Introducción a la fabricación de válvulas de bola: Fundamentos e importancia
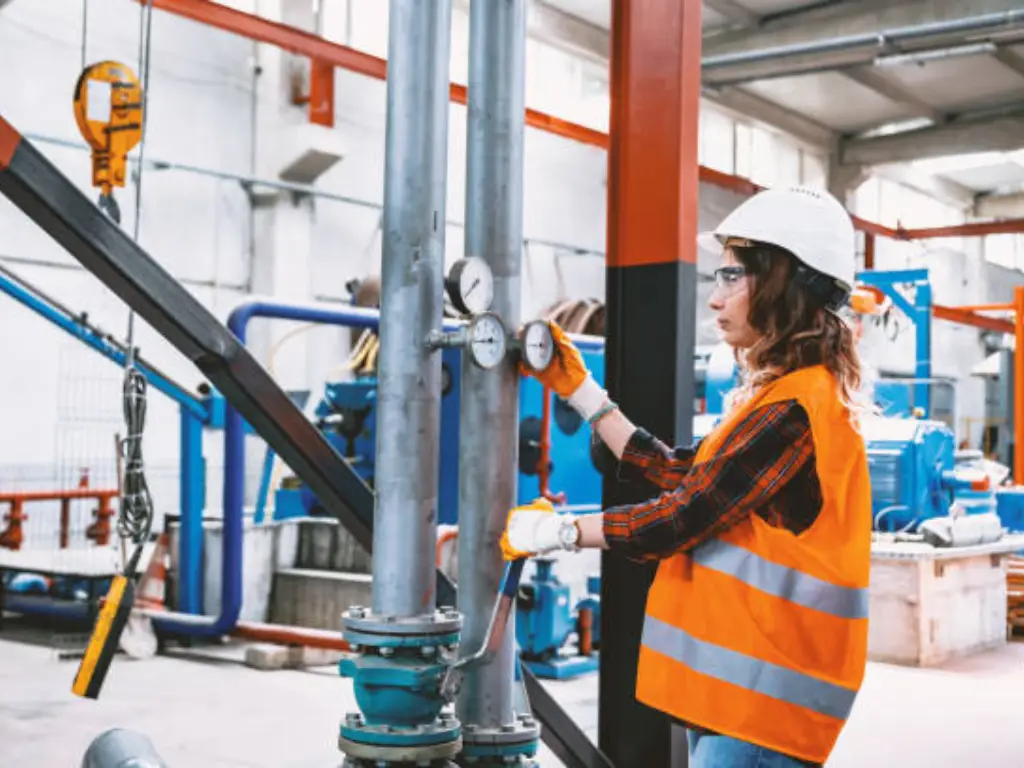
En diversas aplicaciones industriales, las válvulas de bola son componentes esenciales conocidos por su capacidad de cierre fiable y su buen funcionamiento. El proceso de fabricación de estas válvulas es crucial para garantizar su fiabilidad y longevidad. En este artículo se describen los pasos necesarios para fabricarlas y se explica su función en la regulación de gases y líquidos.
Selección de materiales en el proceso de fabricación de válvulas de bola
El paso inicial en la fabricación de válvulas de bola es elegir los materiales adecuados, que pueden ser acero inoxidable, latón y PVC. Cada uno tiene sus propias características especiales. Una de ellas es el acero inoxidable, preferido por su excelente resistencia a la corrosión y durabilidad, que lo hacen adecuado para diversas aplicaciones. El latón es barato y maleable, lo que lo convierte en una opción rentable para la producción. El PVC es ligero y resistente a muchos productos químicos. La selección del material es el primer paso en el proceso de fabricación de válvulas de bola y viene determinada por el uso previsto de la válvula, las circunstancias operativas y las especificaciones necesarias.
Forja vs. Fundición: Métodos de fabricación de válvulas de bola
En la fabricación de válvulas de bola se utilizan con frecuencia dos métodos: la forja y la fundición. Cada uno de ellos tiene sus propios procesos, características, ventajas e idoneidad para diversas aplicaciones. Conocer la distinción entre fundición y forja es esencial para elegir el método de fabricación adecuado para las especificaciones particulares de una válvula de bola. En la siguiente conversación se identificarán específicamente ambos métodos por sus procesos, características, lados de ganancias y pérdidas, así como beneficios o deméritos. Cuando se utiliza el método de forja, el metal se calienta y, a continuación, se comprime, se dobla y se le da forma para que encaje en el diseño de la válvula de bola forjada utilizando una máquina de forja. Esta matriz ayuda a dar al metal la forma específica, mientras que la máquina aplica presión para forzar el metal a la forma correcta. Para válvulas más grandes, puede ser necesario soldar diferentes componentes.
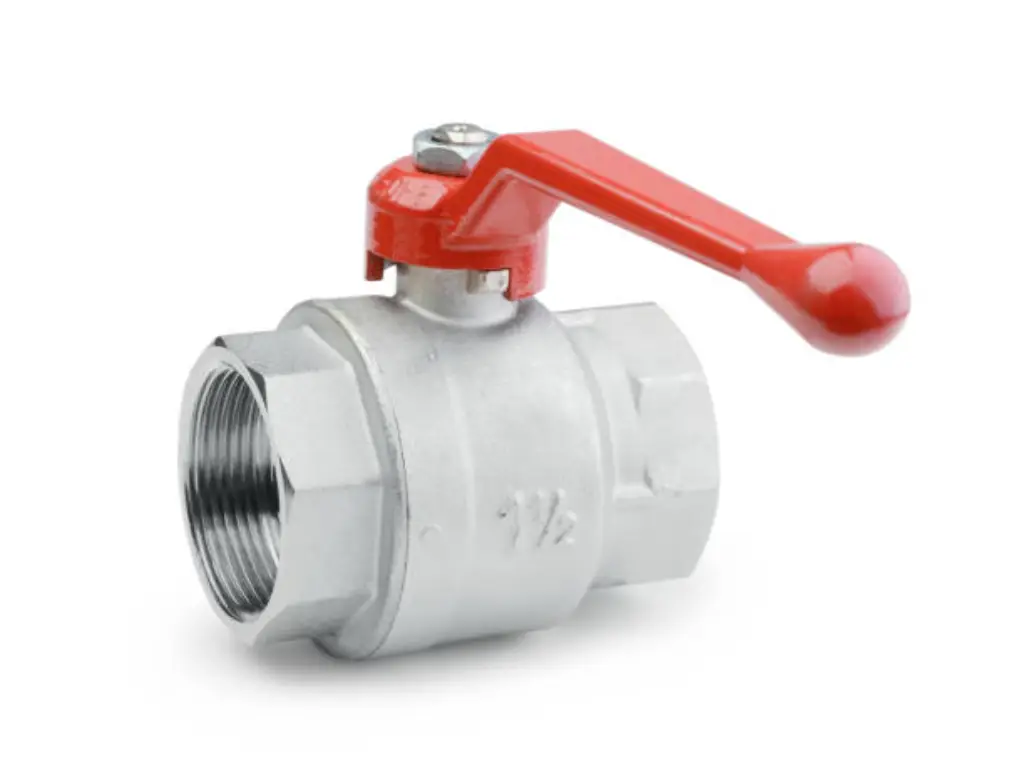
Forja
Proceso:
- Consiste en dar forma al metal utilizando alta temperatura y presión.
- Comienza calentando una pieza de metal hasta que se vuelve maleable.
- A continuación, el metal se somete a alta presión mediante martilleo o prensado, forzándolo a adoptar la forma deseada.
Características de las válvulas de bola forjadas:
- Robustez excepcional.
- Resistencia e integridad estructural superiores.
- Se consigue mediante la alineación de la estructura del grano del metal durante el proceso de forja.
Ventajas:
- Puede soportar aplicaciones de alta presión y condiciones de funcionamiento duras.
- Minimiza el desperdicio de material, por lo que resulta eficaz y rentable.
- Gran durabilidad y fiabilidad.
- Adecuado para aplicaciones críticas en las que la seguridad y la longevidad son primordiales.
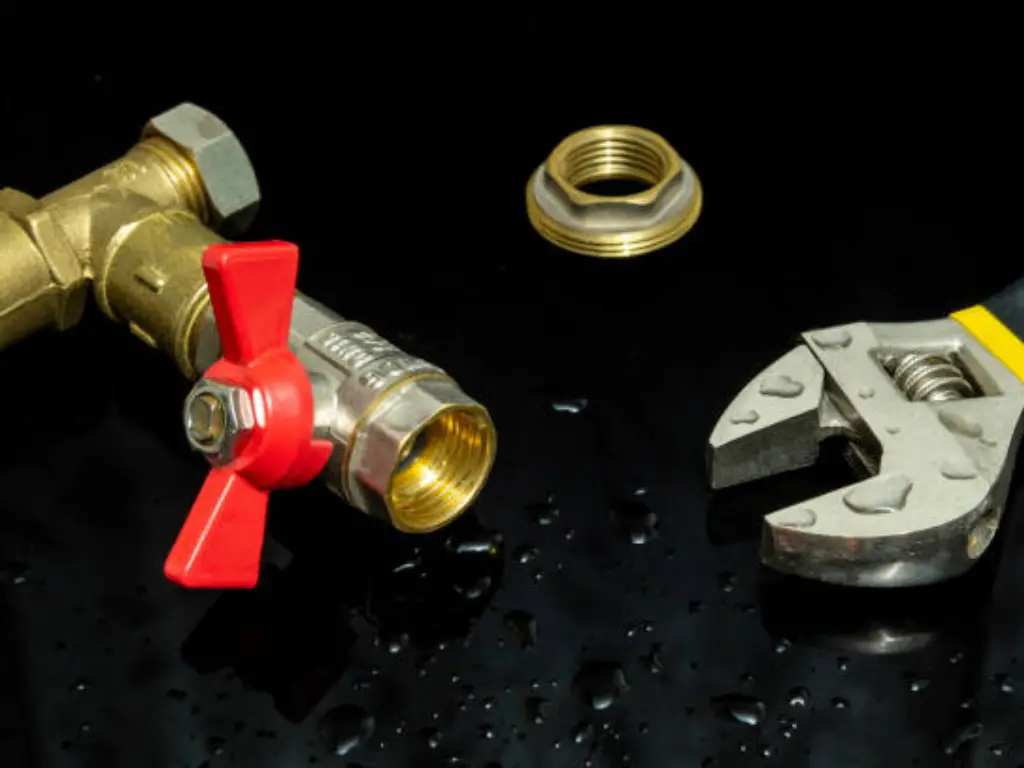
Reparto:
Proceso:
- Consiste en verter metal fundido en un molde para darle la forma deseada.
Características de las válvulas de bola de fundición:
- Permite una mayor flexibilidad en el diseño.
- Permite fabricar válvulas de bola con geometrías complejas y detalles intrincados.
Ventajas:
- Puede fabricarse con una gama más amplia de materiales, incluidas diversas aleaciones.
- Mayor facilidad para adaptar las propiedades de las válvulas a requisitos específicos.
- Más económico para producir grandes cantidades de válvulas, especialmente las que tienen diseños detallados.
Desventajas:
- Pueden no tener el mismo nivel de resistencia estructural que las válvulas forjadas.
- Puede no ser adecuado para aplicaciones de presión extremadamente alta.
A la hora de fabricar una válvula de bola, la elección entre forja y fundición depende de varios factores, como las necesidades de resistencia, la complejidad del diseño y el coste de producción. La forja garantiza la mayor robustez y, por tanto, es la mejor para aplicaciones de alta presión; al mismo tiempo, la fundición ofrece personalización del diseño y rentabilidad, especialmente durante la fabricación en serie. Esta comprensión separa a los fabricantes, que pueden elegir adecuadamente el método que se adapte a sus requisitos específicos y criterios de aplicación.
Desglose paso a paso del proceso de fabricación de válvulas de bola
La fabricación de una válvula de bola implica muchos pasos detallados y precisos que son muy importantes para garantizar que el producto final cumpla estrictas normas de calidad. A continuación se ofrece una descripción ampliada de las principales etapas:
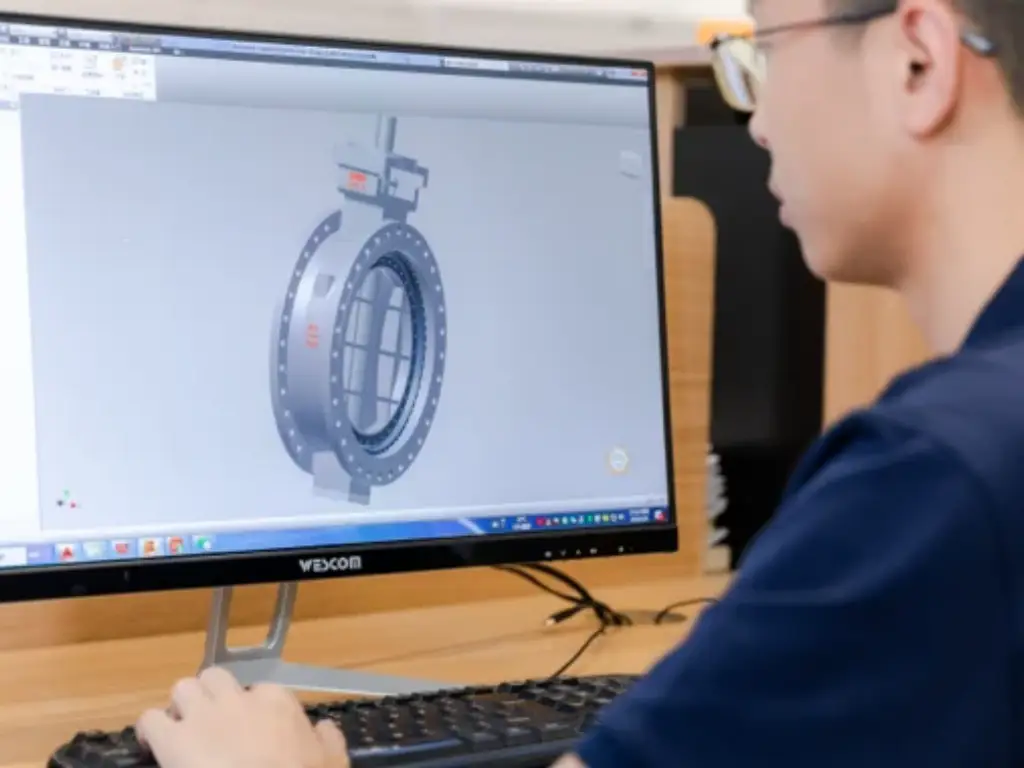
1. Diseño:
- En el proceso de fabricación, el diseño es la primera etapa. Los ingenieros crean un plano de la válvula con programas de diseño asistido por ordenador (CAD). Este diseño muestra las dimensiones de la válvula y especifica los niveles de tolerancia para garantizar que todas las piezas encajen perfectamente entre sí. El programa CAD permite realizar ajustes precisos y simulaciones para optimizar el rendimiento antes de iniciar la producción.
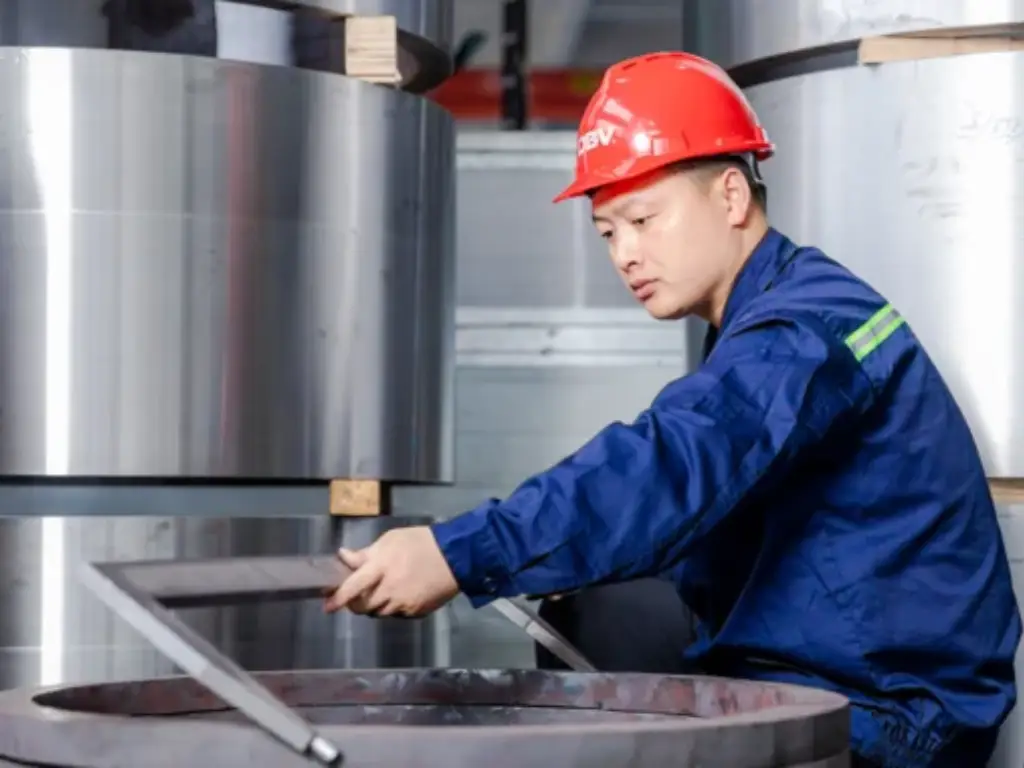
2.Preparación del material:
- El paso siguiente a la finalización del diseño es la preparación de las materias primas. La preparación de la materia prima suele implicar el corte de varillas metálicas en tamaños específicos, para lo cual se puede utilizar un tipo de metal como el acero inoxidable o el latón en función de los requisitos o la norma, según el tamaño que necesite cada pieza.
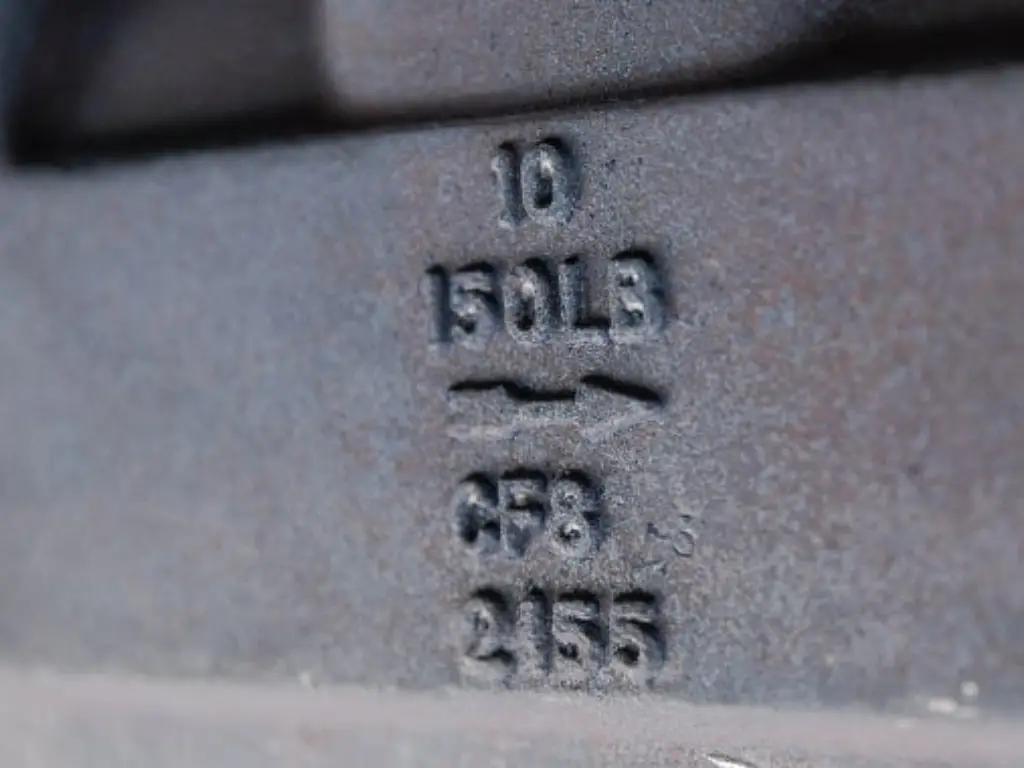
3.Forja o fundición:
- A continuación, estos materiales preparados se convierten en cuerpos de válvula mediante métodos de forja o fundición. En el caso de la forja, el metal se calienta a altas temperaturas donde toma forma utilizando un martillo o una prensa, respectivamente, mientras que el proceso de fundición implica verter metales fundidos en moldes preformados que definen la forma del cuerpo de la válvula, respectivamente; ambos moldes tienen la intención de introducir un componente fuerte y duradero que actúe como columna vertebral de cualquier válvula.
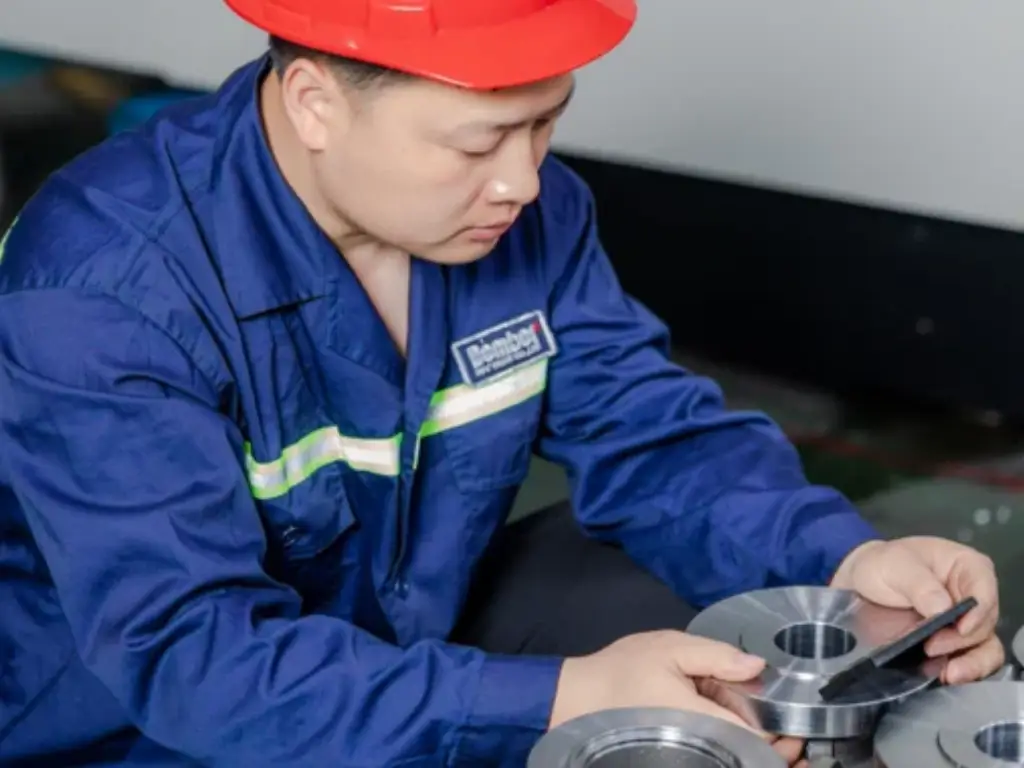
4.Recorte y chorreado:
- Después de las actividades de forja o fundición, puede haber algunos excesos en ocasiones o defectos en los cuerpos de estas válvulas; por lo tanto, los recortes los eliminan mientras que el chorro de arena suaviza las superficies mediante la adopción de materiales abrasivos finos que impactan sólo contra ellos. Garantiza que tengan un acabado limpio, de modo que puedan funcionar correctamente sin tener que enfrentarse a ningún problema relacionado con su aspecto.
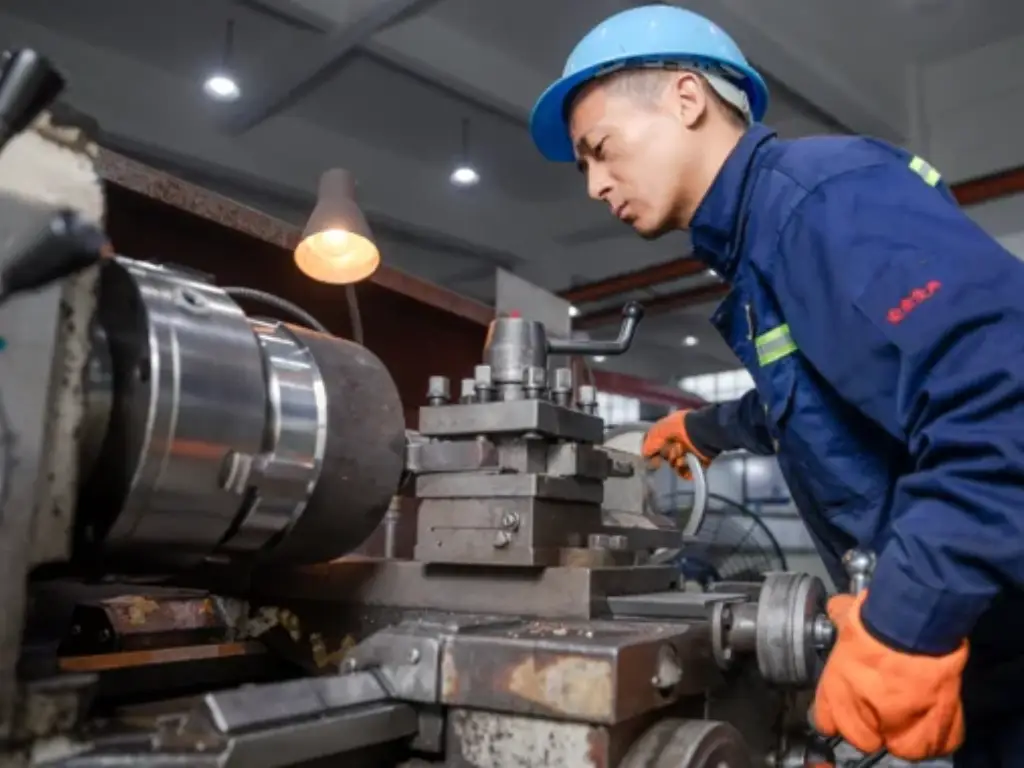
5.Mecanizado:
- El mecanizado de precisión es vital para mantener las tolerancias exactas especificadas durante la fase de diseño, que normalmente requiere procesos de taladrado, torneado y fresado realizados en máquinas CNC, siendo todas las piezas fabricadas tan perfectas hasta el más mínimo detalle, ya que las máquinas CNC comunican las dimensiones exactas de acuerdo con las especificaciones, garantizando así un ajuste adecuado cuando este sistema está listo para su montaje completo.
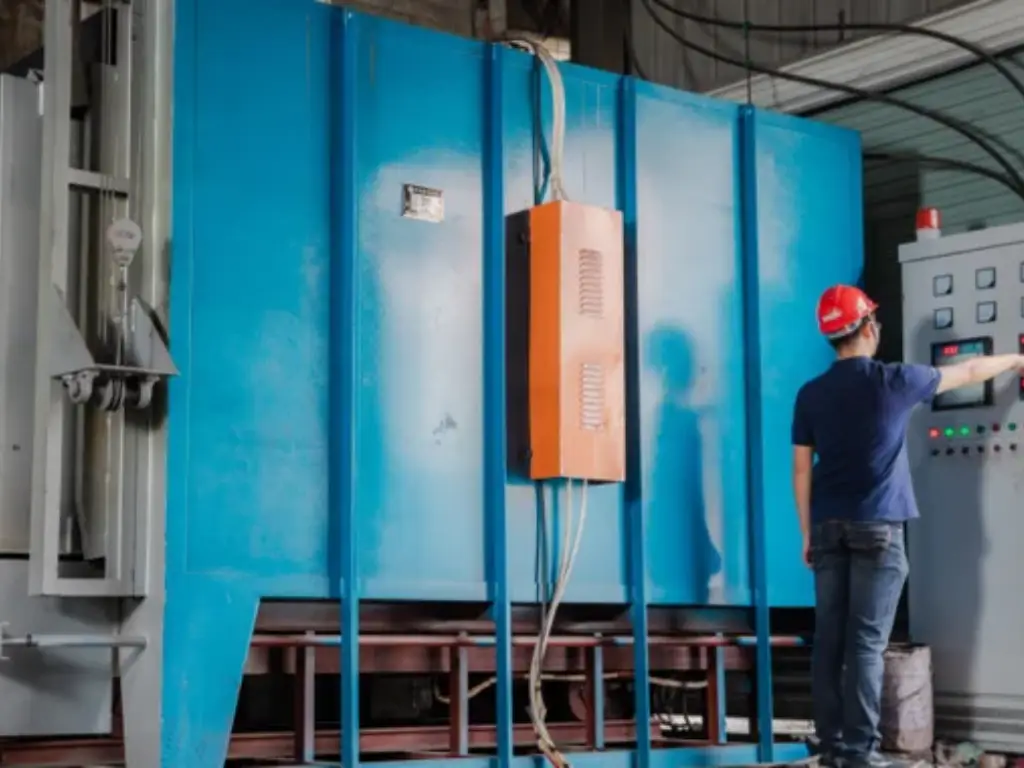
6.Tratamiento térmico y chapado:
- A continuación, se aplica un tratamiento térmico a los componentes de la válvula para mejorar sus propiedades materiales, sometiéndolos a cambios de temperatura y ciclos de enfriamiento específicos, modificando así la microestructura y mejorando la resistencia y durabilidad del material. Tras el tratamiento térmico, se aplica un recubrimiento, como el niquelado, porque hay que añadir resistencia a la corrosión si la válvula tiene que sobrevivir a condiciones ambientales duras.
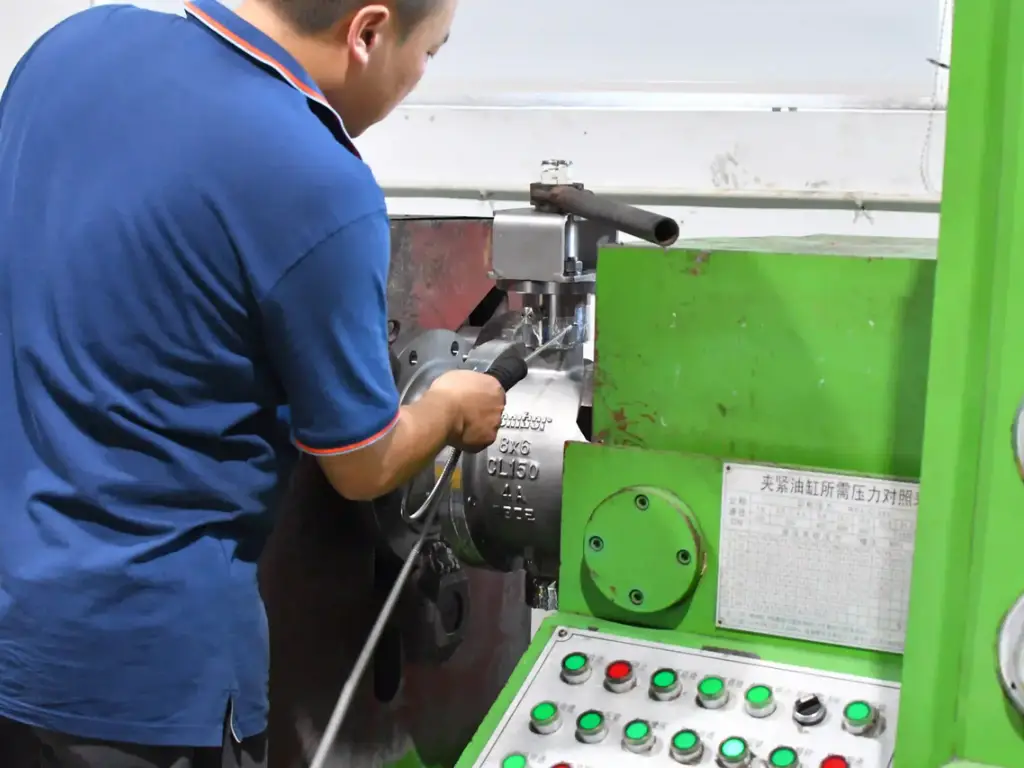
7.Asamblea:
- Durante la fase de montaje, todas las piezas mecanizadas se unen entre sí. Esto suele implicar colocar una bola dentro del cuerpo de la válvula, fijar las juntas en su sitio y colocar las tapas de los extremos; por lo tanto, esta fase en particular requiere precisión y cuidado, ya que las válvulas necesitan que todo esté alineado correctamente, de lo contrario no funcionarán sin problemas.
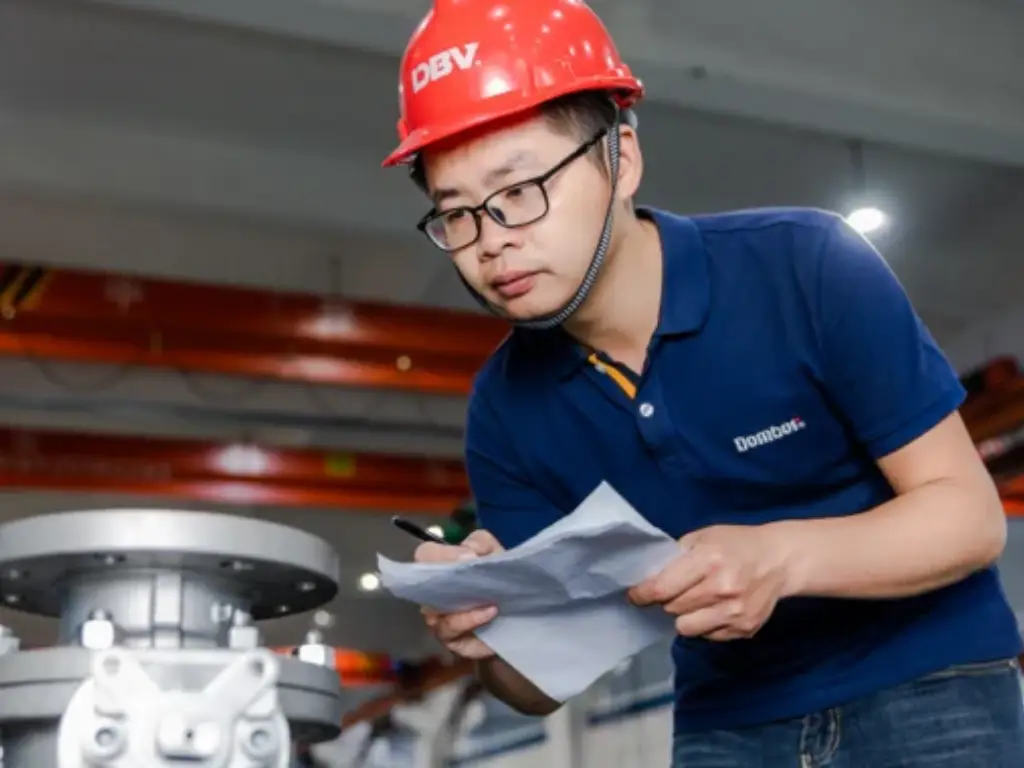
8.Pruebas y Control de calidad:
- El último paso en el proceso de fabricación son las pruebas rigurosas y el control de calidad, donde cada válvula se somete a varias pruebas para satisfacer las especificaciones del cliente junto con las normas de la industria que prevalecen en este sector, pero sobre todo se realizan pruebas de presión para detectar cualquier fuga o confirmar si las válvulas pueden soportar las presiones operativas para las que fueron diseñadas durante la fase de diseño; por lo tanto, cualquier producto que no supere estas duras pruebas no podrá ser entregado en el extranjero.
La fabricación de válvulas de bola implica una serie de pasos complejos que van desde el diseño preciso, la preparación del material hasta la conformación, el acabado, las maquinarias, etcétera. Estas medidas son cruciales para producir válvulas de alta calidad que puedan utilizarse eficazmente en distintos sistemas.
Principales medidas de control de calidad en la fabricación de válvulas de bola
En el proceso de fabricación de válvulas de bola, el control de calidad es muy importante para garantizar que los productos se fabrican con alta calidad. Estas medidas implican pruebas como comprobaciones de precisión dimensional, pruebas de fugas y pruebas de manejo de presión para garantizar que el producto final cumple las normas y especificaciones requeridas. El control de calidad garantiza que cada una de las válvulas desarrolladas cumple las normas y especificaciones establecidas, lo que las hace fiables para su uso en distintas aplicaciones. En consecuencia, los fabricantes han empleado normas de calidad internas y externas para garantizar la seguridad y fiabilidad de estas válvulas.
Pruebas y acabado en el proceso de fabricación de válvulas de bola
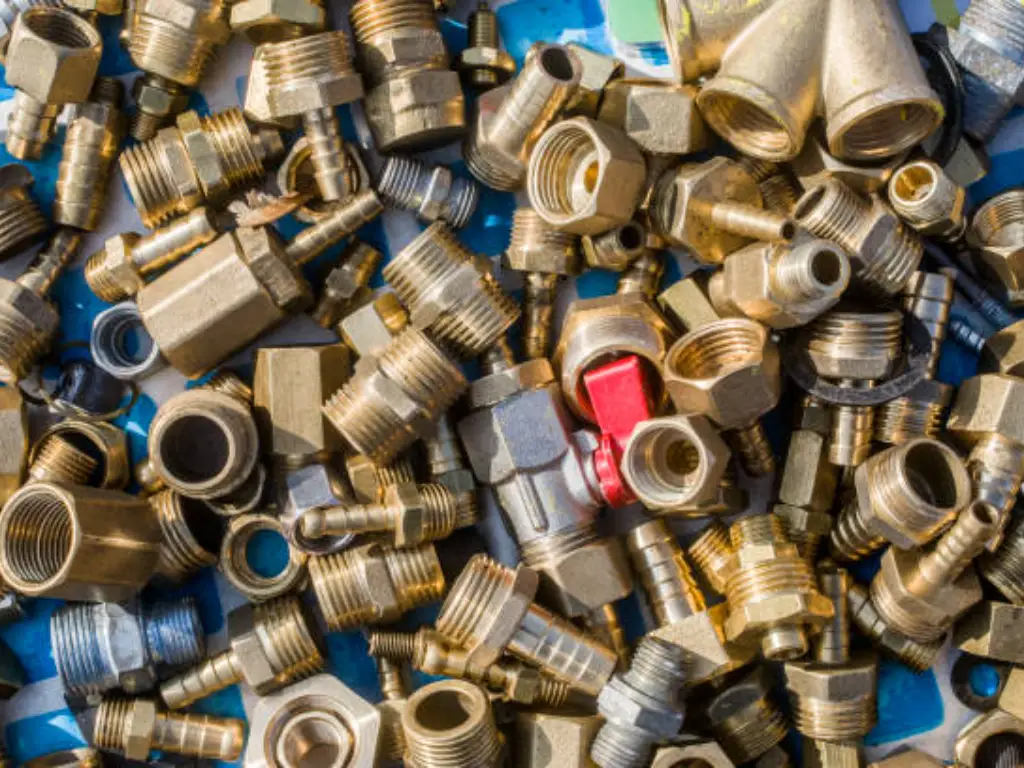
Las pruebas y el acabado son los últimos pasos en la fabricación de válvulas de bola. Las válvulas con fugas pueden someterse a pruebas de estanqueidad mediante flujos de aire o fluidos a alta presión. También se confirma la precisión dimensional. La etapa de acabado incorpora la limpieza, el desbarbado, así como el revestimiento y la pintura de los cuerpos de las válvulas para protegerlas de la corrosión y mejorar su aspecto estético. Para permitir las aplicaciones industriales, las válvulas deben embalarse adecuadamente para que, tras llegar a su destino, sigan siendo aptas para su uso.
Aplicaciones y ventajas de las válvulas de bola de alta calidad
Varias aplicaciones, como el petróleo y el gas, el procesamiento químico y el tratamiento de aguas, entre otras, utilizan válvulas de bola de primera calidad. Son buenas para estos entornos difíciles porque ofrecen un sellado hermético a las burbujas, pueden controlar flujos de alta presión y no se corroen fácilmente. El uso generalizado de válvulas de bola se debe en parte a su durabilidad y bajo mantenimiento. El proceso de fabricación de las válvulas de bola puede ayudar a las industrias a comprender la ingeniería y precisión que implica la producción de estos componentes cruciales.
El producto final siempre puede ser complejo pero meticuloso en lo que respecta a todo el proceso seguido para fabricar una válvula de calidad que pueda utilizarse en cualquier lugar que se necesite. Desde la selección de materiales hasta las pruebas finales, todos y cada uno de los pasos son necesarios para garantizar la producción de válvulas que cumplan altos estándares de rendimiento y fiabilidad.
Dombor: El fabricante líder de válvulas industriales desde 2001
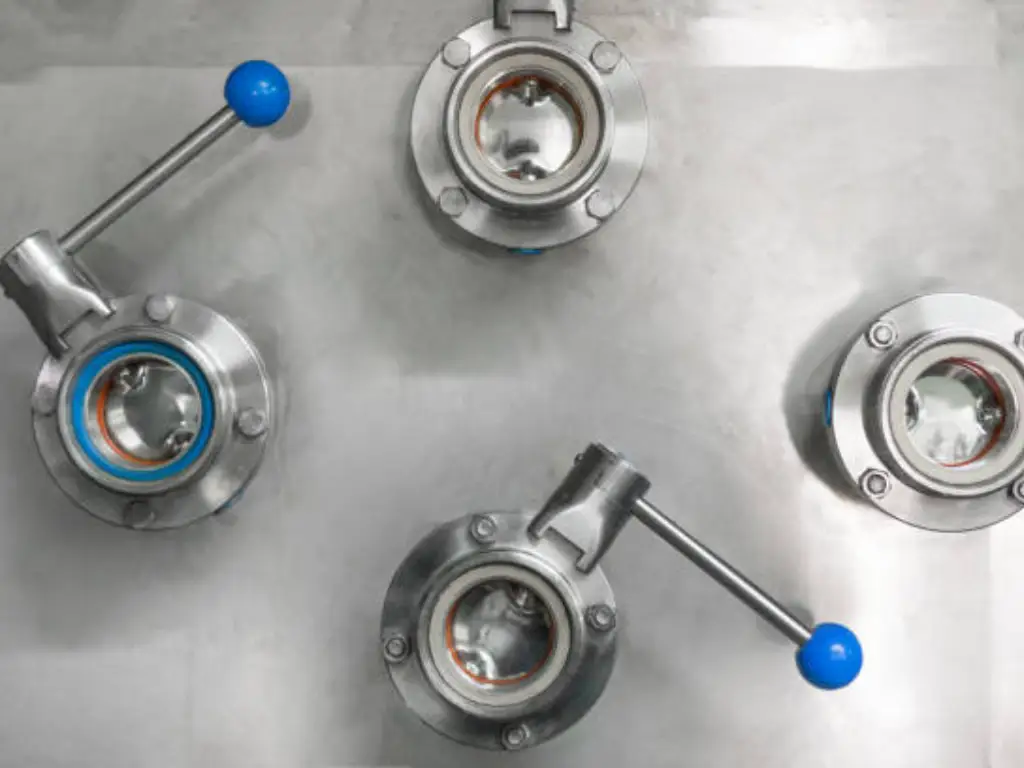
Dombor es uno de los mejores fabricantes de válvulas industriales desde 2001. Han trabajado en más de tres mil proyectos, principalmente en los sectores del petróleo, el gas y la industria química, lo que convierte a Dombor en la empresa con más experiencia. Sus numerosas licencias y certificados, como API6D, API609, CE, ISO9001, etc., garantizan que sus productos son de una calidad muy superior a la de otras empresas. A través de sus métodos de producción modernizados, como instalaciones de prueba avanzadas y máquinas CNC de alta precisión, Dombor asegura un funcionamiento eficiente de sus válvulas. La tecnología HVOF de la empresa se utiliza en la fabricación de válvulas de sellado duro para aumentar su durabilidad, haciéndolas el doble de fiables que el resto del sector gracias a su mayor resistencia a la corrosión y a sus niveles de dureza. Esta marca ofrece productos únicos con varias opciones de personalización, así como un periodo de garantía de dos años, por lo que se distingue por su innovación y excelente prestación de servicios. Por otra parte, para las empresas que necesitan soluciones de vanguardia para válvulas, Dombor es muy recomendable.