Introducción
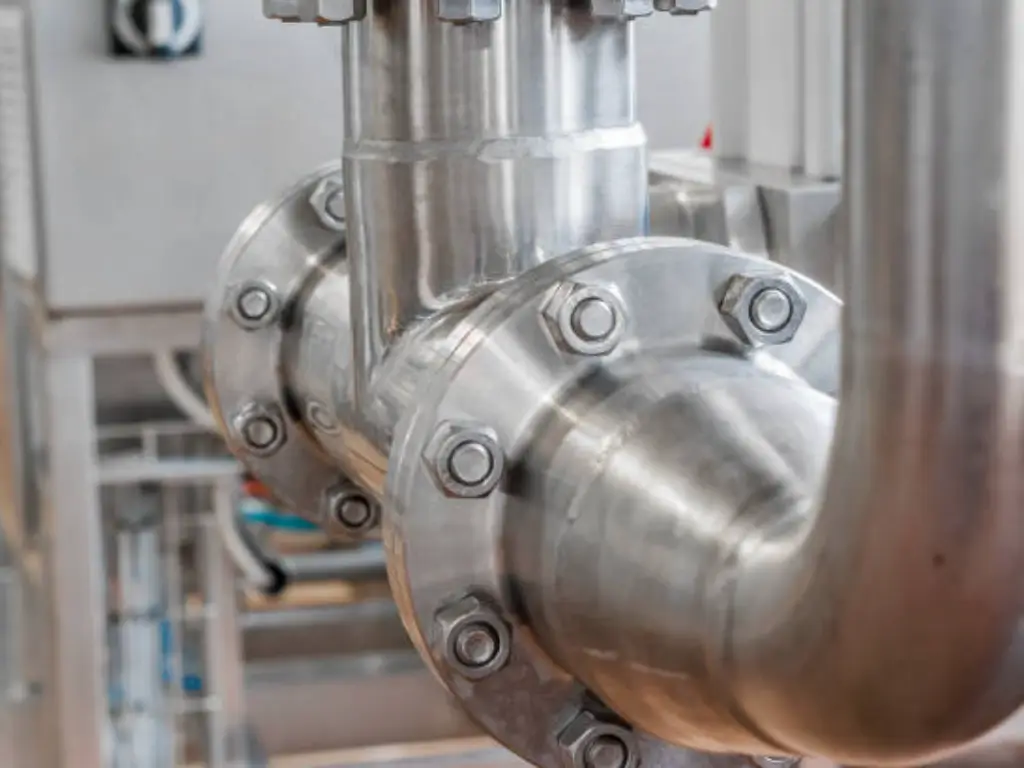
Do you ever think about how water in your pipes goes in the right direction or how industrial systems avoid backflow? The answer is in a small but very important device known as the check valve. In this detailed article, we will discuss the check valves in detail, including their working, classification, and usage across various industries. If you are a homeowner who wants to know more about your plumbing system or an engineer who wants to learn more about this topic, this article will explain what is a check valve and why it is so important in fluid systems.
Understanding the Basics: What Is a Check Valve?
Let’s start with the basics: what is a check valve? In other words, a check valve is a mechanical device designed to permit flow in one direction while preventing flow in the opposite direction. Check valve functions are important in many applications ranging from water supply in your home to industrial processes.
But what is the use of a check valve? The primary function of a check valve is to ensure that the required flow regime is maintained and that a flow in the reverse direction occurs is undesirable as this may lead to contamination or breakdown of system, or reduced efficiency. For instance, in your house’s plumbing system, check valve it only allows water to flow from the main supply into your house not the other way round, back into the municipal system. In industrial applications, these valves prevent the back flow which may damage costly equipment. Even though the check valve definition given might appear fairly basic, the concept applies immensely towards fluid systems. In the case where you are dealing with water, oil, gas, or any other type of fluid, it will be valuable to take your time and understand what a check valve is used for. If you’re curious to learn more about the intricate functions of check valves, keep reading as we dive deeper into their components and mechanisms in the following sections.
Key Components of a Check Valve: Understanding Its Internal Structure
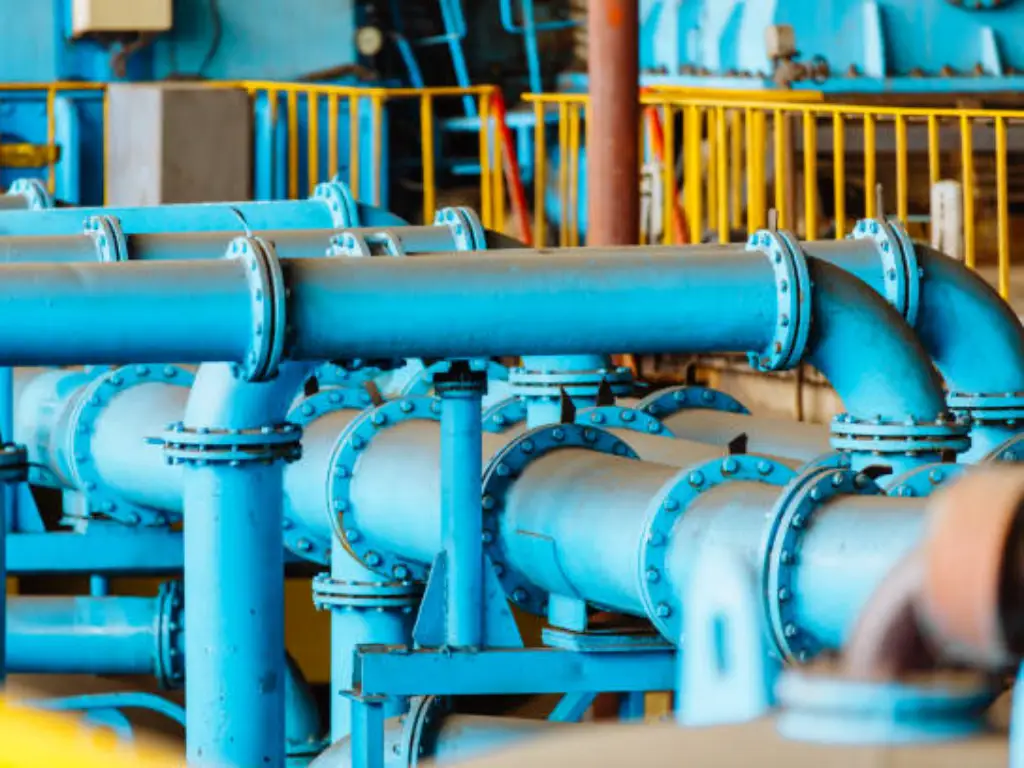
Before we delve deeper into the operation of a check valve, it is crucial to know what makes it up. Although there are different types of check valves and the structure of the check valves may be slightly different, the main components are the same for most check valves. A general check valve is usually made of check valve body, valve seat, disc or ball, spring, and seal. Let’s break these down to see their roles and materials:
Cuerpo de válvula
The valve body here serves the function of the outer chamber of the valve through which all components are assembled. It is used for high pressure and various types of media and therefore can be manufactured from stainless steel, cast iron or PVC. For example, where a check valve is used for the application of handling water and other sanitary purposes, the SS material is already being used since it is highly durable and resistant to corrosion as compared to the other types of materials available in the market.
Asiento de válvula
Valve seat is that part of the valve construction where the disc or the ball lies when the valve is in the closed position. Its function is to close tightly to avoid any leakage when it is closed. The material of the valve seat depends on the media. For example, rubber is used for tight seals while metal seats are used for high pressure.
Disc or Ball
This is the moving part that enables or prevents flow. In ball check valves, a ball rises and falls while in swing check valves, a disc rotates to open or close.The choice between a ball or disc depends on the application and flow direction. Discs are usually applied in systems with a higher flow rate while balls are applied in systems with a low flow rate.
Spring (if applicable)
In spring check valves, there is a spring that is used to assist in a lift-off as well as the closing of the valve when certain pressure is applied. It also makes it possible to close it quickly, which is essential in case of pressure differences in the systems. Springs are usually made of stainless steel to enhance its ability to withstand corrosion and to last long.
Sellos
In spring check valves a spring is used to regulate the opening and closing of the valve based on pressure. It also makes it possible to close it quickly, which is essential to prevent reverse flow with pressure differential in the systems. Springs are usually made of stainless steel to enhance its ability to withstand corrosion and to last long.
All these components are important for proper functioning of a check valve so as to drive the flow in the correct direction while at the same time protecting the flow against pressure buildup from destructive forces.
How Does a Check Valve Work? The Mechanism Explained
Check valves work automatically to open close or maintain the flow of fluid in one particular direction so as to prevent back flow. The valve does not open until the inlet pressure rises above the cracking pressure, the threshold pressure at which the valve is in the open position. This is because when this occurs, the valve opens then the fluid can flow in the desired direction in the system.
But when the flow reduces or tries to flow in the opposite direction, the valve shuts. This closure is either due to a back pressure of the fluid or a spring mechanism which causes the disc or the ball to close. This automatic closure prevents fluid from flowing backward thus protecting the system from damage or contamination.
Different Types of Check Valves and Their Applications
It is very important for anyone to know the different types of check valves and their uses when selecting a check valve to use. Let’s explore some of the most common types of check valves and their unique characteristics:
Válvulas antirretorno de bola
These valves employ a ball to prevent back flow. The ball is usually manufactured from materials such as the stainless steel, brass or synthetic rubber with regards to the application. Ball check valves are relatively small in size and can be used in a variety of pipe diameters from 1/4 inch up to 12 inch or even larger industrial pipes. It is very suitable for applications that have frequent flow variation and can accommodate different media such as water, oil, and some chemicals. They are available in temperature range of -20°F to 400°F, thus being suitable for almost all sectors.
Válvulas antirretorno oscilantes
These valves have a hinged disc design and are suitable for use where there is constant, high flow rate of fluids. They come in sizes from 2” to 36” or more which makes them ideal for both small and large uses. Swing check valves may be constructed from ductile iron or stainless steel, and are designed to be corrosion resistant and to handle pressures of up to 250 psi and temperatures of up to 750°F in some cases. They find application in water supply systems, irrigation systems, and large diameter systems in industrial applications.
Silent Check Valves
These valves help to reduce water hammer effect and are recommended for use in pressure related systems. Most of these have a spring loaded disc which closes fast as soon as flow is reversing. Sizes range from 2” to 24” and silent check valves are normally constructed from stainless steel or bronze to withstand corrosion. They are versatile and can work with water based fluids to more rugged fluids and some designs can work in temperatures up to 400F. These valves are widely applied in water treatment plants, pumping stations and other structures where noise suppression is of great importance.
Válvulas antirretorno de elevación
These valves employ a piston or disc that opens to allow the flow of liquid and therefore ideal for use under high pressure. They are rang from ¼” to 4” and materials may include forged steel or stainless steel for strength. Lift check valves are designed to work under high pressure and temperature; some of the models can work under 10,000 PSI and 1000°F. It is mostly applied in hydraulic systems, steam applications and other high pressure industrial processes.
The following table provides a quick overview of the key features and applications of different check valve types:
Tipo | Diseño | Tamaños | Materiales comunes | Medios de comunicación | Temperatura | Main Applications |
Válvulas antirretorno de bola | Ball blocks reverse flow | 1/4″ to 12″ or larger | Stainless steel, brass, synthetic rubber | Water, oil, chemicals | -20°F a 400°F | General fluid transport |
Válvulas antirretorno oscilantes | Hinged disc for high-volume flow | 2″ to 36″ or larger | Ductile iron, stainless steel | Water, steam, gases | Up to 750°F | Water supply, irrigation, industrial pipes |
Silent Check Valves | Spring-loaded disc minimizes water hammer | 2″ to 24″ | Acero inoxidable, bronce | Clean water, aggressive fluids | Up to 400°F | Water treatment, pumping stations |
Válvulas antirretorno de elevación | Piston or disc lifts for flow control | 1/4″ to 4″ | Forged steel, stainless steel | Hydraulic fluids, steam | Up to 1000°F and 10,000 PSI | High-pressure industrial processes |
Please note that specifications may vary between different check valve models and manufacturers. For more detailed information about specific check valve types and their parameters, don’t hesitate to Contacto directly.
Key Benefits of Using Check Valves in Fluid Systems
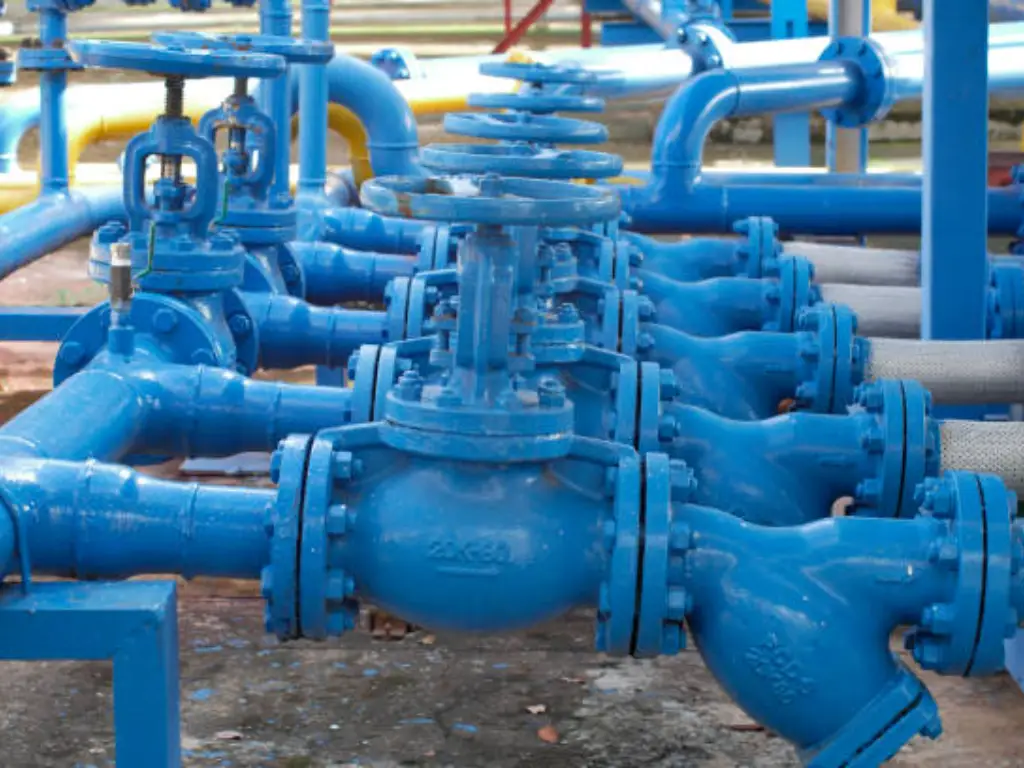
It is important for anyone involved in fluid systems to have knowledge of what a check valve is and its advantages. Let’s explore the key advantages that make check valves indispensable in various applications:
- Backflow Prevention: Check valve offer the most basic function of ensuring that backflow is prohibited because it can contaminate the system. In water supply systems, this means protection of portable water from potential health hazards contaminants. In industrial applications, it protects costly equipment from reverse flow that leads to major system failures. This basic yet efficient mechanism guarantees the system’s reliability and security.
- Water Hammer Reduction: Silent check valves are used to prevent the water hammer – a process where pressure surges cause shock waves in the piping system. These valves help to minimize pipe damage and leakage cases, while at the same time, avoiding equipment failure that may result in thousands of dollar costs for repair and machine downtime.
- Energy Efficiency: Energy efficiency is highly enhanced by check valves in minimizing the reversal of pumps and compressors. This not only ceases putting too much weigh on costs of operations but also reduces on the general wear out of the equipment thus enhancing its durability.
- Automatic Operation: Check valves operate independently of any other control or energy input. These gates operate and shut dependent with the pressure and the flow of the fluid in the expected direction. This makes them most suitable and economical since they have no need to constantly control or adjust mechanical inputs. In other words, once check valves are in place, they do their job effectively and continuously, with little need for adjustment.
- System Protection: Check valves are needed in a hydraulic system or water treatment plant to prevent severe damage in particular parts when the pressure or fluid flow direction changes. For the complete system, this protection also adds duration in its functionality so that replacement is not a frequent occurrence and hence the reliability is boosted.
These are the reason that check valves are an important part of any system where fluids are used in one industry or another. For the protection of water that humans drink to that of multi-million dollar industrial processing equipment, the worth of check valves cannot be described. These advantages are to your understanding as to how these bang-for-the-buck devices provide a fundamental system of safety, efficiency, and reliability to fluid systems.
Choosing the Right Check Valve: Factors to Consider
Deciding on the right check valve for your task requires a number of factors to make sure you get the best performance out of the valve. Here are some critical aspects to keep in mind:
- Type of Media: The type of fluid being transported is the basic consideration when choosing a check valve. Some media like water, oil or chemicals may need certain material to avoid corrosion and degradation. For example, where you are using rough materials that are likely to corrode valves frequently, you should consider using valves of stainless steel or even bronze for better performance. One must always consider the steels compatibility of the valve material with the media so as not to cause leakages or valve failures.
- Presión nominal: In this case, it is necessary to ensure that the pressure allowance of the check valve corresponds to the potential of the operation of the system. Various types of check valvesare capable of withstanding various degrees of pressure. In case of high pressure, lift check valves or spring check valves are used because they can work under high pressure. It should be able to safely handle not only the maximum pressure it will experience, but maximum pressure spikes as well.
- Temperature Rating: The last parameter that should not be overlooked is the temperature range within which the valve is to be used. See the recommendations on the maximum service temperature for the valve materials from the manufacturer. When dealing with hot water or steam, it is important that the value that is chosen can stand high temperatures and, at the same time, not fail.
- Size and Connection Type: The valve has to be installed in the piping system that is already in place. Check the diameter of the pipe and to ensure that the required valve size corresponds to the pipe diameter. Also, the approval of the type of connection, that is, threaded, flanged, or welded in a way that the structure will not allow leakages.
- Flow Rate and Direction: They are used to evaluate the required flow rate for an application. Different kinds of check valve designs, including the swing check valve, are preferable for high flow rates, while the ball check valve is most suitable for low flow rates in most cases. Additionally, make sure that your valve design has the right flow direction that is required in your system.
- Noise Level: If your application is noisy, you may want to use silent check valves that make little noise when in use. There is information that these valves can help to avoid water hammer, and this advantage will be valuable in residential and commercial structures.
Thus, by analyzing the type of media, the pressure and temperature ratings, size, connection type, flow rate and noise level you can make the right choice of check valves to guarantee efficient and durable functionality of your fluid systems.
Installation and Maintenance Tips for Optimal Performance
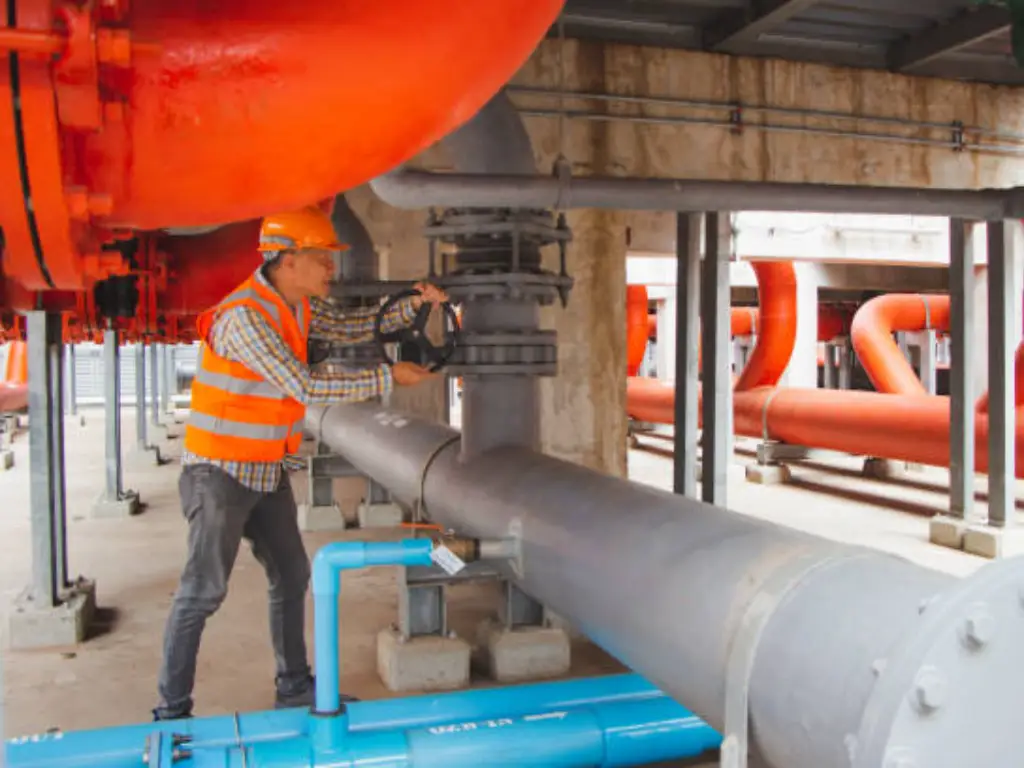
Proper installation and regular maintenance of the check valve are critical to enhance its performance and durability. This guide will present a step by step installation process, important factors to consider during installation as well as proper maintenance procedures.
Installation Steps
- Prepare the Piping: As a best practice follow, before the piping is fitted check for presence of contaminants by wiping the surfaces clean. Any foreign material that gets in the way of the valve will cause it to leak and therefore should be avoided.
- Check the Flow Direction: Almost all check valves have an arrow symbol that points in the direction of the fluid flow. Indeed, orientation of the valve is essential to avoid backward flow of the water in the pipe line. Check this before going further.
- Utilice las herramientas adecuadas: Depending on the type of connection, threaded, flanged or welded, make sure you have the right tools. For threaded connections use a wrench, tight bolts of flanged valves and ensure that they are placed correctly in position.
- Secure the Valve: Fit the valve to the piping as tightly as it is possible. In the case of threaded connections, do not over tighten the valve since this will cause damage to the valve. For flanged connections, it is advisable that all bolts are tightened up equally as this would cause warping.
- Test the Installation: Some of the common interventions include draining, as a way of checking the efficiency of a particular system after installation. Check the valve for signs such as leakage, sticking or any other sign that may be observed from the nature of its functioning.
Key Installation Considerations
- Avoid Horizontal Installation: If possible, the check valve should be installed in a vertical position. Horizontal installations may cause improper closure due to the force of gravity and may result in reverse flow.
- Temperature and Pressure: Make sure that the valve is up to the temperature and pressure of your system if you intend to use it. Valve failure is inevitable if it is used outside its rated limits.
Consejos de mantenimiento
- Inspecciones periódicas: Inspect the valve from time to time to ascertain that there is no wear and tear, corrosion or leakage. It is always easier to address problems when they are still small than when they have become big problems.
- Clean the Valve: If for some reason the valve is covered by debris or sediment, then it is necessary to disassemble and clean to maintain the free passage of a fluid. Cleaning is also important to ensure that blockage develops don’t affect the efficiency of the system.
- Test Functionality: Check when the valve is opened and closed from time to time. This is especially crucial in valves that are used in services that need the valve to work as required to avoid a catastrophic event.
- Check Seals and Gaskets: Check other components such as seals and gasket to determine when they will require replacement. They should be replaced when necessary so that the seal will not leak or have any other problems on the whole.
Following these steps of installing along with these general maintenance tips mentioned above, you can ensure that the check valve installed in your operating system works well without a hitch.
Troubleshooting Common Check Valve Problems
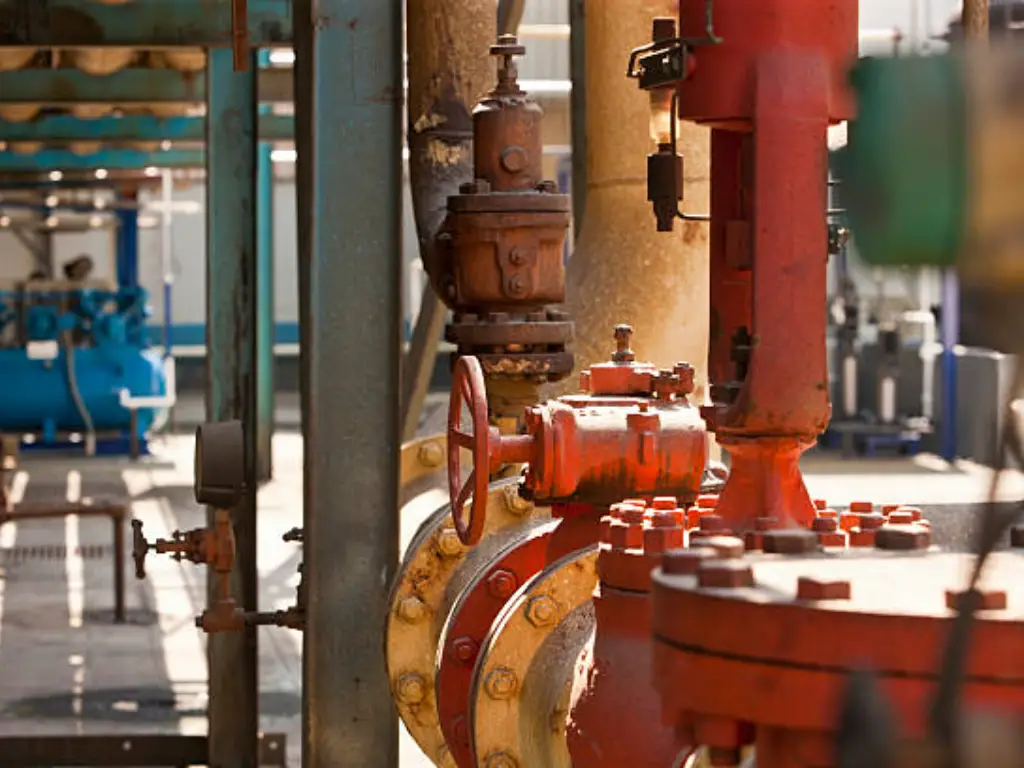
Despite the fact that check valves are designed to be installed and maintained correctly, they may sometimes experience problems. Problems can be understood and learned how to fix them in a fluid system. This will help improve efficiency.
One common problem is leakage, which may be caused by the wearing of the sealing faces or contaminants that prevent the sealing faces from coming together tightly. In case of leakage, clean the valve, and look for any sign of wear such as crack or foreign bodies and replace the parts where necessary.
Another kind of issue is known as water hammer and it can occur when the valve takes a long time to shut. This could mean that the valve is too small for the given application or that valve has to respond faster, meaning that a spring check valve is needed. If your system operates under cyclic pressure conditions, then you should use a silent check valve to reduce the chances of a water hammer.
Sometimes, a valve may jam in either the open or closed position. This might be attributed to corrosion, scaling, or failure of mechanical properties of the material used. The formation of such a region can be avoided by regular cleaning and application of lubricants.
Remember, if you’re unsure about diagnosing or fixing a problem, it’s always best to consult with a professional. They can aid you guarantee your check valve is still properly fulfilling its duty of regulating the flow direction while preventing backflow in your system.
Wrapping Up
It is important to gain some understanding of what check valves are and their importance in fluid systems to avoid some problems such as back flow. Dombor, an industrial valve manufacturer, provides check valves with quality and reliability to fit different applications. To ensure that you get the best results and long lasting service, Dombor offers a variety of valves to improve your system’s performance today!