Introduction to the Importance of Butterfly Valve Dimensions
Butterfly valves are the most preferable option for the flow control of the liquids or gases. They are efficient, simple in operation, and have a range of materials that suit different applications. Did you know that the butterfly valve dimensions selection is one of the most important aspects of its effective operation? As a matter of fact, the size of a butterfly valve is a major factor which determines how well the valve regulates fluid flow within a system. The wrong size valve may cause inefficiencies of the system because of leakage, higher wear and tear, and even system failure.
This article will be a comprehensive guide on butterfly valve sizes and specifications. It will take you through the world of butterfly valve sizes and specifications. We are going to get into the types of valves, how to measure them correctly and the factors influencing your selection process. Finally, you’ll walk away with the knowledge of how to select the best butterfly valve for your application.So, let’s get started!
Exploring Different Types of Butterfly Valves and Their Dimensions
Butterfly valves are multi-purpose and are used in different industrial applications owing to their compact design and effective flow control properties. In this section, we present six main types of butterfly valves, emphasizing their most important characteristics, applications, structural differences and their dimensions.
Wafer Type Butterfly Valve
- Design: The wafer type butterfly valve is designed to form a seal against the bi-directional pressure differential to avoid backflow in systems intended for unidirectional flow. It is located between two flanges and is fastened with bolts or nuts that run through the outer casing of the valve.
- Applications: Usually applied to compact designs and suitable for light to medium applications like heating, ventilation, and air conditioning systems, as well as light industrial processes.
- Main Features: Compact and lightweight, low-cost, and has a good sealing ability.
Lug Type Butterfly Valve
- Design: Lug type valves are characterized by the threaded openings that are at the ends of the body and are used to attach flanges to either side. This design allows the disconnection of either side of the piping system without affecting the other side.
- Applications: It can be used in dead-end services and in frequent maintenance situations, e.g., in chemical and food processing industries.
- Main Features: Facilitates isolation without the need for a complete system shutdown, and robust construction.
Flanged Butterfly Valve
- Design: This valve type has flanges on either side that matches the corresponding flanges of the pipe. The valve is installed by flanging and bolting the flanges together, creating a very strong and reliable connection.
- Applications: Being ideal for the treatment and distribution of water that is characterized by large flow volumes and high-pressure systems.
- Main Features: Superior strength, easy to install and maintain, perfect for high pressure applications.
Concentric Butterfly Valve
- Design: It has a disc placed in the middle of the flow path with the stem passing through the disc at the center. The seating material is arranged in a line along the body perimeter.
- Applications: Primarily used in low-pressure and low-temperature applications where slight leakage is acceptable.
- Main Features: Low complexity, cost-effective, moderate pressure and temperature capabilities.
Double Eccentric Butterfly Valve (Double Offset)
- Design: At this valve, the disc is offset from the stem and the seat axis, which minimizes the friction and wear of the valve during its operation.
- Applications: This can be used in higher pressure and temperature applications, like district heating, steam systems, and oil pipelines.
- Main Features: Lifespan increase due to friction reduction and better sealing at higher pressures.
Triple Eccentric Butterfly Valve (Triple Offset)
- Design: Features three offsets: two in the plane of the disc and one in the seating geometry. It is this design that eliminates the wear and tear on the sealing elements during the operation.
- Applications: Used for critical and severe services such as high temperature and corrosive environments.
- Main Features: Provides a bubble-tight sealing with very low torque that is suitable for high-performance service and critical conditions.
Here is a butterfly valve dimensions chart based on the latest data from various industrial valve manufacturers’ product catalogs and technical specification sheets. The chart includes several common types of butterfly valves:
Valve Type | Size Range (DN) | Pressure Rating (PN) | Face-to-Face (mm) |
Wafer Style Butterfly Valve | DN50 – DN1200 | PN10, PN16, PN25 | 43 – 314 |
Lug Style Butterfly Valve | DN50 – DN1200 | PN10, PN16, PN25 | 43 – 314 |
Flanged Style Butterfly Valve | DN50 – DN2000 | PN10, PN16, PN25 | 43 – 480 |
Concentric Butterfly Valve | DN50 – DN1200 | PN10, PN16, PN25 | 40 – 295 |
Double Eccentric Valve | DN80 – DN1600 | PN10, PN16, PN25 | 46 – 370 |
Triple Eccentric Valve | DN80 – DN1600 | Class 150, 300, 600 | 46 – 370 |
Please note that the data provided above represents common size and pressure rating ranges. Actual dimensions and specifications may vary depending on the manufacturer and specific valve design. When selecting a butterfly valve, it is essential to refer to the manufacturer’s detailed technical specification sheets to ensure that the chosen valve meets your specific application requirements.
How to Measure Butterfly Valve Dimensions: A Step-by-Step Guide
To guarantee the proper fit and the best performance, the accurate measurements of butterfly valve dimensions are mandatory. Here’s how to do it:
- Identify the Type of Valve: First of all, you need to know what kind of valve you are working with (wafer, lug, or double-flanged butterfly valve) because the measuring approach may differ a bit for each.
- Diameter Measurement: Employ a caliper or a tape measure in order to measure the diameter of the valve. For the wafer and the lug types, measure the inner diameter of the pipe flange into which the valve will fit. For double-flanged valves, measure the flange face and not the flange bolts.
- Length Measurement: Specify the face-to-face length of the valve. It is important to keep this in mind, because the valve won’t be able to fit between the flanges without being modified otherwise.
- Flange Measurements: With lug and double-flanged valves, the bolt circle diameter has to be measured which is the circle formed by the center of each bolt hole. Additionally, number the holes and measure the diameter of each one of them.
These actions will help you to have all the required measurements to choose or verify the size of the valve for your system. The accuracy of the measurements means that the system can work better and fewer maintenance problems will occur.
Selecting the Right Butterfly Valve: Understanding Size and Fit
When considering butterfly valve selection for your application, size and fit are the most important elements to keep in mind. The first step is to find out the required flow rate and the pressure drop across the valve. This data will assist you to choose a valve size that can accommodate your system’s flow demands without causing pressure loss or flow restriction.
Besides, you have to think of the pipe diameter and its compatibility with the valve that is already installed in your pipeline. The butterfly valves are offered in a broad range of sizes, typically from 2 inches to 48 inches in diameter. It is important to choose a valve with a nominal size that corresponds to your pipe size in order to be sure of the correct fit and working.
Another aspect to consider in addition to the pipe size is the valve’s face-to-face dimensions. This is even more critical when replacing an old valve or when installing a valve in a limited space. Verify the valve’s face-to-face length is consistent with your pipe and there is enough space for the valve to open and close without any obstruction.
In addition, the valve’s pressure rating is also an important point to be taken into account. Butterfly valves are designed to be suitable for different pressure classes including ANSI Class 150, 300, and 600 for high performance. The pressure rating signifies the highest pressure the valve can safely tolerate at a certain temperature. Furthermore, it is always advisable to choose a valve with a pressure rating that is at least equal to, or higher than, your system’s pressure rating to ensure safe and efficient operation.
Through a deliberate assessment of these factors and acknowledging the significance of size and fit, you can select the right butterfly valve for your needs and guarantee the optimum performance, dependability, and life span of your system.
The Impact of Materials and Construction on Butterfly Valve Dimensions
The choice of materials and the installation design of butterfly valves are critical to the determination of the dimensions and functionality of the valves within a system. These parameters not only influence the wear and performance of the valve but also decide its size and fit for specific devices. Let us, therefore, find out why these aspects are so important.
Material Choice
Materials used for butterfly valves must be selected according to mechanical properties and resistance to the environments that they will be subjected to.For instance:
- Stainless Steel: The stainless steel is well known for its corrosion resistance and strength. Due to this, it is commonly used in valves for applications where the environment is harsh, such as in chemical processing or marine conditions. In addition, the strength of this valve design makes it possible to manufacture thinner valves without compromising the integrity of the valve, which could eventually lead to a reduction in dimensions.
- Ductile Iron: This material provides good durability and cost-effectiveness. These are some of the factors that make it suitable for water and wastewater applications. It typically has a higher weight than stainless steel, so the support structures should be more robust, consequently the installation dimensions will be affected.
- Elastomers (like EPDM): Selecting the elastomer which will be used for seals and seats within the valve is critical since it determines the valve’s sealing ability, pressure handling and durability. The profiles and thicknesses of different materials will be disparate and will affect the size of the valve.
Construction Design
The way a butterfly valve is built—including its disc size, stem thickness, and the method of operation (e.g., lever or gear operated)—affects its dimensions in several ways:
- Disc Size and Shape: Bigger disks can deal with higher flow rates but may need bigger bodies and stems to support the increased force and torque, thus, affecting the face-to-face dimension of the valve.
- Stem and Seating Design: Thicker stems might be needed for higher pressure applications, which could cause larger operational clearances and possibly bigger actuation mechanisms. The seating configuration, whether it is a resilient seated or a triple-offset, has an effect on the dimension, mainly on the length and the space needed for operation.
Pressure and Temperature Considerations
The operational pressure and temperature range dictate the robustness of construction required:
- High Pressure: The valves which are able to withstand higher pressures usually have thicker bodies and more robust seating mechanisms that make the valve bigger.
- Temperature Extremes: Materials and construction must be resilient to the expansion and contraction associated with the temperature fluctuations without compromising integrity or functionality, which may necessitate the creation of additional dimensional allowances.
Knowing the interconnections between these parameters allows for choosing the right butterfly valve dimensions that not only fit physically but also work reliably under the expected operational conditions. This sensible selection of materials and construction makes it possible for the valve to satisfy the requirements of specific applications and therefore increase the efficiency and reliability of the system.
Product Spotlight: Specifications of DomBor Butterfly Valves
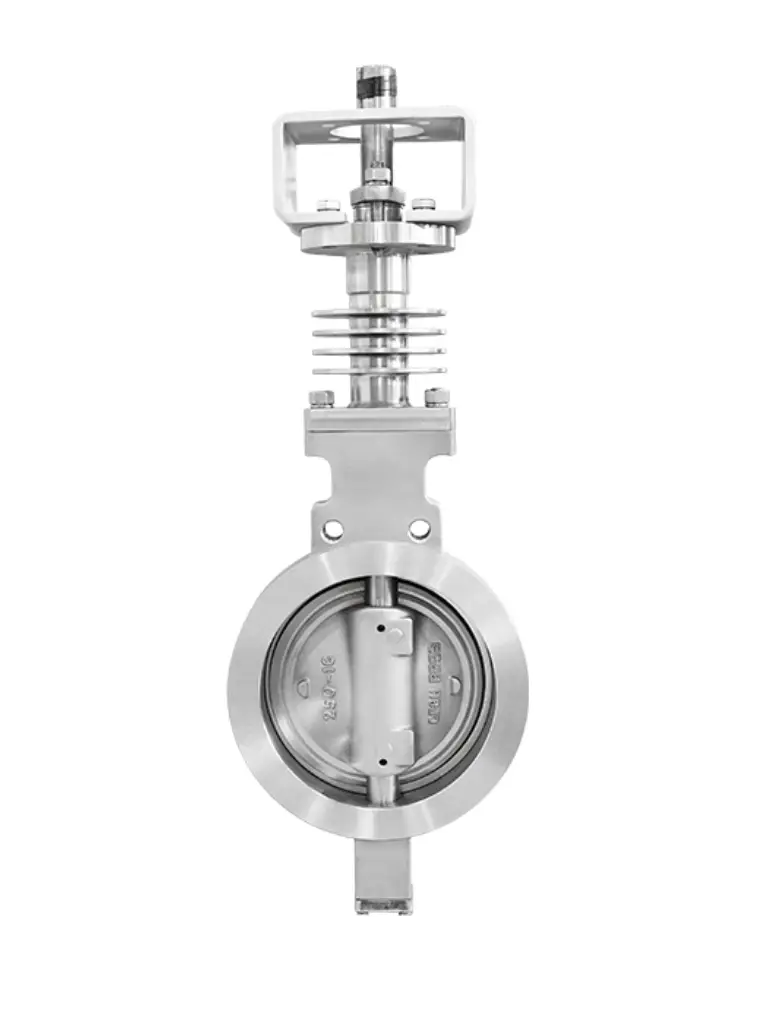
Wafer Type Butterfly Valve
The DomBor Wafer Type Butterfly Valve is a perfect choice for applications that require accurate flow control and the ability to operate in a wide range of conditions. Designed for durability and efficiency, these valves have a compact design which allows for easy installation and maintenance in limited spaces. Their applicability to high-pressure and high-temperature environments, together with zero leakage shut-off capability, makes them the preferred choice for industries like oil & gas, power generation, and chemical processing. The design standards of ASME B16.34 and API 609 guarantee that the quality and safety norms of the international community are met.
Technical Specifications
Specification | Details |
Size Range | 2″-40″ (50mm-1000mm) |
Body Materials | Carbon Steel, Stainless Steel, Nickel Aluminum Bronze, Alloy Steel |
Temperature Range | -196 to 600 degrees Celsius |
Pressure Ratings | Class 150 to Class 900, PN 2.5 to PN150, 10K-20K |
Stem Material | Stainless Steel |
Seat Materials | Soft seat, metal seat, full metal seat |
Shutoff Rating | Zero Leakage |
Disc Materials | Carbon Steel, Stainless Steel, Nickel Aluminum Bronze, Alloy Steel |
Body Style | Wafer |
Design Standard | ASME B16.34, API 609 |
Flange Drilling | ASME B16.5, EN 1092, GOST 33259 |
Testing Standard | API 598, EN12266-1, ISO 5208 |
Certifications | API 609, CE, EAC, SIL3, API 607, ISO 19001 |
Face to Face | API 609, ISO 5752, MSS SP-68, ASME B16.10, EN558-1 |
Fugitive Emissions | ISO 158484-1 |
Applications | Bulk liquid storage, oil & gas, LNG storage & transportation, steam distribution systems, power generation, geothermal steam, sugar & ethanol, pulp & paper liquor, refining, chemical processing, water & wastewater, air separation, cryogenic services |
Operation | Wench, Worm Gear, Electric, Pneumatic |
This table encapsulates the comprehensive technical specifications of DomBor’s Wafer Type Butterfly Valve, showcasing its versatility and capability to meet diverse industrial requirements effectively.
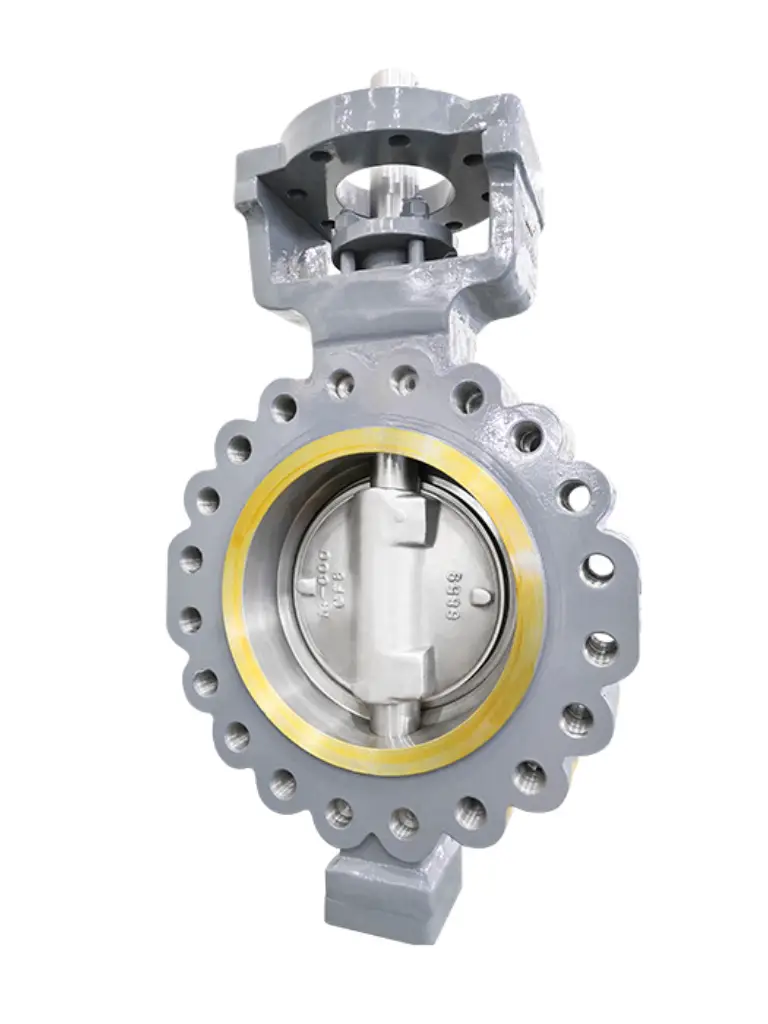
Lug Style Butterfly Valves
The DomBor Lug Style Butterfly Valves are designed for heavy industrial applications where system integrity and maintenance flexibility are the top priorities. These valves are marked out by their lug-style body which features the flange of the valve being bolted directly to its mating flange. This secure connection facilitates the removal and maintenance without affecting the entire system. Designed for the toughest applications, these valves guarantee zero leakage performance under a wide temperature range, making them suitable for critical and high-pressure industries like oil and gas, chemical processing, and power generation.
Technical Specifications
Specification | Details |
Size Range | 2″-40″ (50mm-1000mm) |
Body Materials | Carbon Steel, Stainless Steel, Nickel Aluminum Bronze, Alloy Steel |
Temperature Range | -196 to 600 degrees Celsius |
Pressure Ratings | Class 150 to Class 900, PN 2.5 to PN150, 10K-20K |
Stem Material | Stainless Steel |
Seat Materials | Soft seat, metal seat, full metal seat |
Shutoff Rating | Zero Leakage |
Disc Materials | Carbon Steel, Stainless Steel, Nickel Aluminum Bronze, Alloy Steel |
Body Style | Lug |
Design Standard | ASME B16.34, API 609 |
Flange Drilling | ASME B16.5, EN 1092, GOST 33259 |
Testing Standard | API 598, EN12266-1, ISO 5208 |
Certifications | API 609, CE, EAC, SIL3, API 607, ISO 19001 |
Face to Face | API 609, ISO 5752, MSS SP-68, ASME B16.10, EN558-1 |
Fugitive Emissions | ISO 158484-1 |
Applications | Bulk liquid storage, oil & gas, LNG storage & transportation, steam distribution systems, power generation, geothermal steam, sugar & ethanol, pulp & paper liquor, refining, chemical processing, water & wastewater, air separation, cryogenic services |
Operation | Wench, Worm Gear, Electric, Pneumatic |
This table provides a comprehensive overview of the technical specifications and features of DomBor’s Lug Style Butterfly Valves, highlighting their adaptability and reliability for high-stakes industrial environments.
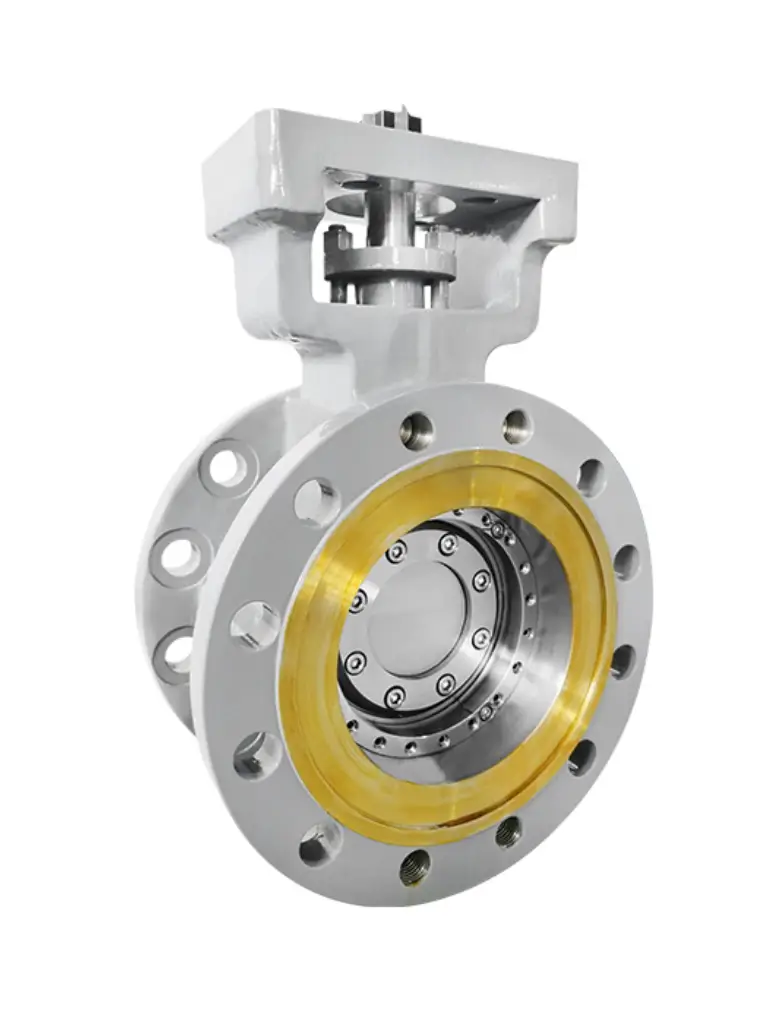
Flange Style Butterfly Valves
DomBor Stainless Steel Butterfly Valves, Flanged Style are manufactured for the purpose of providing ruggedness and high reliability for use in various challenging industrial environments. The valves are designed with a flanged body which guarantees a tight, bolted connection to the pipeline and with the help of this mechanism, easy installation and better sealing are achieved. For high pressure and high temperature applications, these valves are designed to handle a wide variety of media such as steam, gas, and liquids. These valves are the best ones with zero leakage rating and compliance with the top industry standards, which are suitable for critical applications in industries such as power generation, oil and gas, and water treatment.
Technical Specifications
Specification | Details |
Size Range | 2″-40″ (50mm-1000mm) |
Body Materials | Carbon Steel, Stainless Steel, Nickel Aluminum Bronze, Alloy Steel |
Temperature Range | -196 to 600 degrees Celsius |
Pressure Ratings | Class 150 to Class 900, PN 2.5 to PN150, 10K-20K |
Stem Material | Stainless Steel |
Seat Materials | Soft seat, metal seat, full metal seat |
Shutoff Rating | Zero Leakage |
Disc Materials | Carbon Steel, Stainless Steel, Nickel Aluminum Bronze, Alloy Steel |
Body Style | Flange |
Design Standard | ASME B16.34, API 609 |
Flange Drilling | ASME B16.5, EN 1092, GOST 33259 |
Testing Standard | API 598, EN12266-1, ISO 5208 |
Certifications | API 609, CE, EAC, SIL3, API 607, ISO 19001 |
Face to Face | API 609, ISO 5752, MSS SP-68, ASME B16.10, EN558-1 |
Fugitive Emissions | ISO 158484-1 |
Applications | Bulk liquid storage, oil & gas, LNG storage & transportation, steam distribution systems, power generation, geothermal steam, sugar & ethanol, pulp & paper liquor, refining, chemical processing, water & wastewater, air separation, cryogenic services |
Operation | Wench, Worm Gear, Electric, Pneumatic |
This comprehensive table summarizes the technical specifications of the DomBor Flanged Style Butterfly Valves, highlighting their suitability for high-performance applications across a broad range of industrial sectors.
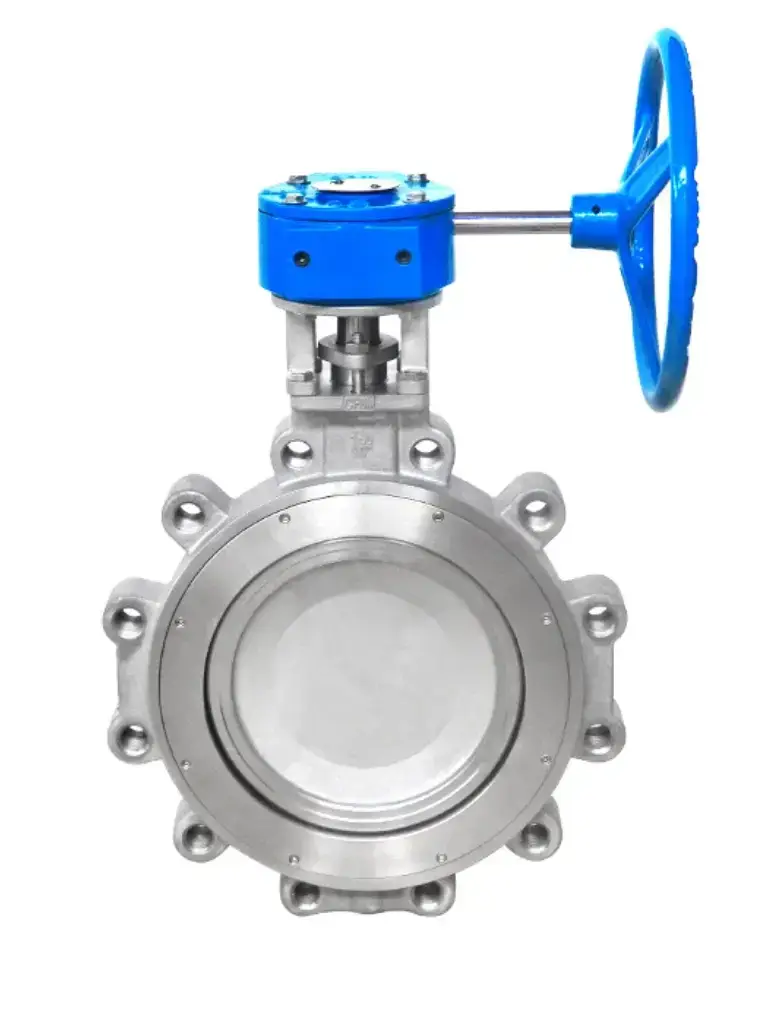
High Performance Butterfly Valves
DomBor high performance butterfly valves are engineered to deliver the exact performance in high pressure and high temperature conditions required for critical services. These valves implement the latest engineering to give you exceptional performance with functions like no leakage for resilient seated models and Class IV leakage for metal seated valves. These valves are made of corrosion resistant materials like stainless steel and nickel aluminum bronze. They are available in a variety of configurations like wafer, lug, and double flanged styles to suit heavy industrial applications where accuracy and dependability are essential.
Technical Specifications
Specification | Details |
Size Range | 2″-64″ (50mm-1600mm) |
Body Materials | Carbon Steel, Stainless Steel, Nickel Aluminum Bronze, Alloy Steel |
Temperature Range | -196 to 320 degrees Celsius |
Pressure Ratings | Class 150 to Class 900, PN 2.5 to PN150, 10K-20K |
Stem Material | Stainless Steel |
Seat Materials | RTFE with Resilient Energizer, PTFE with Resilient Energizer, Fire Safe: RTFE and Inconel with Resilient Energizer |
Shutoff Rating | Zero Leakage (Resilient Seated), FCI 70-2 Class IV (Metal Seated) |
Disc Materials | Carbon Steel, Stainless Steel, Nickel Aluminum Bronze, Alloy Steel |
Body Style | Wafer, Lug, and Double Flanged |
Design Standard | ASME B16.34, ASME VIII, API 609 |
Flange Drilling | ASME B16.5, EN 1092, GOST 33259 |
Testing Standard | API 598, EN12266-1, ISO 5208 |
Certifications | API 609, CE, EAC, SIL3, API 607, ISO 19001 |
Face to Face | API 609, ISO 5752, MSS SP-68, ASME B16.10, EN558-1 |
Fugitive Emissions | ISO 158484-1 |
Applications | High Pressure, High Temperature, Critical Service |
Operation | Wench, Worm Gear, Electric, Pneumatic |
This detailed table outlines the technical specifications and performance features of DomBor’s High Performance Butterfly Valves, highlighting their suitability for use in high-stakes applications requiring robust control and reliability.
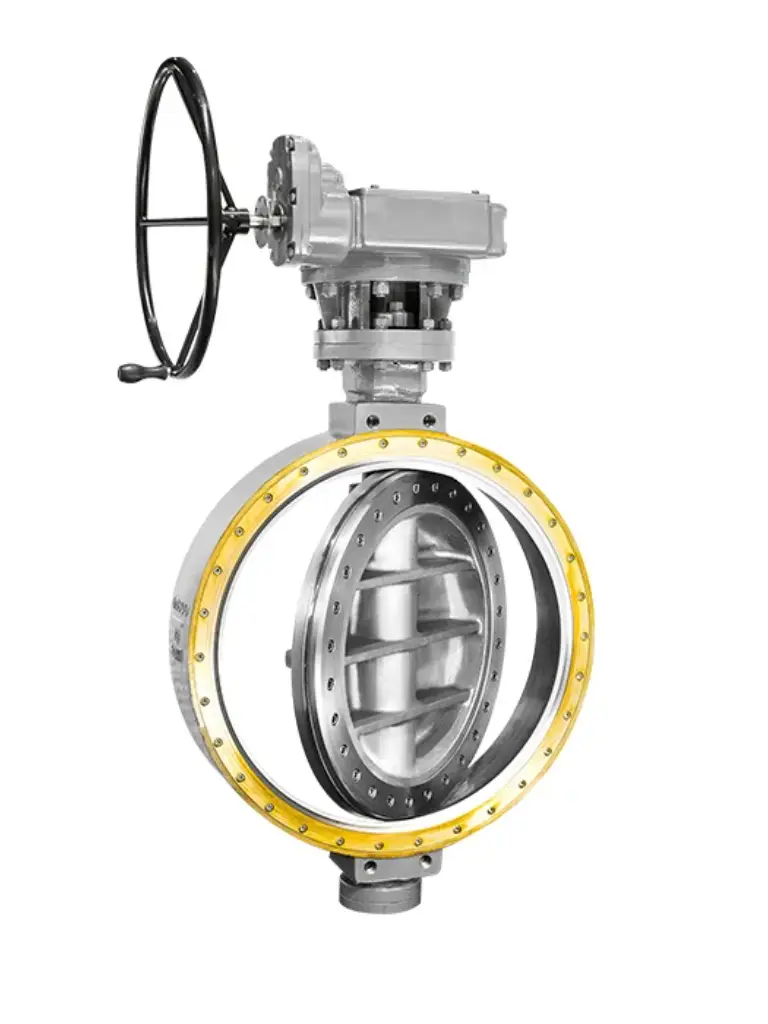
Triple Offset Butterfly Valves
DomBor’s Triple Offset Butterfly Valves are the symbol of precision and durability in the most demanding applications. These valves have an innovative triple offset design that avoids the contact of seat and disc, resulting in a tight seal and a prolonged service life. They are made from sturdy materials such as stainless steel and alloy steel which can withstand both high temperatures and high pressures. With the triple offset design, the valve is able to give zero leakage, which makes it a good choice for critical applications in industries such as oil and gas, power generation, and chemical processing where reliability and performance are the main characteristics.
Technical Specifications
Specification | Details |
Size Range | 2″-144″ (50mm-3600mm) |
Body Materials | Carbon Steel, Stainless Steel, Nickel Aluminum Bronze, Alloy Steel |
Temperature Range | -196 to 550 degrees Celsius |
Pressure Ratings | Class 150 to Class 1500, PN 2.5 to PN250, 10K-20K |
Stem Material | Stainless Steel |
Seat Materials | SS+Graphite |
Body Style | Wafer, Lug, Double Flanged, Butt Welded |
Design Standard | ASME B16.34, API 609 |
Flange Drilling | ASME B16.5, EN 1092, GOST 33259 |
Testing Standard | API 598, EN12266-1, ISO 5208 |
Certifications | API 609, CE, EAC, SIL3, API 607, ISO 19001 |
Face to Face | API 609, ISO 5752, MSS SP-68, ASME B16.10, EN558-1 |
Fugitive Emissions | ISO 158484-1 |
Applications | Bulk liquid storage, oil & gas, LNG storage & transportation, steam distribution systems, power generation, geothermal steam, sugar & ethanol, pulp & paper liquor, refining, chemical processing, water & wastewater, air separation, cryogenic services |
Operation | Wench, Worm Gear, Electric, Pneumatic |
This table provides a detailed overview of the technical specifications and capabilities of DomBor’s Triple Offset Butterfly Valves, highlighting their suitability for demanding operational conditions where precision and longevity are crucial.

Concentric Butterfly Valves
DomBor Concentric Butterfly Valves are engineered to ensure a longstanding and dependable service in general and mild service applications. These valves include a concentric disc and a stem which is aligned with the disc center and pipe centerline. This simple setup allows for the valve to not be damaged by the pressure, which gives a bidirectional bubble-tight shutoff. These valves are made of materials such as cast iron, ductile iron, and stainless steel and are mainly used in chemical processing, food and beverage, and wastewater treatment industries. The simplicity and efficacy of concentric butterfly valves have made them a popular selection of valves for cost-effective flow control solutions.
Technical Specifications
Specification | Details |
Size Range | 2″-40″ (50mm-1000mm) |
Body Materials | Cast Iron, Ductile Iron, Carbon Steel, Stainless Steel, Nickel Aluminum Bronze |
Temperature Range | -29 to 180 degrees Celsius |
Pressure Ratings | PN6-PN16, 150psi |
Stem Material | Stainless Steel |
Seat Materials | BUNA-N, EPDM, FKM, Polyurethane |
Shutoff Rating | Bidirectional Bubble-tight |
Disc Materials | Nylon Coated Ductile Iron, Aluminum Bronze, Stainless Steel |
Body Style | Wafer, Lug, and Double Flanged |
Design Standard | MSS SP 67, API 609 |
Flange Drilling | ASME B16.5, EN 1092, GOST 33259 |
Testing Standard | API 598, EN12266-1, ISO 5208 |
Certifications | API 609, CE, EAC, SIL3, ISO 19001 |
Face to Face | API 609, ISO 5752, MSS SP-68, ASME B16.10, EN558-1 |
Fugitive Emissions | ISO 158484-1 |
Applications | Chemical, Food and Beverage, Pulp and Paper, Waste Water and more |
Operation | Wench, Worm Gear, Electric, Pneumatic |
This detailed table showcases the technical specifications of DomBor’s Concentric Butterfly Valves, underscoring their adaptability and effectiveness in diverse applications that require straightforward, reliable valve operation with minimal maintenance requirements.