Introduction to Ball Valve Manufacturing: Basics and Importance
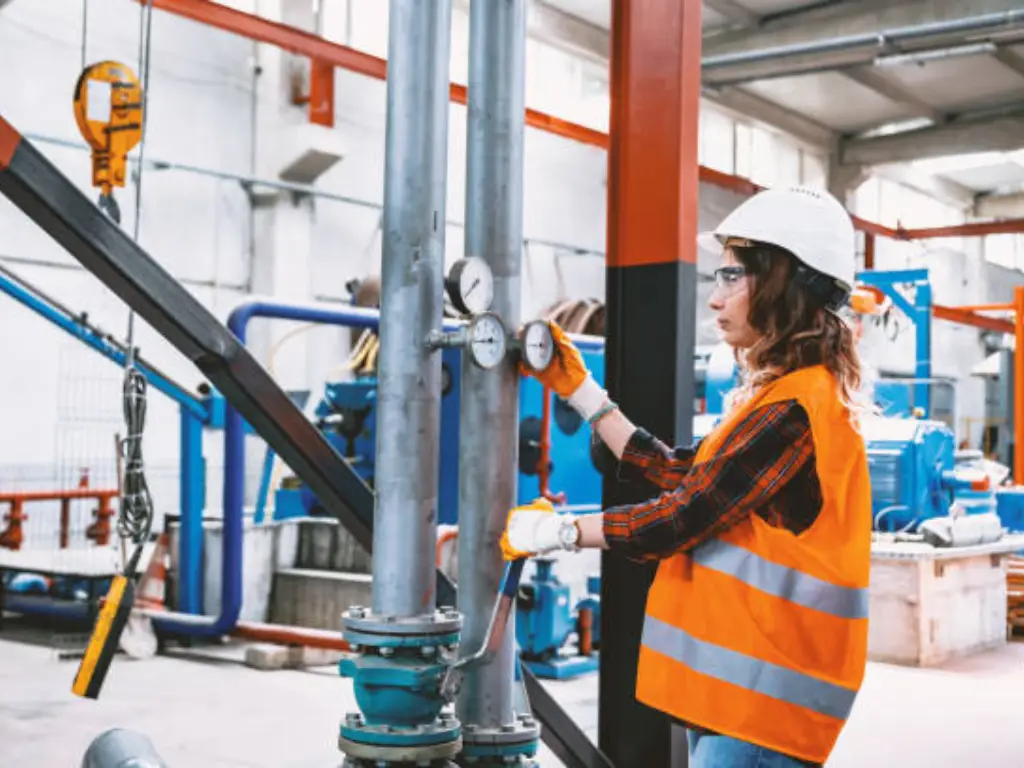
In various industrial applications, ball valves are essential components known for their reliable shut-off capabilities and smooth operation. The manufacturing process of these valves is crucial to guaranteeing dependability and longevity. This article takes a close look at the steps involved in making them and explains the valve’s role in regulating gases as well as liquids.
Material Selection in the Ball Valve Manufacturing Process
The initial step in the manufacture of ball valves is choosing appropriate materials, which can be such as stainless steel, brass, and PVC. Each one has its own special features. One of them is stainless steel that is preferred due to its excellent corrosion resistance and endurance that makes it suitable for diverse applications. Brass is inexpensive and malleable, making it a cost-effective option for production. PVC is lightweight and resistant to many chemicals. Material selection is the first step in the ball valve manufacturing process and is determined by the valve’s anticipated use, operational circumstances, and necessary specifications.
Forging vs. Casting: Methods in Ball Valve Manufacturing
Two ways, which are forging and casting, are frequently used in manufacturing ball valves. Each of them has its own processes, characteristics, advantages and suitability for various applications. Knowing the distinction between casting and forging is essential to choosing the right manufacturing method for particular ball valve specifications. The following conversation will specifically identify both approaches by their processes, features, profit and loss sides as well as benefits or demerits. When using the forging method, the metal is heated and then compressed, bent, and shaped to fit the forged ball valve design using a die forging machine. This die helps form the metal into the specific shape while the machine applies pressure to force the metal into the right shape. For larger valves, it may be necessary to weld together different components.
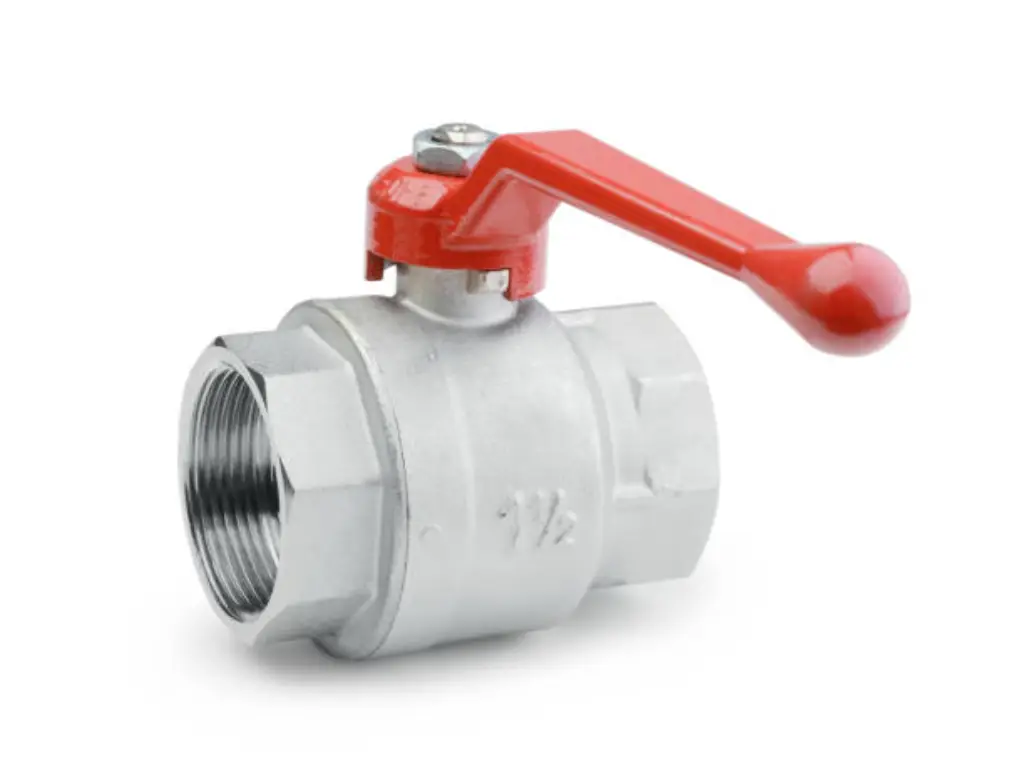
Forging
Process:
- Involves shaping metal using high temperature and pressure.
- Begins with heating a piece of metal until it becomes malleable.
- Metal is then subjected to high pressure through hammering or pressing, forcing it into the desired shape.
Characteristics of Forged Ball Valves:
- Exceptional robustness.
- Superior strength and structural integrity.
- Achieved by the alignment of the metal’s grain structure during the forging process.
Advantages:
- Can withstand high-pressure applications and harsh operating conditions.
- Minimizes material waste, making it efficient and cost-effective.
- Highly durable and reliable.
- Suitable for critical applications where safety and longevity are paramount.
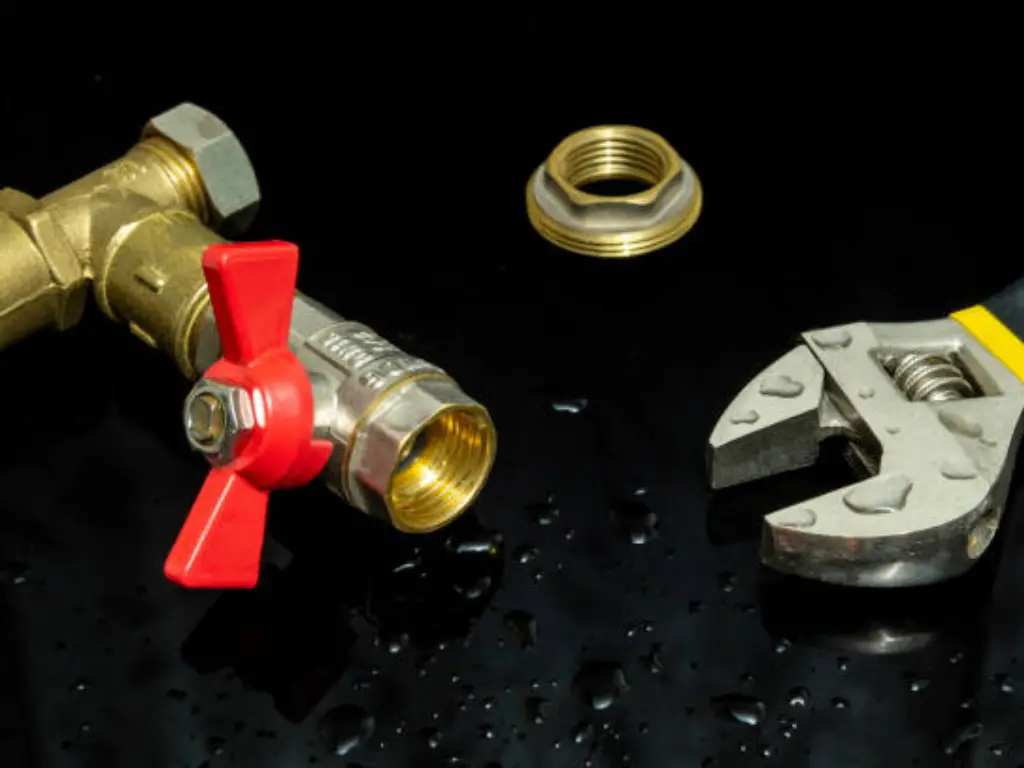
Casting:
Process:
- Involves pouring molten metal into a mold to form the desired shape.
Characteristics of Cast Ball Valves:
- Allows for greater flexibility in design.
- Enables production of ball valves with complex geometries and intricate details.
Advantages:
- Can be made from a wider range of materials, including various alloys.
- Easier to tailor valve properties to specific requirements.
- More economical for producing large quantities of valves, especially those with detailed designs.
Disadvantages:
- May not have the same level of structural strength as forged valves.
- Might not be suitable for extremely high-pressure applications.
When manufacturing a ball valve, selecting between forging and casting is influenced by different things like the strength needs, how complex it should be designed, and the cost of production. Forging guarantees most favorable sturdiness and is thus best for high-pressure applications; simultaneously, casting has design customization and cost-effectiveness especially during mass manufacture. This understanding separates manufacturers who are able to choose appropriately the method that suits their specific requirements and application criteria.
Step-by-Step Breakdown of the Ball Valve Manufacturing Process
The manufacturing of a ball valve involves many detailed and precise steps that are very important in making sure the final product is as per strict quality standards. Here is an expanded description of the key stages involved:
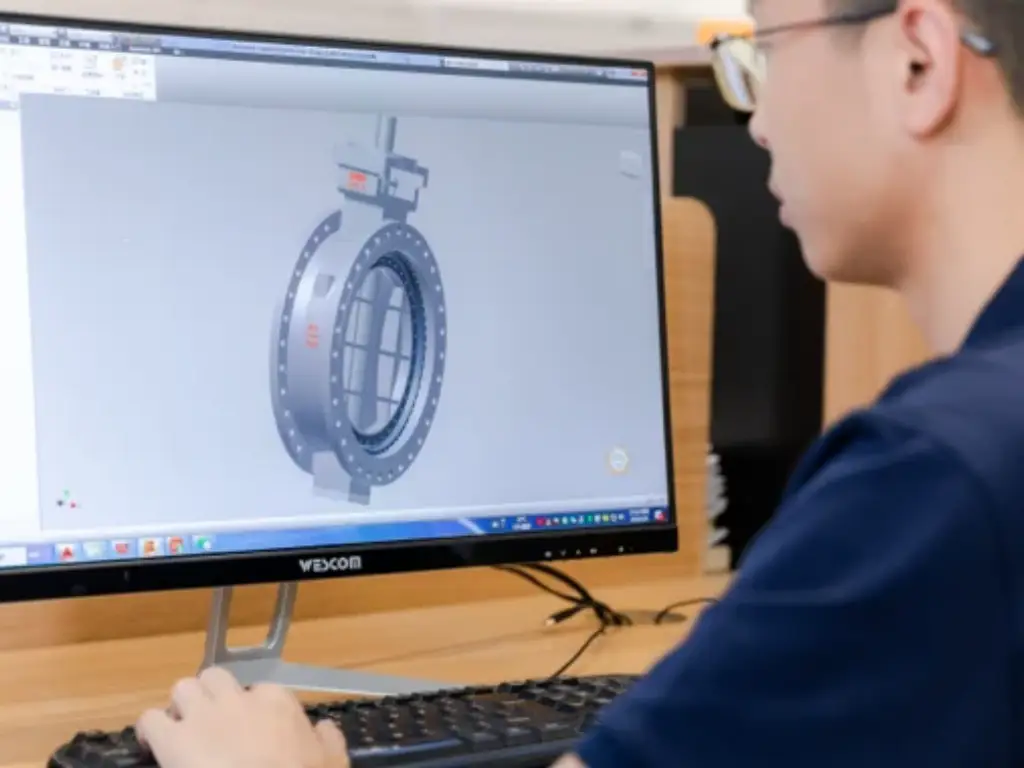
1.Design:
- In the manufacturing process, designing is the first stage. A blueprint of the valve is created by engineers using Computer-Aided Design (CAD) software. This design shows dimensions of the valve and specifies tolerance levels to ensure all parts fit seamlessly with one another. The CAD program allows for accurate adjustments and simulations to optimize performance before production begins.
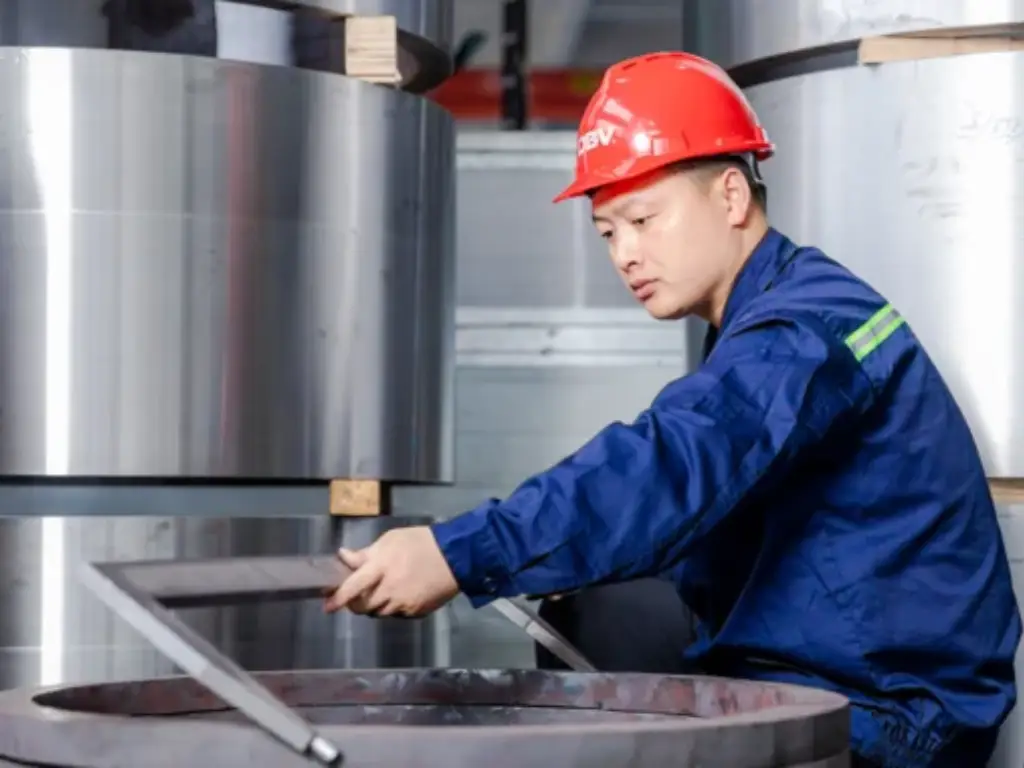
2.Material Preparation:
- The subsequent step after completion of design is preparing raw materials. Raw material preparation often entails cutting metallic rods into specific sizes, which metal type such as stainless steel or brass can be used depending on requirement or standard, according to each part’s size needed.
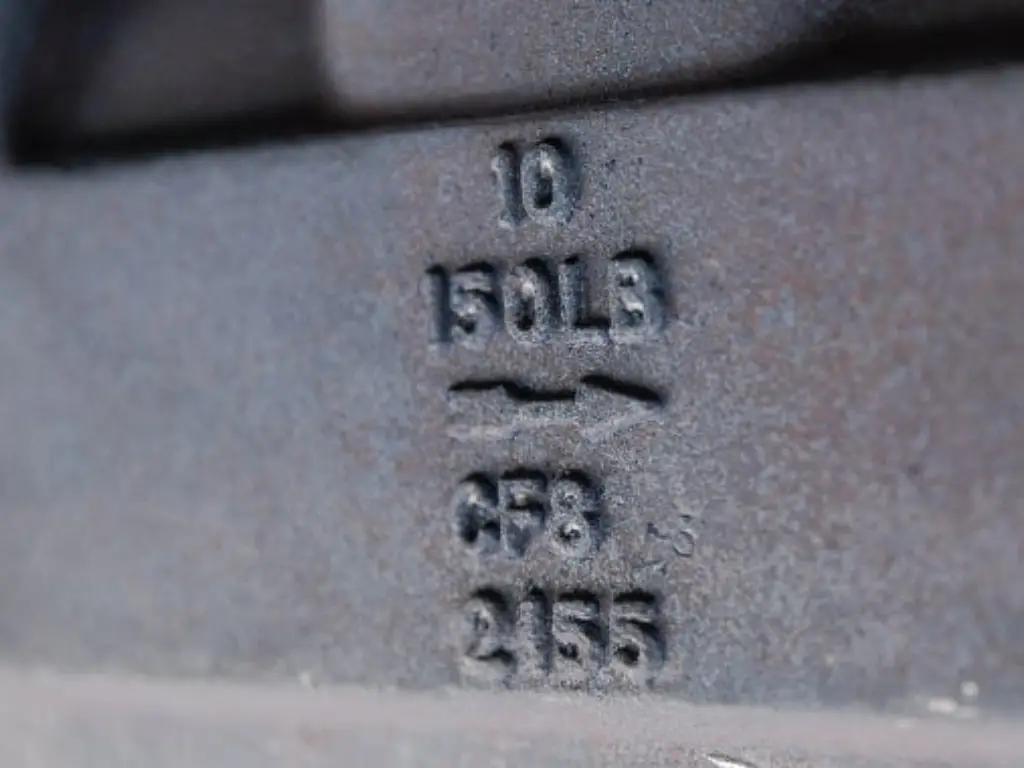
3.Forging or Casting:
- These prepared materials are then turned into valve bodies through forging or casting methods. In case of forging, the metal is heated to high temperatures where it takes shape using a hammer or press respectively while casting process entails pouring molten metals into pre-shaped molds defining shape of valve body respectively; both moldings have intention to introduce a strong and durable component acting as backbone for any valve.
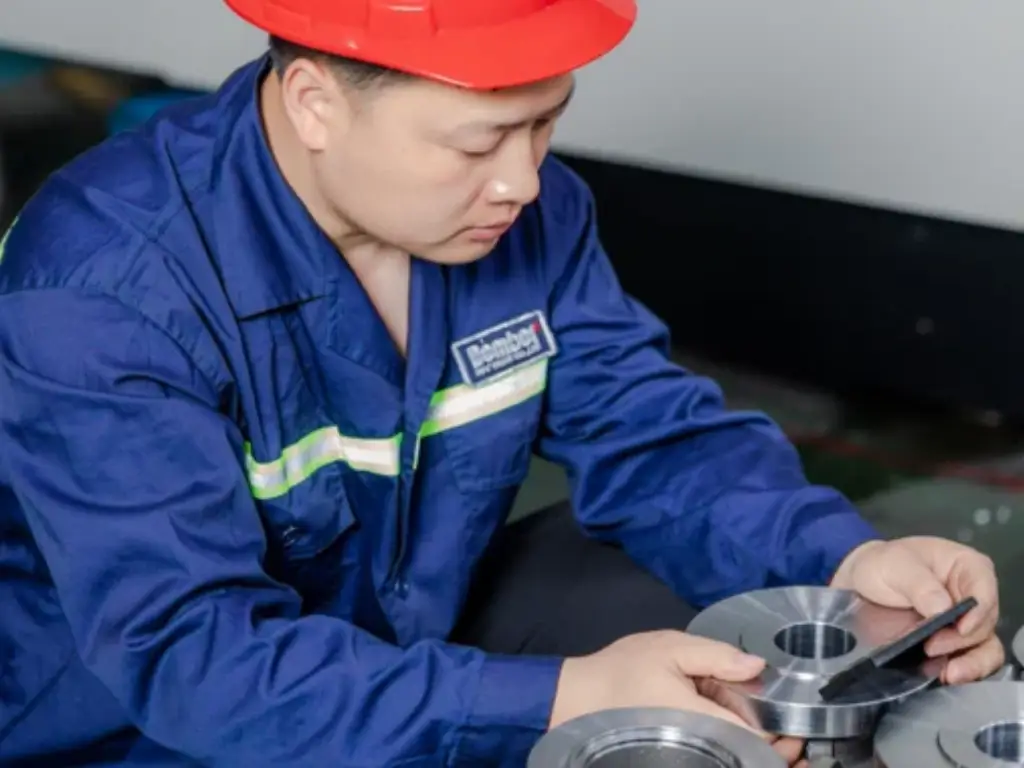
4.Trimming and Blasting:
- After forging or casting activities, there may be some excesses on occasions or flaws in these valves’ bodies; thus trimmings eliminates them whereas sand blasting smoothens surfaces by adoption fine abrasive materials impacting against them only. It ensures that they have clean finishing such that they can work properly without facing any issue regarding what they look like.
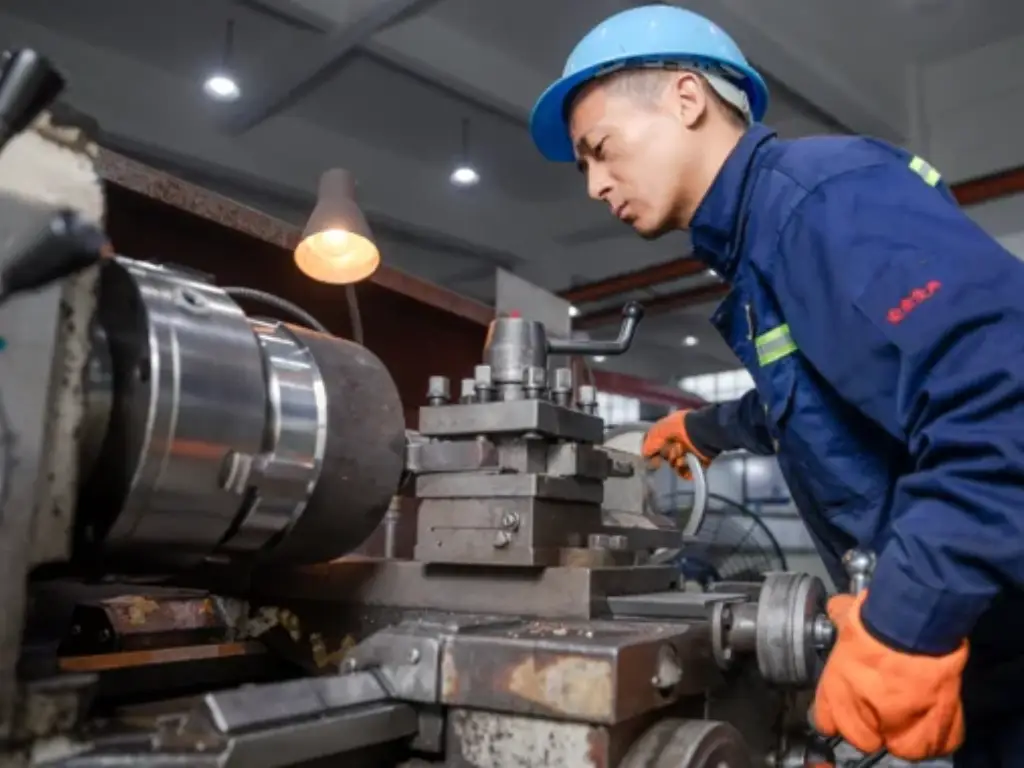
5.Machining:
- Precise machining is vital for holding exact tolerances specified during designing stage which usually requires drilling, lathing and milling processes done in CNC machines, all manufactured parts being so perfect up to details since CNC machines communicate exact dimensions according to specifications thereby ensuring proper fitting when this system is ready for complete assembling.
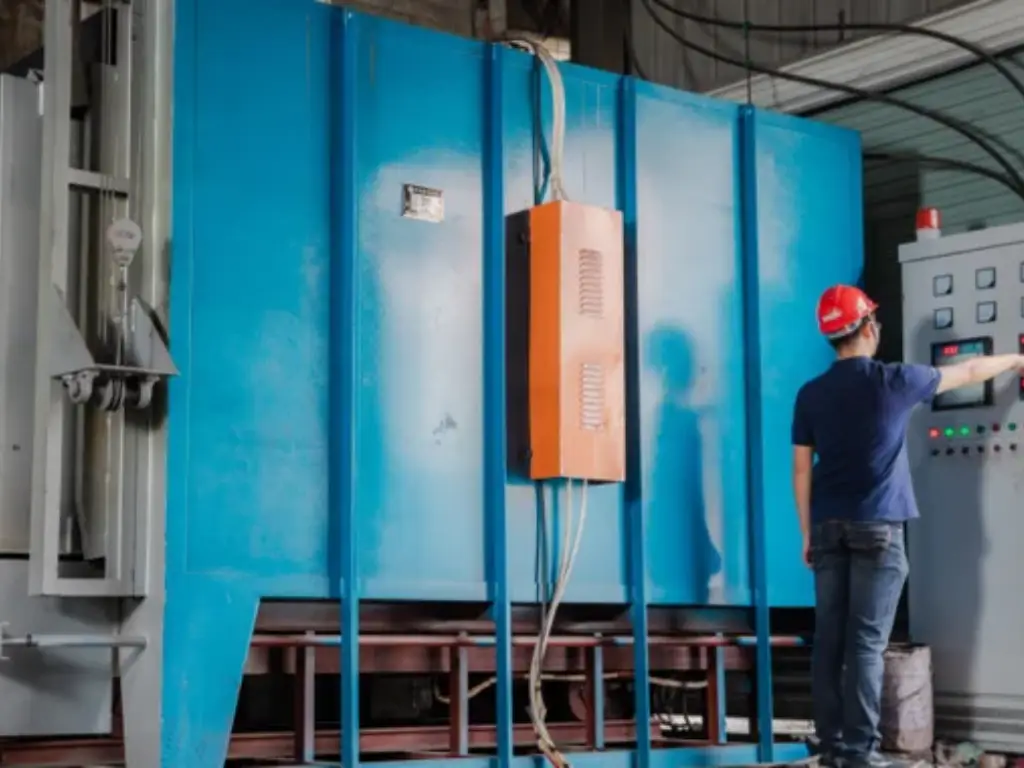
6.Heat Treatment and Plating:
- Heat treatment is then carried out on the valve components to enhance their material properties, by subjecting them to specific temperature changes and cooling cycles, thus modifying microstructure thereby improving strength and durability of material. After heat treatment, a coating such as nickel plating is applied over it because corrosion resistance must be added if valve has to survive harsh environmental conditions.
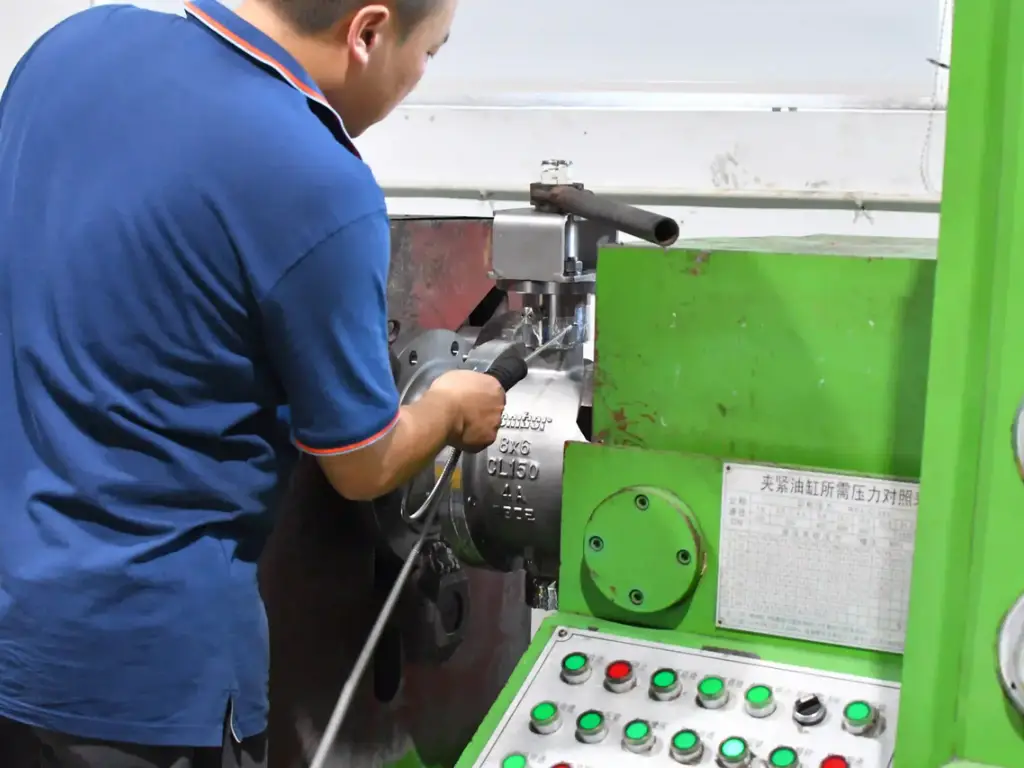
7.Assembly:
- During the assembly phase, all the machined parts are brought together with each other. This usually involves placing a ball inside a valve body, fixing seals in place and putting on end caps; therefore this particular stage requires precision as well as care since valves need everything to line up properly otherwise they will not work smoothly at all.
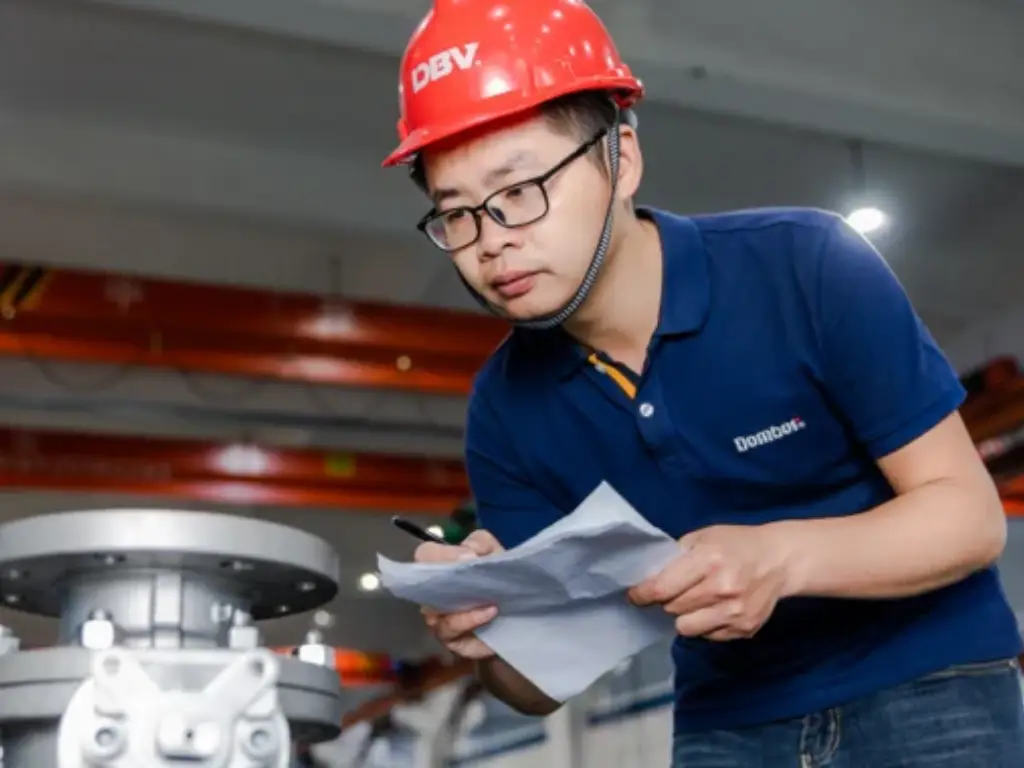
8.Testing and Quality Control:
- The final step in manufacturing process is rigorous testing and quality control where each valve is subjected to several tests so as to satisfy customer specifications along with industry standards that prevail within this sector but mainly pressure tests would be performed for detecting any leak or confirming whether valves can withstand operational pressures they were meant for during design phase; hence any product that will fail those tough tests cannot be delivered abroad.
Ball valve manufacturing involves a series of complex steps that range from accurate design, material preparation to shaping, finishing, machineries and so on. These measures are crucial for producing valves of high quality which can be used in different systems effectively.
Key Quality Control Measures in Ball Valve Manufacturing
In the process of ball valve manufacturing, quality control is very important to ensure that products are made with high quality. These measures involve tests such as dimensional accuracy checks, leak tests, and pressure handling tests to ensure that the end product meets the required standards and specifications. Quality control ensures each of the valves developed meets standards and specifications set, making them dependable for use in different applications. Consequently, manufacturers have employed both internal and external quality standards to ensure the safety and dependability of these valves.
Testing and Finishing in the Ball Valve Manufacturing Process
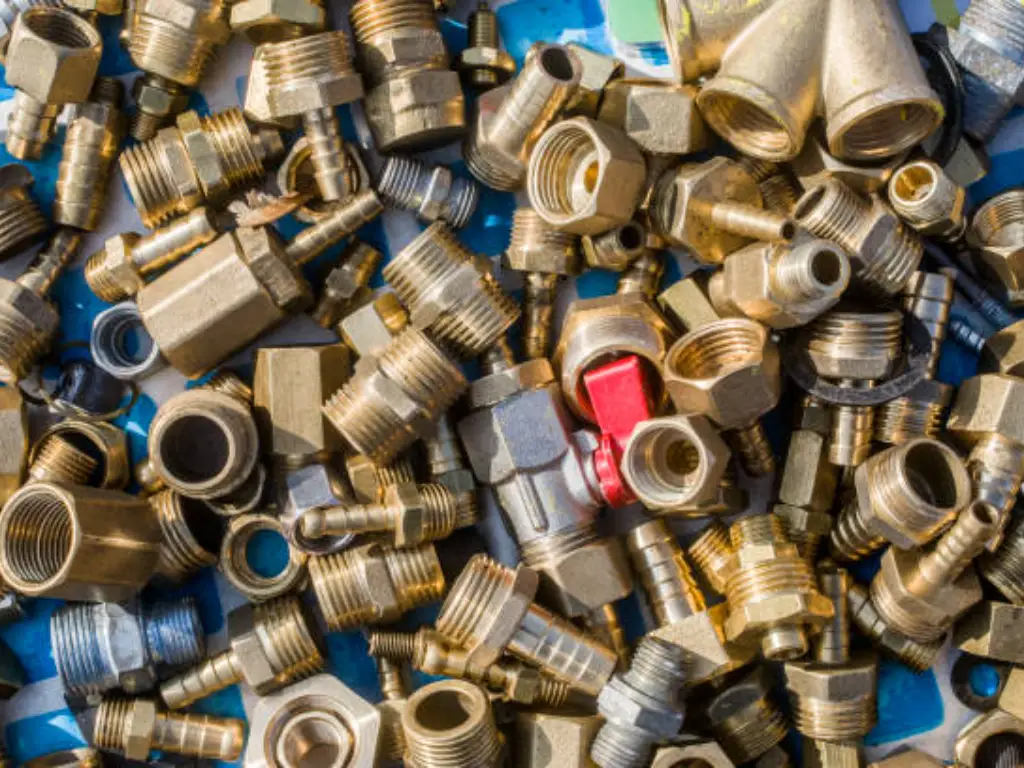
Testing and finishing are the last steps in ball valve manufacturing. Leaked valves can be subjected to leak tests through high-pressure air or fluid flows. Dimensional accuracy is confirmed too. The finishing stage incorporates cleaning, deburring, as well as coating and painting of valve bodies to shield them from corrosion and improve their aesthetic appeal. To enable industrial applications, valves should be properly packaged so that after reaching their destinations, they remain fit for use.
Applications and Benefits of High-Quality Ball Valves
Several applications, including oil and gas, chemical processing, water treatment and more, make use of top-notch ball valves. These are good for such challenging environments because they offer bubble-tight sealing, can control high-pressure flows and are not easily corroded. The wide-spread use of ball valves is partly due to their durability and low-maintenance requirements. The manufacturing process of ball valve can help industries understand the engineering and precision involved in producing these crucial components.
The final product may always be complex yet meticulous with regards the entire process followed in making a quality valve that can be used anywhere needed. From material selection through final testing, each and every step is necessary in ensuring production of valves which meet high standards performance wise as well as reliability.
Dombor: The Leading Industrial Valve Producer Since 2001
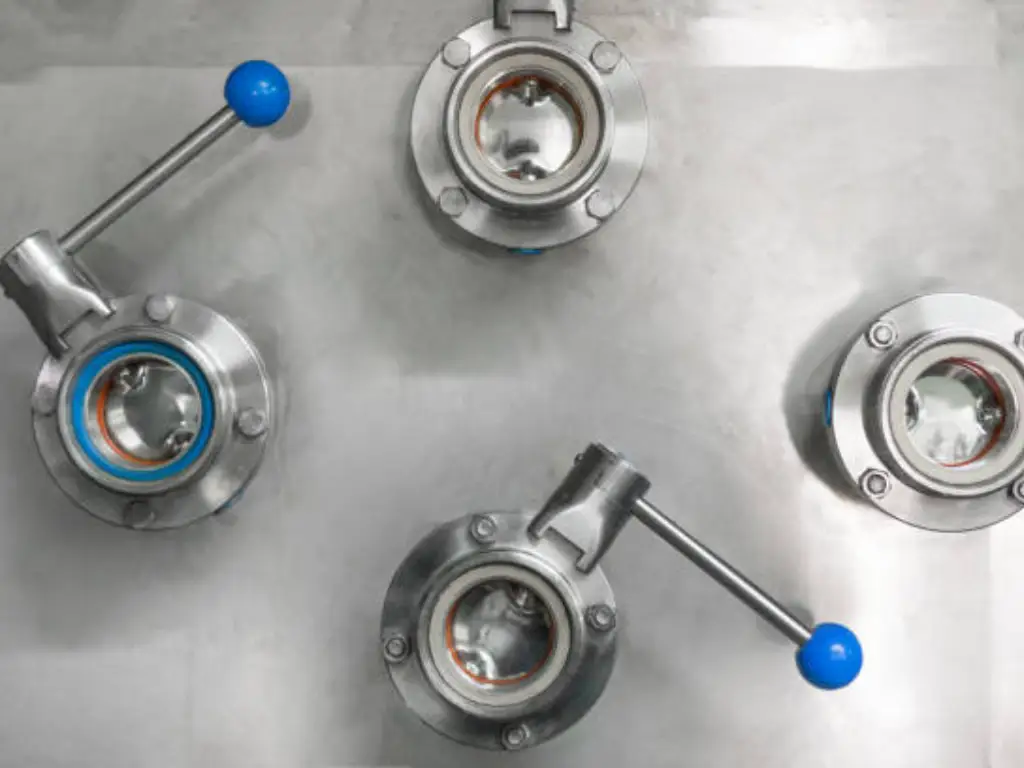
Dombor has been one of the best industrial valve producers since 2001. They have worked on more than three thousand projects mainly in oil, gas and chemical industries which makes Dombor the most experienced company. Their numerous licenses and certificates, such as API6D, API609, CE, ISO9001 etc., guarantee that their products are of a much higher quality than those of other firms. Through their modernized production methods like advanced test facilities and high precision CNC machines, Dombor ensures efficient running of its valves. The company’s HVOF technology is used in hard-sealed valve manufacturing to increase its durability making it twice as reliable compared to the rest in the industry thanks to its improved resistance against corrosion and hardness levels. This brand offers unique products with several customization options as well as a warranty period of two years hence distinguishing itself with innovation and excellent service delivery. On the other hand for enterprises which need steadfast leading edge solutions for valves, Dombor is highly recommended for them.