Eine Raffinerie ist eine Industrieanlage, die aus mehreren Geräten besteht, die für die Umwandlung von Erdöl (Rohöl) in verschiedene verwertbare Erdölnebenprodukte erforderlich sind. Bevor dieser Prozess durchgeführt werden kann, müssen Erdöl/Erdgase in ihrem Rohzustand mit hochentwickelten Maschinen aus der Erdkruste gebohrt werden.
Öl- und Gasraffinationsverfahren können in chemische und physikalisch-chemische Verfahren unterteilt werden. Die verfügbare Ausrüstung, die Qualität des Rohöls und der Verwendungszweck des raffinierten Öls bestimmen, welches der Verfahren geeignet ist. Zu den Nebenprodukten, die aus Rohöl gewonnen werden, gehören Benzin, Asphaltbasis, Dieselkraftstoff, Heizöl, Flüssiggas (LPG), petrochemische Rohstoffe und vieles mehr.
Dieser Artikel befasst sich mit der Geschichte der Ölraffination, den Auswirkungen der Ölraffinerie-Maschinenund alle wichtigen Prozesse, die für die Raffination von Rohöl erforderlich sind.
Geschichte der Ölraffinerie
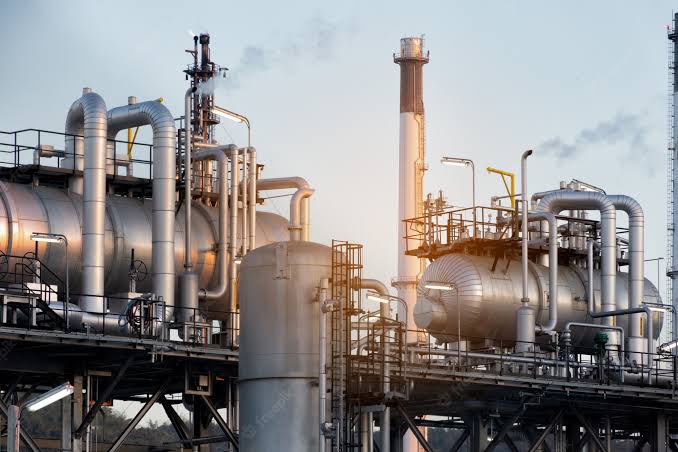
Seit der Erfindung der richtigen Ausrüstung für Ölraffinerien, Die Entdeckung von Erdöl ist ein weltweites Phänomen. Einem berühmten Werk des chinesischen Geographen, Politikers und Schriftstellers Li Daoyuan zufolge lässt sich die Geschichte der Ölraffination bis in die Nördliche Wei-Dynastie im ersten Jahrhundert, etwa 512 - 518 nach Christus, zurückverfolgen.
Im Laufe der Jahre gab es viele bemerkenswerte Perioden, in denen Rohöl zu brauchbaren Produkten verarbeitet wurde. Eine davon wurde in den Jahren 865 - 925 n. Chr. aufgezeichnet, als einige arabische Handbücher Beschreibungen darüber enthielten, wie Rohöl oft von arabischen Chemikern destilliert wurde, um Teer herzustellen, der auf den Straßen verwendet wurde.
Die moderne Geschichte des Erdöls soll im Jahr 1846 begonnen haben, als der Kanadier Abraham Gessner ein Verfahren zur Herstellung von Kerosin aus Kohle erfand. Einige Jahre später übernahm Igy Łukasiewicz das Verfahren und begann mit der Produktion von Kerosin aus handgegrabenen Ölquellen. In der Zwischenzeit konnte Rumänien die erste industrielle Erdölraffinerie der Welt beherbergen, da das Land reichlich Rohöl besaß.
Ursprünglich war Kerosin das erste Nebenprodukt, das bei der Raffination von Rohöl anfiel. Diese Entdeckung ebnete den Weg für die Ölindustrie, da Kerosin als Brennstoff für Öllampen sehr gefragt war. Mit dem Aufkommen des Verbrennungsmotors und seiner Bedeutung für die Automobilindustrie entstand nach und nach ein riesiger Markt für Benzin.
Seitdem sind an verschiedenen Orten der Welt mehrere private und öffentliche Raffinerien entstanden. Im Laufe der Zeit begannen die großen Unternehmen, enorme Summen in die Herstellung hochentwickelter Ölbohr- und Verarbeitungsanlagen zu investieren, um eine maximale Ausbeute zu erzielen.
Im Jahr 2017 wurde der Markt für Erdölraffination auf über $6 Billionen geschätzt, und es wird geschätzt, dass der Verbrauch aufgrund des raschen Bevölkerungswachstums und des Einsatzes von Technologien stark zunehmen wird. Dies macht ihn zu einem der größten und wachsenden Sektoren der heutigen Weltwirtschaft.
Warum leistungsstarke Ölraffineriemaschinen notwendig sind
Der einzige Zweck jeder technologischen Entwicklung ist entweder die Lösung eines Problems oder die Verbesserung der Leistung. Die Einrichtung der richtigen Ausrüstung und Maschinen wird nicht nur die Leistung einer Raffinerie verbessern, sondern auch dazu beitragen, alle Probleme zu lösen, die durch den Einsatz veralteter Maschinen entstehen können.
Im Folgenden werden einige der Gründe genannt, warum leistungsfähige Ölraffineriemaschinen notwendig sind.
- Für die ordnungsgemäße Lagerung von Ölerzeugnissen
Eine Raffinerie muss mit geeigneten Tankanlagen ausgestattet sein. Die Tanks dienen der Lagerung von Rohstoffen und bereits raffinierten Produkten. Wenn die Raffinerie über genügend Tanks verfügt, ist ein kontinuierlicher Betriebsablauf gewährleistet, da das Rohöl problemlos aus der Ölquelle entnommen und gleichzeitig in den für die Verarbeitung erforderlichen Tank umgefüllt werden kann.
Für Zwischen- und Endprodukte müssen mehr Tanks bereitgestellt werden als für Rohöl selbst. Der Grund dafür ist, dass sie in der Regel flüchtiger sind und einen hohen Druck aufweisen. Außerdem müssen zusätzliche Tanks für verarbeitete und fertige Produkte bereitgestellt werden, um eine Unterbrechung der Lieferkette während der Wartungsarbeiten zu vermeiden.
Die meisten Tanks sind in der Lage, Rohöl/Produkte mit einem Verarbeitungszyklus von etwa 50 Tagen zu lagern. Nicht flüchtige Produkte wie Heizöl und Diesel werden in zylindrischen Tanks mit einem flach geneigten Kegeldach gelagert. Während flüchtige Produkte Tanks mit Schwimmdach benötigen, um die Verdunstung zu verringern. Zu den Arten von Raffinerietanks gehören liegende Tanks, Drucktanks, Tanks mit variablem Dampfraum, interne/externe Schwimmdachtanks, Festdachtanks usw.
- Giftige Kohlenwasserstoffe ausstoßen
Das Austreiben von Kohlenwasserstoffen ist ein wichtiger Prozess in Ölraffinerien, der mit Hilfe von Fackeln durchgeführt wird. Eine Fackel hat die Form eines hohen Schornsteins, an dessen Spitze Flammen brennen. Diese Ausrüstung ist sehr wichtig für die Anlagensicherheit, da flüchtige Kohlenwasserstoffe explosiv sein können, wenn sie der Luft ausgesetzt werden.
Im Falle eines Maschinenausfalls oder -stillstands müssen alle giftigen Bestandteile aus allen Geräten gespült werden, bevor sie gewartet werden können. Die Fackel besteht aus einem geschlossenen Rohrleitungssystem, das dazu beiträgt, alle giftigen Kohlenwasserstoffe zum Fackelstandort zu befördern, wo sie unter strenger Aufsicht verbrannt werden.
- Zur Erleichterung des Massengutverkehrs
Um den Transport von Schüttgut zu erleichtern, wurden Hochseetanker und ein Netz von Pipelines gebaut. Die Hochseetanker ermöglichten es, Raffinerien näher an den Marktgebieten als an den Ölfeldern anzusiedeln. Seitdem wurden in einigen Städten Tiefseehäfen gebaut, um die großen Raffinerien durch Pipelines zu verbinden.
Pipelines gibt es inzwischen überall auf der Welt, denn sie sind nach wie vor das effizienteste Mittel für den Transport von Erdölmassengut durch Raffinerien und Verladehäfen auf See. Mit dem Einsatz von hochentwickelten Veredelungsmaschinen wie z. B. Kreiselpumpen und Druckerhöhungsanlagen, die entlang der Pipelinetrassen gebaut werden, erhält das transportierte Material genügend Pumpleistung, um sein Ziel zu erreichen.
- Leiten von Wärmeenergie zwischen zwei Medien
In jeder Raffinerie, vor allem in der Rissbildung In einer Anlage, in der Öl und Wasser getrennt werden, ist thermische Energie für die Produktverarbeitung unerlässlich. Allerdings kann sie große Schäden an Steuerungssystemen und empfindlichen Maschinen verursachen, wenn sie nicht richtig reguliert wird. Aus diesem Grund ist die Wärmetauschermaschine erforderlich.
Der Wärmetauscher ist ein Thermoregulationsgerät, das in erster Linie dazu dient, überschüssige Wärme abzuführen und die Temperatur während der Verarbeitung zu regulieren. Das erste Medium ist die zu verarbeitende Flüssigkeit oder das zu verarbeitende Gas, das andere Medium ist das wärmeabsorbierende Kühlmittel, das aus gekühltem Gas oder Flüssigkeit besteht.
Der Arbeitsprozess einer vollkontinuierlichen Ölraffinerie
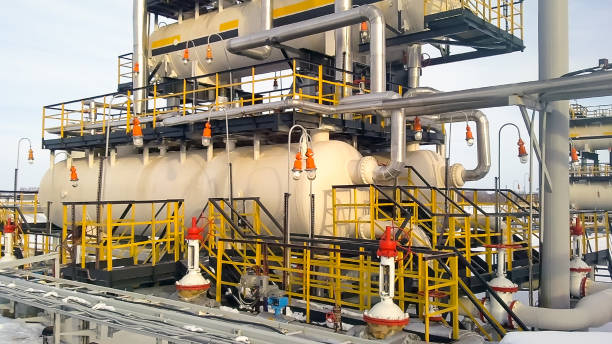
Wenn das Rohöl bereits aus einer Ölquelle gefördert wurde, erfordert der Verarbeitungsprozess vier verschiedene Stufen, bevor es auf den Markt gebracht werden kann. Es handelt sich dabei um Trennung, Umwandlung, Behandlung und Vermischung.
Informieren Sie sich in den nächsten Abschnitten über diese Prozesse.
- Trennung
Dieses Verfahren wird hauptsächlich zur Trennung der Erdölbestandteile (auch als Fraktion bezeichnet) durch Destillation durchgeführt. Die Trennung erfolgt, indem das Rohöl durch einen heißen Ofen geleitet wird, um flüssige und dampfförmige Komponenten zu bilden. Diese Komponenten werden dann in eine atmosphärische Destillationsanlage oder eine Vakuumdestillationsanlage geleitet.
Die Destillationsanlagen sorgen dafür, dass der flüssige und dampfförmige Inhalt in Fraktionen getrennt wird. Nach Erreichen eines bestimmten Siedepunkts verbleiben die schweren Fraktionen im unteren Teil, während die leichten Fraktionen darüber bleiben. Petroleum und Benzin, die leichtesten Fraktionen, steigen in der Destillationseinheit nach oben und werden wieder zu Flüssigkeit kondensiert.
Mittelschwere Fraktionen wie Destillationsmittel und Kerosin befinden sich in der Mitte der Destillationseinheit, während die schwersten Fraktionen wie Schweröle und Rückstandsöle am Boden bleiben. Die Separatoren sind zahlenmäßig die am meisten verarbeitenden Maschinen in jeder Raffinerie. Diese Maschine kann auch als Scrubber, Zentrifuge, Slug Catcher und viele andere Bezeichnungen bezeichnet werden.
- Konvertierung
Dies ist die zweite Verarbeitungsstufe, in der die Fraktionen durch verschiedene Verfahren, wie hydrothermisches, thermisches und katalytisches Cracken oder Kochen, in Größe und Struktur umgewandelt werden. Dieser Prozess stellt sicher, dass schwere, minderwertige Fraktionen zu leichteren, höherwertigen Fraktionen, wie Benzin, weiterverarbeitet werden.
Das Cracken ist die häufigste Form der Umwandlung, da es mit Hilfe von Katalysator, Druck, Wärme und eventuell Wasserstoff erfolgt. Bei diesem Verfahren werden schwere Kohlenwasserstoffmoleküle in leichtere aufgespalten. Die Crackanlage besteht aus dickwandigen Reaktoren, Wärmetauschern, einer Kette von Öfen und vielen anderen Behältertypen.
- Behandlung
Verunreinigungen wie Schwermetalle, Schwefel und Stickstoff sind häufig im Rohöl enthalten. Diese Verunreinigungen sind in benzinbetriebenen Motoren unerwünscht und müssen daher vor dem Vertrieb entsprechend behandelt werden.
Der wichtigste Aufbereitungsprozess ist das Hydrotreating, bei dem die Chemikalien durch Bindung mit Wasserstoff, durch Zugabe von Säure oder durch Absorption in einer anderen Kolonne entfernt werden. In diesem Stadium werden einige Feinarbeiten durchgeführt, indem mehrere Ströme mit der Aufbereitungseinheit kombiniert werden.
- Mischen
Das Mischen ist die letzte Stufe des Raffinationsprozesses. Dabei werden verschiedene Fraktionen zu brauchbaren Erdölprodukten gemischt. Es gibt verschiedene Sorten von Ottokraftstoff, und diese Sorten hängen von den Fraktionen ab, mit denen sie gemischt werden, z. B. Alkylat, Reformat, Spaltbenzin usw.
Raffinerien produzieren in der Regel 8 bis 15 Fraktionen von Kohlenwasserstoffen, die mit Motorkraftstoffen gemischt werden müssen. Zusatzstoffe wie Oktanverbesserer, Antioxidantien, Rostschutzmittel, Metalldeaktivatoren und andere werden für die richtige Mischung verwendet. Ottokraftstoffmischungen werden durch den Dampfdruck, die Oktanzahl und einige andere spezielle Überlegungen bestimmt.
Betriebsverfahren einer Ölraffinerie
Die Raffination ist eine nachgelagerte Phase in der Erdölförderung und -verarbeitung und besteht aus sieben Grundoperationen. Diese Verarbeitungsschritte können je nach Wahl des Betreibers entweder physikalisch oder chemisch durchgeführt werden. In letzter Zeit scheint jedoch das chemische Verfahren zu überwiegen.
Der Betriebsprozess kann in sieben Stufen unterteilt werden, wobei jede Stufe aus einem anderen Verarbeitungsmittel besteht. Die Prozesse und die erforderlichen Mittel sind unten aufgeführt.
Ablauf der Operation | Erforderliche Mittel |
Trennung | Raffination mit Lösungsmitteln. Destillation. |
Konvertierung | Zugabe von Wasserstoff. Entfernung von Kohlenstoff. |
Reformierung | Katalytisches Reforming. Kohlenwasserstoff-Reforming. |
Umstrukturierung | Isomerisierung. |
Kombination | Katalytische Polymerisation Alkylierung. |
Behandeln, Veredeln und Mischen | Benzin, Kerosin und Diesel. Schmierstoffe und Wachse. Asphalt. |
Schutz der Umwelt | Abwasserbehandlung. Beseitigung von Feststoffen. Rückgewinnung von Schwefel. |
Chemische Prozesse in der Ölraffinerie
Die chemische Verarbeitung bei der Erdölraffination dient dazu, große Kohlenwasserstoffe in kleinere Stücke zu zerlegen (Cracken), kleinere Stücke zu größeren zusammenzufügen (Vereinheitlichung) oder verschiedene Stücke so umzuordnen, dass die gewünschten Kohlenwasserstoffe entstehen (Umwandlung). Dieser chemische Prozess kann in thermische und katalytische Formen unterteilt werden, die im Folgenden erläutert werden.
Thermischer Prozess
- Visabrechung
Bei diesem Verfahren werden die Erdölfraktionen aus dem Destillationsturm auf eine Temperatur von 900⁰F/482⁰C erhitzt. Anschließend wird es mit Gasöl abgekühlt und schnell geblitzt im Destillationsturm. Dieses Verfahren ist erforderlich, um die Viskosität von Ölen mit hohem Gewicht zu verringern.
- Verzögertes Verkoken
Beim Delayed-Cooking-Verfahren werden die Fraktionen aus dem Destillationsturm auf über 900⁰ F/482⁰ C erhitzt, bis sie beginnen, in Benzin, Nepeta und Schweröl zu zerfallen. Nach Beendigung des gesamten Prozesses bleiben in den Kokern Rückstände in Form von schwerem, reinem Kohlenstoff (Koks) zurück.
- Flexicoking
Diese Form des thermischen Crackens ist mit der Vergasung von Koks unter Verwendung von Dampf und Luft verbunden. Beim Flexicoking wird eine große Menge an Kokskohle in Kohlenmonoxid umgewandelt, bevor sie mit leichten Kohlenwasserstoffen gemischt wird, um ein minderwertiges Erdölgas zu erhalten. Ein Teil des Koks wird verbrannt, um die erforderliche Wärme während des Prozesses der Umwandlung des Vakuumrückstands in Destillat, Gase, Koks und Flüssigkeit bereitzustellen.
Katalytisches Verfahren
- Hydrocracken
Dieses Verfahren wird bei der Umwandlung von schwerem Gasöl in Benzin eingesetzt und wird meist bei Öl, Kerosin, Naphtha und Gas angewendet. Diese Materialien werden in Gegenwart eines Katalysators mit Wasserstoff auf hohe Temperaturen erhitzt, bis sie 300-400° Celsius erreichen. Das Hydrocracken hilft auch bei der Beseitigung von Fremdstoffen wie Stickstoff, Schwefel und Spurenmetallen.
- Katalytisches Cracken
Dieses Verfahren eignet sich für die Umwandlung von Rückstandsöl oder Gasöl in Benzin oder Diesel. Sowohl Rückstandsöl als auch Gasöl werden unter starker Hitze und hohem Druck in Gegenwart eines Katalysators aufgespalten. Wenn die Kohlenwasserstoffe mit dem Katalysator in Berührung kommen, beginnen sie, in kleinere Kohlenwasserstoffe zu zerfallen. Manchmal werden Produkte mit einem geringen Wasserstoffgehalt, z. B. Bitumen, dem Prozess als Kohlenwasserstoffe zugesetzt.
- Polymerisation
Der Polymerisationsprozess sorgt dafür, dass leichte Olefingase, d.h. Ethylen, Butylen und Propylen, in Kohlenwasserstoffe mit höherem Molekulargewicht und höherer Oktanzahl umgewandelt werden, die als Benzinmischung dienen können. Dieses Verfahren wird häufig in Gegenwart eines sauren Katalysators durchgeführt. Die Verarbeitungstemperatur beträgt etwa 300-450 °C und kann durch Einspritzen von kaltem Ausgangsmaterial und Kühlwasser in den Reaktor gesteuert werden.
- Katalytische Entparaffinierung
Die katalytische Entparaffinierung stellt sicher, dass das erzeugte Öl, z. B. Diesel, in genau dem Temperaturbereich flüssig bleibt, in dem es verwendet werden soll. Damit diese Produkte den kommerziellen Anforderungen entsprechen, muss der Temperaturbereich mit den Anforderungen an den Kaltfluss übereinstimmen. Bei der katalytischen Entparaffinierung handelt es sich um ein Umwandlungsverfahren mit geringem Schweregrad, das eine Form des selektiven katalytischen Crackens von n-Paraffinen beinhaltet.
- Alkylierung
Bei der Alkylierung handelt es sich um ein chemisches Verfahren, bei dem leichte, gasförmige Kohlenwasserstoffe miteinander kombiniert werden, um hochoktanige Bestandteile von Benzin zu erzeugen. Diese Kohlenwasserstoffe enthalten Olefine wie Butylen und Isoparaffine wie Isobutan. Alle diese Komponenten werden in den Reaktor geleitet, um ein Gemisch aus schweren Kohlenwasserstoffen zu bilden, wobei der Prozess in Gegenwart eines Salzsäurekatalysators durchgeführt wird.
Was ist bei der Verwendung von Ölraffinerieausrüstung zu beachten?
Nachfolgend finden Sie die Faktoren, die Sie bei der Verwendung von Ölraffinerieausrüstung berücksichtigen müssen:
- Hohe Korrosionsanfälligkeit
Korrosion ist eine der größten Herausforderungen für die meisten Raffinerien. Der Grund dafür ist, dass die meisten Raffinerie-Ausrüstung sind aus Stahl und Metall gefertigt. Korrosion ist eine Form der Materialverschlechterung, die sich aus der Wechselwirkung mit der Umgebung ergibt. Korrosion beeinträchtigt nicht nur die chemischen Eigenschaften eines Materials, sondern führt auch zu einer negativen Veränderung seiner physikalischen Struktur.
Es gibt bestimmte anaerobe Mikroorganismen im Rohöl, die Korrosion verursachen. Sie kann auch auftreten, wenn sich Wasser am Boden eines Lagertanks absetzen kann. Die Entsalzung kann dazu beitragen, anorganische Stoffe aus dem Rohöl zu entfernen, um die Korrosion zu verringern. Auch kathodischer Schutz, Metallbeschichtungen und die Auswahl der Materialien können bei der Korrosionskontrolle helfen.
- Erfordern häufige Wartung
Die Anlagen in einer Raffinerie können nur dann effektiv arbeiten, wenn sie so sauber wie möglich gehalten und ständig überprüft werden. Viele dieser Ausrüstungen sind in offenen Bereichen montiert und somit schlechtem Wetter und salzhaltiger Luft ausgesetzt. Außerdem können Schäden durch Abnutzung und Verschleiß sowie durch menschliches und maschinelles Versagen verursacht werden. Aus diesen Gründen muss eine ordnungsgemäße Wartung durchgeführt werden.
Zu den Wartungstechniken gehören Reinigung, Schmierung, Austausch, Prüfung, Reparatur usw. Die Aufgabe des Wartungstechnikers besteht darin, dafür zu sorgen, dass die vorbeugende und vorausschauende Wartung häufig oder in bestimmten Abständen durchgeführt wird. Die Kosten für die Wartung von Rohrleitungsventilen können gesenkt werden, wenn sie von einem Fachmann wie einem Hersteller von Absperrklappen.
- Das Gerät muss von qualifiziertem Personal bedient werden
Die meisten Anlagen in einer Raffinerie erfordern ausreichende technische Kenntnisse. Unqualifizierte oder ungeschulte Personen dürfen die Maschinen nicht bedienen, um Schäden zu vermeiden. Bei vollautomatischen Anlagen darf die Umprogrammierung nur von Fachpersonal vorgenommen werden, das mit dieser Aufgabe betraut ist. Außerdem müssen die Steuerschalter für Notfälle deutlich gekennzeichnet sein. Feste Schutzvorrichtungen müssen unbedingt verwendet werden, um wichtige und gefährliche Geräte zu umschließen.
- Schmierstoffe sollten dekontaminiert werden
Alle rollenden Teile in einer Raffinerie müssen geschmiert werden. Eine Verunreinigung des Schmiermittels kann bei einigen Raffinerieanlagen zu Lagerausfällen führen. Daher müssen regelmäßig Spülungen, Entlackungen und Flüssigkeitswechsel durchgeführt werden. Daher sollten Raffinerien am besten mit Unternehmen zusammenarbeiten, die auf die Wartung von Schmiermitteln spezialisiert sind, um das beste Ergebnis zu erzielen.
- Druck
Damit Erdölprodukte leicht zu kontrollieren sind und sich schneller im Rohrleitungssystem bewegen können, benötigen sie einen hohen Druck und den Einsatz von Ölfeldventile. Mineralölprodukte können von leicht bis schwer sein. Damit schwerere Stoffe problemlos durch ein langes Rohrleitungssystem fließen können, ist ein stärkerer Pumpentyp erforderlich. Zu den verschiedenen Pumpentypen gehören: Zentrifugalpumpe, Kolbenpumpe, Exzenterschneckenpumpe, Exzenterschneckenpumpe, Zahnradpumpe usw.
Häufig gestellte Fragen
- Was ist ein Barrel Öl?
Barrel Öl ist die Volumeneinheit für die Messung von Öl und ein Barrel entspricht ungefähr 42 US-Gallonen.
- Was ist eine Offshore-Anlage?
Eine Offshore-Bohrinsel ist eine speziell auf dem Wasser errichtete Anlage, die mit Einrichtungen zur Bohrung, Förderung und Verarbeitung von Erdöl und natürlichen Gasen unter dem Meeresboden ausgestattet ist. Die Anlage ist groß genug, um Arbeiter unterzubringen und Produkte zu lagern, bis ein Schiff für den Transport bereitsteht.
- Welche Art von Rohöl wird in der Reserve gelagert
Reserven gibt es schon seit langem. Rohöl wird in die Kategorien "süß" und "sauer" eingeteilt. Süßes Öl enthält einen Schwefelgehalt von höchstens 0,5 Prozent, während saures Öl einen Schwefelgehalt von mehr als 0,5 Prozent, aber weniger als 2,0 Prozent aufweist. Die meisten Lagerstätten nehmen nur Rohöl an, das ihren festgelegten Spezifikationen entspricht.
- Was sind die Verwendungszwecke von Rohöl?
Rohöl wird unter anderem für den Transport, für Privathaushalte, für die Stromerzeugung sowie für industrielle und gewerbliche Zwecke verwendet.
- Was ist der Unterschied zwischen Upstream- und Downstream-Ölverarbeitung?
Die vorgelagerte Stufe umfasst die Explorations-, Bohr- und Förderphase, während die nachgelagerte Stufe die Raffinations- und Verteilungsphase umfasst.
- Was ist ein Gehäusekopf?
Der Mantelrohrkopf ist eine vorgelagerte Ausrüstung. Er wird für die Verbindung von Rohrgehäusen mit Bohrlochköpfen verwendet. Der Verrohrungskopf ist mit einem Strang und einer Bohrungsschale mit einer 45-C-Ansatzschulter ausgestattet, um Schäden durch Überdruck zu vermeiden.
- Verwendungszwecke eines industriellen Kugelhahns
Eine Industriekugelhahnwird zur Steuerung des Öl-/Gasdurchflusses und des Drucks in Rohrleitungen verwendet, indem die im Ventil eingebettete Kugel gedreht wird.
Schlussfolgerung
Der einzige Zweck aller Erdölraffinerien besteht darin, Rohöl in Erdölprodukte umzuwandeln, die als Brennstoff zum Heizen, für den Transport, als chemisches Ausgangsmaterial, für den Straßenbau und vieles mehr dienen können. Dieser Umwandlungsprozess fällt unter die nachgelagerte Produktionsstufe, ebenso wie der Rohöltransport.
Um sicherzustellen, dass das Rohöl in vollem Umfang genutzt wird, müssen die Investoren genügend Ressourcen für die Beschaffung und Montage von Ausrüstungen bereitstellen, mit denen alle Verarbeitungsanforderungen erfüllt werden können. Es gibt zahlreiche Ausrüstungen, die in einer Raffinerie benötigt werden, aber wenn es um Ventile geht, zeichnet sich Dombor als einer der besten Hersteller von Industrieventilen und Lieferant. Unsere Ventile sind so konstruiert, dass sie einen Teilstrom ordnungsgemäß verwalten und hohen Temperaturen standhalten.