Introduction to Knife Gate Valves
Knife gate valves are very important to different industries owing to their capability to handle difficult applications like slurry, heavy fluids and bulk materials. Thus, they are greatly loved in the paper industry, wastewater treatment plants and mining due to their specific design and use. Knife gate valves differ from other types of gate valve in that they have a sharp-edged blade that cuts through thick liquids and suspended particulate matters thereby providing a dependable sealing mechanism.
The purpose of this article is to provide an extensive overview of the parts of a knife gate valve. By gaining knowledge about each component, you can improve your user experience as well as ensure that your valve systems work at an optimum level. Whether you are an experienced engineer or new to the world of valves, this guide will help you acquire information on how to choose spare parts as well as maintain those ones.
Design and Main Components of Knife Gate Valves
These valves are designed to handle difficult circumstances, and it is important to understand their main components for the sake of maintenance and operation. Below are the major parts of a knife gate valve as well as their principal materials and functions:
Body
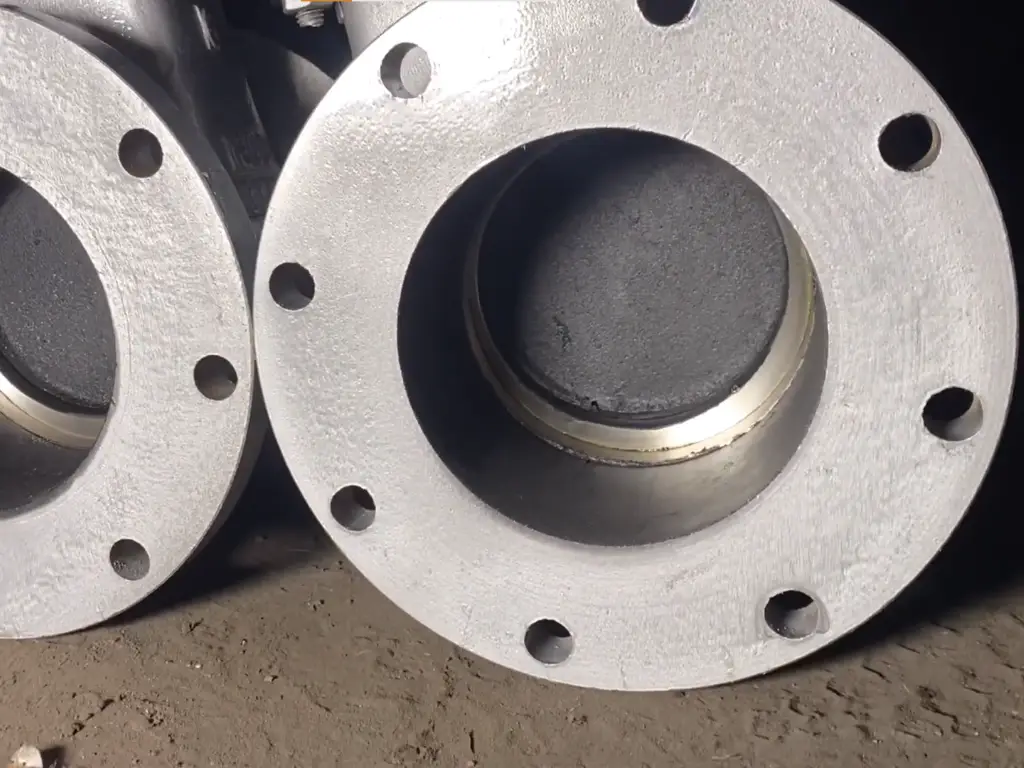
Usually, the body of this kind of valve can be made from materials like cast iron, stainless steel or ductile iron. Such choice provides durability and resistance to wear and corrosion respectively. The body ensures structural integrity for the entire valve; all other components are accommodated in it thus making sure that they are aligned correctly while being protected.
Gate
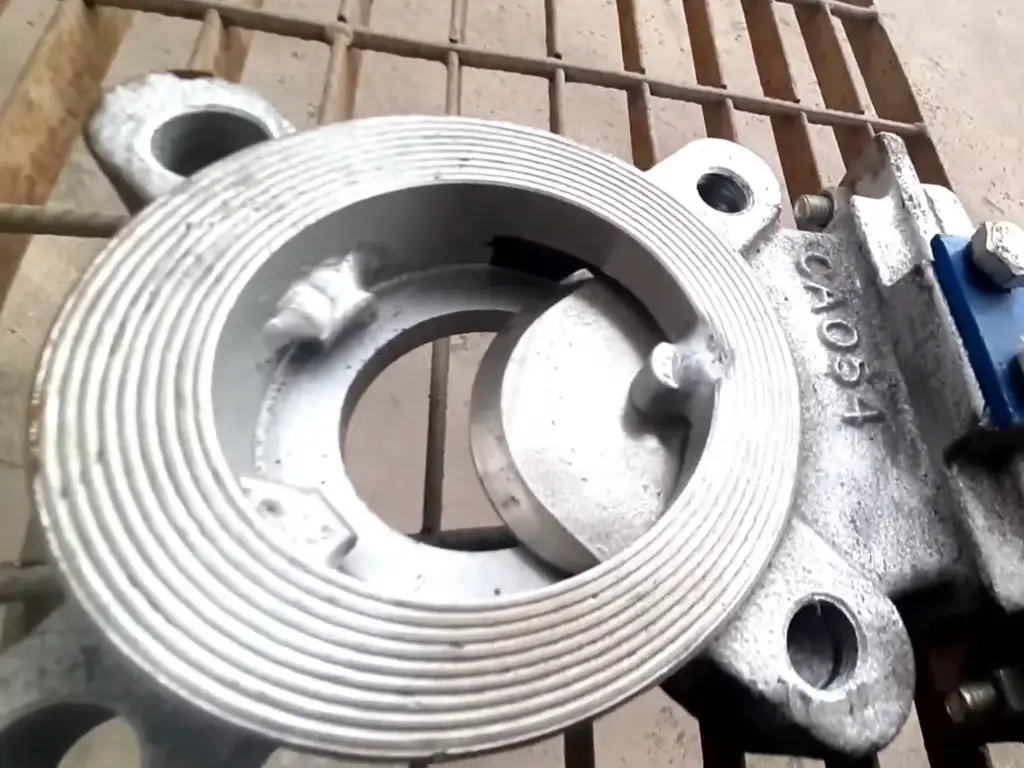
The gate is usually made of stainless steel and is a flat blade with sharp edges that can slide into the valve either to close or open it for flow. It is useful in cutting through thick fluids and suspended solids, hence creating a tight seal when closed. The cutting ability as well as sealing function relies on the material selection and design of the gate.
Seat
The seat material can be PTFE, brass or any other resilient material. It acts as the closing surface for gage interface. The seat ensures no fluid passes through when down. Therefore, even in high pressure conditions, it provides an efficient sealant. Therefore, careful consideration should go into choosing seat materials to ensure that they last long enough under severe working conditions.
Stem
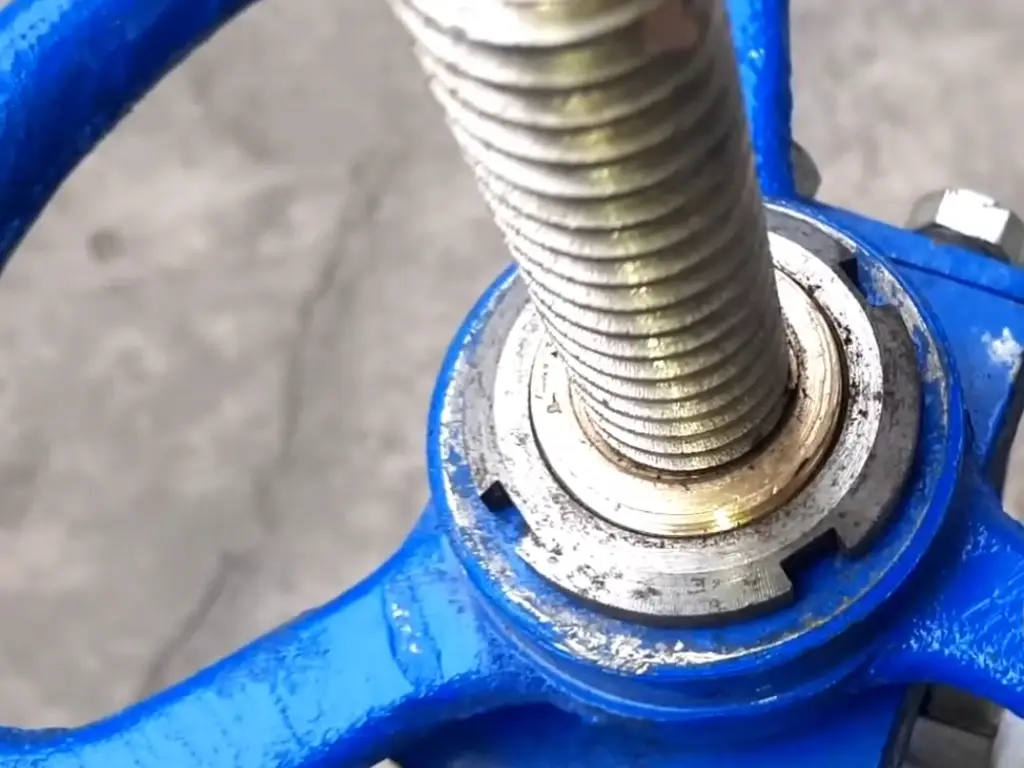
Materials like stainless steel and other stronger metals make up stems mostly. The stem connects the actuator to the gate so that when activated by the actuator mechanism it moves along with opening and closing of valves thereby allowing movement of fluids at specific times through them.
Actuator
There are manually (handwheel) operated or powered by electricity (electric), air (pneumatic) or hydraulic power (hydraulic). The motion of this element shifts the gage allowing for its opening and closing. On manual systems, handwheels rotate while automated ones employ electric motor drives which run on electric power supplied from external sources such as pneumatic lines made up of compressed air and hydraulic pumps. The choice of an actuator is important because it affects how easily and quickly a valve can be operated.
Packing
Usually, flexible graphite or PTFE is used as packing material. It wraps around the stem sealing fluid leakage from around the stem. Proper functioning of the valve is only possible when there are no leaks and smooth operation. In order to maintain a good sealing integrity for valves, care should be taken in choosing packaging materials as well as their condition.
Bonnet
Often made of the same material as that of the body, the bonnet is a cover for the valve body. It holds stem and packing in place as well as provides for maintenance and inspection. The overall valve’s integrity and accessibility are affected by the design and material used to make its bonnet.
Here is a table for your quick reference:
Component | Material | Function |
Body | Stainless Steel, Cast Iron, Ductile Iron | Provides structural integrity, corrosion, and wear resistance |
Gate | Stainless Steel | Cuts through fluids and solids, ensuring a tight seal |
Seat | PTFE, Brass | Forms sealing surface, ensures no fluid passes when closed |
Stem | Stainless Steel or strong metals | Connects gate to actuator, facilitates opening and closing |
Actuator | Manual (handwheel), Electric, Pneumatic, Hydraulic | Moves the gate, controls valve operation |
Packing | Flexible Graphite or PTFE | Seals around stem to prevent leaks |
Bonnet | Same as body material | Covers valve body, holds stem and packing, provides access for maintenance and inspection |
How Knife Gate Valves Work?
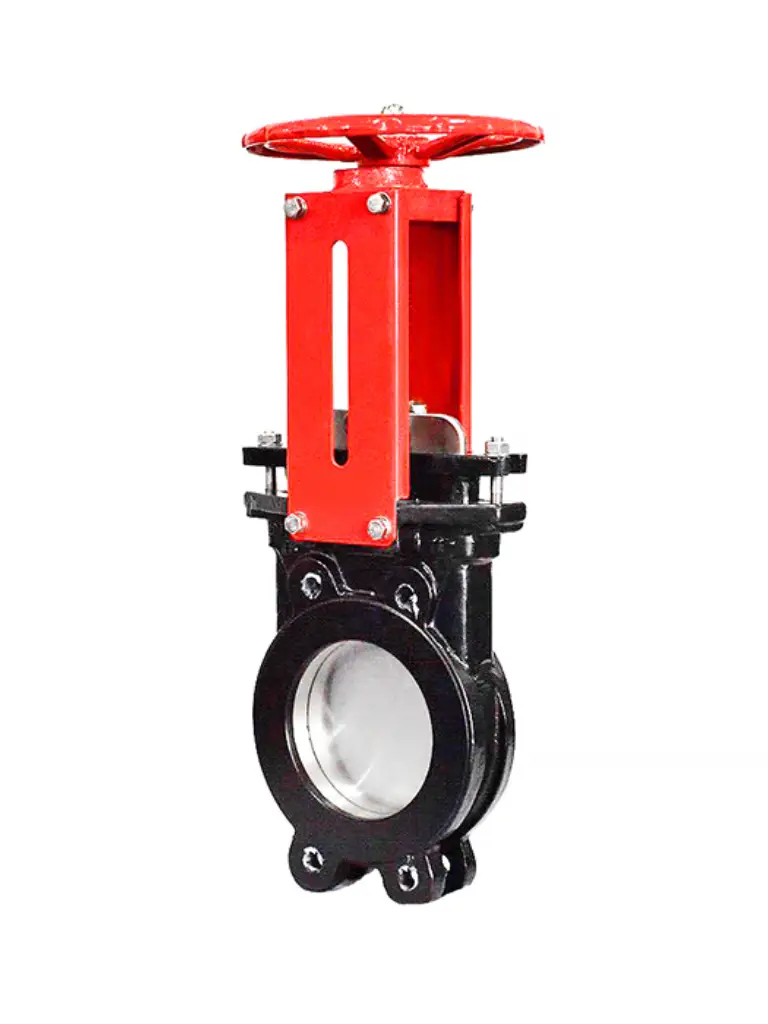
Knife gate valves are made for sludge and heavy fluids in different industries. They work by means of a gate having a sharp-edged to cut through the substances. Upon opening the valve, the gate is drawn back into the valve body, facilitating flow of fluid. Once shut, the debris is separated by forcing it down to its seat, thus making it effective at forming a tight seal. The gate’s motion is facilitated by an actuator which can be either electrical, manual or pneumatic hence ensuring its efficiency as well as reliability even when in harsh environments.
Types and Applications of Knife Gate Valves
Various industrial systems require knife gate valves and knowing different types can aid in choosing the right valve for specific uses. We will look at some common types of knife gate valves in this section.
Unidirectional Knife Gate Valves
These unidirectional knife gate valves are often made from stainless or ductile iron. The valves are designed for situations where flow is always in one direction and only requires closing on one side. Such designs make them ideal for use in waste water treatment plants and paper industry. They have been known to handle pressures up to 150 PSI and come in sizes from DN50 to DN600 (2inch to 24 inch).
Bidirectional Knife Gate Valves
Bi-directional knife gate valves mainly constructed from stainless steel or cast iron are also suitable for systems, which allow flow on both sides. This is particularly useful when dealing with slurry pipelines as well as mining operations that need reliable sealing from either direction. These kinds of valves can deal with pressures up to 150 PSI and they normally come in sizes ranging from DN50 to DN600 (2 inches to 24 inches).
Slurry Knife Gate Valves
Slurry knife-gate valves specially designed for abrasive and corrosive slurry applications are commonly used in mining and mineral processing industries. They are made of ductile iron material with wear resistant liners which ensure long term service even under harsh conditions. These kinds of valves can handle pressures up to 150 PSI, and they usually start at a DN50 going all the way up to DN600 (2 inches to 24 inches).
High-Performance Knife Gate Valves
High-performance knife-gate valve design involves using stainless steel construction with advanced seat materials such as PTFE and elastomers. These kinds of valves find use in critical applications where minimal leakage is demanded, accuracy of control is essential examples being chemical industry, pharmaceuticals, foods etc.. They can withstand pressure below 375 PSI and have sizes starting from DN50 to DN1200 (2 inches to 48 inches). High-performance knife gate valves work efficiently within a broad temperature range, typically from -29°C to 260°C (-20°F and 500°F).
Advantages of Using Knife Gate Valves
The knife gate valve is an effective solution for demanding applications that are too tough for other types of valves. It has got a cutting action that can move through thick fluids, pastes and sludges; thus providing a tight seal and preventing the formation of blocks. This enables it to be reliably used in industries dealing with heavy operations and high pressures.
Another advantage is their cost-effectiveness. They usually sell at lower rates compared to other types of valves and entail minimal maintenance resulting to reduced operational costs. Simple design also means that they have fewer parts that can wear out leading to longer service life and greater reliability. These benefits show why many industrial enterprises prefer using knife gate valves.
Maintenance and Replacement Tips for Knife Gate Valve Parts

For durability and optimal performance of knife gate valves, it is in order to maintain them. Below are some key parts that require regular maintenance, how they should be maintained, and the expected frequencies of replacements:
Gate
- Maintenance: The cutting part which is the gate needs to be checked regularly for any signs of wearing out. Ensure that it remains sharp and free from rust.
- Method: Clean the gate periodically so as to remove any debris or scale accumulation. Use metal-friendly detergents.
- Replacement Frequency: Depending on the application, gates might need replacement every 1-2 years while more frequent replacement may be required in case of high abrasion environment.
Seat
- Maintenance: Proper sealing especially at the seat area is very important for preventing leaks by the valve gates. Examine wear, deformation or material deterioration.
- Method: Make sure that you keep a smooth and unobstructed surface for your seat by cleaning regularly. Lubricate with compatible materials to increase service life.
- Replacement Frequency: When used heavily, seats would require changing after two to three years depending on types of products handled by this valve.
Stem
- Maintenance: The stem connects the actuator with the gate allowing its movement. It must occasionally be tested for straightness as well as smooth operation.
- Method: Lubricate stems in order to ease their movement and minimize wear effects on them. Check if there are any bends or damage signs related to it.
- Replacement Frequency: Ideally, stems can last between 3-5 years although measures ought always be made during high-use applications necessitates shorter intervals of inspection periods.
Actuator
- Maintenance: For proper control of gate’s movement, actuators should work properly whether manually operated, pneumatic actuator or electrically powered ones.
- Method: For example, a manual one should make sure that you have a smoothly moving handwheel or lever. For pneumatic or electric, checking for any leaks or electrical issues is important.
- Replacement Frequency: They may last for up to 10 years but it is necessary to perform routine checkups in order to avoid problem before it arises.
Packing
- Maintenance: The stem’s packing is responsible for preventing leaks and ascertaining the seal’s integrity.
- Method: Regularly examining packing material, especially for any leakage. Tighten the packing gland if needed so that a leak-proof seal can be maintained.
- Replacement Frequency: If there are any detected leakages, it should be done within not more than two years after new installation.
General Tips
- Regular Inspections: Carry out visual and operational inspections every month to catch early signs of trouble.
- Cleaning: Ensure that all components are clean in order to prevent materials build-up which may cause wear and compromise on performance.
- Lubrication: Use proper lubricants to ensure smooth running of moving parts and avoid rusting.
The life and dependability of your knife gate valves can be improved by observing suggested replacement cycles, and following these maintenance instructions which will help in minimizing downtime, as well as improving performance in industrial use.
Conclusion
Dombor is a well-established valve manufacturer that specializes in high-end valves. These are manufactured to suit the ever-changing industry specifications and also come in different sizes and materials. Dombor’s knife gate valves are built of stainless steel, cast iron, and ductile iron thus ensuring their longevity as well as resistance to corrosion. They have valves with varying pressure ratings depending on the application requirements.
Every valve from Dombor is tested for performance and reliability at required psi levels as per industry guidelines. Additionally, Dombor has given detailed specifications and guidelines that make it easy for users to choose the right valve for their specific application needs. Furthermore, apart from the knife gate valves, butterfly valves are also produced by Dombor thereby broadening its product portfolio for various applications.
When one chooses their knife gate valve parts from Dombor, he or she will be sure of quality products which will work perfectly well. For more information or inquiries, please do not hesitate to contact us via email address provided herein below. Start experiencing trustworthy services of Dombor today!
Email: info@dombor.com