a practical way to control flow without the need for constant human intervention. From ensuring the smooth operation of equipment to minimizing risks during operation, flow control valves are vital components in various industries. They also enhance the quality of end products, making them indispensable in today’s industrial world.
What is a Flow Control Valve?
A flow control valve is a specific type of valve that manages the flow or pressure of a fluid such as gas or liquid. The main purpose of a flow control valve is to regulate the velocity and volume of the flow in a piping system. This valve can operate automatically, depending on the pressure and temperature changes, or can be manually controlled.
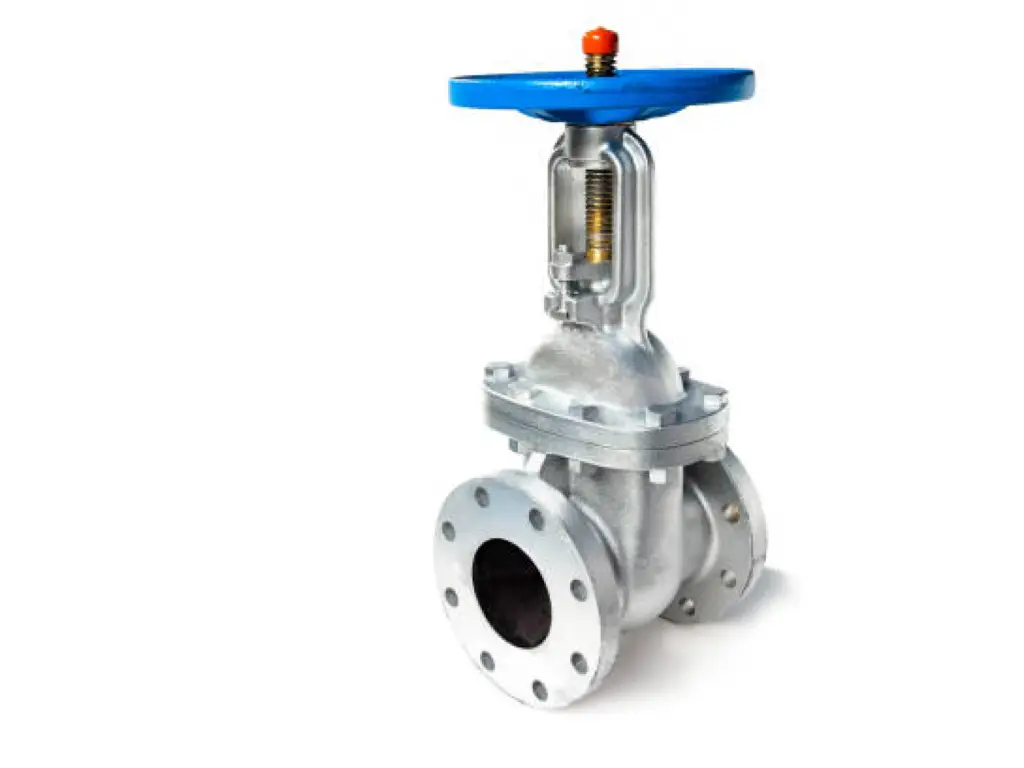
Flow control valves are typically responsive to signals from independent devices like flow meters and temperature gauges. They’re fitted with actuators and positioners to regulate their function, enhancing the flow control industry’s capability to manage fluid pressure in different applications.
How Does a Flow Control Valve Work?
The operation of a flow control valve mainly entails the modulation of the flow or pressure of a fluid, including changes of pressure. In essence, a flow control valve impacts the rate of energy transfer at any given point within a system. It opens, closes, or partially blocks the flow of the fluid to achieve a desired flow rate or maintain a set pressure. By modulating flow rates, these valves ensure the smooth operation of devices downstream and maintain system integrity.
Control valves can also work with hydraulic actuators (also known as hydraulic pilots). For instance, in a hydraulic flow control valve, the valve responds to shifts in pressure or flow, opening, or closing to maintain an optimal flow rate. By doing so, it ensures the hydraulic system operates efficiently and safely. It is the fluid pressure in the system that determines the opening and closing of automatic flow control valves, rather than relying on an external power source. Automatic control valves do not require an external power source and they include pressure reducing valves, flow control valves, back pressure maintenance valves, altitude valves, and relief valves.
What are the Various Types of Flow Control Valves?
There are multiple types of valves designed to meet the diverse needs of different industries for control purposes. Some of these flow control valve types include:
- Pinch Valves: These valves utilize a flexible element, such as a rubber tube, to interrupt and regulate the flow of fluid. They’re particularly useful when working with slurries or liquids with a significant amount of suspended solids.
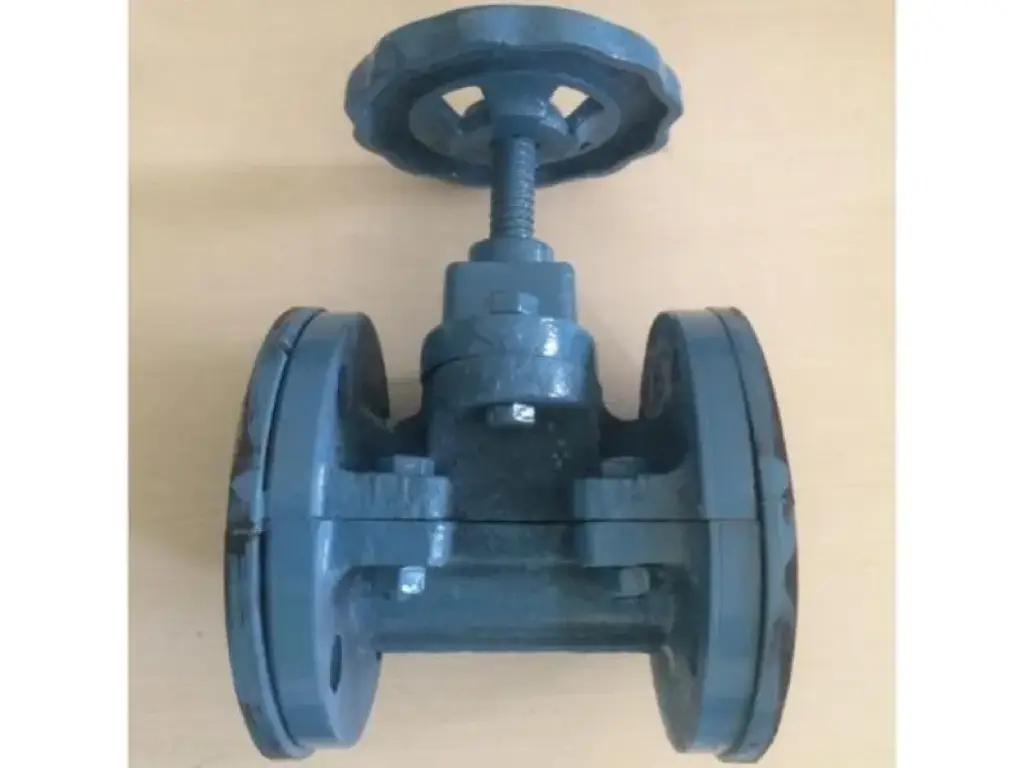
- Diaphragm Valves: These valves use a flexible diaphragm that comes into contact with a seat at the top of the valve body, forming a seal. Diaphragm valves are great for handling corrosive, erosive, and dirt-laden services.
- Gate Valves: These valves function primarily for on/off, non-throttling service. They’re often used where minimum pressure loss and a free bore is required.
- Globe Valves: Globe valves are linear motion valves perfect for adjusting, halting, and initiating flow. They can completely close the flow path or remove it from the flow path completely.
- Needle Valves: These offer precise flow control. They possess a sharp-pointed disc and a matching seat, making them suitable for applications that require precision, such as chemical feed control and continuous blow-off.
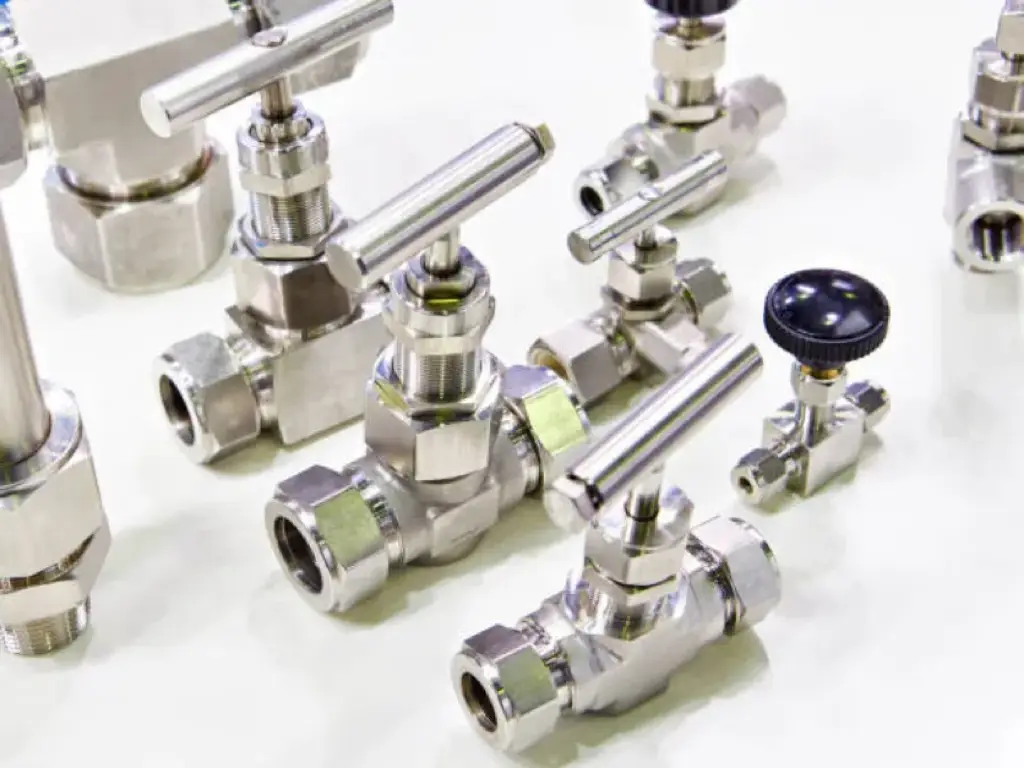
- Ball Valves: These are commonly used in commercial and industrial applications due to their durability and excellent shutoff capability. They operate by rotating a ball to open or close the valve.
- Plug Valves: Plug valves regulate flow by rotating a cylindrical or cone-shaped plug within the valve body.
- Butterfly Valves: These valves control the flow of fluid by rotating a disc in the flow passage. Although they might lack the high degree of precision attained with other valve types, they are notably cost-effective.
What Are Some Advantages and Disadvantages of Different Types of Flow Control Valves?
Flow Valve Type | Advantages | Disadvantages |
Pinch Valve | Conveniently handling slurries or liquids with many suspended solids; Durable and resistant to abrasion; Simple design means less maintenance | Reduced efficiency with larger diameter pipes; Not suitable for high-pressure applications |
Diaphragm Valve | Suitable for handling corrosive, erosive, and dirty fluids; Superior hygiene makes it suitable for food and medical applications | Suited for moderate pressures and temperatures; the elastomeric material may degrade over time |
Gate Valve | Ideal for straight-line flow of fluid with minimal restriction; Suited for a wide range of fluids | Not suited for throttling purposes; Slow to open and close |
Globe Valve | Provides better shut-off than gate valves; Excellent throttling capabilities | Causes a significant pressure drop; Larger and more expensive than other types |
Needle Valve | Allows precise regulation; Exceptional performance under extreme conditions | Not suited for high flow rates; More expensive than other valves |
Ball Valve | Rapid shut-off; High flow capacity; Minimal pressure drop | Not suited for throttling applications; Can potentially trap fluid in the ball’s cavity |
Plug Valve | Easy to install and use; Allows rapid opening and closing | Possible leakage if the plug wears over time |
Butterfly Valve | Lightweight and compact; Affordable; Quick operation | Not as effective in controlling flow rate as other valves; Limited ability to provide an airtight shut-off |
What Are the Various Applications of Flow Control Valves?
- Industrial processes and manufacturing operations to regulate fluid flow.
- Hydraulic and pneumatic systems to control the speed of motors and cylinders.
- HVAC (Heating, Ventilation, and Air Conditioning) systems to regulate the flow of coolant.
- Water treatment facilities to manage the flow rate of water.
- Plumbing systems in buildings to control the flow of water.
- Automotive and aerospace industries for controlling fuel and hydraulic fluid flow.
- Power plants to regulate steam for driving turbines.
- Agricultural equipment for precise delivery of water and fertilizers.
- The oil and gas sector manages the flow of oil and gas through pipelines.
- Chemical and pharmaceutical industries control the flow of liquids or gases during the production process.
How to Select Flow Control Valves for Different Industrial Applications?
- Type of Fluid: Understand what kind of fluid (gas, liquid, etc.) the valve will be controlled. Different valve types handle different fluid types better than others.
- Operating Pressure and Temperature: Determine the operating differential pressures and temperatures that the valve will be exposed to. Certain valves are better suited to high temperatures or pressures, while others might not perform as well under these conditions.
- Flow Rate: The desired flow rate will determine the valve size you’ll need. Larger valves will allow larger volumes of fluid to pass through at a given time.
- System Compatibility: Ensure the chosen valve type is compatible with other system elements.
- Safety Requirements: Some applications may have specific safety requirements that a valve must meet.
- Maintenance and Durability: Consider the maintenance needs and durability of the valve. Certain valve types, while maybe cheaper upfront, may require more regular maintenance, which can lead to increased costs over time.
- Cost-Effectiveness: Analyzing the cost versus the expected benefits and lifespan of the flow valve can help to justify the investment.
- Expert Advice: Consult industry experts or well-reputed suppliers like Dombor for personalized advice on the best flow control valve for your specific application.
What Are the Maintenance Requirements for Different Types of Flow Control Valves?
The maintenance requirements for flow control valves vary based on the type of valve, the system in which it operates, and the kind of fluid it regulates. Regular inspections, cleaning, and lubrication are essential to maintain the performance and extend the life of the valve. Moreover, certain valves such as automatic control valves require special monitoring as their maintenance needs might be more complex. For instance, some require frequent adjustment or replacement of internal parts.
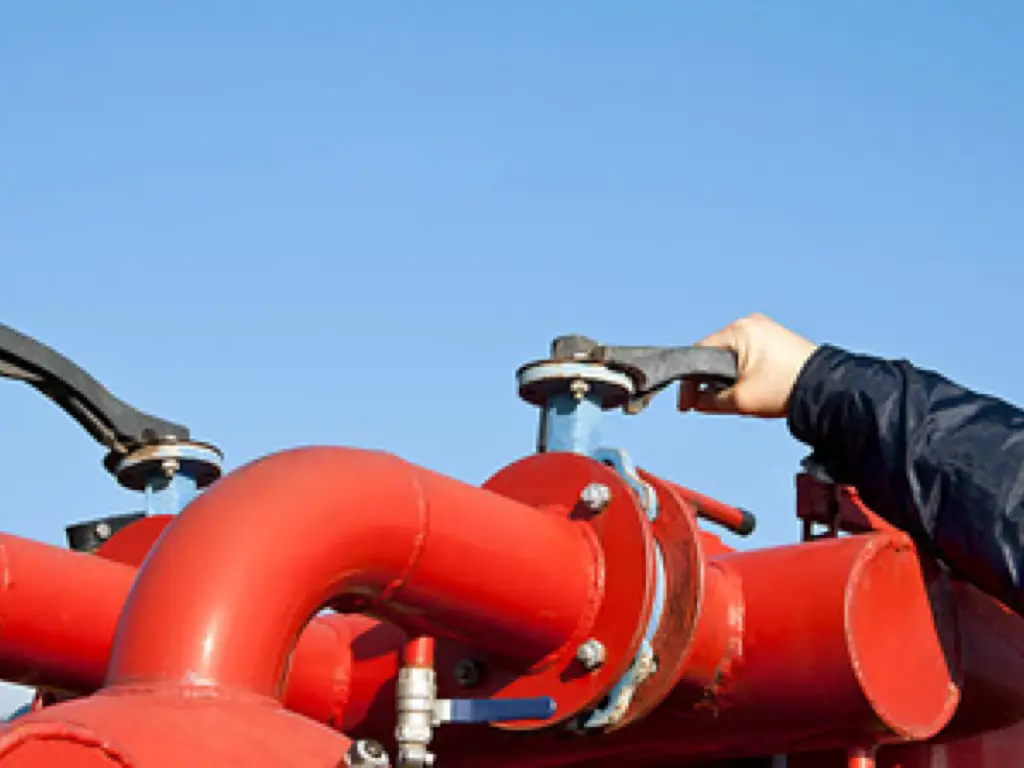
Proper training in valve maintenance is essential and should cover all aspects of operation, calibration, troubleshooting, and repair procedures. It’s worth noting that ignoring regular maintenance can result in valve failure – an issue that could compromise the integrity of the entire system.
Conclusion
Flow control valves play a significant role in various industries and systems, from simply regulating the flow rate of the fluid to maintaining safety and efficiency in operations. While the selection can be extensive, understanding the features, advantages, and applications of each type assists in choosing the best type for your needs.
Choosing a Trusted Partner
As a trusted partner in the flow control industry, Dombor can provide the right flow control valve for your operations. With a comprehensive range of options, top-notch customer service, and industry expertise, Dombor will ensure you get the best value for your investment. Partnering with Dombor guarantees a solution that perfectly meets your requirements and exceeds your expectations.