During engine operation, the flow of gas or liquid into and out of the cylinders or combustion chambers must be permitted or constrained. Diesel valves or gasoline ball valves, the primary mechanical components of internal combustion engines, carry out this function. Many additional types of flow-blocking or flow-passing valves perform similar functions.
Diesel shut-off valves are crucial system parts because they serve as a preventative safety measure. This device prevents the circuit entering the system from reaching the boiling temperature by intercepting and blocking the fuel before it comes to the burner. This is an approach to preventing harm to the system and the people nearby.
Anyone working in the gasoline or fuel industry must thoroughly know about the wide variety of diesel cut-off valves because they are a necessary component. Get in touch with Dombor to learn about and purchase diesel valves for various industrial applications from the best industrial ball valve supplier.
What Are Diesel Valves?
An engine’s fuel supply can be turned off with the help of a diesel fuel shut-off valve. When the running parameters are exceeded, its primary purpose is to safeguard the system from harm. These gadgets come in two variations. One diesel control valve cuts off the gasoline flow to shut off the engine. And the other has a needle valve that a person can adjust to let in just enough flow to keep the engine running at a chosen idle speed.
Due to the materials used in constructing a gasoline or diesel fuel valve‘s body, which provide exceptional corrosion resistance, durability, and many pressure ranges and operating temperatures, these valves can readily handle combustible liquids derived from petroleum.
How Does Diesel Fuel Shut-Off Valve Work?
A diesel fuel shut-off solenoid valve‘s main job is to move fuel from a vehicle’s gas tank to the engine. It is a device connected to a machine’s electrical system and is used to monitor and find mechanical issues or abnormal temperatures. The actuated gate valve closes and cuts off the machine’s access to diesel fuel if there is a disruption in the electrical current flowing through the engine due to a problem.
The primary way a diesel check valve operates is to open or close by producing a magnetic field in response to an electric current. An engine’s diesel fuel shut-off valve is connected to the machine’s primary electrical system. An electrical signal from the battery is received by it, causing the solenoid valve to open and permitting diesel fuel to flow from the gas tank to the engine.
Diesel fuel is transferred from the fuel line to the diesel solenoid valve through an inlet pipe by a shut-off valve when it is functioning correctly. An inlet pipe has a rubber stopper at the entrance secured by a metal spring connected to the back. A metal bar connects the plug to a metal pin close to the solenoid coil. A magnetic field produced by an electric current flowing through the valve causes the pin to retract, removing the stopper from the input pipe. Fuel can flow freely from the fuel line to the engine after removing the plug. However, a diesel fuel shut-off valve differs from a standard valve because it can recognize and decipher signals from the primary electrical system.
Source: Dombor
The machine’s primary electrical system keeps track of the engine’s temperature and mechanical variations, allowing it to spot problems and exceptionally high temperatures. The spring will push the stopper back into the input pipe when the electrical system senses a problem with the machine because it will then halt the electrical current being provided to the diesel valves. Diesel fuel cannot enter the engine when the valve is closed, which stops the engine. Valves like concentrated butterfly valves are popular in many industries.
What Are The Different Valves For Diesel Fuel?
The following list includes a few popular kinds of diesel valves used in industrial pipes for diverse purposes:
- Pressure Control Diesel Valve
To manage the fuel flow to the engine, diesel pressure control valves are frequently utilized in industrial settings. The extremity, often the pump exit, is where it is found. Lower manufacturing costs are associated with a pump-external Pressure Control Valve, but extra turbulence in injector dynamics is brought on by the regulator’s proximity to the injectors.
A ball valve for the diesel valve that is built into the pump combines the power running through the pump’s cooling circuits and lubrication with the fuel leakage from the pumping chambers in a pump-integrated Pressure Control Valve system. For the fuel tank to refill, this flow is mixed and discharged from the pump.
- Industrial Ball Valve
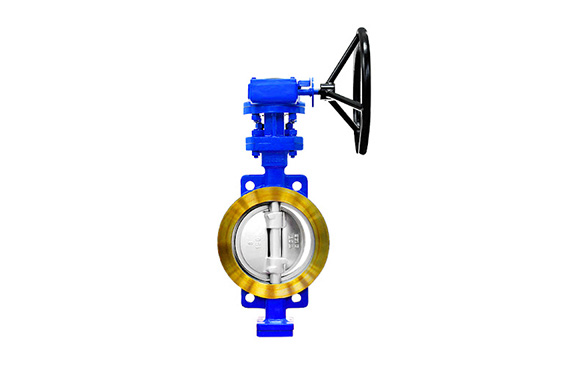
A ball that slides up and down inside the check valve is how a double block and bleed ball valve operates. The chamber is shaped conically to facilitate the ball’s entry into the seat, and the seat is machined to fit the ball to seal and stop a reverse flow. Lighter balls can be chosen if the pump’s capacity is insufficient, while heavier balls can be selected if a water hammer occurs after the pump stops.
Due to their minimal maintenance requirements, the diesel check valve is among the first choices for use in pumping stations that are infrequently manned. This is usually the case if the ball makes noise due to an inadequate pump capacity.
The regular ball is constructed with a metal core lined with NBR rubber, and the rubber’s hardness has been tuned to keep the ball from becoming lodged in the seat. Polyurethane balls are great for abrasive media when varied ball weights are required to prevent noise. Full flow with minimal pressure loss is guaranteed by a full and smooth bore, and the possibility of bottom deposits impeding tight closure is also gone. An industrial ball valve supplier can produce high-quality valves.
- Globe Valve
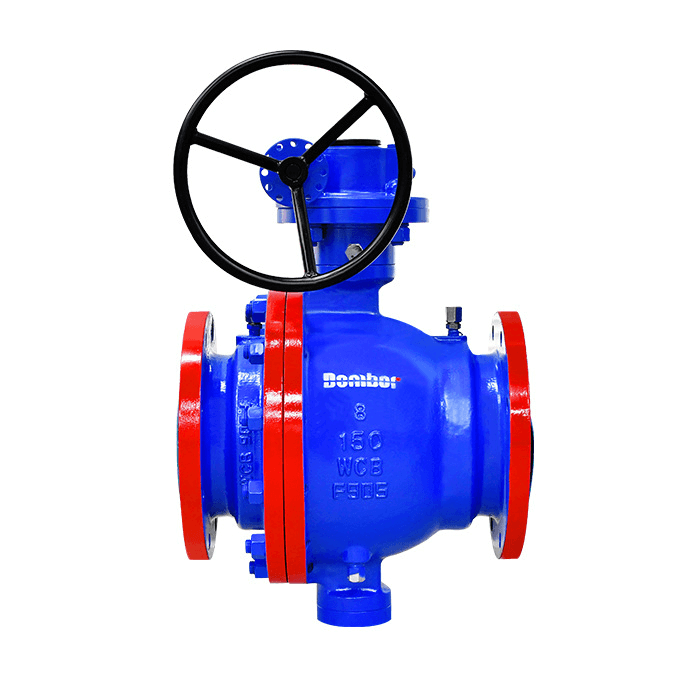
Due to their versatility in stopping, starting, and regulating flow, globe valves are among the most often utilized. The two sections of a globe valve, divided by an internal baffle, are spherical. Usually, the baffle and pipe are parallel. Compared to other valves, globe valves have an excellent shut-off mechanism and leak less.
Due to globe valve ability to stop, start, and regulate flow, globe valves are advantageous in various applications. For example, fuel oil systems, piping systems, and cooling systems can all be employed in a regulatory role.
- Diesel Quantity Control Valve
The diesel quantity control valve controls the low-pressure or lift pump’s ability to provide a fixed amount of diesel fuel to the high-pressure pump’s pistons. When the high-pressure pump’s pistons are given more diesel, more pressure is produced, which raises the pressure in the common rail. When the high-pressure pump’s pistons are given less diesel, less pressure is created, which lowers the pressure in the common rail. Managing the diesel flow to the pistons produces lower fuel temperature and less strain on the high-pressure pump. The diesel tank receives any excess fuel.
One-half of the engine speed is used to operate the high-pressure pump, which is connected to the engine with a belt or gear drive system. Engine power output and diesel efficiency are significantly impacted by pressuring diesel and returning a sizable amount to the tank. The input metering capabilities of more recent pumps can boost engine power output and fuel efficiency while minimizing parasitic loss or power loss to make the components work.
- Diesel Fuel Pressure Relief Valve
It is essential to maintain the system’s integrity while taking care to prolong the life of system components; therefore, a one-way diesel valve is created to meet the needs of today’s diesel engines. This security is offered to consumers by a diesel pressure relief valve. It also safeguards pumps, fittings, hoses, and filter housings by reducing pressure fluctuations. These gadgets are dependable and frequently made of high-quality materials. Even under the worst working conditions, they are perfect for installation and maintenance.
- Gate Valve
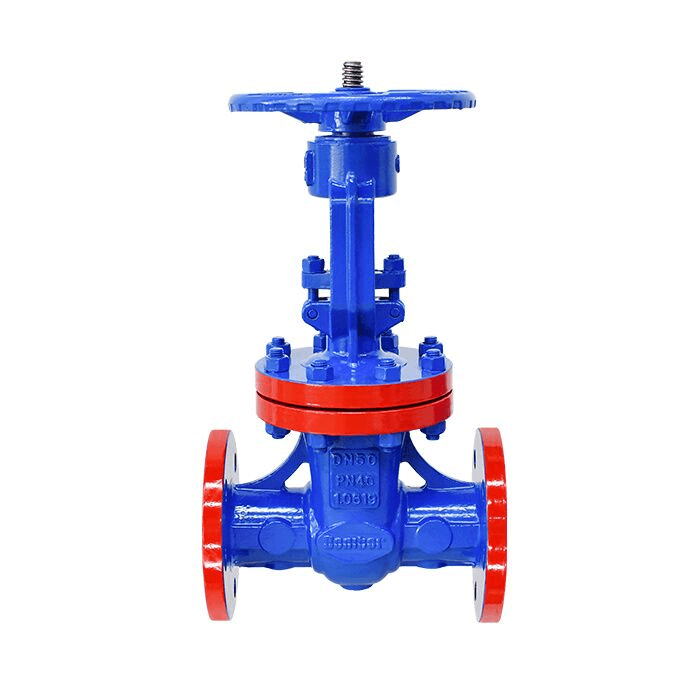
Gate valves belong to the shut-off/on family and are best used in isolation applications. The gate within progressively lifts and lowers when the top handle is turned. There is no resistance when the gate is fully open because it is outside the flow route. Gate valves should only be used to initiate or stop the flow; they should not be utilized for throttling because doing so can seriously harm the disc. Various media, including air, liquid, and steam, are employed with gate valves. Gate valves are frequently used in the wastewater industry and as main water shut-off valves.
There are other types of valves, like a butterfly valve, that help regulate fuel in industries.
Materials Used In Making Diesel Valves
Diesel valves’ primary functions necessitate intense strain and incredibly high temperatures. The materials used in engine valves must be capable of withstanding such high mechanical and thermal loads caused by engine dynamics to resist that stress and temperature.
The primary materials used to make the exhaust valves are high heat-resistant metals like silicon-chromium, nichrome, or cobalt-chromium alloys, while the primary materials used to make the intake valves are nickel, chrome, stainless steel, cast steel, or tungsten steel.
Components Of Diesel Valves
Below are the essential components of a diesel valve:
- Actuator
Actuators automate valve action in industrial pipeline transportation to ensure dependable and precise fluid management. Process engineers can remotely control valves because the actuator generates enough force to shut the valve closure mechanism and overcome frictional forces from the service fluid.
Every actuation mechanism has different performance characteristics and needs an external power source. A pneumatic actuator offers a quicker cycle time and is more robust than an electric actuator. A hydraulic actuator offers additional torque to activate valves in massive pipelines requiring more effort.
- Body
A valve’s main pressure barrier is its body, sometimes called the shell. It performs the role of the main component in a valve assembly since it provides the framework for the entire assembly. Fluid pressure loads from connecting pipework are resisted by the valve’s body, which is its first pressure boundary. Welded or bolted joints attach the pipework for the inlet and outlet. A variety of forms are achieved by casting or forging valve bodies. Though ideally, a sphere or a cylinder would be the most cost-effective shapes to withstand fluid pressure when a valve is open, numerous additional factors must be considered.
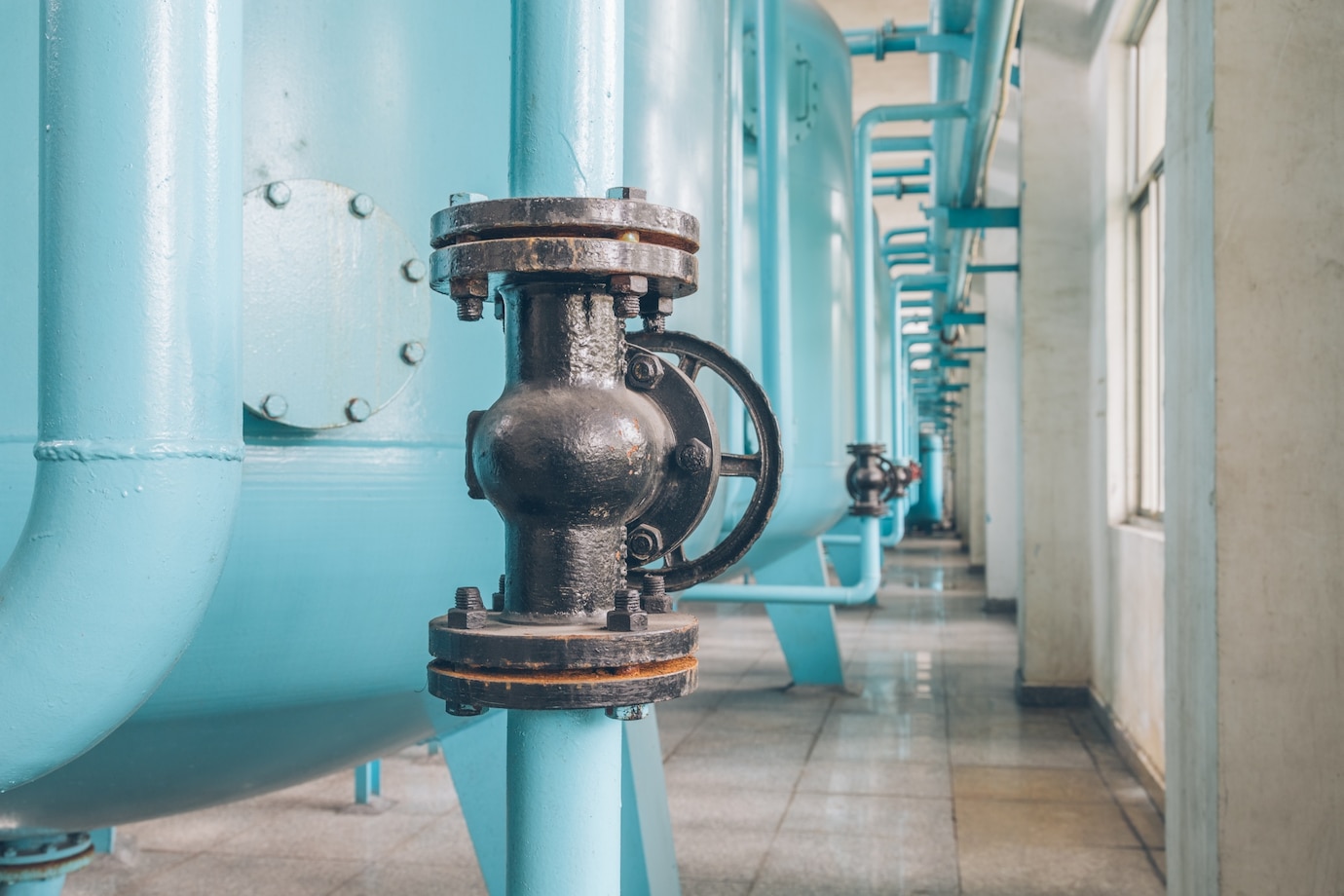
- Bonnet
The bonnet is the opening’s cover in the diesel engine shut-off valve body. The body may be divided into two pieces in some designs, and bolts connect these pieces. Like valve bodies, bonnets come in a variety of designs. Some bonnets serve only as valve covers, while others hold up the valve’s stem, disc, and actuator—as well as various internals and accessories. The second central pressure limit of a valve is its bonnet. The joint securing it to the body is either welded or bolted. It is made of the same material as the body when cast or forged.
A pressure boundary is where the bonnet connects to the body. This implies that the bolts or weld joint that secures the bonnet to the body is capable of holding pressure. Despite being a requirement for most valves, valve bonnets are a reason for concern. Bonnets can make the process of making valves more challenging, increase the size of the valve, account for a large percentage of the cost of the valve, and be a potential leakage point.
- Stem
The valve stem’s function is to transmit the necessary motion to the disc, plug, or ball to open and close the valve. The gasoline ball valve disc is attached to one end of it, which is connected to the valve actuator, lever, or handwheel.
Applications Of Industrial Valves Used In Diesel Valves
The majority of industries rely heavily on valves. They are used in several components of standard mechanical equipment, such as the gasoline engine of an automobile and water systems. Here are a few instances of the several industries where industrial valves are essential to their efficient operation.
- Pipelines
Although this application is fundamental to many businesses, hundreds of thousands of miles of vital pipelines move media from its source to the location where it will be converted into its final product. This medium works perfectly well for both onshore and offshore gas and crude oil pipes. To improve pipeline operating conditions, diesel check valves are employed in the stream sections of the piping.
- Oil And Gas Industry
A component of the pipelines category is the oil and gas sector. The rising demand for oil and gas has necessitated drilling deeper wells, building longer pipelines, and reducing production costs. The device must not only be a cheap valve but also more durable, functionally superior, and able to withstand repeated use. Extreme temperatures, high pressures, or cryogenic and very low-pressure applications frequently characterize the service environments and operating conditions for valves. The ability to be controlled remotely is a feature that is crucial for valves used in the oil and gas industry.

- Marine
The marine sector relies heavily on industrial valves and equipment. The greater the size of the ship, the greater the need for producing power, treating sewage, and carrying out operational activities, all of which need valves. Businesses can estimate the number and types of valves required on board the ship using information about its size.
Marine industry professionals use industrial control valves to load and store a ship’s electrical supply as well as to supply water for a variety of uses. It facilitates the treatment of wastewater and stores liquid cargo onboard. The valves used in the marine sector should be solid and dependable because they shouldn’t rust or react when exposed to seawater.
Factors To Consider When Selecting Diesel Fuel Valve
Consider these factors when selecting a diesel fuel valve for industrial applications:
- Pressure Drop
Knowing the pressure drop inside the flow management system when choosing a diesel valve is crucial. Changes in system pressure regulate flow and, as a result, the diesel valve’s operation. When the downstream pressure exceeds the upstream pressure, the reverse pressure drop determines how tightly the valve closes off during backflow. A diesel valve’s input and output ports must be under a certain minimum pressure. When selecting a valve, ensure it satisfies this demand and consider the required maximum pressure.
- Safety
Due to the highly flammable nature of the fuel media used in diesel fuel line check valves, it is essential to take all necessary precautions to avoid any sparks developing inside the coil or housing. The coil must be expressly stated to prevent any explosion from the valve. Always look for one of these standards’ marks on a valve before purchasing one with explosive fuel.
Ensure the valve has the proper IP rating to protect against dust, liquid, humidity, and touch. This is especially crucial when the valve is put in challenging industrial settings for remote operation.
- Maintenance
For a valve to last longer and be safe, maintenance is necessary. A diesel fuel valve receives internal and external damage due to the service media and environmental factors. It increases the likelihood that valves will break, leading to fugitive emissions, leaks, safety issues, and inconsistent fluid control.
Businesses should set up dependable procedures and timetables for corrective and preventative actions for industrial valves. Engineers should specify the regularity of examining and repairing defective valves and the maintenance needs for each valve. The replacement parts must adhere to the original manufacturer’s specifications to guarantee optimal valve function.
- Response Time
When working with combustible fuels and oils, shut-off valves must react quickly. While the reaction time of indirectly operated valves can be as high as 1000 ms, direct operated valves typically have a response time of around 30 ms. When selecting a valve for the oil and gas industry, it is crucial to determine the value because the response time of the valve differs with various manufacturers and operation types.
- Type Of Material
A crucial factor that assures safe operation and lowers maintenance and replacement costs throughout your business depends on the type of usage for the industrial valves and the material used in their construction.
The valves constructed of stainless steel are well known to be good choices in various processing environments, including those involving corrosive media like chemicals, fuel, and acids, with complete cleanliness requirements and procedures by employing a relatively high pressure or high temperature.
In addition, when choosing a body material, it is crucial to consider how well it will work with other chemicals. If elastomers are involved in your valve, a thorough study of their chemical compatibility and pressure and temperature restrictions should be done.
- Type Of Environment
Take into account the environment in which the valve will need to operate. Choosing the ideal valve for the current procedure is possible by making inquiries and considering the workplace. The solutions will show the materials most appropriate for the function.
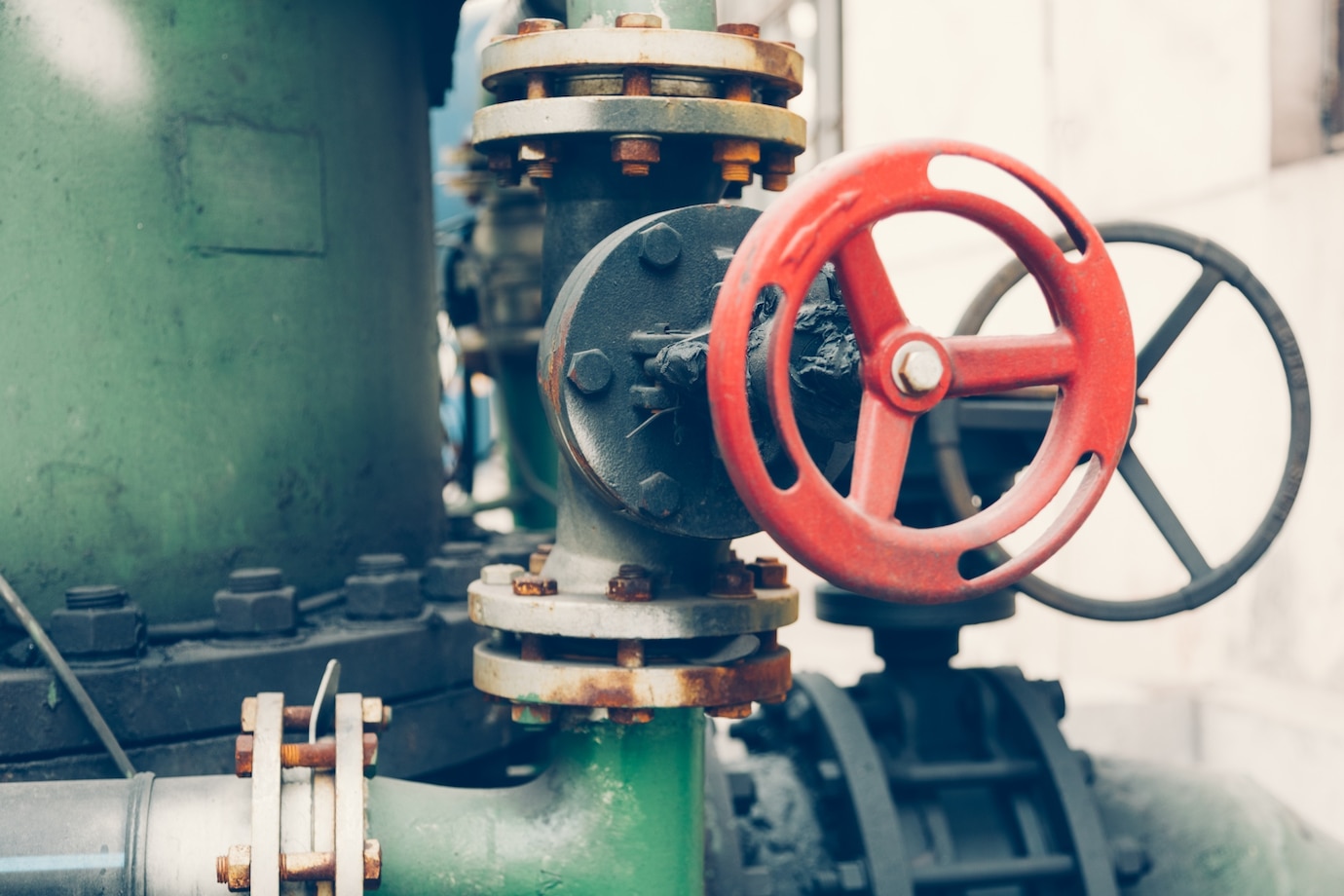
- Cost
The actual cost of a valve includes its initial purchase price and the costs associated with keeping, maintaining, or replacing that valve over time. How long a valve will function in the system between maintenance inspections is necessary when calculating the cost of buying a valve.
The cost of labor and downtime must also play a significant role in maintenance costs, in addition to the price of replacement parts. Business owners should be aware that some valves require far less maintenance than others. While some can be maintained on-site, others need care outside the production line.
Contact Industrial Valve Manufacturers To Get Diesel Valves
Industrial pipelines must include diesel fuel valves as a necessary component. Even though they are utilized in virtually every process and system, picking the best takes time and effort. Matching the valve’s size to the anticipated flow through the industrial pipe system is necessary for choosing the suitable valve.
As previously stated, the advice is provided to assist everyone in quickly and easily selecting the best valve for a specific operation. Contact Dombor if your business is interested in buying premium diesel fuel valves and receiving attentive customer support from the most incredible China valve manufacturer.