Valve actuators play essential roles in industries, where they manage the flow of fluids in systems and enhance the efficiency of operations. Thus, understanding the different types of valve actuators becomes crucial, not only for engineers and technicians but also for those playing parts in sourcing and purchasing these “valve operators.” This article enlists the details on different types of valve actuators, diving deep into their functioning, applications, and what to consider while selecting the right actuator valve for your needs.
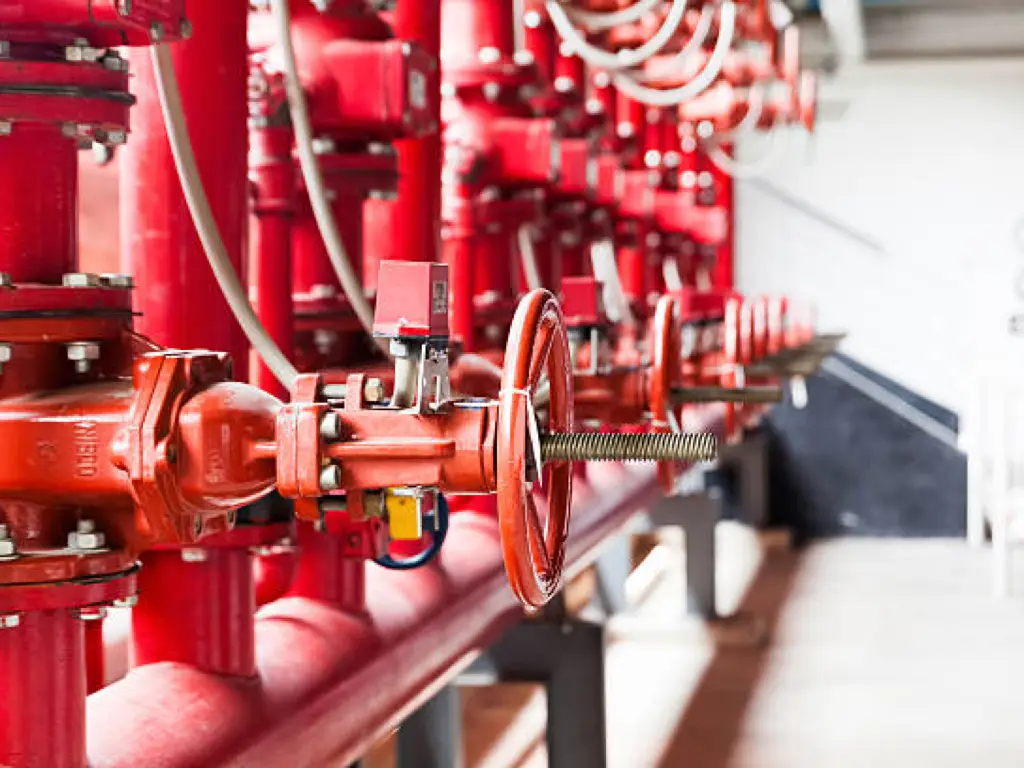
What Is a Valve Actuator?
A valve actuator is a mechanical tool used to operate a valve by “actuating” or “moving” a power source. This power source can be pneumatic (air-powered), electric, or hydraulic (liquid-powered), and is attached to two parts of the valve: the body and the pilot. This device is typically manipulated manually through a direct or geared mechanism attached to the valve stem.
Actuated valves are a type of control valve, essentially composed of a box with an input, an output, an operating mechanism, and a controller. Their value lies in their various advantages for many industrial applications, including water treatments, offshore platforms, energy production, naval industries, pipeline, and processing industries.
Valve Method of Control and Function
Valve actuators regulate the position of a valve’s closure mechanism and can be categorized into two key methods of control. The first is the rotary motion where the valve such as a ball valve, butterfly valve, or plug valve revolves at least a quarter revolution to transport from an open to a closed state. The second valve method of control is linear motion, featuring valves like gate, pinch, globe, and diaphragm valves. These ‘linear valves’ use a moving stem mechanism to transition between open and closed states. The valve position plays a crucial role in controlling the flow of fluids.
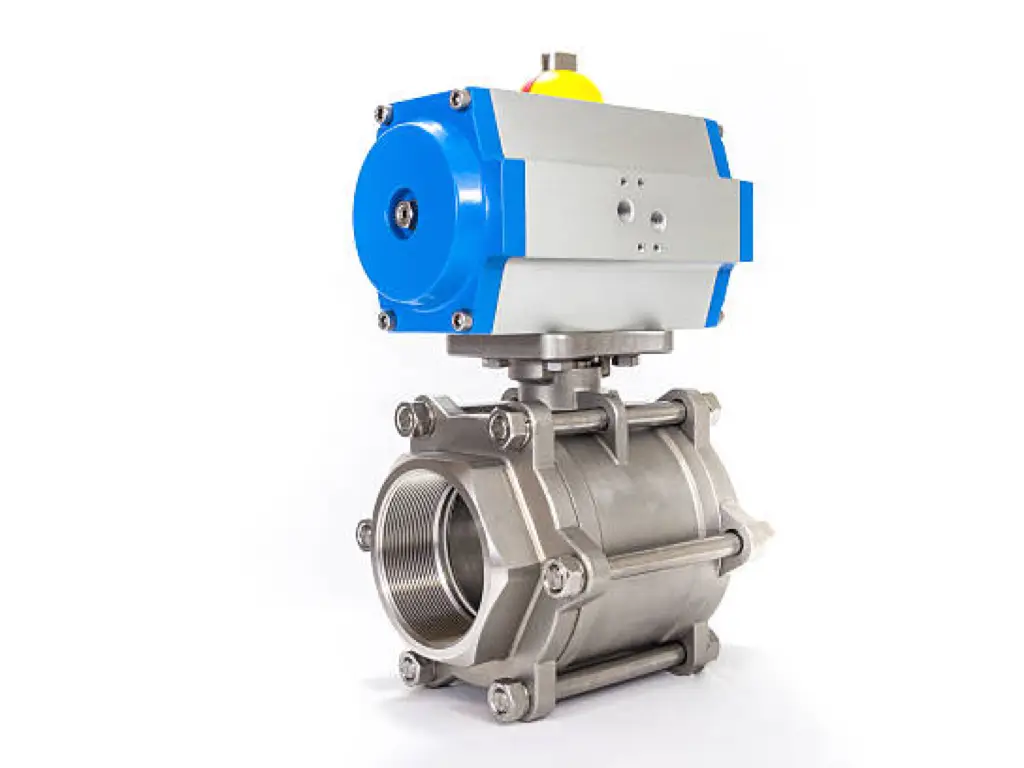
Actuators can also have varied functions, enabling them to either start, stop or throttle flow as per requirement. In any industrial setting, the correct method of precise control and function substantially increases efficiency, especially in situations where power failure can occur.
Valve Operation Types
Rotary (Quarter-Turn) Operation: This applies to butterfly, ball, and plug valves, including quarter-turn dampers. These valves require a simple 90-degree rotation to open or close, making sizing adjustments easy and efficient.
Multi-Turn Operation: This operation involves more complex mechanisms to move the valve closure element between open and closed positions. It is commonly used with globe valves, sluice gates, and gate valves.
Understanding valve operation types and choosing the suitable type of actuator are essential to enjoy the full benefits of valve actuators.
Types of Valve Actuator
Types of Valve Actuators | Advantages | Disadvantages |
Manual Valve Actuators | Simple and economical to use, No power source required, Reliable and straightforward control mechanism | Limited speed and efficiency, Requires manual effort, Not suitable for large or emergency applications |
Pneumatic Valve Actuators | Fast and robust responses, economical, and has a simple set up | Requires a source of compressed air, Lower force and torque compared to hydraulic actuators, Not suitable for extremely high temperature and high pressure environments |
Electric Valve Actuators | Accurate and precise control, Suitable for remote operation, Can be coupled with complex control systems | Requires a power source, vulnerable to power outages, More expensive than manual or pneumatic actuators |
Hydraulic Valve Actuators | High force and torque capabilities, suitable for heavy-duty industrial applications | Requires hydraulic lines, Vulnerable to leaks, Not suitable for high-speed applications |
Manual Valve Actuators
Manual valve actuators, or often referred to as manually operated valves, enable a user to directly control the valve’s position without needing an external power source. They provide a simplistic yet effective solution for systems demanding manual control and have a specific duty cycle.
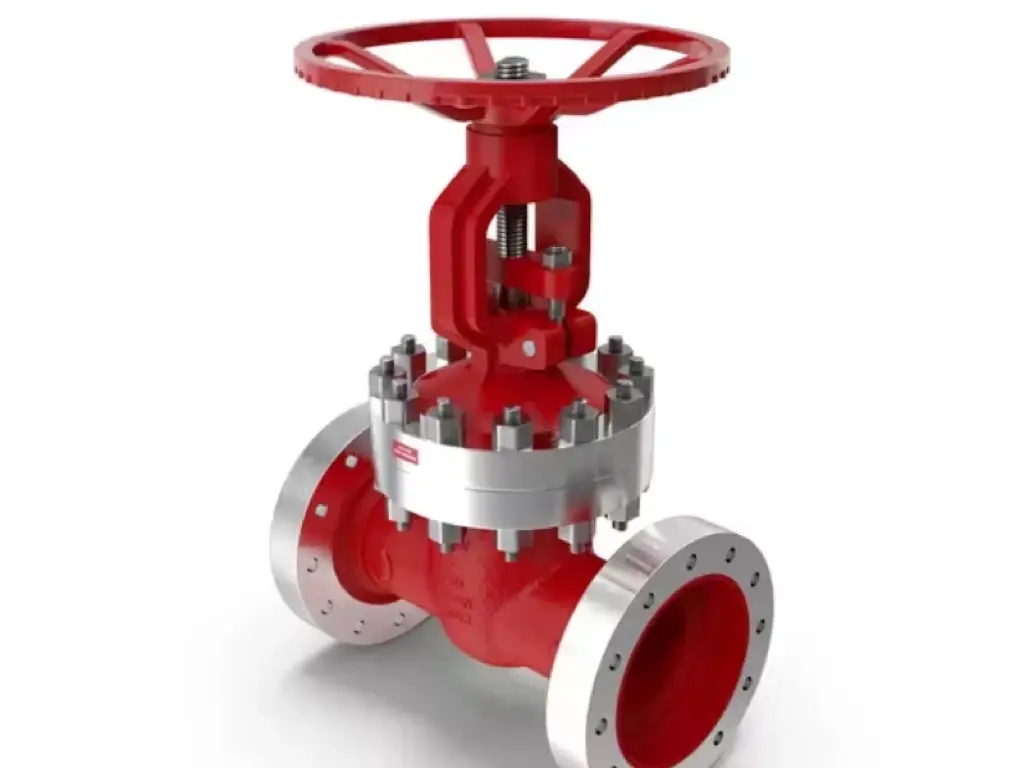
How Do They Work?
Manual actuators operate using mechanical means such as a handwheel, lever, or a chain wheel arrangement. Via these manual input devices, an operator can control the state of the valve by exerting force onto these mechanisms, transforming this force into the essential torque to move the valve.
Types
Basic Lever: This is the simplest form of a manual valve actuator. Basic levers require physical effort to operate, moving upwards and downwards to open or close the valve.
Latching-Lockable Lever Handle: The lockable lever kind of actuator is similar to a basic lever actuator but comes with an additional locking mechanism. This allows the operator to lock the actuator in either the open or closed position, reducing the risk of accidental operations. It’s often used to secure high-risk valves.
Oval Handles: Oval handle actuator design is generally found when the operator should have firm control over the actuation. They are ergonomic to operate: the oval design provides a comfortable grip, making it easy and safe for operators to handle the actuator in all types of conditions.
Hand Wheels: Hand wheels are usually found on larger valves that require a substantial amount of torque to operate. Turning the wheel opens and closes the valve, making it easy to control the flow rate. Hand wheel operated actuators are often used for modulated or controlled flow applications, and are an efficient choice for systems where micro-adjustments are frequently required. ISO hand wheels are designed to meet international standards for valve operation, ensuring compatibility and ease of use across different systems.
Manual Valves with Limit Switches: These manual actuators consist of an additional feature: the limit switch. It is an electromechanical device that monitors the position of the valve (open or closed) and sends feedback to a control panel or alarm. This enhances safety and allows operators to monitor the valve’s conditions remotely.
Applications
The simplicity, reliability, and independence from a power source make manual actuators an optimal fit for applications requiring less frequent valve operation. They especially serve well in systems where automated actuation isn’t necessary, but clarity on valve status is crucial.
Pneumatic Valve Actuators
Pneumatic valve actuators, often employed for semi-automatic or automatic valve operation, use pressurized air to rotate a valve. Pneumatic valve actuators employ the use of pressurized air to create rotational motion for the valve, shifting it from one state to the other. Known for their durability and simplicity, they are widely used across different industry applications.
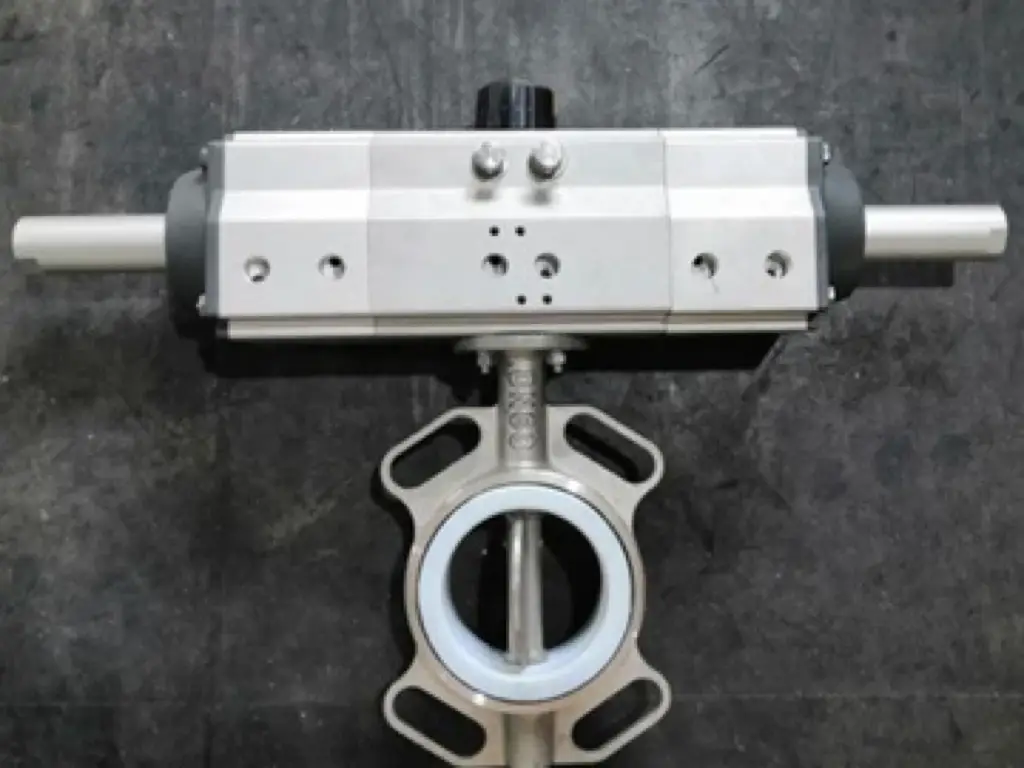
How Do They Work?
These actuators function by applying air pressure onto a piston or a diaphragm connected to the valve stem. This force then moves the valve into the desired position. A pneumatic actuator’s operation might lack a motor, but when applied in combination with solenoid valves, it still requires a power source.
Types
Piston Valve Actuator: A piston valve actuator employs a piston-cylinder arrangement to create motion for operating the valve. It uses pressurized air pushing against the piston within a cylinder to move, allowing larger forces and longer stroke compared to other types of pneumatic actuators.
Diaphragm Valve Actuator: The diaphragm valve actuator uses a flexible diaphragm instead of a piston to create motion. It incorporates a diaphragm, typically made of elastomeric material, which flexes when the air is pumped into the chamber, causing the actuator to move.
Double-Acting Valves: Double-acting valve actuators use pneumatic power (compressed air) to open and close the valve. Air is supplied to either side of a piston or diaphragm inside the actuator which allows for control in both directions, hence the term ‘double-acting’.
Spring-Return Valves: Also known as ‘single-acting’ actuators, these actuators use a spring mechanism to return the valve to its original position once the air pressure is released. The actuator opens or closes the valve using the force from compressed air but relies on a spring to return to its initial state when the actuator is not powered. They are often used in fail-safe operations where the valve needs to return to a safe position in the event of a power loss.
Applications
Typical applications of pneumatic valve actuators include parts of machinery where quick and robust responses are necessary. With their powerful and straightforward construction, they’re commonly used in sectors including chemical industries, power plants, and oil refineries.
Electric Valve Actuators
Electric valve actuators are devices that depend on an external power source. On receiving a signal, they prompt a valve to its ideal position, generating the needed level of torque for operation.
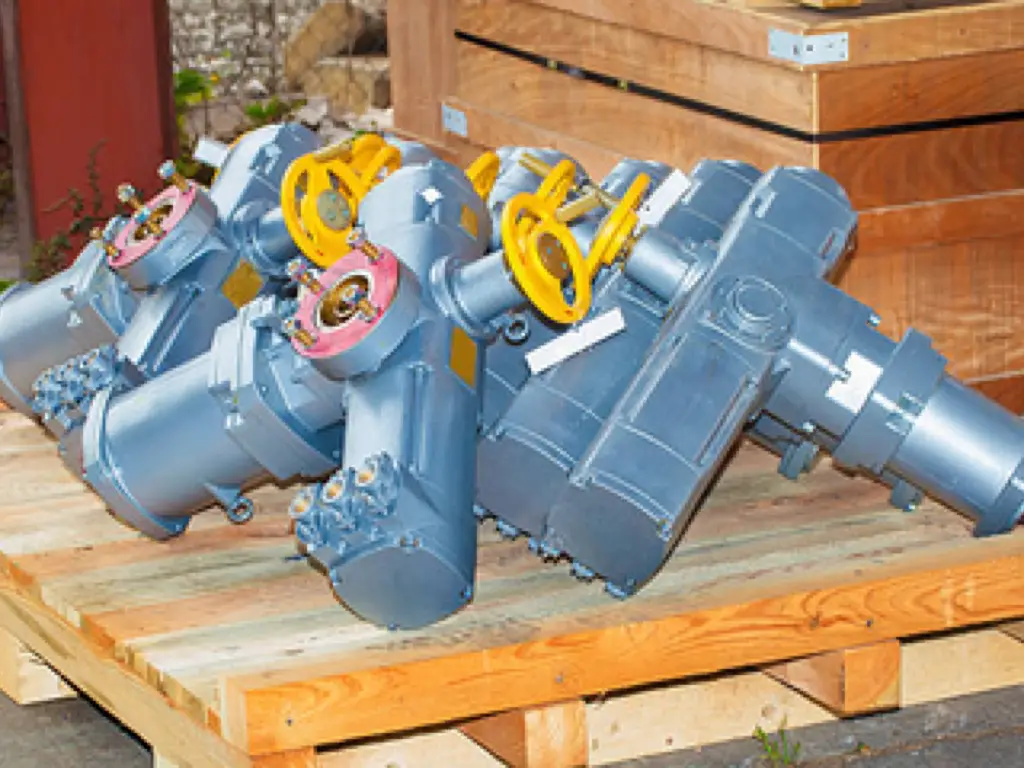
How Do They Work?
These actuators work by using electrical energy, usually an AC or DC motor, to produce mechanical motion. The motor provides a rotational output, which is converted into linear motion through a series of gears to move a valve to its desired position.
Types
Rotary Electric Valve Actuators: Rotary electric actuators work on the principle of rotation. They generate circular motion to drive a component, like a valve. Incorporated with electric motor power, these actuators are often used to control rotating equipment such as ball or butterfly valves that require quarter-turn action.
Linear Electric Valve Actuators: Contrary to the rotary actuators, linear electric actuators create motion in a straight line. They convert the rotational motion of an electric motor into linear displacement. They are typically used in control valves that require linear motion to displace the valve actuator stem, such as gate and diaphragm valves.
Applications
Due to their high level of precision, electric valve actuators find their use in industries requiring quick and accurate responses. These include the water and wastewater industry and areas involving automation of process control.
Hydraulic Valve Actuators
Hydraulic valve actuators, known for their high-precision, high-force, and reliable operation, operate on pressure-induced hydraulic power. They have the edge over other types of actuators when high force is the prime concern, especially given the compact size they offer.
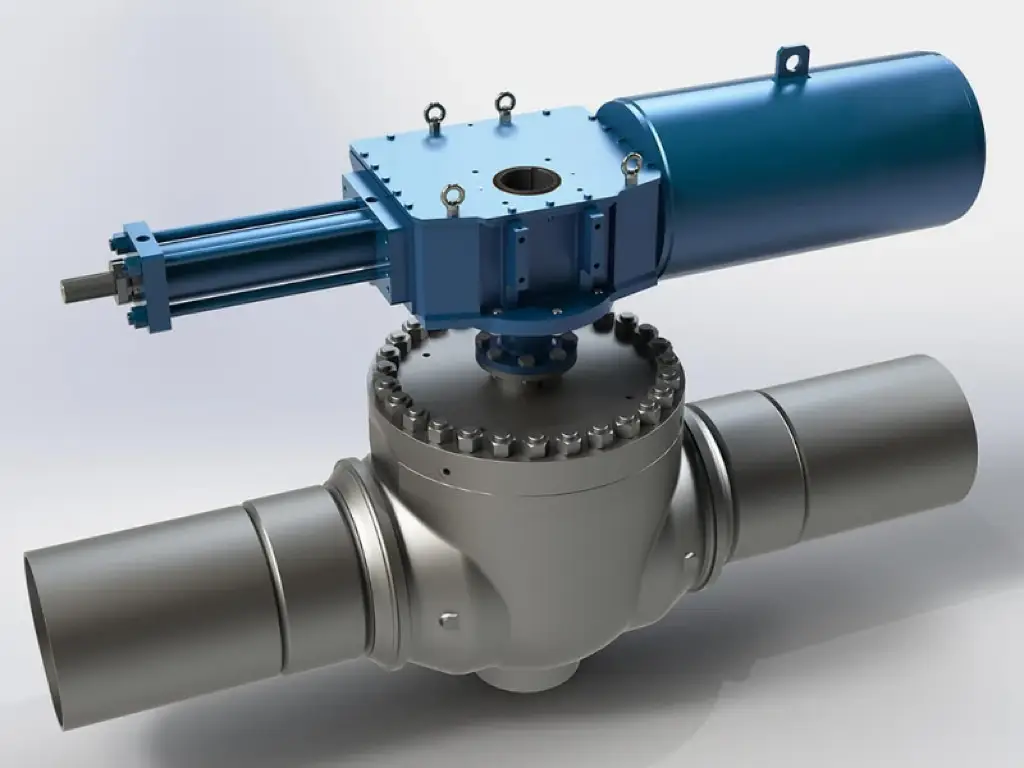
How Do They Work?
Hydraulic actuators convert hydraulic power, or fluid power, into mechanical power. A cylinder is loaded with hydraulic fluid that becomes pressurized when a control signal is received. This pressurization forces a piston to move, thereby actuating the valve.
Types
Rotary Hydraulic Valve Actuators: Rotary hydraulic actuators convert fluid pressure into rotary motion to operate a mechanism. These actuators are primarily used with quarter-turn valves like ball, plug, or butterfly valves that require rotational movements for opening or closing.
Linear Hydraulic Valve Actuators: Linear hydraulic actuators similarly use fluid power, but they convert it into linear motion. The linear moving element could be a piston, rod, or slide, and these actuators are often used in gate, pinch, and diaphragmatic valves that demand a linear displacement of the valve closure element.
Applications
These actuators are primarily used in heavy-duty industrial applications and scenarios where high forces or torques are required, which can not be fulfilled by other types of actuators.
Functions of Valve Actuators
Valve actuators are the heart of many industrial processes, performing several key functions. They allow automatic control of valves, which can be vital in situations that need rapid shut-off. Actuators allow for regulation – managing the flow rate of liquids or gases within different phases of an industrial process. This is greatly beneficial for ensuring system efficiency and safety. Moreover, they make remote operation and control possible, leading to a significant reduction in labor costs and increased flexibility within the operational environment.
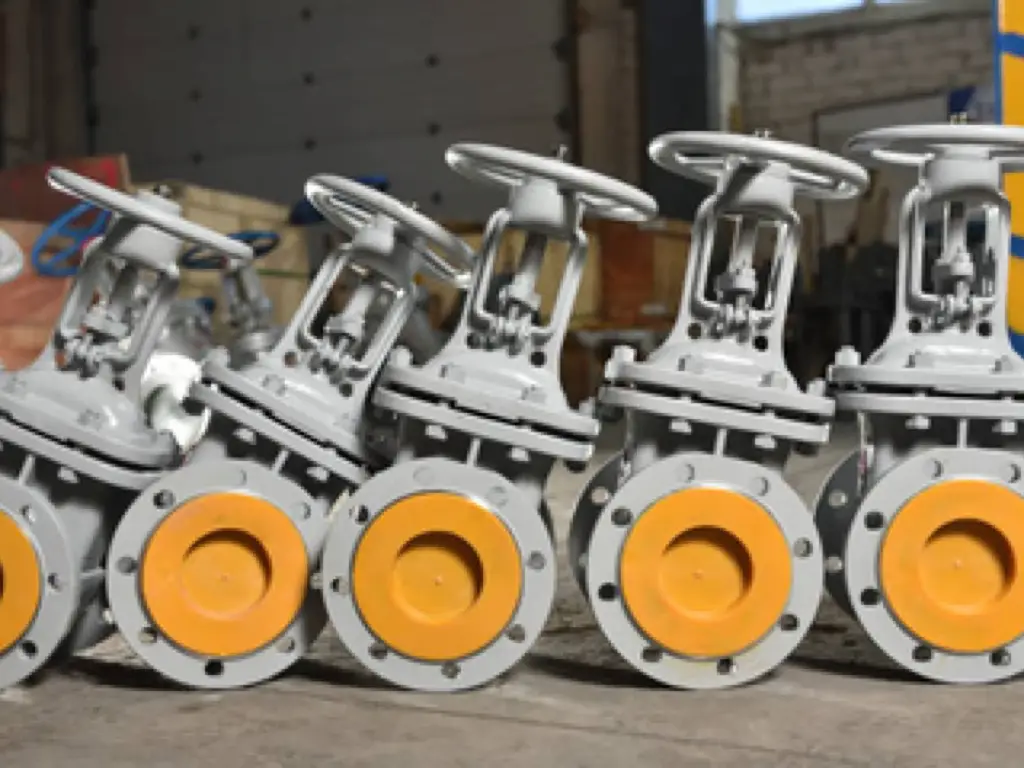
In many heavy-duty industrial applications, robust and fail-safe operation is a crucial characteristic. Valve actuators assure reliable performance even under the most challenging conditions. They are designed to operate within a spectrum of temperatures, atmospheres, and pressures, often with in-built fail-safe features to ensure system safety in emergencies.
Actuator Specifications
The specifications of an actuator are crucial attributes to consider before selection. Detailed examination of rotary and linear actuator specifications directs the right choice, enhancing the overall performance of an industrial process.
What Factors Should Be Considered When Using a Valve Actuator?
Temperature: Many actuators have specific operating temperature ranges. One must make sure that the operating environment’s temperature is within that range.Compatibility: The actuator must be compatible with the valve type and size it will operate.Operating Pressure: The actuator should be designed to withstand the operating pressure within the system to ensure reliability.Environmental Conditions: The actuator’s material and design should be appropriate for the conditions to resist corrosion or damage.Torque and Speed: The actuator should be capable of providing the necessary torque to operate the valve and at the required speed.
What Factors Should Be Considered When Selecting a Valve Actuator?
Type of Operation: Consideration should be given to whether the actuator is for linear or rotary operation, which depends on the valve’s design and required operation.
Power Source: One must assess if the power source needed for the valve actuator (electric, hydraulic, pneumatic, or manual) is available or feasible.
Durability: The actuator’s build quality and durability, especially in harsh conditions, is an important factor.
Cost: Budget constraints and the overall investment versus the actuator’s service life and maintenancecosts should be evaluated.
Size and Weight: The size and weight of the actuator must be compatible with the mounting arrangement and should be appropriate for the safe operation of the valve.
Compliance with Standards: It’s important to choose an actuator that complies with industry standards and relevant health and safety regulations.
After-sales Service: The availability of after-sales service and spare parts from the manufacturer could be crucial for long-term operation.
Feedback Mechanism: Depending on the application, the ability of the actuator to provide feedback about the valve’s position may be a necessary feature.
Conclusion
In closing, recognizing the variations between actuator valves, their distinctive operations, and the factors influencing their selection can considerably benefit an operation’s success. Understanding these factors can make the difference between seamless operation and frequent malfunctions. It’s hence vital to match the right valve actuator — whether that’s electric, pneumatic, hydraulic, or manual — to the right application. Future advancements and continuous research in this area promise more efficient and more capable valve actuator designs, further refining industrial processes.
Professional Manufacturer of Valve Actuator-Dombor
Be sure to contact manufacturer of industrial valves – Dombor for solid and highest quality valves. They offer a wide range of high quality products such as pneumatic, electric and hydraulically actuated valves. They can also accept custom requests as long as you want industrial application standards. Their internationally certified enclosures reinforce their commitment to safety and quality. In addition to this, Dombor ensures fast shipping and a strong after-sales service, including product warranties and dedicated customer service.