What is a Butterfly Valve Gear?
A butterfly valve gear is a mechanism that regulates the motion of a butterfly valve disc. It is a vital part that allows the valve to control the flow of the fluids through pipelines and systems. The gear is designed to transmit rotational force generated by the actuator or manual operator to the valve stem which rotates the disc to open or close the valve.
Five Primary Types of Butterfly Valve Gear You Should Know
Butterfly valve gears are offered in many types, each one of them is intended for a specific application and need. The type of drive selected is determined by the amount of control required, the operating environment, and the power source that is available. The main types of butterfly valve gears include manual gears, gear operators, electric actuators, pneumatic actuators, and hydraulic actuators.
The succeeding paragraphs will shed light on the different types of butterfly valve gears, their features, and their applications. Thus, knowing the distinction between the valves, you will be able to make the right choice when selecting the specific valve for your particular requirements.
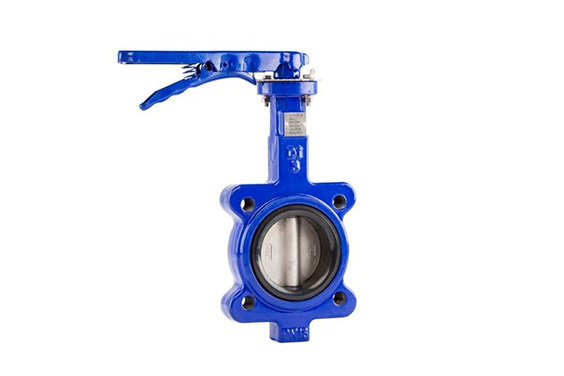
Manual Butterfly Valve Gear Type: Simplicity and Cost-Effectiveness
The manual butterfly valve gear type is the simplest and the easiest to operate among all the various options available. As the name suggests, these valves are operated by hand, with a lever or a hand wheel being the most common means of controlling them. The valve handle is designed in such a way that it is directly connected to the valve stem, which allows the operator to rotate the disc and control the flow of the fluid through the valve body. This type of valve, also known as a lever operated butterfly valve, is a popular choice for its simplicity and cost-effectiveness in controlling the flow of fluid within a closed system, which makes it a viable alternative to ball valves in certain situations.
Valve bodies of manual butterfly valves are usually made of cast iron, ductile iron or stainless steel. The stem and disc are normally made of stainless steel for better corrosion resistance. The torque capacity of manual butterfly valves is restricted by the strength of the operator and the size of the valve. The small-sized valves, up to 6 inches diameter, can be easily operated by hand, while the large-sized valves may need a gear operator or a motorized actuator to overcome the increased torque requirements.
One of the most significant benefits of manual butterfly valves is their simplicity. They do not need an external power source or complicated control systems, which allows their installation and maintenance to be simple. However, manual butterfly valves have their disadvantages. They cannot be used for applications that demand regular or exact control because manual operation is slow and less precise. Also, they may not be well suited for larger valve sizes as well as high pressure conditions, where the force needed to operate the valve manually becomes inappropriate.
Here is a table for quick reference:
Characteristic | Description |
Torque Capacity | Limited by operator strength and valve size |
Materials | Cast iron, ductile iron, stainless steel |
Durability and Reliability | High, with proper maintenance |
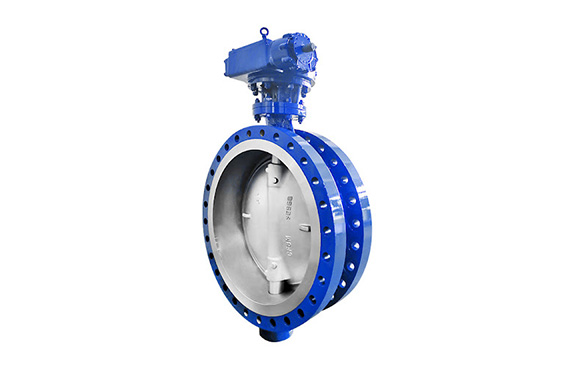
Gear-Operated Butterfly Valve Gear Type: Enhanced Control and Efficiency
The gear operated butterfly valve work better than manual valves because they are more precise and effective. These valves operate with a gear operator, which is a mechanical device that converts the rotational motion of the actuator or hand wheel into the rotational motion of the valve stem. Materials used in gear-operated valves are the same as manual valves with the addition of cast iron or ductile iron for the gear housing and bronze or stainless steel for the worm gear and worm wheel.
The gear operator is composed of a worm gear and a worm wheel. The worm gear is mounted to the input shaft, which is connected to the handwheel or the actuator. The input shaft starts to rotate and it moves the worm gear, which then engages with the worm wheel. The worm wheel is attached to the valve stem, and its rotation will bring the disc either open or closed.
The gear operator offers several benefits in comparison to manual operation. First of all, it lets you control the valve position with more accuracy. The ratio of gearing between worm gear and worm wheel decreases the amount of power needed to work the valve therefore it is easier to make fine adjustments. This is an essential advantage because in many instances, accurate flow control is vital, for example, in chemical processing plants or power generation facilities. Also, The gear-operated butterfly valves enjoys higher torque capacity over the manual valves because the gear operator provides mechanical advantage. The gear ratio of the worm gear and worm wheel is responsible for the degree of torque being multiplied. Common gear ratios range from 20:1 to 80:1, which is capable of producing increased torque and the ability to operate larger valves.
Here is a table for quick reference:
Characteristic | Description |
Torque Capacity | Increased by gear ratio, typically 20:1 to 80:1 |
Output Torque | Higher than manual valves |
Gear Ratio | 20:1 to 80:1 |
Materials | Cast iron, ductile iron, stainless steel, bronze |
Durability and Reliability | High, with proper lubrication and maintenance |
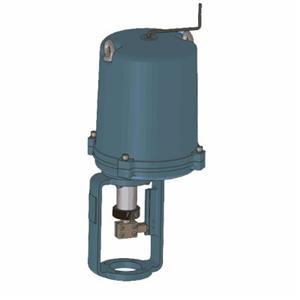
Electric Butterfly Valve Gear Type: Automation and Precision
The electric butterfly valve gear types bring valve control to a new level of automation and precision. They are provided with an electric actuator which is a motor-driven device that commands the valve to move by an electrical signal. Electric actuators are available in various materials, including aluminum, cast iron, and stainless steel, to suit different environmental conditions and corrosion resistance requirements. The electric butterfly valves have high torque capacity and accurate control due to the electric actuator. The output torque of electric actuators can be in the range of a few hundred to several thousand Newton-meters (Nm) depending on the size and design of the actuator.
Automation of electric butterfly valves is one of the major benefits of the electric valves. They may be integrated into process control systems, making remote operation and monitoring possible. This automation does not require manual intervention and allows to control the position of the valve accurately using setpoints or real-time process variables. Electric butterfly valves are highly accurate and have a high repeatability rate. The electro-mechanical actuator can position the valve disc with a high degree of precision, which leads to uniform flow control. This accuracy is very useful in cases where tight tolerances and the precise flow rate are required, for example, in the pharmaceutical industry and in the production of high-purity chemicals.
Here is a table for quick reference:
Characteristic | Description |
Torque Capacity | High, ranging from a few hundred to several thousand Nm |
Output Torque | Determined by actuator size and design |
Gear Ratio | Determines the relationship between motor speed and output torque |
Materials | Aluminum, cast iron, stainless steel |
Durability and Reliability | High, with proper maintenance and protection from environmental factors |
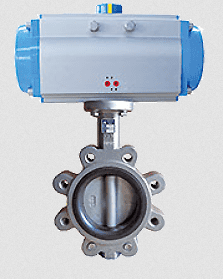
Pneumatic Butterfly Valve Gear Type: Ideal for Hazardous Environments
Pneumatic butterfly valve types are powered by compressed air to operate in hazardous areas where the electrical spark could be a threat. These valves are supplied with a pneumatic actuator, that by converting the energy of compressed air to mechanical motion, operates the valve. Pneumatic actuators are generally made of aluminum, stainless steel, or engineered plastics which offer superior corrosion resistance and suitability in hazardous environments.
Pneumatic butterfly valves are characterized by high reliability and quick response times, with torque capacities ranging from several dozen to up to several thousand Nm, depending on the actuator size and air pressure. The output torque of pneumatic actuators is proportional to the air pressure and the effective surface area of the piston. The normal air pressures are in the range of 40-120 psi (2.8-8.3 bar).
Another crucial advantage of pneumatic butterfly valves is their in-built safety. They are safe because they don’t need electricity and, therefore, there is no risk of sparks or electrical hazards. Hence, they can be used with no fear of any spark or spillage in highly flammable environments like oil and gas processing or chemical plants.
Here is a table for quick reference:
Characteristic | Description |
Torque Capacity | Few dozen to several thousand Nm, depending on actuator size and air pressure |
Output Torque | Proportional to air pressure and piston surface area |
Air Pressure | Typically 40 to 120 psi (2.8 to 8.3 bar) |
Materials | Aluminum, stainless steel, engineered plastics |
Durability and Reliability | High, with proper maintenance and air quality control |
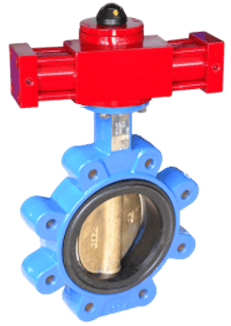
Hydraulic Butterfly Valve Gear Type: Power and Reliability for Demanding Applications
The hydraulic butterfly valve gear types are driven by pressurized hydraulic fluid. These valves are equipped with a hydraulic actuator that turns the energy of the fluid pressure into mechanical movement. Hydraulic actuators are usually made of steel, stainless steel or ductile iron, which are great in strength and durability.
The hydraulic actuators output torque may reach the value of several hundred thousand Nm, depending on the actuator size and hydraulic pressure. The hydraulic systems normally operate at pressures between 1,000 to 3,000 psi (69 to 207 bar) to generate huge force to operate large valves or valves under high pressure. The ability of hydraulic valves to manage the demanding applications like those encountered in the oil and gas industry or in large-scale water distribution systems is due to their high torque capability.
Hydraulic butterfly valves have the feature of providing a smooth and precise control. The hydraulic fluid acts as a cushioning medium, absorbing the shock of instant valve movements thereby making the operation smooth. It is important to note that this smooth control is especially useful in cases where abrupt pressure changes could lead to damage to the whole system or the valve.
Here is a table for quick reference:
Characteristic | Description |
Torque Capacity | Highest among all gear types, up to several hundred thousand Nm |
Output Torque | Determined by actuator size and hydraulic pressure |
Hydraulic Pressure | Typically 1,000 to 3,000 psi (69 to 207 bar) |
Materials | Steel, stainless steel, ductile iron |
Durability and Reliability | Extremely high, with proper maintenance and fluid quality contro |
Please note that the values provided are typical ranges and may vary depending on the specific manufacturer and model.
The table summarizes the key advantages and disadvantages of each butterfly valve gear type according to the above discussion:
Gear Type | Pros | Cons |
Manual | Simple and cost-effectiveEasy to install and maintainSuitable for small valves and low-pressure applications | Limited torque capacityNot suitable for frequent or precise adjustmentsImpractical for larger valves or high-pressure applications |
Gear-Operated | Increased torque capacity and mechanical advantageMore precise control and easier operationSuitable for larger valves and higher pressure applications | More complex than manual valvesRequires regular lubrication and maintenanceHigher cost compared to manual valves |
Electric | High torque capacity and precise controlAutomated operation and remote monitoringSuitable for integration with process control systems | Requires a power supplyMore complex and expensive than manual valvesMay not be suitable for hazardous environments without proper protection |
Pneumatic | Inherently safe for use in hazardous environmentsFast response times and reliable operationSimple design with fewer moving parts | Requires a compressed air supplyMay not be as precise as electric actuatorsCompressed air quality must be maintained to prevent damage |
Hydraulic | Highest torque capacity among all gear typesSmooth and precise controlSuitable for the most demanding applications | Requires a hydraulic fluid supplyMore complex and expensive than other gear typesHydraulic fluid leaks can be messy and hazardous |
Butterfly Valve Gear Type Applications in Various Industries
Butterfly valves, with their various gear types, find applications across a wide range of industries due to their versatility, reliability, and ability to handle diverse process conditions. Below is a summary table presenting different butterfly valve gear types used in various industries:
Gear Type | Application Industries |
Manual Gears | Water Treatment, Agriculture, Low Pressure Industrial Processes |
Gear Operators | Oil & Gas, Power Plants, Heavy Industry |
Electric Actuators | Water & Wastewater, HVAC, Light to Medium Industrial Processes |
Pneumatic Actuators | Chemical Processing, Food and Beverage, Pharmaceutical |
Hydraulic Actuators | Mining, Large Valve Operations, High Pressure Applications |
These are some of the main applications of butterfly valve gear types in different industries. The selection of the gear type shall depend on the situation of each application, which takes into account the process conditions, control precision, safety considerations, and automation needs. Through recognition of the strengths and weaknesses of every gear type, industries can make the best choice of a butterfly valve that would meet the needs of their specific applications and thus guarantee their proper performance and reliability.
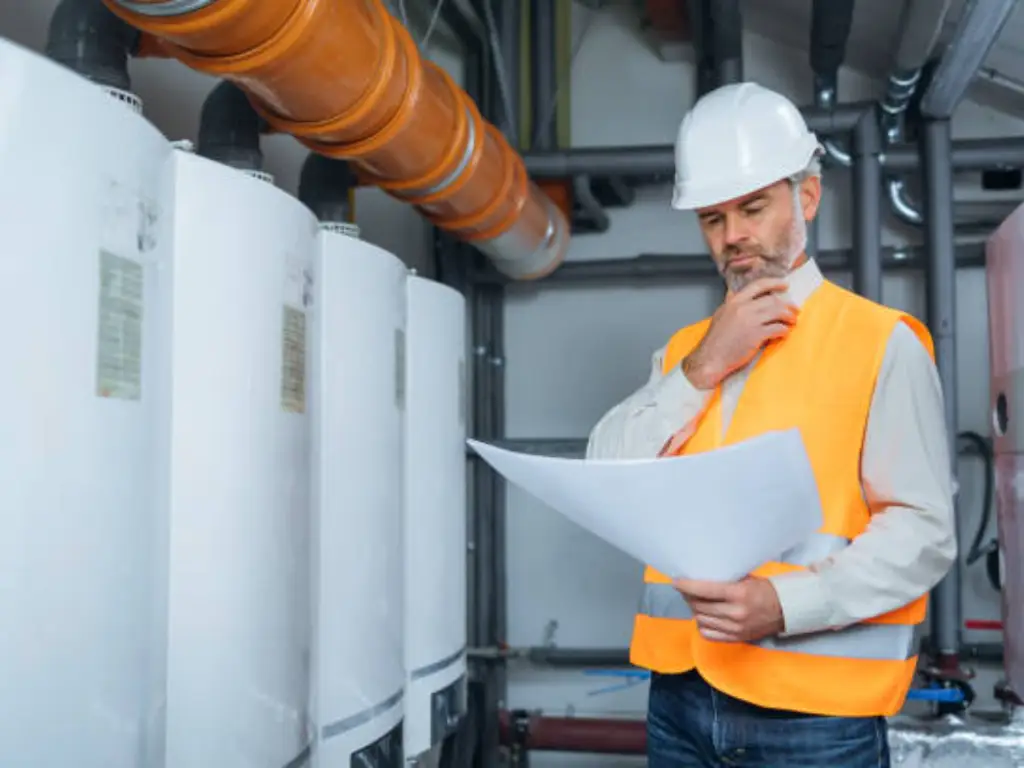
Factors to Consider When Selecting a Butterfly Valve Gear Type
When selecting a butterfly valve gear type for your application, several factors need to be considered to ensure optimal performance and reliability. These factors include:
- Application requirements: Think about the precise requirements of your application that include the level of control, the operating environment, and the process conditions. Different gears are designed for different purposes, therefore, you should select the one that fits your needs the most.
- Valve size and pressure rating: The size of the valve and the pressure rating of the system will determine whether the gear type is to be selected. Bigger valves and higher pressures may necessitate gear types with higher torque capacity, for instance, gear-operated or hydraulic valves.
- Control precision: If your application requires a valve to be set at a very specific location, choose gear types that provide a high level of accuracy, such as electric or gear-operated valves. Manual valves may not be able to achieve the desired accuracy for particular applications.
- Automation needs: If you are seeking automated valve control, electric or pneumatic gear types are suitable choices. These gear types can be easily interfaced with a process control system to enable remote operation and monitoring.
- Safety considerations: In hazardous surroundings, for example, with explosive atmospheres, pneumatic gear types are frequently used because of their intrinsic safety. Electric valves might not be good enough for such conditions, unless they are specifically designed for hazardous areas.
- Maintenance and reliability: Think about the maintenance needs and the anticipated reliability of each type of gear. Certain gear types, such as manual valves, might need more frequent maintenance as a result of their mechanical nature. Some of them, for example pneumatic valves, may be more reliable because they have fewer parts and are easier to operate.
- Cost: The cost of the valve and the cost of the parts that are associated with the valve should also be considered. As for manual valves, they are the cheapest option, while automated ones, including electric and hydraulic valves, may have higher initial costs. Nevertheless, the long-term benefits of automated control and efficiency should be taken into account when making the overall cost assessment.
Through the analysis of these factors and recognizing the distinctive features of each butterfly valve gear type, you can then choose the best gear for your application.
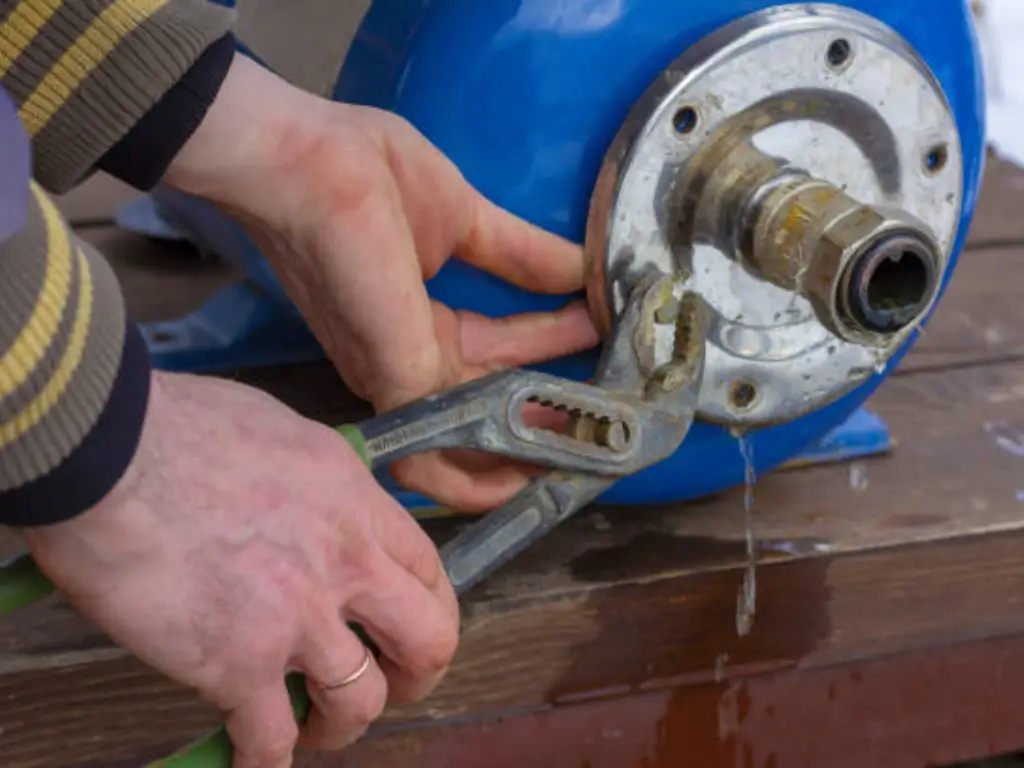
Butterfly Valve Gear Type Maintenance and Troubleshooting
Proper maintenance and troubleshooting are essential to ensure the reliable and efficient operation of butterfly valves, regardless of the gear type. Regular maintenance helps to prevent failures, extends the valve’s service life, and minimizes downtime. Here are some key aspects of butterfly valve gear type maintenance and troubleshooting:
- Lubrication: Regularly lubricate the valve stem, gears, and other moving parts to prevent friction and wear. Select the recommended lubricant according to the valve manufacturer, and adhere to the specified lubrication intervals.
- Tightening and adjustment: Periodically check and tighten any loose bolts, nuts, or fasteners. Set the gear lever as required to ensure the best performance and avoid excessive wear.
- Cleaning: Make sure the valve and its parts are always clean and free from dirt, debris, and corrosion. Clean the valve body, seat and sealing surfaces to ensure complete sealing and prevent leaks. Apply the recommended cleaning agents and methods by the manufacturer.
- Inspection: Regularly check the valve for any indication of wear, damage, or corrosion. Search for any visible cracks, deformation or other irregularities. Make sure to inspect the valve disc, seat, and stem since they are crucial for the proper operation of the valve.
- Seal replacement: Seals and gaskets can wear out over time and as a result of leaks. Replace worn or damaged seals when necessary to prevent valve damage. Adhere to the seal replacement procedures recommended by the manufacturer and make sure that the recommended seal materials are used.
- Actuator maintenance: For valves with electric, pneumatic, or hydraulic actuators, ensure you follow the manufacturer’s guidelines for the actuator. Such may be lubrication, seal replacement as well as calibration of the actuator’s control components.
- Troubleshooting: If a valve does not function well, the first thing you need to do is to find out the reason of the problem. Main problems include leaks, sticking/binding of the valve disc, and actuator malfunction. Referring to the valve manufacturer’s troubleshooting guide will help you with step-by-step instructions for identifying and resolving the problem.
- Spare parts: Have a stock of critical spare parts, such as seals, gaskets, and bearings, to minimize down time when a valve failure takes place. Make sure that the spare parts are compatible to your particular valve model and gear type.
- Training: Train maintenance personnel well enough to ensure that they have all the skills and knowledge needed to perform the maintenance tasks safely and effectively. This involves the knowledge of the valve’s principles of operation, the safety precautions, and the maintenance methods.
Regular maintenance work and proper troubleshooting techniques can be used to ensure that the butterfly valves perform efficiently and last for a longer performance time irrespective of the gear type. Such a preventive strategy will contribute to lowering unexpected downtime, cutting maintenance costs and guaranteeing the smooth operation of the process.
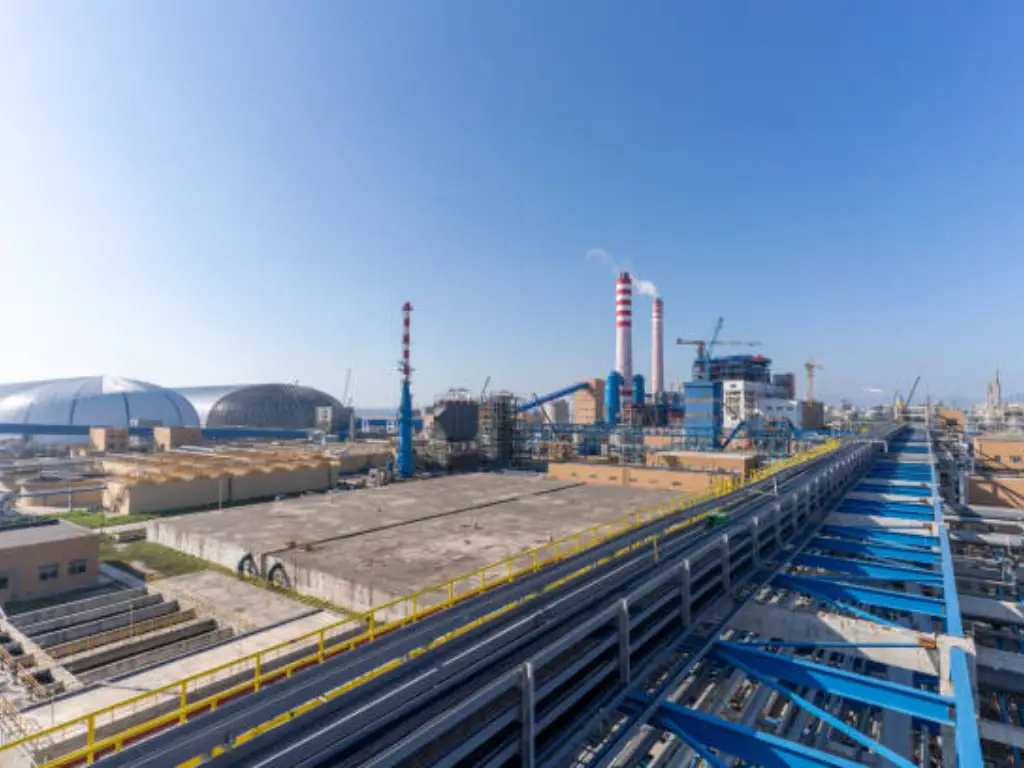
The Future of Butterfly Valve Gear Type Technology
Industries, as they are undergoing constant evolution and encounter new challenges, also the technology behind butterfly valve gear types is also being developed to satisfy the emerging needs. Here are some trends and developments that are shaping the future of butterfly valve gear type technology:Here are some trends and developments that are shaping the future of butterfly valve gear type technology:
Smart valves and IoT integration
- The implementation of smart sensors and IoT (Internet of Things) technology into butterfly valves is making it possible to track events in real-time and collect data.
- Smart valves can provide a great benefit in the form of information on valve performance, condition and maintenance requirements, which allows for predictive maintenance and optimized process control.
- IoT integration guarantees remote monitoring and management of valves, hence improving efficiency and decreasing the need for on-site interventions.
Advanced materials and coatings
- The growth of high-tech materials and coatings is making butterfly valves more durable, corrosion resistant and performance-oriented for sustainability.
- The new materials, like high-performance polymers and ceramics, used for valve components, are greatly better in terms of wear resistance and chemical compatibility.
In summary, it is important to know the different butterfly valve gear types and their applications so that you can make an informed decision about what valve is best suited for your specific needs. Through taking into account criteria like controlling accuracy, automation level, safety and reliability your process will be more effective and efficient. Whether you are choosing for a simple manual valve or an advanced electric or hydraulic actuator, selecting the appropriate butterfly valve gear type and the related products will help you to achieve your flow control purpose. You can choose from the vast array of options and also get credible shipping assurance from trusted valve manufacturers, thereby you can implement the most suitable butterfly valve solution for your application with confidence.